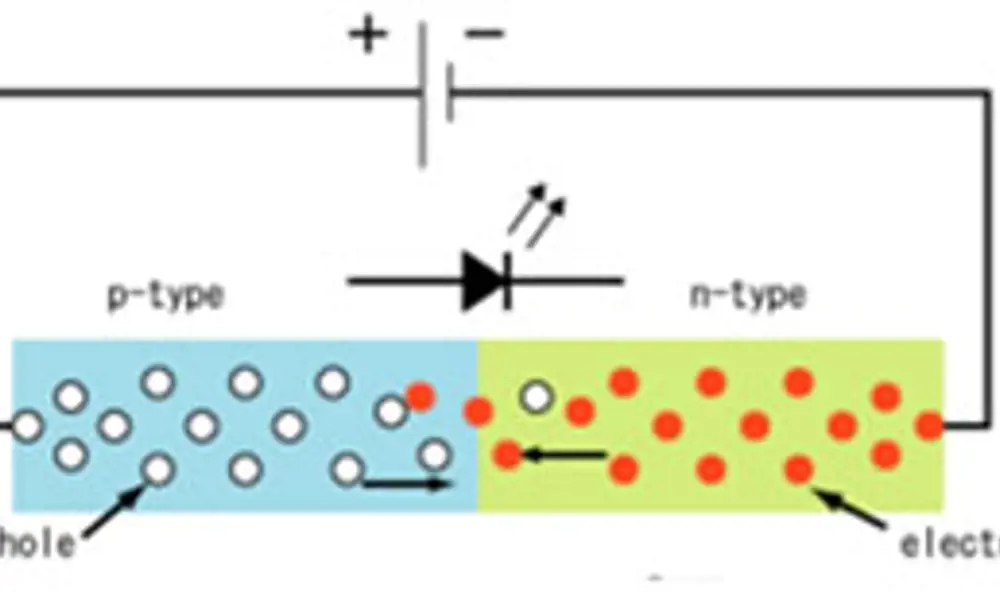
Changing lightbulbs
The inner working of an LED
There is intense competition between the manufacturers of light-emitting diodes to win orders from the makers of lighting systems to replace conventional bulbs.
As the efficiency of light-emitting diodes rises and production costs fall, they are being used in their billions as backlights for screens in mobile phones, televisions and laptop computers. Now LEDs are making inroads into one of the most lucrative lighting markets of all, the light bulb. DrRichard Stevenson, editor of Compound Semiconductor magazine, reviews the rapid rise of the LED.
For more than a century, the incandescent glowing filament light bulb was the dominant source of electric light. Today, it is the LED that is rapidly becoming the illumination technology of choice. This semiconducting light source is making inroads into commercial and domestic lighting, with its promise of huge energy savings and much longer lifetimes. LEDs have come a long way since the 1970s when they were manufactured as low-voltage indicator lamps for integrated circuits.
A driving force in the progress of LEDs has been the demand for more efficient light sources that can match the light bulb’s luminescence. At its best, an incandescent bulb delivers around 12 lumens/watt (lm/W). The compact fluorescent lamp brought some progress with a light output of around 75 lm/W, using as much as 75% less energy than an incandescent bulb – but it does contain mercury. Commercial LED bulbs now deliver up to 100 lm/W, with the potential to become even brighter.
The production of LEDs accelerated rapidly in the 1990s, when they appeared in the backlights and keypads of mobile phones. They were also incorporated into traffic lights and replaced bulbs in the brake lights of cars. LEDs can even deliver the absolute levels of brightness needed for a car’s headlights, while many companies are using them in backlights for computer monitors, televisions, satellite navigation systems and tablet computers.
LEDs are now set to enter a new market that promises to be the biggest yet: domestic and industrial lighting. Sales for this use are small today, but analysts are tipping LED-based bulbs to revolutionise the lighting market by 2020. With lighting accounting for more than 15% of electricity and up to 40% of household use, the efficiency of LEDs has the potential to trim the electricity bill for households and commerce while reducing carbon dioxide emissions. What is more, LED light bulbs last 25times as long as incandescents, and more than twice as long as compact fluorescents.
The rise of the LED owes much to the expansion of its colour palette, along with increases in brightness and efficiency. This progress came through the development of semiconductors that allow LEDs to emit light over a broader part of the visible spectrum than the narrow band of red light used in those early indicators.
Further progress came through changes in the design of the devices so that rather than trapping light internally, they release a far higher proportion of it. Modern designs can let out almost 80% of their light, compared to around 12% for conventional LEDs.
Enlightened times
The understanding of how an LED emits light goes back to the early days of semiconductors when, in 1951, a team of American researchers at Signal Corps Engineering Laboratories, New Jersey, described its behaviour. The following year, Heinrich Welker produced the first gallium arsenide crystals at Siemens, an advance that provided a substrate for developing the first LEDs. The substrate is the platform for making an LED, which is formed from the growth of a stack of thin films on to this material.
Initially LEDs just emitted in the infrared spectrum, but by the 1970s, devices featuring films of gallium phosphide (GaP) and gallium arsenide phosphide (GaAsP) could emit red, yellow, orange and green light. These devices, though in themselves too low-powered to do more than just provide status indicator lamps, were the forerunners of the LEDs used in brake lights and signs on railway stations. These are based on aluminium indium gallium phosphide (AlInGaP), a material with high light-emitting efficiencies.
These materials can produce a wide range of colours, but they still leave an important hole in the visible spectrum: they cannot emit blue light. This is a major weakness: blue light is essential to create LEDs that emit the white light needed to backlight screens or power light bulbs. Most of the white LEDs produced today feature a chip that emits blue light. By applying a yellow phosphor coating on the chip, the blue and yellow light mix to produce white light.
The breakthrough for blue-emitting LEDs came from Professor Nakamura, a lone researcher at the Japanese firm Nichia Chemical Industries. In 1993, he made an LED based on the semiconductor gallium nitride (GaN), until then a notoriously difficult material to process. Nakamura’s LED was 10times more efficient than its forerunners and was also better at controlling the internal current flow.
Within a few years of the birth of the white LED, devices manufactured by Nichia and several rivals were backlighting mobile phones. However, the commercialisation of Nakamura’s discovery, which earned him the 2006 Millennium Technology Prize, did not initially lead to LEDs bright enough for powering lightbulbs. To do that, semiconductor engineers had to overcome a number of obstacles.

To improve the efficiency of LEDs, engineers produce them with processes that enable more light to get out of the device. A mirror beneath the LED stops light getting out in this direction, where it would be wasted, while roughening the top surface increases the light extraction in this direction © Richard Stevenson
Fine tuning
One weakness of an LED is that it behaves in a similar way to a glass block. Some of the emitted light fails to emerge because of internal reflections and reabsorption on the substrate. To stop this happening, semiconductor engineers have devised two different ways to make LEDs.
One approach begins with the same process used for making conventional LEDs, namely the growth of a stack of thin films on a substrate. However, instead of simply cutting up the substrate to form a collection of chips that can be processed into LEDs, a highly reflective metallic layer deposited on top of the stack of thin films acts as a mirror. After the structure is turned over, a laser separates the substrate from the semiconductor film, leaving it with a roughened surface. After contacts are applied, the result is a far more efficient device: the mirror stops light from leaving the chip in the wrong way, while the roughened surface makes it far less likely for photons to be reflected back into the device. Instead, more of them are extracted from the LED.
A different approach to overcoming trapped light is tackled by etching a very fine pattern into a substrate’s surface. This surface modification, which does not require substrate removal with a laser, prevents light from bouncing around in the LED. Both approaches have their advocates and both have efficiencies exceeding the ‘greenest’ bulb of recent times, the compact fluorescent lamp (CFL).
The CFL has never been universally popular, despite delivering an efficiency that is typically five times that of the prevailing lighting source of the 20th century, the incandescent bulb. These traditional bulbs convert just 10% of their electrical input into light, losing the rest as heat.
The CFL’s perceived faults are that it emits an undesirable green-tinted form of white light, takes a long time to warm up and is often incompatible for use with dimmer switches. While CFLs can outlive traditional light bulbs, they cannot come near the lifetime of the LED, which promises to last so long that the whole idea of changing a bulb becomes redundant, a significant advantage in locations where the cost of replacing a light far outweighs the cost of the bulb itself.

Epistar is making white-emitting LED packages by first bolting red and blue LED chips together, as shown here. This collection of chips is then coated in a yellow-emitting phosphor. This combination of red LEDs, blue LEDs and a yellow-emitting phosphor has stronger emission at longer wavelengths, which gives the light a warm hue that is similar to that produced by an incandescent bulb while still delivering high efficiencies © Epistar
The L Prize
While the LED avoids these drawbacks, a flood of shoddily made LED light bulbs onto the market could create public scepticism about the technology’s benefits. In May 2008, to try and prevent this, the US Department of Energy (DoE) launched the L Prize competition “to spur lighting manufacturers to develop high quality, high efficiency solid-state lighting products to replace the common light bulb”. One category was to build a replacement for the 60 W incandescent bulb with a prize of up to $10 million for the winner. Criteria for winning this competition included demands that the winning LED should draw less than 10 W, last for 25,000 hours (25times longer than a typical incandescent bulb), produce great colour quality and emit light in all directions.
In August 2011, the DoE declared Philips Lumileds as the first winner of the L Prize after the company submitted 200 bulbs for testing. Scrutinising a subset of these bulbs revealed that they drew an average power of just 9.7 W, with an output of 93.4 lm/W. Accelerated testing determined that their output would fall by less than 1% if they were left on for 25,000 hours. These bulbs easily exceeded the metric for colour-quality, with anecdotal evidence suggesting that the human eye could not distinguish the difference in colour produced by this prizewinning LED lamp and an incandescent bulb, which is renowned for delivering uniform emission. Philips’ engineers achieved this by decoupling the blue-emitting LED chips from their yellow phosphor coating and putting the phosphor close to the outside of the bulb. The phosphor acts as a diffuser, making it impossible to identify the light emitted by any of the bulb’s 18 LEDs.
The judges of the L Prize also evaluated robustness, subjecting the LEDs to temperature extremes, high levels of humidity and fluctuations in the supply voltage. All the LED-based bulbs passed this examination, while every CFL in the test failed.
The prizewinning bulb went on sale in 2011 in the US for $60, with rebate schemes offering considerable discounts on the list price. While Philips and other manufacturers also sell cheaper LED bulbs with slightly lower efficiencies, prices are still much higher than many consumers are willing to pay. High chip costs are to blame, with LEDs accounting for more than half the cost of the bulb.
The two options available to bring prices down are to reduce chip manufacturing costs or to drive more current through the devices so that they emit more light. While the second option draws on less of the world’s resources, increasing the amount of current through today’s LED would result in a fall in efficiency, as a result of a mysterious malady known as ‘droop’. Understanding what causes droop and how to prevent it will determine how to reduce the number of chips in a bulb. It would not be acceptable to cut chip costs by running LEDs less efficiently, because that would take away the main selling point of this type of lighting.
Rectifying droop
Researchers in industry and academia have been working to understand the cause of droop, with a plethora of publications claiming to explain the droop, although no one has yet provided a watertight explanation. However, several research groups have developed devices with different layers that can reduce the impact of LED droop.
Manufacturers are also working on ways to reduce LED manufacturing costs. One approach is to use silicon as the substrate rather than sapphire or silicon carbide, the most common materials used today. This substrate is far cheaper, and would allow underutilised silicon foundries, built many years ago to make the cutting-edge computer chips of their day, to manufacture LEDs.
Unfortunately, growing high-quality LED material on silicon is loaded with difficulty. One of the biggest issues is that the production of devices emitting blue light requires depositing nitride layers on to silicon at 1,000°C. The multi-layer film and the silicon substrate contract at different rates as they cool to room temperature. As a result, a wafer can be flat during material deposition, but as it as it leaves the growth chamber and cools to room temperature, the wafer experiences severe bowing. In the worst cases, the nitride film cracks and cannot yield working LEDs.
One way to produce flat wafers is to monitor their curvature during growth with an instrument that directs a laser onto the wafer surface and measures the angle of reflectance. This tool has helped engineers to learn how to insert layers beneath the LED to control the shape of the wafer.

Strawberry plants growing in a multi-layer system in LED4CROPS at Stockbridge Technology Centre. The potential for strawberry propagation and production in a multi-tier system is being evaluated using Philips Greenpower LED Production Modules
Horticultural use of LEDS
In addition to their many uses in electronic devices and domestic lighting, LEDs are finding new applications in horticulture and agriculture. They have the potential significantly to increase crop yields and reduce energy consumption. Worldwide trials show that LEDs can be used to grow crops in multiple layers inside buildings without overheating. This could allow local agriculture to thrive in high-density urban areas, where arable land is expensive and scarce. Water use efficiency is much higher in such systems, owing to minimal losses from evapotranspiration and through collection and recycling in a closed-loop system.
LEDs can also extend the growing seasons in countries at northern latitudes, where weather conditions and seasonal daylight fluctuations are extreme. Stockbridge Technology Centre is working with Philips, a leader in adapting LEDs for horticulture, and Cambridge HOK in the UK on a range of crops to create ‘light recipes’ for a range of individual crops under the framework of LED4CROPS. It is already clear that crop production and quality can be increased significantly and better scheduled irrespective of the external climate.
Because of their low heat output, LEDs can be placed close to the crop where conventional growing lamps cannot go, thus allowing multi-layer production systems to be developed. In addition, Philips’ interlighting systems stand horizontally between rows of tall plants, such as tomatoes, with light reaching the lower leaves that would otherwise be heavily shaded by the crop canopy above them, and therefore less efficient photosynthetically.
By controlling the wavelengths of light produced by LEDs, growers can also optimise lighting to benefit particular crops, as each responds best to specific spectra. Currently, LED use is being tried with a number of crops including tomatoes, peppers, lettuce, strawberries and several species of flowers. Further research will investigate how to tailor light delivery to increase growth rates, improve plant quality and increase the nutritional content of many other crops.
UK LED Manufacture
The research group led by Professor Sir Colin Humphreys FREng at the University of Cambridge has mastered the growth of gallium nitride (GaN) LEDs on 6-inch silicon substrates, which will substantially reduce their cost. It has also succeeded in reducing the high density of defects in such LEDs, which significantly increases their efficiency. Thus low-cost high-efficiency GaN LEDs on large-area silicon can now be grown, which will enable the widespread adoption of LED lighting in our homes and offices. This has the potential to save the UK about 10% of its total electricity use and about 10% of the carbon emissions from power stations.
Humphreys’ group set up a spin-off company, CamGaN, to exploit their technology, which was acquired by Plessey Semiconductors in 2012. Three of Humphreys’ postdoctoral researchers are working with Plessey to transfer the technology and the company is aiming to manufacture 2 million LEDs per week at its factory in Plymouth, with commercial production due to start later this year.
This will be the first ever manufacturing of LEDs in the UK.
Plessey has yet to unveil results for its devices. However, there is evidence that LEDs on silicon can offer a performance that is close to their conventional cousins. Gallium-nitride-on-silicon (GaN-on-Si) devices produced by the US firm Bridgelux have an efficiency about 10% below that of the leading commercial devices and have demonstrated a light output of 135 lm/watt. Toshiba now uses Bridgelux’s process to make LEDs that will compete with those launched by Plessey. In this race for commercial success, one advantage that the UK firm has over this rival – and others developing GaN-on-silicon LEDs – is that it uses a far thinner stack of layers between the substrate and the LED, which reduces the stresses within the structure and trims the production costs.
Brighter future
From a consumer perspective, which company goes on to be the most successful GaN-on-silicon LED manufacturer is not important. The desire is to see firms creating LEDs that deliver the efficiencies required to make high-quality, competitively priced light bulbs. That will increase the LED content in our homes so that they can be used in all types of lighting.
The growing pressure to tackle climate change is also likely to drive down the costs of making LEDs. Even if they do not match the price of existing lighting technologies, the rising cost of electricity will make LEDs more attractive. For example, one estimate is that advances in LED technology could reduce the wattage of airfield lighting by up to 90%. When San José in California switched to LED traffic lights, its annual costs fell by nearly $1.7 million to $160,000.
These potential gains have persuaded some governments to spend money on programmes to encourage the development of the technology. For example, South Korea, a major maker of LEDs, has established a $6 billion stimulus package to promote green homes which includes LEDs for lighting in public facilities. The US Department of Energy has estimated that rapid adoption of such lighting in the US over the next 20years could reduce electricity demand for lighting by 33% which would represent a tremendous saving in energy.
Keep up-to-date with Ingenia for free
SubscribeOther content from Ingenia
Quick read
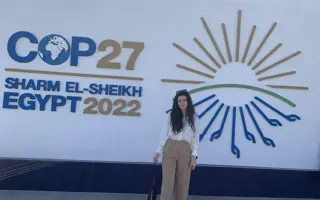
- Environment & sustainability
- Opinion
A young engineer’s perspective on the good, the bad and the ugly of COP27

- Environment & sustainability
- Issue 95
How do we pay for net zero technologies?
Quick read
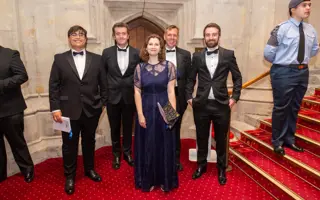
- Transport
- Mechanical
- How I got here
Electrifying trains and STEMAZING outreach
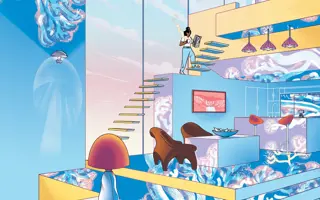
- Civil & structural
- Environment & sustainability
- Issue 95