Colossus demolished
Purpose built
The hammerhead cantilever-design crane had been constructed in the 1970s to carry out lifts when nuclear submarines were being refitted and refuelled. It was located in the centre of the Submarine Refit Complex at Devonport, spanning the central office structures between two docks (Docks 14 and 15). It also served the central promontory area comprising assorted workshops, training and storage facilities.
The crane comprised a steel lifting arm structure (jib) supported on a rotating platform and mounted on a concrete plinth built on four 2 m2 reinforced concrete legs at 13.5 m2 centres that extended down to bedrock. The total height, from the base of the foundations to the top of the structure, was 81 m.
The main hoist had an 80 metric ton lifting capacity at its 72 m maximum reach, while the auxiliary hoist had a five metric ton capacity at 67.5m maximum reach. With the inclusion of 333 metric tons of cast iron ballast situated in racks at the rear of the machinery house, the crane jib weighed a hefty 1450 metric tons.

The Devonport crane in its heyday © Babcock International Group
The Life of the Devonport colossus
Commissioned in 1977, the Devonport submarine refuelling crane was built as part of the Submarine Refit Complex, which was established to refuel the Royal Navy’s Swiftsure-class nuclear submarines that were launched throughout the 1970s, and later the Trafalgar-class submarines commissioned in the 1980s.
Constructed by crane engineering specialists Stothert & Pitt in a giant cantilever, or ‘hammerhead’, design, the Devonport crane was used to lift large items of plant, equipment, and containers used while removing and replacing fuel modules – a job it undertook for 30 years until its final refuelling, of the Trafalgar-class nuclear attack submarine HMS Triumph, in April 2008.
Hammerhead cranes are typified by a large, horizontal, double-cantilever placed on top of a steel or concrete tower, with the forward part of the cantilever carrying a lifting trolley, and constructed in large sizes up to 350 tons. Such huge hammerhead cranes were once common throughout the world’s dockyards, where they were mostly used to install large armour plating and guns for battleships, but now only around 15 remain in the world, about seven of which are in the UK.
The dismantling of the Devonport crane marks the end of an era in another sense, with the last refuelling of an SSN (Ship Submersible Nuclear). In the future, the new Astute-class SSNs are being built with submarine lifetime cores, so will only require final defuelling.
Weighing the options
The crane removal team considered various options to remove this sizeable structure in the safest and least disruptive manner. The usual approach in removing a large elevated fabricated structure such as the Devonport refuelling crane is to undertake disassembly in the reverse sequence to that employed in its construction.
For this to take place, the crane mass must remain balanced on its central bearing support and material must be removed in an alternating sequence from each end, starting at the ‘nose and tail’ extremes and working inwards to the central bearing unit, maintaining balance within a tolerance band at all times.
This piecemeal approach would have involved separating over 200 sections of around eight metric tons each. A similar method was used by Babcock to successfully remove a large hammerhead dockside crane at Rosyth in 2007 and so we knew that crawler cranes would have been required on the dockside to lower to the ground any removed material, which would have needed a lot of time to carry out.
It was thus decided that the removal of the jib (the crane’s lifting arm) in one piece was the most attractive option but the question remained as to how to actually achieve it.
A solution emerges
In pursuing the one-piece removal option, our research considered ship- and barge-based cranes that have been used to lift structures weighing several thousand metric tons in the oil and gas industry. The problem for us, though, was one of access. No lift vessels were found that could achieve the required load lift and reach radius on a craft that was able to access the Devonport dockyard – given the entrance water width and depth restrictions.
An alternative technique was to use a land-based crane erected on site. Land-based crane capacity, lack of available space on the dockside, and ground bearing load limits proved to be issues here and were initially thought to rule out this approach until a ‘traverse and lower’ option was proposed by Dutch heavy lifting specialists Mammoet (meaning ‘mammoth’).
The elegance of the Mammoet solution lay in using a set of their existing support beams in tandem with the high load capacity of the crane legs and the reinforced concrete strengthened dock walls in 15 Dock, which are designed to resist a worst-case once-every-10,000-year earthquake.

Four support towers and beams were erected to support the massive weight of the crane jib © Babcock International Group
A plan is formed
The idea was to use four enormous temporary towers founded at dockside level, two on either side of 15 Dock. High-level main gantry beams would span from the pedestal to the eastern towers (the very lift beams, extended for this application, that had been used to raise the stricken Russian submarine K-141 Kursk from the floor of the Barents Sea in 2001 – another project in which Mammoet was involved).
Measuring around 40m long and positioned to align with the crane’s concrete pedestal, the beams would span from the pedestal onto the eastern towers. Shorter lowering beams, approximately 25m long, would span at high level across the dock from the east to the west towers.
In addition, four bespoke jacking brackets attached to the crane would enable the crane jib to be jacked up free of its rotating platform using specialist jacking and skidding equipment, allowing the jib to be slid slowly, inch by inch, across the gantry beams until positioned over the dock, where it would be supported by the shorter beams. The jib and short beam supporting cradle would then be lowered directly onto a barge in the dock using heavy-lifting hydraulic strand jacks mounted on the towers.
This one-piece removal method had significant advantages in terms of two critical considerations: safety and efficiency.Whereas piecemeal methods would have taken nine months and involved long-term relocation of some 600 people from the offices below, the one-lift approach required a programme of just four months. This allowed the offices to remain occupied with only short exclusion periods during crane lifts over buildings, when the area was evacuated.
In addition, the method reduced the number of man-hours spent working at extreme height by a factor of 10, helping to make this a safer option.
Removing the crane
Tower construction progressed rapidly during the summer of 2008, despite high winds occasionally delaying progress. The main support beams arrived at Devonport, as did the barge onto which the crane would be lowered. With the tower structure erected, independent installation checking complete, and a good weather window confirmed by the Met Office, the removal commenced on 27 September 2008, at 7.30am.
The first few metres across the crane plinth to tower connection were perhaps the most demanding and slowest stage.While traversing the top of the crane platform, the crane was supported on a two-beam and sliding jack arrangement. On the main tower structure, however, two additional inner beams and sliding jacks were engaged and enabled a transition to load sharing over four beams. This was reversed and the inner beams and jacks were disengaged as the crane crossed the connection onto the lowering cradle over the dock.
After about seven hours, the crane was in position on the pinned lowering cradle. Following installation of the inner strand jacks the cradle pins were disengaged and the lowering operation began. Some six hours later (by now around 2.00am the following morning) lowering was held and secured at about a metre above the barge, with final lowering into position on the barge re-commencing at 7.30am with the onset of daylight visibility. The process was completed two-and-a-half hours later.
Phase Two
The next phase was to tow the barge and crane away from 15 Dock, to a site at the south-east end of Devonport’s 5 Basin, where the crane would be broken up. To remove the barge from the dock, the towers on the western dock wall had to be removed to allow the overhanging lowering beams to pass over the dockside. Again, with such a large sail area created by the crane structure, a careful focus on wind conditions was required to manage the stability of the barge against wind loading.
Basin levels had to be raised by pumping water into the basin to achieve alignment between the barge deck and land. After disassembly of the towers and, once again, confirmation of an appropriate weather window by the Met Office, the move across the basin took place successfully 11 days after completion of the lowering project, and the final move from barge to shore was achieved the following day.
Transferring to shore
Although it seemed the most straightforward stage of the operation, transferring the crane to shore was arguably one of the most exacting challenges. The crane was jacked up and slid across two beams straddling from the barge to the shore.The barge had to be ballasted by pumping water around internal tanks to maintain both the correct righting moments and barge levels while the crane weight firstly moved off-centre and then transferred off the barge onto the shore.
Had the barge floated up as the weight came off, the resulting slope of the crane, in conjunction with the low-friction sliding pads, would have resulted in the crane sliding uncontrollably towards the dockside.
New facilities
Ultimately, the process was slowly, safely and successfully completed and, with the crane on shore and at ground level, disassembly could begin. Having passed all company and independent radiological surveys (and clearance for the presence of asbestos and other hazardous materials), crane dismantling works continued through into January 2009, after which it was smelted and recycled for re-use.
With this latest project completed, work can now continue on the Future Nuclear Facilities programme at Devonport, due for completion in 2012. In the meantime, with no submarines being defuelled in the interim, it is business as usual at Devonport and its facilities will continue to support submarine maintenance programmes. The crane itself will be replaced with a new state of the art, low-level reactor access house, marking the end of one era and the start of another.
Future Nuclear Facilities at Devonport
The Ministry of Defence is investing some £230 million in the Future Nuclear Facilities programme at Babcock’s Devonport Royal Dockyard, announced in August 2007. The programme is made up of a number of projects under a partnering agreement between Babcock and the MoD. It consists of the Defuel, De-equip and Lay-up (DDLP) preparations project, and the Fleet Time Docking project.
The DDLP project includes three key areas: the Reactor Access House, including the travel and alignment system along which the access house moves from its parked position; a defuelling crane housed within the access house; and defuel tooling. Following completion of design reviews and hazard and operability studies in July 2008, the project is now nearing the end of the detailed design phase. Jacobs Engineering is developing the Reactor Access House structure and travel and alignment system; Babcock BNS Bristol is finalising the integral access house crane design and Rolls-Royce is developing the defuelling equipment.
The Fleet Time Docking project will provide a facility within the Submarine Refit Complex to carry out improvements in the vacant periods in between submarine maintenance and includes removal of the high-level refuelling crane, as well as production of a facility safety case and removal of items of equipment that required lifting before the crane went out of service. Future packages will include civil alteration works to accommodate the new DDLP equipment; provision of a docking capability for the new Astute-class submarines within the refit complex; and redundant facilities equipment disposal.
Completion of the Future Nuclear Facilities programme is scheduled for 2012, when the facility will be operational. The new facility will be able to perform the defuelling of decommissioned Swiftsure-class and, in the longer term, Trafalgar-class nuclear powered attack submarines. Babcock is the contractor completing the programme and will be owner and operator throughout the submarine decommissioning.
BIOGRAPHY – Malcolm Smith
Malcolm Smith is Babcock’s Special Projects Director, and leads the Babcock element of the Future Nuclear Facilities programme at Devonport Royal Dockyard. A Chartered Engineer and Fellow of the Institution of Mechanical Engineers, he has over 25 years experience in the naval nuclear programme, working on design and safety substantiation of nuclear reactor systems and support equipment. He was technical director on the Devonport facilities redevelopment programme, known as the D154 project, to upgrade the nuclear submarine refit and maintenance facilities, which was completed in 2002.
Keep up-to-date with Ingenia for free
SubscribeOther content from Ingenia
Quick read
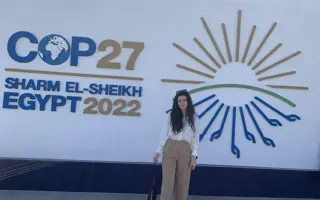
- Environment & sustainability
- Opinion
A young engineer’s perspective on the good, the bad and the ugly of COP27

- Environment & sustainability
- Issue 95
How do we pay for net zero technologies?
Quick read
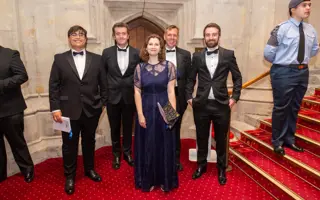
- Transport
- Mechanical
- How I got here
Electrifying trains and STEMAZING outreach
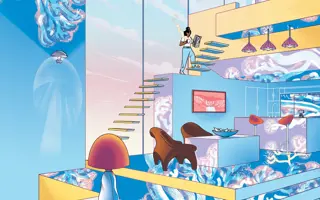
- Civil & structural
- Environment & sustainability
- Issue 95