
Building bridges
Volunteers from Hong Kong and Chinese universities and Arup work with villagers to build a footbridge using a manual system involving pulleys, ropes and a 500 kg chain block © Arup
A group of professional engineers working in Arup’s Hong Kong office have conceived, developed and helped to build a footbridge in a remote area of China. Working with a team of 50volunteers from different backgrounds, they lived with villagers and created a lifeline for decades to come. Ingenia interviewed Freda Chu, a Senior Engineer for Arup who led the project, to find how the bridge building fostered links between professionals and villagers in China.
Since its inception in 2007, the Hong Kong charity, Wu Zhi Qiao (Bridge to China) Charitable Foundation, has organised the building of bridges and village facilities in remote rural and underprivileged areas of mainland China. The charity’s objective is to improve the lives of the poor and to help increase integration between Hong Kong and mainland China by encouraging students to help those in need – see Wu Zhi Qiao Charitable Foundation.
In six years, Wu Zhi Qiao has mobilised over 1,000 volunteers and completed 26 building projects across mainland China; benefitting around 40,000 villagers to date.
New venture
In December 2009, the charity departed from its previous bridge builds by beginning work on a new and unusual project. The Arup x WZQ Bridge in the village of Mixia, Yunnan Province, was entirely funded, designed and constructed by the engineering group Arup, working with assistance from architecture and engineering university students from both Hong Kong and China. The scale and complexity of the proposed bridge was greater than any previous Wu Zhi Qiao project.
Mixia lies in a remote mountainous region near the border between China and Vietnam, 11 hours’ drive from the nearest airport in the city of Kunming. The location for the bridge is inaccessible by vehicle, and can only be reached by following a steep and muddy footpath more than a kilometre out of the village – a 40 minute trek on foot.
The original river crossing took the form of a primitive footbridge constructed from bamboo and supported by a bamboo basket filled with stones for the central pier. The span of the bridge was 18 m with access on both sides via a scramble down steep banks. The river itself swells during the rainy season, with the water level rising up to 6 m, and this force often swept the bridge away. The charity’s founder, Professor Edward Ng, could see that it had never constructed a bridge for such a difficult location before; hence the need for Arup’s experience.
For the company’s engineers, the project provided an unusual opportunity. As well as the usual consultancy involvement with the design development and onsite supervision, they would also be responsible for the architectural concept, procurement, overall construction cost and all aspects of onsite construction management – all of this without access to any heavy machinery or electricity.
To further complicate the challenge, they would also be facing a language barrier. The villagers are from the Hani tribe, and speak a form of the Tibeto-Burman language, with only a few villagers able to speak Mandarin.
In December 2009, a team comprising Arup staff and students from The Chinese University of Hong Kong (CUHK) and Kunming University of Science and Technology (KUST) visited the remote site to undertake the initial reconnaissance and surveying.
With no vehicle access or power available onsite and access on both banks limited by the steepness of the terrain, the constraints of the design brief were challenging. To bring as much imagination as possible to the project, Arup launched a design competition within its offices worldwide. An expert panel of representatives from the company and the Wu Zhi Qiao Charitable Foundation judged the 44 entries. The selected design was then developed over the course of 11months integrating the expertise of Arup engineers from offices in Hong Kong and mainland China, with the assistance of students from Xi’an University.

Artist’s impressions of the winning design by a team of young engineers from Arup’s Shenzhen, China office © Arup
Local design focus
The chosen cantilever bridge design reduced the risk of flood damage by removing the central pier. It would be constructed on foundations that take vertical gravity loads rather than using arches or horizontal load-bearing cables, both of which would be difficult to install in the limited steep-sloping space on the banks of the river. The design also used gabions (wire cages filled with ballast) filled with local stones to provide footings, reducing the quantity of material that would need to be transported to site. This choice of material significantly reduced the amount of cement required. To suit local conditions, the designers chose an open mesh ‘weather-friendly’ material for the walkway to prevent the buildup of ice during months of harsh winter weather, and restricted the design to a width of 1.2 m to prevent local farmers from bringing their carts onto the bridge and overloading it.

Artist’s impressions of the winning design by a team of young engineers from Arup’s Shenzhen, China office © Arup
Knowing that the bridge would have to be built by hand in just 12 days, without the use of sophisticated labour and plant, by personnel (including local villagers) with limited skills and experience, the engineering team selected hot-dip galvanised steel as the primary building material, with nuts and bolts used to connect components. Complex pre-welded elements were also avoided to reduce the risk of awkwardly shaped parts being damaged during transportation.
This consideration of ‘buildability’ led the engineers to the concept of a base frame on each bank with sufficient stability to enable the final span to be assembled and installed from the overhanging sections. To allow for the difficulties of setting out and ground conditions, the finished design also included an adjustable tolerance of 50 cm in the overall length of the bridge.
The team had to familiarise themselves with local materials such as bamboo, which played a critical role in the construction process. For the construction, a temporary suspension cable system was built onsite, from scratch, consisting of support frames built from locally sourced bamboo of unknown species, and incorporating steel wires, anchors, pulleys and ropes. Rope and knot training became an essential part of the preparations for construction, with the Hong Kong Scouts providing expert training to the project volunteers.
The cable system was anchored to a large boulder on one bank and a large gabion on the other. The use of bamboo scaffolding was not just a romantic notion, but offered the best solution in the circumstances. Instead of bringing in steel scaffolding, which would have to be carried in (and out) by hand, bamboo could be cut onsite under guidance from the villagers who have managed and utilised the local bamboo for generations.
Offsite testing
In September 2011, the team conducted a full-scale mock-up of the bridge assembly at the steel fabrication and assembly sponsor S-Couvrot’s factory in Shanghai. They used this valuable opportunity to translate ‘drawing-board’ designs into a sequence of construction tasks, and identifying issues with accurately moving components manually into place and aligning boltholes with a 2 mm tolerance. They then broke down the assembly instructions into a carefully recorded specific sequence, where some components would be pre-assembled before being lifted into place.
On the dry run, the engineers also identified an unexpected failure in the bamboo. The failure occurred where the horizontal steel pole that carried the cables at the apex of each truss placed a specifically localised force onto the top section of the bamboo. The team brought a variety of different bamboo sections back from the proposed location of the bridge, and with the help of the Department of Civil and Architectural Engineering at the City University of Hong Kong, carried out a set of point load tests which provided the team with a more thorough understanding of the load performance of bamboo. This reassured the team that the issue lay with the mix of materials, and that with the right detailling, bamboo was still an appropriately robust material for use in constructing the trusses. They also discovered that bamboo gives a series of quite audible warning sounds before it fails, a vital piece of knowledge for the volunteers who would be working with the material on site.
For the assembly of the bamboo structures, advice was sought advice from scaffolders in Hong Kong, where bamboo is commonly used as a scaffolding material.
On location
Onsite, a construction team of 49 was assembled, including Arup engineers and architects from the company’s Hong Kong and China offices, engineering and architecture students from the Hong Kong University of Science and Technology and CUHK, architecture students from KUST and committee members from Wu Zhi Qiao.
The risk elements of the project were gone through with a fine-tooth comb. Construction checklists were made, contingency plans for bad weather drawn up, risk registers were distributed and volunteer handbooks compiled. Doctors from CUHK’s School of Public Health gave the team a comprehensive health briefing before they left for the site. There was also an intensive site safety workshop and a first aid training course provided for all participants by St John Ambulance.
Once onsite, the entire team lived in the village during the 12-day construction, which generated a substantial cultural exchange. The project allowed the team of city dwellers to experience what life is like for people living in extreme poverty, on an income per head of less than the World Bank-defined US$1.25 per day. The volunteers also brought clothes and stationery donated by Arup staff, and organised activities and projects to have fun with the local school students, rejuvenated the village school building and renovated the school furniture.
Work begins
With foundation concrete slabs laid in advance, the construction team’s job onsite was to assemble the steel frames that would form the foundations of the bridge on opposite banks of the river. They assembled bamboo A-frame sections before erecting them to form the sides of the 6m-tall bamboo A-frame that would support the temporary rigging. However, the team soon discovered that they had to be flexible in the application of engineering skills and principles, as some elements of the design and dry run back in Shanghai had to be adapted to suit different conditions on the ground.
They found that the bamboo support A-frames had to be ‘flipped’ to position the tallest point furthest from the bank, as the large boulder that was to act as an anchor encroached into the space where the frame was to stand. On the opposite bank, the team also turned the truss as this moved the anchor further away from the apex of the truss and reduced the vertical forces on the temporary structure.
They used Hilti bolts to attach the cables for the rigging to the boulder on one bank, and created the anchor on the other bank by constructing two large gabions.
Meanwhile, they filled the foundation frames with the same wire mesh gabion cages that provided the permanent footings for the bridge. The villagers and team members filled these with locally sourced stones, having wielded sledge hammers in the river bed to provide suitably sized rocks.
With the base frame constructed on both sides of the river and the rigging erected, they lifted two longer beams into place on each side and bolted them onto the top to begin the ‘reach’ across the river, with diagonally inclined struts offering support from beneath. At each stage of the frame assembly, they bolted all sections together to form a rigid structure. The team then moved intermediate beams into positions stretching further across the divide, before bridging the gap with the final section and closing the span.
Finally, they installed a guardrail consisting of a series of semicircular bars, at the same time as the open-meshed decking was laid in place.
Communities united
The differing approaches to the problem between the city-dwellers and the villagers provided a valuable learning experience for all concerned, as the contrasting resourcefulness demonstrated by both sides helped to create a connection between both communities. While the villagers were used to solving problems with the often ingenious use of the very limited resources available to them, many of the students were able to use their knowledge of materials and engineering to provide alternative solutions.
Often the different approaches would offer the same solution, as is demonstrated by the old bridge with its use of bamboo cages full of stones and the use of gabions in the new bridge design.
Student involvement is a key part of the Wu Zhi Qiao’s approach, as this provides a unique opportunity to forge links between different communities. On this occasion, the complexities of the Arup x Wu Zhi Qiao bridge necessitated a high level of expert professional input in the planning of the entire operation, much more than the students would have been able to handle. The result was a bridge that should have a lifespan of at least 50 years and that was awarded the 2012 Edmund Hambly Medal by the Institution of Civil Engineers.
Arup continues to develop what has been learned on this project and is currently in talks with Wu Zhi Qiao on initiatives to expand the bridge building projects to students without architectural or engineering backgrounds. The idea is to organise the students into workshops to design a relatively simple bridge and then form a team to go and build it. This would be a great way to pass on skills and give the students better insight into what engineers do. It is hoped that such engagement could encourage participants to consider pursuing careers in engineering.
As for the Wu Zhi Qiao Charitable Foundation, it, in conjunction with China’s Ministry of Housing Urban-Rural Development, has a full slate of projects planned for 2013. Continuing to work with student volunteers from Hong Kong and mainland universities of China, they intend to build eight more bridges across different areas of the Republic in 2013. The charity will also develop a new bridge prototype and establish a demonstration earth house construction project in Gansu.
Read more at www.bridge2china.org
Keep up-to-date with Ingenia for free
SubscribeOther content from Ingenia
Quick read
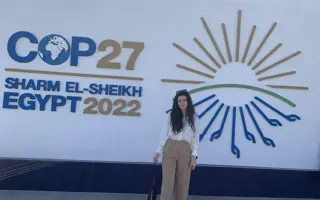
- Environment & sustainability
- Opinion
A young engineer’s perspective on the good, the bad and the ugly of COP27

- Environment & sustainability
- Issue 95
How do we pay for net zero technologies?
Quick read
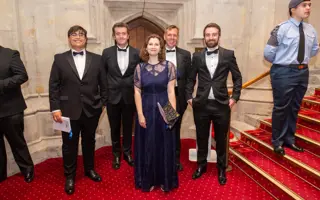
- Transport
- Mechanical
- How I got here
Electrifying trains and STEMAZING outreach
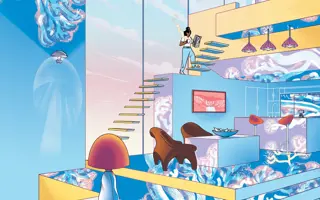
- Civil & structural
- Environment & sustainability
- Issue 95