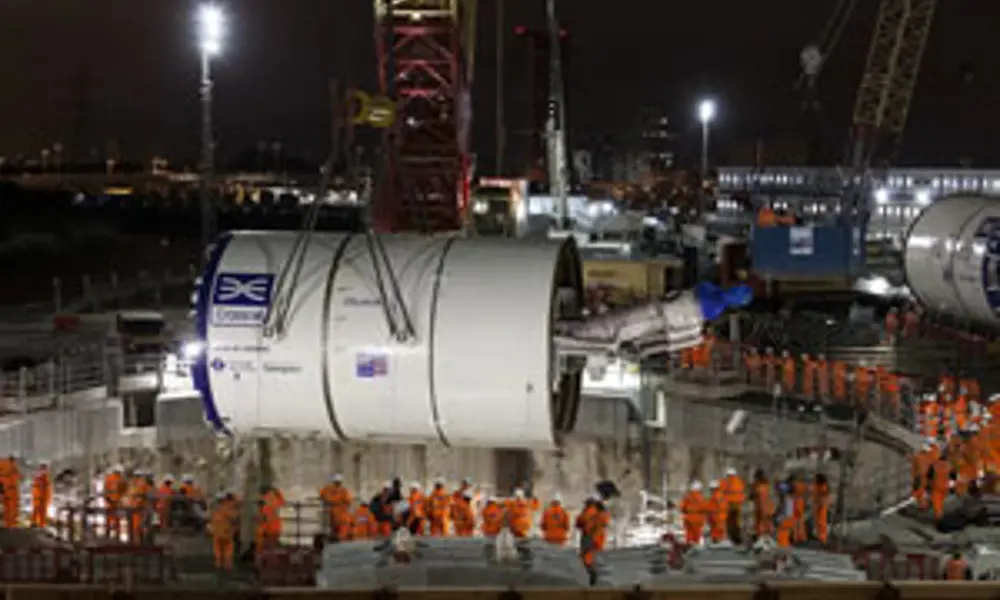
Crossrail: tunnelling on an epic scale
Elizabeth’, a 550-tonne tunnel boring machine (TBM), being lowered into a 40m deep shaft constructed at Limmo Peninsula - Crossrail’s eastern tunnels launch site, near Canning Town, in October 2012. TBMs Elizabeth and Victoria will construct Crossrail’s longest tunnel section - 8.3 km between Canning Town and Farringdon © Crossrail
One of Europe’s largest civil engineering projects – the Crossrail rail link between east and west London – is approaching its halfway point. Ingenia talked to Terry Morgan CBE FREng, Andrew Wolstenholme OBE FREng and Chris Dulake, Chairman, Chief Executive and Chief Engineer respectively of Crossrail, to determine the aims of the project and the challenges they face in building the central section of capital’s newest addition to its public transport system.
In just five years from now, trains will start operating on London’s new Crossrail railway. Crossrail is among the most ambitious infrastructure projects ever undertaken in the UK and will radically change how people travel. It will increase rail passenger capacity by 10%, putting London’s major financial centres within 40 minutes of Heathrow Airport. The new train line will also bring an additional 1.5 million people within 45 minutes’ commuting distance of London’s key business and leisure districts.
Crossrail will be the UK’s first commuter/metro link. Overground trains running to set timetables from Maidenhead and Heathrow in the west and Shenfield and Abbey Wood in the east will provide 24 trains an hour through the centre of London. It is expected that 200 million passengers a year will use the new route.
The scheduled cost of the scheme is £14.8 billion without rolling stock. Original plans for a privately financed solution for the trains have changed and provision of rolling stock is now the responsibility of the public sector. The contract to supply the trains is out to tender at the moment and is likely to bring the overall cost of the railway to around £16 billion. To date, the project is running to cost and is still scheduled to open in 2018.

Timelines and names of tunnel boring machines (TBMs): Drive X is being dug by TBMs ‘Phyllis’ and ‘Ada’ under a £500 million contract being carried out by BAM Nuttall/Ferrovial/Kier, it is due to complete this year. Drive Y is being dug by ‘Elizabeth’ and ‘Victoria’. Drive Z is driven by TBMs ‘Jessica’ and ‘Ellie’ which will start early 2014. Drive G will take place next year using one TBM from Drive Z. Contractor Dragados/John Sisk is carrying out Y, Z and G as one package worth £500 million. Completion date for all three is the end of 2014. Drive H is the Thames tunnel, worth £190 million for contractor Hochtief Murphy, with machines ‘Sophia’ and ‘Mary’ currently in the ground and aiming to finish their work halfway through 2014
There are currently more than 8,000 workers on 40 construction sites across the capital and beyond. About two thirds of the Crossrail route will be on the surface. Network Rail is carrying out a multi-billion pound upgrade on behalf of Crossrail sponsor Transport for London to prepare for the arrival of the full cross-London service.
With these challenges come risks. There are technical risks associated with completing this complex work safely while keeping London moving around the construction sites. There are also risks and challenges associated with delivering Crossrail within defined funding limits and to a schedule that has been reprogrammed to reduce costs by means of engineering-led solutions.
TUNNELLING
Right now, the tunnelling to create the central underground section is fully underway and is the main focus for this year and up until 2015. The tunnels, new stations and extensive platforms needed to cater for the trains and passengers are under construction below some of London’s busiest streets and progress is at a critical stage.
Two tunnels, one for eastbound trains and one for westbound connections will run 21km between east and west London with an average rate of tunnel construction per machine of 100m a week. Tunnels are being constructed mostly through the medium of London clay but with areas of water-bound Lambeth Group – a set of geological strata comprising of varying gravels, sands, silts and clays.

Sprayed Concrete Lining (SCL) technique involves rapidly spraying the excavated ground with concrete to stabilise it and form the permanent tunnel lining. SCL will be used to build 12 km of station platform tunnels, passages, access and grout tunnels along the Crossrail route where smaller, relatively short tunnels are needed. Unlike bored tunnels which are built using a tunnel boring machine, SCL allows variation in the tunnel shape and diameter and 7.5 km of SCL tunnels will become permanent features of the project © Crossrail
Eight Herrenknecht tunnel boring machines (TBMs) costing £10 million each are doing the work in five drives. As the TBM advances forward, the cutter head excavates the ground. The loosened material is removed from the cutter head via a screw conveyor, which moves the material through the back of the TBM and out of the tunnel via a conveyor belt. As the machine cutting head moves forward, precast concrete segments are built in rings right behind to create the tunnel lining. Eight segments create one ring.
The TBMs advance by pushing off against the concrete lining segments and balance the pressure inside the cutter head with that in front of it to maintain the stability of the ground. Each segment weighs 3,000kg and a complete ring weighs 24 tonnes. The TBMs push against the previous rings built with forces of up to 5,000 tonnes to propel the machine through the ground.
As with any tunnelling project, settlement on the surface above is one of the major risk factors and Crossrail is excavating beneath some of the most iconic parts of the capital and under Tube and other critical underground structures. Settlement, created by ground movement at the tunnel horizon caused by TBM excavation, is measured as volume loss and causes sagging and hogging in the ground – the respective downward and upward curvature of the ground seen at the surface. The contractors’ target for a maximum volume loss on the project is 1%, which equates to about 20mm at the surface for each TBM.
Refining years of tunnelling expertise, Crossrail is requiring its contractors to use precisely managed control of progress of the TBMs at the face to mitigate ground movement. They do this by maintaining control of the face pressures on the TBMs and correlating the rate of advance of the machine with the weight and volume of excavated material. Over 65,000 sensors are monitoring the effect of the tunnelling on London.
There are two different types of TBM used to reflect the differing ground conditions along the Crossrail route. Six are earth pressure balance machines, which will be used for the main running tunnels between Royal Oak and Pudding Mill Lane.
These pass through ground which is predominantly London clay, sand and gravels. The Thames Tunnel is predominantly constructed through chalk. This tunnel is using slurry TBMs which support the face and counterbalance groundwater and earth pressure with slurry pressure. Their scale is similar to the other machines, and they are excavating a 2.6km long Thames tunnel 15m below the riverbed.
A major part of the spoil disposal, 4.5 million tonnes, from the tunnelling works, usually a major project risk, is being shipped to Wallasea Island in Essex where it is being used to create a new 1,500 acre RSPB nature reserve.

The Stepney Green eastbound cavern is 50m long, 13m wide and nearly 17m high at its widest point. To construct the cavern, the team had to excavate 7,500m3 of material and apply 2,500m3 of shotcrete to the walls. Due to the site’s urban location, neighbouring a school and a technical college, a concrete batching plant was constructed onsite to manufacture the concrete that is being used to construct the cavern. The team also used a specialised cutting tool to remove temporary supports, rather than the traditional, noisier method of using an impact hammer © Crossrail
CAVERNS UNDERGROUND
The current sprayed concrete lining (SCL) design and construction philosophy has been developed and refined over the last 20 years to become a natural part of the tunnellers’ armoury. Its use was a great success for the stations and platforms on the Jubilee Line Underground extension in London. On Crossrail, the process has been refined still further to form some spectacular structures.
In essence, the technique allows the mining of large spaces underground, stabilised with sprayed concrete as work progresses. Since the Jubilee Line was completed, the controls placed on SCL tunnelling have been modified and improved still further. All structural elements are now designed and checked to construction methods agreed with contractors. The area of exposed soil is limited to a target of 30m² for each excavated face in a pre-planned and defined sequence of excavations. Supervision and control of quality are exercised throughout the creation of the structures by both the contractor’s and the client’s supervisors.
On Crossrail, one of the largest of the SCL structures is the Stepney Green eastbound cavern where trains branch south to Woolwich or east towards Stratford. It is believed to be the biggest soft ground cavern ever created in Europe. A volume of material amounting to 7,500m3was dug out in 30m² sections and a total of 2,500m3of sprayed concrete applied to the walls. This will be surpassed by the creation of a similar cavern at Whitechapel with a width of 17m.
SCL is being used to create not just these giant caverns, but also for the construction of platforms at most of the underground stations and for cross passages. In the past, temporary linings provided instant strength but lacked durability. A secondary lining would then have to be cast in situ to supply that structural strength.
With advances in additives in concrete, a mix has been found that gives the tunnellers early strength but is also durable, an evolution in SCL work.
Crossrail’s tunnel teams are also able to spray the secondary lining onto a sprayed waterproof membrane on top of the primary lining. Because they can spray concrete rather than cast, the tapering shapes and curves created will give the Crossrail platforms a style of their own.
The average thickness of the primary lining is 300mm and the secondary lining, 350mm. The composite performance of the secondary and primary structures reduces the total thickness of the SCL by approximately 25% compared to previous ways of working. This will represent a significant saving on 25,000m3being sprayed.

Crossrail originally planned to strengthen the central section of the Connaught tunnel by backfilling it with concrete foam and then boring through the concrete. However, the existing lining was not secure enough to allow for work in a tunnel beneath the dock water. Instead a cofferdam was constructed along the line of the Connaught tunnel within the dock which was pumped dry allowing the tunnel to be expanded and strengthened from within without risk of inundation © Crossrail
DEFYING GRAVITY
As with the bored tunnelling, the strategy adopted for dealing with the risk of surface settlement connected to SCL station works has been to mitigate at source. Live compensation grouting is applied when any slight movement is detected from the thousands of sensors placed along the route. This involves injecting grout through predrilled horizontal manchette tubes (sleeved grouting pipe) from grouting shafts that then finds a path to compensate for soil volume loss beneath the buildings. So far 50km of manchette tubing has been drilled across the job.
If a building moves 5mm, the grout can be targeted in real time to hit the right spot. The technique was used on the Jubilee Line Extension but has been refined and improved further for Crossrail. The compensation grouting is being carried out by a joint venture between Keller Geotechnique and BAM Ritchies.
STATIONS
Nine new stations are being constructed by the project – at Paddington, Bond Street, Tottenham Court Road, Farringdon, Liverpool Street, Whitechapel, Canary Wharf, Woolwich and Custom House. One station that will have a particularly significant impact is Farringdon.
When the railway opens in 2018, Farringdon will be one of the UK’s busiest stations linking Crossrail, Thameslink and London Underground services, turning the area around it into an important business and residential zone. It will also provide a highly accessible connection between Heathrow Airport and Gatwick that the Crossrail team believes will become so important to London that Farringdon will become a mainstream destination in its own right.
In terms of the civil engineering work, Farringdon already is an important destination. This is where the four TBMs constructing the east- and westbound running tunnels will meet, and preparations are already underway for the arrival of ‘Phyllis’ and ‘Ada’ – all the TBMs have female names. They are due to complete their 8.5km journeys from Royal Oak in the west later this year.
The SCL teams will then move in to expand the station cavern and spray the concrete lining as the bored tunnel rings are removed. Over time, they will excavate a platform space measuring 11m wide by 10.5m high, much larger than the 6.2m diameter tunnel created by the TBMs.
In general and where practicable, the TBMs will be taken out of the tunnels in their entirety, Victoria and Elizabeth will be removed through shafts built as part of the Farringdon Station complex and the others from portal structures near ground level along the route.

Crossrail’s new ticket hall at Liverpool Street is to be built on the site of a burial ground for London’s infamous psychiatric hospital, ‘Bedlam’. As well as skeletons, archaeologists have uncovered pottery fragments, clay pipes and animal bone artefacts including knife handles. Crossrail currently operates over 40 worksites and archaeological investigations will be carried out at each site ahead of main construction works to build the central stations © Crossrail
COLLABORATING ON INNOVATION
All the way through the construction process, Crossrail has been looking to encourage innovation from the main contractors and supply chain. Main contractors tender against the employer’s design but once the successful bidder had been selected, to create a further opportunity to improve on design and working methods, Crossrail introduced a 60-day optimised contractor involvement period to allow new ideas to be introduced, with savings from any emerging efficiencies shared 50:50 between the contractor and Crossrail.
One of the most obvious successes of this approach has been at the 500m long Connaught tunnel section of the job running beneath the Royal Docks. The original plan had been to enlarge in situ an existing tunnel from the 1870s that had been refurbished in the 1930s.
This was a high-risk area on the project; any water inundation would have been catastrophic. Project contractor Vinci instead proposed draining the 13 million litres of water from the dock and enlarging the tunnel within a 1,300m² cofferdam. With the water out, it could open up a hole in the tunnel roof 20m by 10m to carry out the engineering equivalent of keyhole surgery inside, widening and deepening the tunnel to accommodate Crossrail trains. The project manager negotiated a six-month dock closure and the job is now complete. A new concrete slab has been laid at the bottom of the dock and water has been reintroduced.
In association with Imperial College London, last year the project launched the Crossrail Innovation Strategy to promote collaborative engagement with innovation across the supply chain. Ideas are evaluated and catalogued before being uploaded on to www.innovate18.co.uk where the entire Crossrail supply chain can access information and adopt it.
Sample ideas picked up have been the installation of 360° CCTV onto excavators to improve safety from Costain Skanska, LED hoarding lights to reduce maintenance costs and energy consumption from Costain and a modular EchoBarrier noise reduction system from Vinci.
Building Information Modelling (BIM) is a major theme for the entire construction sector at the moment. Crossrail is aiming to be the first major infrastructure project to create a fully integrated single 3D model of the entire railway and all the elements that went into creating it that can be handed over to the operator to optimise maintenance and management of the service long into the future.
FUTURE PROOFING
The population figures for London post-2030 have been revised significantly upwards since the last census, from 8.5 million to 10 million. Its transport systems will need to expand again to cope. In the tradition of the best Victorian engineering, Crossrail has built capacity for the service to be increased into the designs for tunnelling and railway work.
The team appreciated that it would be hugely costly, disruptive and very difficult to retrofit any extra capacity. For the initial service, trains will be 10 carriages long, but platforms have been constructed to take 12. The signalling system through the central section will be able to manage 32 trains and hour, eight more than the 24 the Crossrail service will open with.
Throughout all the cost management and value engineering carried out to keep the project within its £14.8 billion construction budget, that extra capability has survived and will be part of Crossrail’s legacy for London for the next half century and more.
Keep up-to-date with Ingenia for free
SubscribeOther content from Ingenia
Quick read
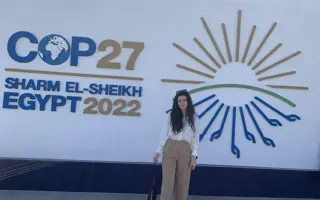
- Environment & sustainability
- Opinion
A young engineer’s perspective on the good, the bad and the ugly of COP27

- Environment & sustainability
- Issue 95
How do we pay for net zero technologies?
Quick read
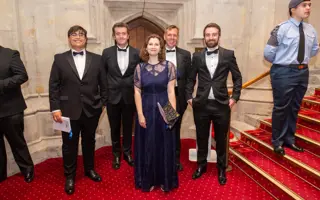
- Transport
- Mechanical
- How I got here
Electrifying trains and STEMAZING outreach
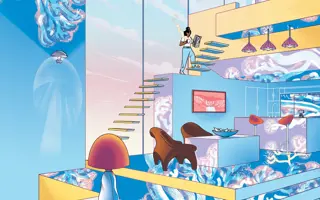
- Civil & structural
- Environment & sustainability
- Issue 95