Constructing the Hindhead Tunnel
The second longest road tunnel in the UK was completed in July2011. The £371 million project, which has relieved congestion around Hindhead in Surrey, had a wide range of engineering challenges to overcome. Ingenia asked Paul Arnold, Senior Project Manager at the Highways Agency and Paul Hoyland, a project director with Balfour Beatty, about how they came to satisfy the many stakeholders involved.

The natural amphitheatre known as the Devil’s Punchbowl, skirted by the old A3. The road will be returned to nature and replaced with sandstone excavated as part of the tunnel dig, reuniting the Punchbowl with Hindhead common for the first time in nearly two centuries © Highways Agency/Balfour Beatty
‘The A3 Hindhead improvement’ is a modest title for a construction project that has eliminated a notorious road bottleneck, improved the environs of the village of Hindhead and safeguarded an important area of outstanding natural beauty. It is not only the works themselves, but the partnerships formed on this sensitive project that have won approval from the people and organisations who had previously been most concerned. In brief, the road improvement involved eliminating the bottleneck of the A3/A287 crossroads at Hindhead, moving 30,000 vehicles per day away from the old A3 on the shoulder of the Devil’s Punchbowl and into a new tunnel beneath Hindhead Common. With the completion of the project, all of the A3 between London and Portsmouth is now dual carriageway.
The form of by-pass that made these improvements possible is a twin-bore tunnel, chosen for environmental reasons, consistent with the scheme’s whole design to minimise damage to the local natural environment. The necessary corollary of this was working closely with landowners such as the National Trust, environmental bodies and local communities.
The Devil’s Punchbowl is a great natural amphitheatre owned by the National Trust. Much of the Hindhead Common land is within a site of special scientific interest and areas that are not protected are occupied by housing.
Improving the existing road was not an option because it would have required the demolition of historic buildings in Hindhead. At the northern end, widening the road around the shoulder of the Devil’s Punchbowl would have been both difficult and damaging to the environment. The solution was to construct a bypass, protecting the most environmentally sensitive part of the route by placing the road in tunnel.
At 1.8 km, the Hindhead tunnel is the second longest road tunnel in the UK (after the Queensway Tunnel under the Mersey estuary) and is special because of the exceptional care taken to preserve the local environment.
Early considerations
In October 2002, the Highways Agency awarded an ‘early design-and-build’ style contract to Balfour Beatty Major Projects, whose team included Mott MacDonald as their design partners. With Atkins being consultants to the Highways Agency, these organisations formed the A3 team that delivered the scheme to time and budget. The works started in January 2007 and the road was fully opened in July 2011.
Early contractor involvement enabled the design to be developed between client, designer and constructor in the best way for efficient construction and long-term reliability. It also allowed time for complex and emotive environmental concerns to be considered rationally and effectively. Although this article is primarily concerned with the tunnelling works, it also gives examples of specific measures taken to preserve the local environment.

Soil nailing at the Hazel Grove cutting. The steepness of the walls helped minimise the land take of the tunnel and shield the road from the surrounding environment © Highways Agency/Balfour Beatty
Tunnelling decisions
Site investigation had shown that the ground along the proposed tunnel route was a mix of sandstone and sand, with more clayey sand (sand with clay) towards the southern end of the tunnel. The water table along the route was mostly lower than the bottom of the tunnel, meaning that the works would be almost wholly dry.
The challenge with tunnelling is how to excavate the tunnel without the face, roof or walls collapsing as the works progress. In this case, the method chosen was a variation of the method known as NATM (New Austrian Tunnelling Method). In NATM, as the tunnel is advanced, sprayed concrete is used to provide rapid, temporary support to the walls and roof prior to a structural lining being installed. In the Hindhead tunnel, a variation of the technique known as Sprayed Concrete Lining (SCL) was used. This differs from NATM in that the lining is fully designed before work starts, and is applied based on a ‘menu’ of predesigned support solutions, which also provide the permanent structural lining of the tunnel. These pre-designed support solutions included leaving a temporary bench in front of the face and (in more sandy ground) installing inclined perforated pipes into the roof of the tunnel (called canopy tubes) that can be filled with cement grout to form an arch protection over the tunnel roof (Figure 2). The horseshoe shape of the tunnel could be dug using a modified standard excavator instead of a tunnel boring machine. The horseshoe shape saved around 20% of the volume of soil and rock that had to be removed and disposed of (and around £15 million in cost) compared to the circular tunnel that a boring machine would have made.
The decisions about which support method should be used in the different ground conditions being encountered during the tunnel construction were taken at daily review meetings at which data from observations and measurements were examined. The data included tunnel settlements and internal convergence (the inward movement of the tunnel walls), surface settlements, geological face logs, records from probing ahead of the tunnel face, sprayed concrete time and strength records, and quality, environmental and tunnel inspections. The review resulted in the issue of formal instructions for excavation and support, in effect a permit to dig. Additional but not reduced support measures could be provided if deemed necessary.
A significant innovation was to use the sprayed concrete lining to carry the residual permanent ground load after the initial redistribution of stresses as the ground arched around the excavation – to become the primary lining. Traditionally, the original sprayed lining has been a temporary lining, and the secondary lining has provided the structural strength of the tunnel. In the Hindhead tunnel, the initial sprayed lining is also the structural lining. This was made possible by developments both in excavation and in spray mixes. For the primary lining to be structural, it needs a regular section, and to be at least 200 mm thick. Lasers were used to guide the excavation, make it more accurate, and to ensure that the thickness of the sprayed concrete was even. Advances in the additives that can be put in the sprayed concrete also made it far easier to control its application. The primary lining was reinforced with steel fibres.
Advance rates had to be consistent therefore with the concrete’s gain in strength with time. In addition, the lining material had to meet performance requirements of energy absorption, water penetration, drying shrinkage, as well as construction requirements for pumpability and retardation of set.
With a structural primary lining, it was then necessary to add a waterproofing layer and a secondary lining to provide a smooth, reflective internal surface – but one that would act as a vehicle restraint. Normally, the whole of the secondary lining has been cast, requiring a shutter that takes up the entire volume of the tunnel. But in this case, only the lower section of the tunnel lining, where the vehicles will run, was cast. The upper section was sprayed, just like the primary lining. This offered a considerable saving in time, as casting the roof section is always the most difficult part of the job.
Robotic technology was used for the sprayed concrete of both the primary and the secondary lining, meaning that workers could remain well back from unsupported areas, reducing potential hazards. The timescale for installing the lining was considerably reduced in comparison to shuttering the entire tunnel.
The health and safety of construction staff is always a primary concern in determining the tunnelling method. The dust produced from the Hindhead tunnel excavation was a fine crystalline silica. The Health and Safety Executive has strict controls on the amount of dust and of the nitric oxide and nitrogen dioxide generated by the plant and machinery. Rather than a road-header – a rotating disc on the front of an excavator – a modified standard excavator with two teeth was used, which cut or ripped away the rock in blocks, creating less dust. The teeth had to be replaced daily. The levels of nitrogen oxides can be removed with ventilation, but greater air movement would increase its dust content. These had to be carefully balanced along with appropriate selection and maintenance of the construction plant.
Fire protection
Fire is a hazard in tunnels that must be taken into account because the impact of vehicle fires – which are a constant risk on any section of road – are particularly pronounced when they occur in tunnels. It is of concern in terms both of safety and of structural damage and is a very serious problem in the confined space of a tunnel. Planned and tested evacuation techniques should reduce the risk to public safety, but structural damage to the tunnel can be severe. For example, after the fire in the Channel Tunnel in 2008, when a truck on an HGV shuttle caught fire, the tunnel did not reopen fully until February 2009 with repairs costing €60 million.
Were a fire to occur in one of the Hindhead tunnels, the damage should not be structural, because the structural primary lining is protected by the secondary lining which has microfine polypropylene fibres in the concrete mix. The main cause of damage to concrete by fire is the expansion of water within its pores. With nowhere to go, the water shatters the concrete. In the secondary lining, the included polypropylene fibres would melt at high temperatures and allow the water or water vapour to expand and reduce damage. The level of repairs needed, and the disruption caused, after a fire would be reduced.
Balfour Beatty carried out tests on this technique at the Building Research Establishment (BRE), as it was necessary to get not just the right mix of fibres, but also the correct aggregate. Limestone and granite offer the best performance in a fire. These aggregates are used commonly but not universally in concrete, so it was essential that they were specified in this instance. Fire tests at BRE showed that sample lining panels performed well. In contrast, a comparison panel with no added fibres shattered so violently that it damaged the test rig!
Active lighting
One way to save energy in use and make the tunnels safer is by ‘active lighting’. This is lighting that responds to the outside conditions rather than being at a constant level. On a sunny day, therefore, the lighting at the tunnel entrances will be very bright to match the external conditions, but will decrease in intensity towards the centre of the tunnel, and brighten again towards the exit. In contrast, at night, lighting levels will be fairly low at the entrances and brighter towards the centre. The main aim is to allow drivers’ eyes to adjust, and minimise the risk of accidents, but by varying the intensity of the lighting, energy will also be saved.
Earthworks and construction spoil
The environmental targets of the design included minimising both the amount of land-take and the amount of spoil to be taken off site as unwanted. For the first of these, both embankments and cuttings were designed at steep slopes – at 60° to the horizontal and up to 20 m high. This also helped to conceal the line of the road. In order to achieve the required long-term stability, some 10,000 soil nails were used to reinforce the ground by drilling in and grouting 6 m long rods into the slopes at spacings of 1 to 2 m.
Despite the surrounding hilly terrain, the vertical alignment of the tunnels was designed to a gradient of no more than 2-3%, avoiding steeper inclines that would cause heavy vehicles to slow down, and helping to ensure that the two lane dual carriageway could keep traffic flowing at 70 mph. There were a number of environmental issues that were requirements of the project and which could have seriously interfered with progress. Two examples are outlined here: first, the care for wildlife (see Wood without waste) and second, dealing with the amount of timber to be felled (see Considering the wildlife).
Opening
By careful planning and by working with experts from all the relevant disciplines, the A3team kept to schedule and the tunnels were successfully opened on time. The final stage will be to restore as much of the Devil’s Punchbowl as possible and to reunite the two sides of Hindhead Common. This innovative engineering project pushed forward the art and science of UK tunnelling. By demonstrating best practice in so many areas, it was celebrated at both local and national level when it opened in July 2011.
Keep up-to-date with Ingenia for free
SubscribeOther content from Ingenia
Quick read
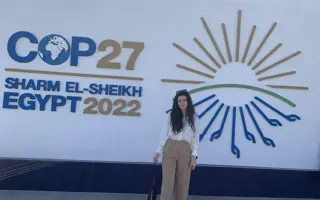
- Environment & sustainability
- Opinion
A young engineer’s perspective on the good, the bad and the ugly of COP27

- Environment & sustainability
- Issue 95
How do we pay for net zero technologies?
Quick read
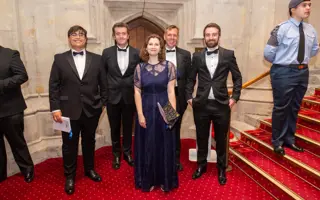
- Transport
- Mechanical
- How I got here
Electrifying trains and STEMAZING outreach
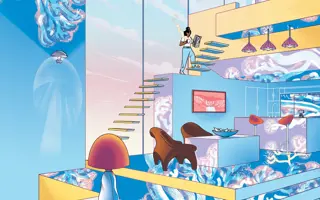
- Civil & structural
- Environment & sustainability
- Issue 95