Engine Health Managment
Aerospace Operations Centres are able to track the health of thousands of engines operating worldwide by using onboard sensors and live satellite feeds. Rolls-Royce are world leaders at equipment health management (EHM) and Nick Waters is their Chief
EHM Engineer. He writes for Ingenia about how the company is able to track and provide real-time monitoring and support for its engines.

Engine Monitoring Unit on Trent 900 engine © Rolls-Royce plc
Increasingly airlines – and now defence forces, too – want to improve their own service and minimise unnecessary costs by concentrating on what they do best and avoiding tasks they can safely leave to others. Now, around half of the Rolls-Royce civil engines fleet is covered by long-term service agreements, with 80 per cent of new business incorporating long-term support elements. This trend sees airlines effectively turning over engineering and maintenance support to the engine maker and effectively buying service support ‘by the hour’.
It is important to recognise that Engine health management (EHM) is primarily there to reduce maintenance cost and avoid service disruption. This support is in addition to the well-established safety systems confirmed by engine certification and managed by the airlines.
The driving force behind this service-focused ethos is the Operations Centre. The centre dealing with civil engines support in Derby is staffed by 170 people and there are also centres at Bristol, UK and Dahlewitz in Germany. They incorporate a ‘front desk’, occupied by a small team of experienced engineers monitoring the worldwide fleet, tracking trends and giving customers real-time advice 24/7, 365 days each year. They also hold a larger back-room team, whose key roles are to support immediate needs and to put the tools and processes in place for medium- and long-term technology, engineering, repair and overhaul, and logistics developments.
ENGINE HEALTH MANAGEMENT
EHM is the cornerstone of the Operations Room effectiveness. It uses a range of sensors strategically positioned throughout the engine to record 20-30 key technical parameters several times each flight. EHM sensors are installed in a large proportion of the company’s civil engines fleet and EHM capability is provided for virtually all of the latest Trent family of engines.
EHM is essentially a technique for predicting when something might go wrong. It is especially useful in industries such as aerospace and medicine where the results of a technical failure could prove very costly indeed – so what EHM aims to do is avert a potential threat before it has a chance to develop into a real problem.
The EHM sensors in aero-engines monitor numerous critical engine characteristics such as temperatures, pressures, speeds, flows and vibration levels to ensure they are within known tolerances – or, more importantly still, to highlight when they are not.
In the most extreme cases air crew could be contacted, but far more often the action will lie with the operator’s own maintenance personnel or a Rolls-Royce service representative in the field to manage a special service inspection. Alternatively, if an engine replacement is required, one of the Centre’s back-room team will arrange for the rapid supply of a spare or lease engine.
Longer term engineering projects can also benefit from the ever-deepening well of data, as causal analysis informs modification programmes for existing engines or trends feed into design strategies for lifing components and the system behaviour of future engines.
EHM IN ACTION AT ROLLS-ROYCE
The EHM system for Rolls-Royce aero engines comprises five key stages: Sense – measuring various parameters within the engine; Acquire – capturing this data at relevant periods during every flight; Transfer – transmitting data from the aircraft to the ground; Analyse – normalising data and detection of any unusual characteristics; and Act – providing advice to the maintainer so that corrective action can be made if necessary. For the Trent 900, which powers the A380, the system works in the following way:
SENSE
The engine is permanently fitted with about 25 sensors. Many of these are multi-purpose as they are used to control the engine and provide indication of engine operation to the pilot as well as being used by the EHM system.
These are selected to make the system as flexible as possible. The main engine parameters – shaft speeds and turbine gas temperature (TGT) – are used to give a clear view of the overall health of the engine. A number of pressure and temperature sensors are fitted through the gas path of the engine to enable the performance of each of the main modules (including the fan, the intermediate and high pressure compressors, and the high, intermediate and low pressure turbines) to be calculated.
These sensors are fitted between each module, except where the temperature is too high for reliable measurements to be made. Vibration sensors provide valuable information on the condition of all the rotating components. An electric magnetic chip detector is fitted to trap any debris in the oil system that may be caused by unusual wear to bearings or gears.
Other sensors are used to assess the health of the fuel system (pump, metering valve, filter); the oil system (pump and filter); the cooling air system and the nacelle ventilation (nacelle is the cover housing – separate from the fuselage – that holds engines, fuel, or equipment on aircraft).
As engine operation can vary significantly between flights (due to day temperature or pilot selection of reduced thrust), data from the aircraft to provide thrust setting, ambient conditions and bleed extraction status is also used.
ACQUIRE
Most modern large civil aircraft use an Aircraft Condition Monitoring System (ACMS) to acquire the data for EHM. This captures three types of reports:
The first are snapshots, where the sensor data listed above is captured and collected into a small report. This is carried out during take-off, during climb and once the aircraft is in cruise.
The second type is triggered by unusual engine conditions. Examples might be if an engine surged, or exceeded its TGT (Turbine Gas Temperature) limits during a take-off. These reports contain a short time-history of key parameters to enable rapid and effective trouble-shooting of the problem.
The final type is a summary, which is produced at the end of the flight. This captures information such as maximum conditions experienced during the flight, and power reductions selected during take-off and climb.
The Trent 900 is the first engine to be fitted with a dedicated Engine Monitoring Unit as well as the ACMS. This engine-mounted system places a powerful signal processing and analysis capability onto the engine. This is used to look in more detail at the vibration spectrum, which helps to pick up problems with bearings or rotating components. It also provides a flexible computing platform so new EHM software can be rapidly deployed to detect specific problems.
TRANSFER
A critical aspect of the EHM system is the transfer of data from aircraft to ground. The A380 uses the ‘ACARS’ digital datalink system as the primary method. This transmits the ACMS reports via a VHF radio or satellite link whilst the aircraft is in-flight. A worldwide ground network then transfers this data to the intended destination.
The positive aspect of this system is its robust nature and ability to distribute information worldwide. On the other hand, the size of reports that can be handled are very small (typically just 3kBytes), so the acquisition systems described above need to work within this limitation.
Future systems are being deployed to increase data volumes through wireless data transmission as the aircraft approaches the gate after landing. This will enable more data to be analysed, but will not be as immediate as ACARS, where data can be assessed well before the aircraft lands again.
ANALYSE
As soon as the individual reports arrive at the specialist EHM analysts OSyS (Optimized Systems & Solutions, a subsidiary company of Rolls-Royce), they are processed automatically. The data are checked for validity and corrections applied to normalise them. For the snapshot data, this is always ‘trended’, so that subtle changes in condition from one flight to another can be detected. Automated algorithms based on neural networks are used to do this, and multiple sensor information is fused to provide the most sensitive detection capability.
When abnormal behaviour is detected, this is confirmed by an OSyS analyst based in the Operations Centre, before being sent to the aircraft operator and logged by the Rolls-Royce Technical Help Desk. Manual oversight is still an important part of the process, as false alerts can cause unnecessary maintenance actions to be taken by airlines and these need to be avoided.
Trended data, and data from the other types of ACMS report, are also uploaded onto the Rolls-Royce aeromanager website, so that plane operators can easily view the health of their fleet of engines.
ACT
The EHM signature will typically highlight a change in an engine characteristic. As in the medical world, expert knowledge is then used to turn this symptom into a diagnosis and usually a prognosis. This is done by using the skills of expert Rolls-Royce engineers working with the OSyS analysts, to assess what the most likely physical cause of a particular signature is, how an operator can confirm this and how urgently this needs to be carried out. For an engine that is showing gradual deterioration, for example, an inspection in several weeks time may be appropriate. If a step change in performance has been observed, inspection within the next 2-3 flights might be recommended.
The Technical Help desk will discuss the recommendations with the operator (to manage the best fit with their planned operation) and will then regularly liaise with them until the problem is understood and any risk to the smooth operation of their service mitigated.
THE SYSTEM IN ACTION
To illustrate how this works in practice, consider an incident where an engine ingests a foreign object that causes some damage to an HP compressor blade. This is unlikely to have any immediate effect on the engine operation, but the damage will steadily propagate over a number of flights until damage that is more substantial is done which will cause the engine to surge.
The EHM system monitors a number of independent parameters that can detect this before the compressor is degraded and a surge occurs. Damage to the compressor blades will reduce the efficiency, and therefore the engine will run hotter when trying to produce the same thrust. The trend of turbine gas temperature (TGT) flight by flight will therefore show a step change. Additional information from the P/T25 and P/T30 sensors (measuring pressure and temperature in front of and behind the high pressure compressor) will enable a simple calculation of the compressor efficiency to be made, and this is more sensitive to small changes than TGT.
Even if the change in performance is too small to detect, loss of any material from some compressor blades will change the balance of the HP rotor. As this rotates at around 12,000 rpm, the vibration characteristic of the engine will change. This can be detected by the simple tracked orders captured by the ACMS, or through more sophisticated vibration signal analysis within the EMU.
With multiple, independent, signatures to view, the OSyS analysis system can detect that a significant change in the engine behaviour has occurred. From these signatures the Rolls-Royce engineers can determine that the most likely cause is damage to the HP compressor, and request the operator to carry out an inspection by using borescope equipment or even to deploy specialised on-wing maintenance procedures – see box titled On-wing Care.
In 2008 alone, the use of EHM mitigated 75 per cent of potential civil engine in-flight events, often employing on-wing care techniques to
do so.
CIVIL
Only about 10 per cent of the Centre’s staff work as part of the front-desk team, which monitors flight operations as they happen and resolved around 3,600 technical queries in 2008. These experienced service engineers work 12-hour shifts around the clock, and shift patterns are designed to rotate staff so everyone works with a mix of different people and projects, thereby broadening their skills and product/fleet knowledge.
Such a data-rich environment also enables its back-room staff to co-ordinate technical campaigns with engine programme engineers, aimed at raising engine reliability, and to develop best-practice maintenance schedules to reduce down-time for customer operations.
Most Operations Centre personnel are involved in ‘back-room’ roles managing key processes and less urgent requirements identified by the front-desk team. These include recording and analysing the steady inflow of technical data, managing specific service requirements to minimise operational disruption – such as timely provision of line-replaceable units or spare or lease engines – or organising engine repairs and overhauls.
The company’s overall repair capability is extensive, with 16 repair and overhaul facilities on four continents. In addition, day-to-day customer support comes from a deployed field services organisation of almost 200 people in 70 locations. As operators face a variety of environments – flying differing sector lengths and encountering unusual atmospheric or airport conditions, which can all have an influence on how engines deteriorate – this local expertise can be vital.
ONWING CARE
This inspection will guide the operator to what action needs to be taken. If it is detected early, it may be possible to blend out minor damage with the engine still installed on the aircraft. ‘Boroblending’ is essentially, on-wing keyhole surgery for engines, thus avoiding the disruption to the airline operator of having to remove an engine and send it the overhaul workshop.
DEFENCE
Real-time satellite tracking of defence assets is not an option, but sensors still monitor engines’ technical parameters, with data collected immediately after each flight and added to the deep well of knowledge deployed by engineers in the equivalent Operations Centre in Bristol. With the centre managing
11 engine types for 160 customers worldwide, they’re kept busy – dealing with around 400 queries each month.
Support teams deployed at key service bases download data at the end of each mission, and this is then shared with the Operations Centre in the same way. Furthermore, as well as data gatherers, the dedicated teams on base include logistics managers and operations managers who provide on-the-spot assistance for first- and second-line service support. Then they can make decisions on how and where maintenance activity should be undertaken.
Where customers don’t have dedicated Rolls-Royce teams – or when flight assets are deployed in combat zones – calls for assistance often come into the Operations Centre direct from forces’ engineering squadron personnel, who need pretty instant advice so they can rapidly resolve operational issues.
Bristol Operations Centre staff view their role as moving up the service chain. The Ministry of Defence has made the move from provider to decider, with the expectation that Rolls-Royce provides a high level of service by developing innovative engine support solutions. These embrace all elements of repair and overhaul, technical and logistics support to ensure the right assets are in the right place at the right time to achieve mission success.
PLANNING AHEAD
The evolution of EHM – and the revolution in its use to reduce costs by preventing or delaying maintenance, as well as flagging potentially costly technical problems – is set to continue. New assets will incorporate EHM capability, and techniques will, where possible, be retrofitted to existing equipment. The volume and scope of work in the Operations Centre will grow in parallel.
Furthermore, broader engineering disciplines can benefit from the growing reservoir of supporting data. As operational profiles of technical performance are revealed in ever more detail – from individual components to whole engines – so engineers can develop more thorough and cost-effective maintenance schedules, and designers can feed higher reliability features into the engine products of the future.
Keep up-to-date with Ingenia for free
SubscribeOther content from Ingenia
Quick read
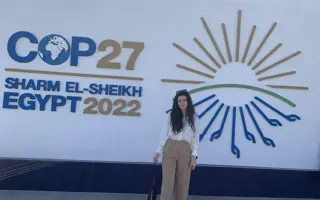
- Environment & sustainability
- Opinion
A young engineer’s perspective on the good, the bad and the ugly of COP27

- Environment & sustainability
- Issue 95
How do we pay for net zero technologies?
Quick read
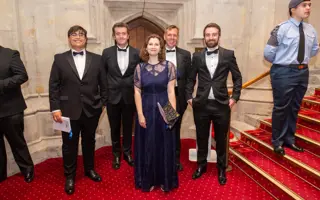
- Transport
- Mechanical
- How I got here
Electrifying trains and STEMAZING outreach
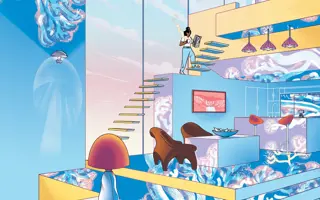
- Civil & structural
- Environment & sustainability
- Issue 95