Design Drives - Materials Innovation
Combining the traditionally different fields of materials engineering and textile design has the potential to transform many aspects of our lives, writes Dr Raymond Oliver FREng and Anne Toomey of the Royal College of Art.

Textile Light Fitting. This reactive fabric is a combination of silver plated wire and luminescent yarn © Neil Musson MA RCA
Textiles are everywhere, in every part of our day-to-day lives. There are micrometre-sized textiles placed inside the body, such as arterial stents; ‘on-body’ textiles such as bandages and clothing; and metre- or even kilometre-scale textiles within the built environment, such as terraforming geotextiles used in flood areas to prevent soil erosion.
Recent innovations in materials science and engineering have significantly broadened the scope for the uses of textiles. New textile applications include glass, ceramics, concrete, aramids and carbon fibre composites. These developments have moved our understanding of textiles, from being passive, simply serving their design purposes of being beautiful, hard wearing, high performance or warm, to becoming active or interactive.
One idea that has generated a lot of interest is known as ‘smart’ textiles. This has had limited success to date, as it has not proved easy to combine intelligent information within textiles, because traditional silicon based systems and devices are physically rigid and so not particularly versatile, while the very identity of textiles is about flexibility and versatility.
New developments in materials science and process technology promise to change this. Materials in the form of conjugated conductive polymers, where electrons are delocalised within the polymer’s structure, are now approaching amorphous silicon in terms of electron mobility and can therefore be programmed in similar ways. Functional polymeric materials based on this approach are being developed that exhibit a range of useful electro-, photo- and bio-active properties. There are also existing materials that offer shape-changing, colour-changing and energy-exchanging properties. Moreover, they are not restricted to being rigid or planar and can be woven into fabrics, deposited as non-woven thin films or processed from solution. This enables them to become printed sensors, actuators, interconnectors and simple transistors and even be fabricated into very large (km2) structures. The implications of such developments offer an opportunity for more radical, rather than incremental, change in the way we will use textiles in the future.
Future textiles
The resulting materials have the advantage of being conformable and flexible. Active polymeric materials which respond to electrical, optical or biological stimulus have the potential to be spun into fibres, printed as a coating or extruded as thin multiple layers. These three physical forms can then generate interactive surfaces and even 3D structures that are determined by end-use application, function or aesthetics. To combine these multifunctional properties into products and new applications, design should take place alongside development, with
a focus on the individual user.
Active polymeric materials can be processed in solution and be used in the creation of 3D product design. This provides the basis for creating near-transparent and conformable logic and memory devices that can be designed to be embedded into nearly all everyday objects, such as storage surfaces, furniture, curtains and carpets, and into many aspects of people’s lives at work, at play and at home. It also, critically, serves to form the physical basis for future Ambient Intelligence.
Health, wellbeing and security
Healthcare and wellbeing is one of the key application areas for smarter materials. At the Royal College of Art (RCA) we, and several partners, are developing ‘smart’ bandage concepts to monitor and treat different chronic wounds. If it is possible to radically change both the materials and the construction processes of a conventional bandage, there is an opportunity, through design, to change the perception and experience of chronic wounds from both the patient’s and the carer’s viewpoint.
With smart bandages, the advantage of incorporating wireless technology along with therapeutic delivery, for example, would mean that medical staff wouldn’t need to remove the bandage to monitor the wound. Continuous and long term monitoring will make the bandages more cost-effective by saving staff time. In addition, skin conductivity sensors can monitor patient stress and anxiety in order to continually assess patient’s comfort and wellbeing.
Our proposal, which includes eight university, research institute and industry groups, will look at ways to control pressure and fluid monitoring. The RCA team will work on the design of the new bandage, including the fabrics and the ‘soft engineering’ of the bandage itself.
A related example being developed is eScent, a wearable technology that releases different scents depending on the time of day and therefore whether it is being worn to a business meeting or at a nightclub. This concept is based on MEMS (micro-electro-mechanical systems) technology combined with a bio-responsive material containing a fragrance. The material can expand in response to an electrical impulse, triggered by, for example, sensing a pH change or sound, and release the fragrance. The beauty of this is that the process is reversible; when the triggering signal is removed, the material returns to its original state. This work is a collaboration between the Royal College of Art and Central Saint Martins (Dr J Tillotson) and an industrial partner. The controlled release and targeted delivery methodology also has significant potential for healthcare too.
Security is another area where smarter textiles can play a role. We are looking at the potential to incorporate holographic materials or quantum dots into bank notes. These tiny materials are invisible to the human eye (quantum dots are of the order of a nanometre in diameter) but have characteristic responses to light. Incorporated into currency, or anything else, they can act like a tiny barcode giving a distinct pattern of multiple colours.
Smarter built environments
The built environment is an important opportunity for ‘smarter’ materials too. Compared to automotive or aerospace construction, most building interiors are inactive. Buildings consist of many surfaces and interfaces and, today, functionality, such as lighting and communication, is added on with various manually activated surface switches. By incorporating new smart materials into the surfaces and interfaces of buildings the actual functionality can be embedded into surfaces that are able to perform more than one action.
There are already some interesting developments in the area of architectural lighting. Multiple electro- and photo-active polymer-thin films are layered on top of one another to yield solid state lighting surfaces, as well as the colour or gradient of light. This signals the beginning of the architectural use of organic light emitting diodes (OLEDs) from surfaces that emit light, rather than the traditional sources of light offered by incandescent bulbs. There are interesting possibilities, too, for incorporating fluorescent and phosphorescent fibres with other smart material properties in textiles in the built environment, such as curtains, wallpaper, furniture and carpets.
Organic photovoltaics are another interesting area utilising large area, thin electro/photo active films for development. One of the most promising approaches to date is based on combining the nanostructured active polymer poly (3-hexyl thiophene) (P3HT) and the fullerene derivative 6,6-phenyl C61 butyric acid methyl ester (PCBM). However, in order for such systems to be truly revolutionary, they will not only need long lifetimes and better photo-conversion efficiency (their efficiencies are still significantly lower than that of their inorganic counterparts), they will also have to be fabricated by the square kilometre. This will mean reel-to-reel printing technology equivalent to today’s modern newspaper presses, using either gravure or offset printing or even multilayer thin film extrusion. Such technology paves the way for incorporating solar energy harvesting and energy storage and printing it by the square metre into wallpaper, for example.
A combined approach
Such exciting possibilities require a new way of thinking. The phenomenal success of the iPod (which is based on traditional silicon technology) has highlighted the importance of strong, user-focused design. Similarly, to make the most of the opportunities of smart materials, engineers and designers need to work together from the start.
Having engineers involved in the design process dramatically increases the designer’s knowledge of the performance potential of materials that could be used and their properties. It also shortens the development time for new materials and production implementation. It means that designers can think about innovative future products before the materials to achieve them become available. On the other hand, it also means that designers, who are focused on the possibilities for end-users, can contribute in the early stages of developing materials with particular properties.
The interdisciplinary nature of design, materials and engineering finds common ground through the opportunities offered by programmable, interactive surfaces and structures. The breadth and depth of human-centred applications presented by these structures form the basis of ‘materials for living’.
The Royal College of Art has a team that includes chemical and material engineers working directly with designers. They are together looking at the commercial potential of new materials based on conjugated polymers with conformable properties which are solution processable. The engineers are used to dealing with systems and materials while the designers deal with materials and societal needs.
Materials are the common thread that runs through both approaches and forms the basis for our discussions. Because many of the potential materials we are looking at are solution-processable, we can consider materials as dots (derived from droplet and spray production followed by phase transformation), lines (from fibre spinning and subsequent phase transformation), surfaces (from thin film, multilayer extrusion and deposition) and structures (from rapid prototyping, 3D printing and injection moulding).
Design to product
There is strong interest in our approach to design with smarter materials from a range of industrial groups. These include the aerospace industry, architects, engineering suppliers in the construction industry interested in using interactive surfaces, the pharma delivery systems industry and developers of wearable technology. The key challenge is turning the designs into real products and systems, a result of the restricted availability of active materials in design friendly formats.
We are currently discussing with material laboratories and companies about the sourcing of materials to incorporate into our designs. A current challenge is obtaining sufficient quantities of materials. Many academic materials laboratories produce suitable quantities to be able to test the properties and publish the results in research papers – but not enough to be able to incorporate into implementable design led products.
Manufacturing challenges
There are also manufacturing challenges to be addressed. First, there is the problem of how to create active electro-, photo- and bio- materials that are highly reproducible and reliable and can be processed in a way that allows the formation of fibres, fabrics and ultra-thin films capable of being produced with large surface areas. Here, electrospinning and thin-film multilayer extrusion provide us with implementable technology solutions which are also capable of scale up.
A second challenge is that the effectiveness of most of the organic conductive polymers of interest is rapidly diminished in the presence of oxygen and/or moisture. This means that, in parallel with their production, comes the need to create protective, encapsulating films that allow long operating lifetimes. An alternative approach of course is to build into the conjugated conductive polymers stabilising molecules that act or react internally to achieve the equivalent of a relatively expensive external organic-inorganic encapsulating protective coating.
The third challenge is that the idea of creating organic Complementary Metal-Oxide Semiconductor (CMOS) technology relies both on the solution processability of the active materials and on the ability to generate higher mobilities. The most promising manufacturing approaches for these materials today are: rapid prototyping, where successive layers of the required materials are built up according to the manufacturing design from a computer-aided design package; layer-by-layer deposition; and atomic layer deposition.
Ambient Intelligence
Smarter materials also bring other, societal, challenges that need to be addressed. Once people begin to interact and share information more with textiles and material surfaces and interfaces within, on and near their bodies, questions of control, trust and privacy emerge, as well as fears about information overload. These aspects could delay the introduction of novel technologies into our everyday lives. This area of social as well as system intelligence is a key to successful and ubiquitous uptake. In healthcare in particular, there is a clear need for standards in this area.
Economies of scale will reduce the cost of incorporating ‘intelligent’ textile surfaces into products and from here we will move into a new era of smart environment development, which generates the physical basis for future Ambient Intelligence (AmI).
Smarter textiles and intelligent materials are an emerging technology. The materials which drive this, that is electro-, photo-, and bio-active polymers and gels, have only been in development within the last 10 to 15 years. However, all the indications suggest that AmI is going to be a key strategic driver for future applications in printed electronics and photonics, which is design-led, needs-driven but materials-anchored.
Further information
www.arrowscience.com
www.rca.ac.uk
Keep up-to-date with Ingenia for free
SubscribeOther content from Ingenia
Quick read
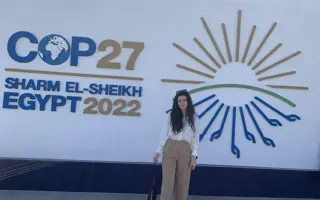
- Environment & sustainability
- Opinion
A young engineer’s perspective on the good, the bad and the ugly of COP27

- Environment & sustainability
- Issue 95
How do we pay for net zero technologies?
Quick read
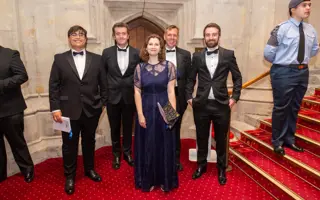
- Transport
- Mechanical
- How I got here
Electrifying trains and STEMAZING outreach
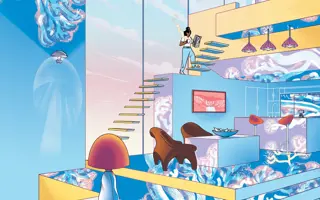
- Civil & structural
- Environment & sustainability
- Issue 95