A cool biorepository
Bespoke system needed
These basic requirements of this novel and far-reaching initiative posed a wide range of challenges to our team at The Automation Partnership, or TAP.
Not least of these is the fact that UK Biobank is a repository on an unprecedented scale. No one has created anything of this size before so we had no off-the-shelf engineering solutions to solve the problems. Most hardware had to be custom-made, not least robots robust enough to store or pick-up as many as 2,000 samples each day; in an extremely hostile -80 °C environment. For a quarter of a century.
Our previous experience in creating high-integrity automated storage and retrieval systems for the pharmaceutical industry gave us the expertise and confidence that we could tackle this hugely complex enterprise successfully. Our team also had the benefit of experience in designing and building robotic systems for use in cold conditions, down to -20 °C.
Keep it simple
UK Biobank, based in Stockport as a host project of the University of Manchester, invited us to tender for the project in 2004. We responded with proposals within three weeks and were nominated as the preferred vendor. One key priority we pursued right from the start was to minimise the number of moving parts, particularly in the refrigeration system. This system is designed to provide consistent and continuous performance for 25 years so simplicity and reliability are essential.
This is why we opted to break with convention and discard the only method of refrigeration currently in widespread use in large-scale, low-temperature storage systems: mechanical refrigeration. Conventional single-compressor refrigeration systems typically can only achieve temperatures of about -40 °C. To produce lower temperatures, a two-stage cascade refrigeration system is required, requiring two different refrigerants.
To keep an archive of this size at -80 °C would require driving the efficiency of a two-stage cascade refrigeration system very close to its limit. To sharpen the risk further, its associated complexity, plus its narrow margin for loss of performance, would impose a very high cost of in-service maintenance, with the need for specialist servicing and repair (often using proprietary knowledge) that may not be available for the next 25 years.
LN2
Instead, TAP and UK Biobank explored the viability of using liquid nitrogen as a refrigerant and elected to opt for this approach. Liquid nitrogen is injected into heat exchangers in the sample storage chambers and delivers powerful advantages over mechanical refrigeration. Our target storage temperature could be reached easily (liquid nitrogen boils at -196 °C) and we would benefit from fast cool-down and recovery rates, effectively giving unlimited cooling capacity.
Nitrogen gas pressurises the storage tanks, causing the liquid to flow when a valve is opened. Excess pressure is relieved by a pressure relief valve fitted to the tank. There is a great simplicity of design, with no highly stressed components and very few moving parts – in fact, no moving parts or serviceable items at all in the crucial ultra-low temperature cabinets containing the precious samples. Liquid nitrogen also provides clear benefits in terms of efficiency, absence of waste heat, quietness of operation and cost of ownership.
These advantages appeared compelling – but nothing on this scale had been attempted before. So we undertook an extremely thorough development and testing process before progressing with the full-scale storage system.
Engineering Cool
Maintaining Cool
Our approach exploits the advantages of a ‘box-within-a-box’ in which the inner containers for the samples are super-chilled to -80 °C, each has a wall of insulated storage drawers that hold the samples, like massive floor-to-ceiling, shallow-drawer filing cabinets. This design avoids the big drawback of a conventional refrigerator – the inevitable warming that occurs when samples are accessed by opening a large door.
In our design, the ultra-low temperature (ULT) compartments – the shallow drawers – are separated from a highly de-humidified -20 °C zone within the outer box by fixed insulated panels on all their surfaces. These tiled walls of storage-trays are accessible to a robot travelling along the access aisle and form seals effective enough to allow the refrigeration system to maintain -80°C conditions comfortably.
Robotic Reliability
Giving Samples
Small Scale
Initial trial tests proved that only the samples held in the opened drawer experienced any change of temperature – even during a simulated failure when a drawer was left open indefinitely. At all times, the samples in adjacent drawers remained at -80 °C. When a drawer was opened
for a realistic placement or retrieval time – typically 30 seconds – a single isolated sample tube was found to only increase in temperature to -65 °C. This is the worst case because fully populated storage racks gain warmth even more slowly because of their greater thermal mass.
Another factor underpinning the integrity of POLAR’s design is the fact that less than 0.2% of the contents of the ULT cabinets are open to the -20 °C aisle temperature at any one time while archiving or accessing samples, limiting the number of samples exposed and preventing warming of adjacent drawers.
Having proved the soundness of this innovative approach, our team scaled-up the system to achieve the required capacity of 10million samples. All samples are stored in individual 1ml sample tubes and mounted on standard laboratory racks that are handled robotically from initial storage to eventual retrieval. Overall, the UK Biobank facility signifies a civil engineering project in its scale – it is a massive storage system holding 30 tonnes of samples and labware. Yet this archive is also a high-precision engineering project in the way it required the implementation of totally dependable and accurate robotic systems.
In the impressive shape of the UK Biobank, medical science is about to gain an enormous and innovative asset that can exploit the benefits of scale to energise research into the root causes of disease. As engineers, my colleagues at TAP and I are as privileged to be associated with it as we are dedicated to ensuring its success.
Further reference
www.ukbiobank.ac.uk
More about convection cooling can be found at www.automationpartnership.com
BIOGRAPHY – Justin Owen
Justin Owen leads the Hardware Engineering Group at The Automation Partnership (TAP), Cambridge. In addition to managing his group he is still a practicing engineer, leading large development projects and providing engineering leadership for TAP’s emerging portfolio of bench-top products. Justin’s involvement with the UK Biobank began in 2004 when TAP was invited to tender for the -80 °C storage component of the project. He led the technology development and engineering from concept to end product and has recently taken the system through commissioning and successful site acceptance tests.
Keep up-to-date with Ingenia for free
SubscribeOther content from Ingenia
Quick read
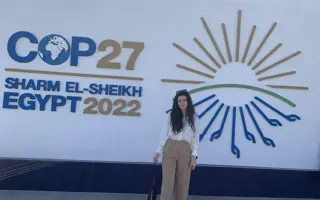
- Environment & sustainability
- Opinion
A young engineer’s perspective on the good, the bad and the ugly of COP27

- Environment & sustainability
- Issue 95
How do we pay for net zero technologies?
Quick read
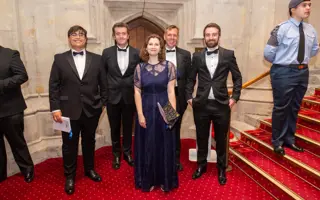
- Transport
- Mechanical
- How I got here
Electrifying trains and STEMAZING outreach
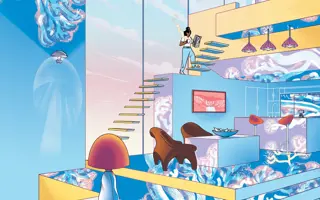
- Civil & structural
- Environment & sustainability
- Issue 95