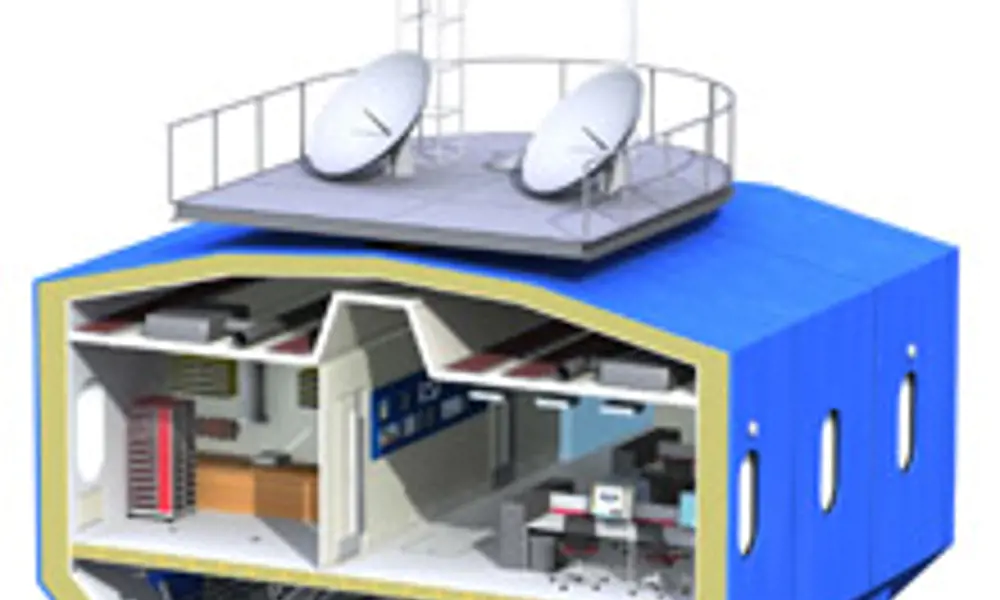
Built to Last- the Construction of Halley VI
Ski based, jackable, single-storey elevated modules are the building block of Halley VI Image by 7-t Ltd
There is a significant risk that after the year 2010 the British Antarctic Survey’s (BAS) most southerly and remote station, Halley V, will be lost due to a major glacial break-up. Karl Tuplin of BAS describes the project management behind the design and procurement of its replacement, Halley VI. Peter Ayres from the winning designer’s team and Hugh Broughton, their Architectural partner,write about the challenges faced in building a long-lasting Antarctic station.
The Halley V scientific research station is located on the Brunt Ice Shelf, Antarctica. Halley’s research studies are of global importance, providing information on ozone depletion, atmospheric pollution, sea level rise and climate change. Its location, since it lies within the auroral zone, is also ideal for geospace research.
Halley V is 17,000 km from the UK and inaccessible by air or sea for nine months of the year. During the remaining three months, the austral summer (December to February) when the frozen Weddell Sea has thawed sufficiently, there is a narrow window of opportunity to re-supply the station with everything required for survival in the following year. During late December there is normally a two to three week window when a ship can squeeze between the thawing pack-ice of the Weddell Sea and the sea cliffs of the continent’s iceshelves to reach Halley and discharge its cargo on to the last remnants of sea ice trapped between the headlands. By mid- January these last remnants have normally melted away leaving the ice shelves to end abruptly in sea cliffs making resupply by ship impossible. This two to three week window is the most critical link of the whole British Antarctic Survey project, having a major impact on resupply methods, construction methodology and design.
A place like no other
As its name suggests Halley V is the fifth station built by BAS during its fifty year history on the Brunt Ice Shelf. All previous stations have lasted approximately a decade before being so deeply buried within the ice shelf, due to the 1.5 m of snow accumulation each year, that they have had to be abandoned as the inexorable movement and forces of the ice have slowly crushed them.
To maintain the unbroken scientific records and the British presence in this sector of Antarctica a new station must be erected and become operational before 2010. In accordance with the Environmental Protocol of the Antarctic Treaty the old station must also be removed in its entirety, where practicable and safe. A final imperative is that the disruption to the science must be kept to an absolute minimum and with some experiments/data gathering there can be no disruption at all! These requirements have therefore set some very tight timelines for the project (Figure 1).
Figure 1 Strategic Timeline
Jan 04 to Oct 06
Project Planning, Design, Fabrication & Trials
06/07 Season
Construction Year 1
07/08 Season
Construction Year 2
08/09 Season
Move science
Mar 09
Halley VI fully operational
09/10 Season
Decommission & remove Halley V
Figure 2 Project objectives
-
Halley VI fully operational by 2010
-
Provides laboratories for world-class science
-
Compliance with the Antarctic Treaty Environmental Protocol
-
Minimal environmental impact; minimises the use of fossil fuel
-
Construction Budget of £19 million
-
Is functionally efficient
-
Provides an aesthetically stimulating environment
-
Must be re-locatable
-
Reduces the survival effort on station
-
Halley V to be decommissioned & removed from Antarctic by 2010
Strategic balance
As with all projects there has been a definite balancing act between time, cost, quality and risk. The main project driver has been time, due to a major glacial event which will have a devastating effect if the new station is not complete. The Project Brief was based on the lessons learned at Halley V and the past fifty years’ experience on the ice shelf. The Project Budget was also based on this past experience. But, perhaps in direct contradiction to this, BAS wanted a break from the past with a completely new station and a search of the construction and technology markets for innovative ideas and new ways of overcoming the problems of the past. Equally, BAS also wanted a change from the largely in-house design and construction methods of the past to outsourcing virtually all activities for this project. This again posed a conundrum: how do you outsource to the market when the UK construction expertise for works in the Antarctic is largely held in-house?
The competition
BAS ran the competition in conjunction with the Royal Institute of British Architects (RIBA) Competitions Office. It was launched in June 2004, and Stage One of the competition had a fantastic response with entries from 86 multidisciplinary design teams from all over the world.
For Stage Two, six multidisciplinary teams were chosen based on a technical assessment of company size, capacity and experience and, most importantly, the experience of key individuals. They were paid an honorarium of £10,000. The selection was deliberately arranged so that it comprised a mix of engineering and architecturally led teams, as well as large and small firms.
The concepts submitted at the end of Stage Two provided BAS with six excellent options; three based on a similar concept and three very varied concepts. This was exactly what BAS hoped the competition would provide, but it made the decisionmaking process all the more difficult.
The following concepts were selected to be separately developed with BAS, in order to turn each one into a viable station suitable for conditions in the Antarctic:
The Buro Happold
jackable three-building concept.
The Hopkins
walking building concept.
The Faber Maunsell
jackable multi-module concept.
Stage Three began with advertisements for contractors, plus a site visit for one member of each team to the existing Halley V and other foreign nation stations.
Testing the water
Although costly to BAS in terms of financing and the loss of bed spaces normally allocated to scientists, the site visit was deemed critical since it allowed the teams to experience living,working and travelling in the Antarctic, as well as the opportunity to appreciate the design of other stations. The visit was the only satisfactory way to convey the enormity of the Antarctic, the logistical difficulties and the challenging conditions. The site visit was a great success.
Unfortunately, the same could not be said for expressions of interest from contractors. Only a handful responded. Fortunately one of these,Morrison (Falklands) Ltd, has a wealth of Antarctic experience and is of a suitable size to undertake the project. It is believed the buoyant construction market in the UK, and the perceived risk of working in Antarctica, deterred many contractors.
Although all three schemes were technically viable, the Technical Panel found itself torn between the external architecture, efficiency and manoeuvrability of the Hopkins walking building, and the internal architecture, total flexibility and the processbased design of the Faber Maunsell modules. In the end the Panel recommended the Faber Maunsell scheme primarily owing to its flexibility and consideration of all the science requirements. The Jury Panel, having analysed all three schemes, also found it agonisingly difficult to choose between the Faber Maunsell and Hopkins schemes, from a technical perspective. However, combining a technical assessment with affordability, the Jury Panel finally recommended to BAS the Faber Maunsell modular scheme.
Logistical challenges for Halley VI
From the outset, it was clear to the Faber Maunsell/Hugh Broughton Architects design team that Halley VI would provide a number of key technical challenges which are particular to the Halley site. The route across the sea ice to the ice shelf is a key bottleneck in the supply route for both construction and operation. Deliveries across the sea ice are via sledge, with an allowable load of six tonnes per sledge. This places onerous constraints on the size of elements which can be delivered to site. The remoteness of the base is exceptional even by Antarctic standards, which means that severe restrictions are placed on the construction programme and annual relief operations. It was, therefore, a fine balancing act to maximise the degree of pre-fabrication in order to minimise site activities, while staying within the constraints of the supply route.
Design approach
In developing a design concept, the design team set itself the following key objectives: to develop a solution which would be relatively easy to deliver to site, build, operate and ultimately decommission; to minimise the environmental impact; to create a home from home for the scientists, a fantastic place in which to live and work, with maximum flexibility to meet the changing needs of the science.
These objectives have been achieved with a modular approach. Ski-based, jackable, single-storey elevated modules can be used for a wide variety of activities ranging from laboratories, bedrooms, food stores and recreation areas, to energy centres containing generators, fuel, water treatment plant and waste facilities. The standard module is the building block for Halley VI. When connected together, the modules form the new station.
Site layout
The station is centred on two six-module platforms. The northern platform provides the principal habitat. The southern platform contains summer accommodation (when the number of residents increases from 16 to around 60) and science modules. The summer accommodation can also serve as a safe refuge for the winter residents in the unlikely event of a catastrophic fire in the winter accommodation platform.
The key features of the site layout are:
-
The platforms are perpendicular to the prevailing wind to minimise unpredictable and unmanageable snow drift accumulation
-
Entrances to the platforms are placed in the centre to reduce circulation distances and offer choice of direction once off the ice
-
The summer and science modules are co-located in a single platform. They can share facilities and plant. This reduces the overall plant required to service the station and allows the summer modules to be maintained above freezing during the winter
-
The plant modules on each platform face each other. This removes the plant or the science modules to the north of the platform, limiting its impact on the environmentally sensitive zones for science observations
-
A pedestrian and services link bridge connects the plant modules. Two melt tanks are placed under the bridge and provide potable water. Water treatment, fuel, electrics, data and communications will be linked between the platforms
-
The link bridge helps to link summer residents with the main platform
-
The southern-most science module provides a clear panoramic view for meteorological observations
-
The northern-most winter sleeping module includes a quiet lounge with panoramic views where residents can escape from the throng of the main social spaces.
Architectural layout
As there is no internal structure – support is provided around the perimeter – the modules are extremely versatile, allowing layouts to be reconfigured to suit changing science programmes or operational drivers. Windows to all rooms allow views of the ice, while making the most of natural light during the summer.
The majority of activities which take place at Halley can be provided for using a repeat standard module. However, there are some activities at the station which are constant, and require a special approach. Eating, drinking and recreation are the activities that lie at the heart of life at Halley, so the spaces associated with these activities need to be located together. They also need to respond to the changing population of the station between summer and winter. These activities are accommodated in a special two-storey central module, the major destination at the station. This module’s plan maximises flexibility, allowing for many activities, by incorporating movable acoustic partitions which enable the lower floor either to be divided into a number of cellular spaces or converted into a large open plan area. A hydroponics installation within a glasshouse at the centre of the atrium will provide the refreshing sight of greenery at the very heart of the station – an unexpected moment of spatial drama.
Structural concepts
The structural design is based on simplicity, standardisation and buildability. The modular structure is designed for easy transport to site, to minimise the annual maintenance effort to overcome snow accumulation and for easy relocation to another site.
The structural subframe of the modules will be formed from a lightweight steel space frame. The subframes will be prefabricated, shipped to site and offloaded onto the sea ice as one complete unit with legs and skis attached and with primary building services pre-installed. From there, they will be towed across the sea ice and up onto the ice shelf proper.
The skis are critical to the success of the design approach since they allow the subframes to be delivered without the need for sledges. The existing BAS sledges weigh 3.5 tonnes, therefore by eliminating the need for a sledge it is possible to increase the allowable mass of a subframe from 6.0 tonnes to 9.5 tonnes. Without the skis it would not be possible to deliver pre-assembled frames of sufficient size to create an efficiently planned module. The skis also act as spreader beam foundations; each ski fits into a steel crampon which provides a shear key to the ice to avoid unwanted sliding of the modules when in their permanent location.
Ductile steel
The steelwork on Halley VI will be subjected to extremely low temperatures, and achieving the correct toughness is important for the avoidance of brittle fracture. For the skis and crampons, which are fabricated from plate, grade S355NL steel is specified.This is a finegrained steel readily available as plate. For the remainder of the steelwork, the toughness will be specified along with the yield strength and other properties, and the steel will be milled to order. All the steel for the Antarctic needs to be able to endure extremes of high temperature on its weeks long boat journey to the South Pole, as well as the extreme wind chill factor it will face in situ on Antarctic glaciers.
A simple steel goal post frame forms the superstructure of each standard module. Floors are formed from prefabricated composite timber cassettes which can be quickly slotted together on site. Preformed floor hatches will give access to services within the belly of the modules.
The cladding needs to be erected quickly, safely and efficiently whilst providing a robust construction with resistance to the passage of cold air, moisture, snow spindrift, thermal shock and high levels of ultraviolet light. It will be formed from relatively lightweight glass reinforced plastic (GRP) insulated panels, similar to those commonly used on commercial aircraft, trains and boats.
Crucially, all the elements are prefabricated and mechanically fixed, and the repetitive modules use fewer different construction components. This means that the work can be undertaken by a multi-skilled labour force, which will remove critical paths from the construction programme and allow great flexibility in planning the works — a crucial aspect given the uncertainties over weather and other working conditions. If all goes to plan, this prefabricated, modular approach means that the entire station can be in place and weather-tight within just 35 days of arrival on the ice.
Snow accumulation
The Halley site is subject to up to 1.5 m of snow accumulation every year. Since the snow does not melt, any surface based building will ultimately be buried and crushed. Halleys I to IV were all subject to this fate. The current station, Halley V, is raised above the surface and is jacked up on its supporting legs every year. However, this is a hugely labour-intensive operation involving extending and re-welding the steel legs, and entails a crew of six steelwork erectors working an entire summer season every year. Another disadvantage of
Keep up-to-date with Ingenia for free
SubscribeOther content from Ingenia
Quick read
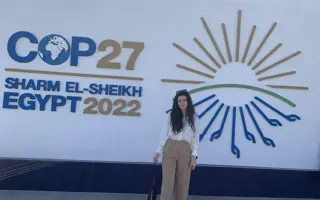
- Environment & sustainability
- Opinion
A young engineer’s perspective on the good, the bad and the ugly of COP27

- Environment & sustainability
- Issue 95
How do we pay for net zero technologies?
Quick read
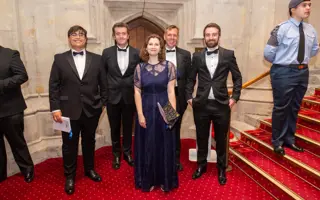
- Transport
- Mechanical
- How I got here
Electrifying trains and STEMAZING outreach
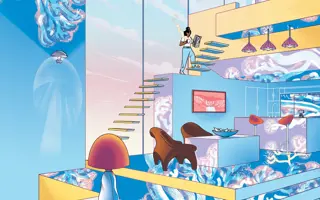
- Civil & structural
- Environment & sustainability
- Issue 95