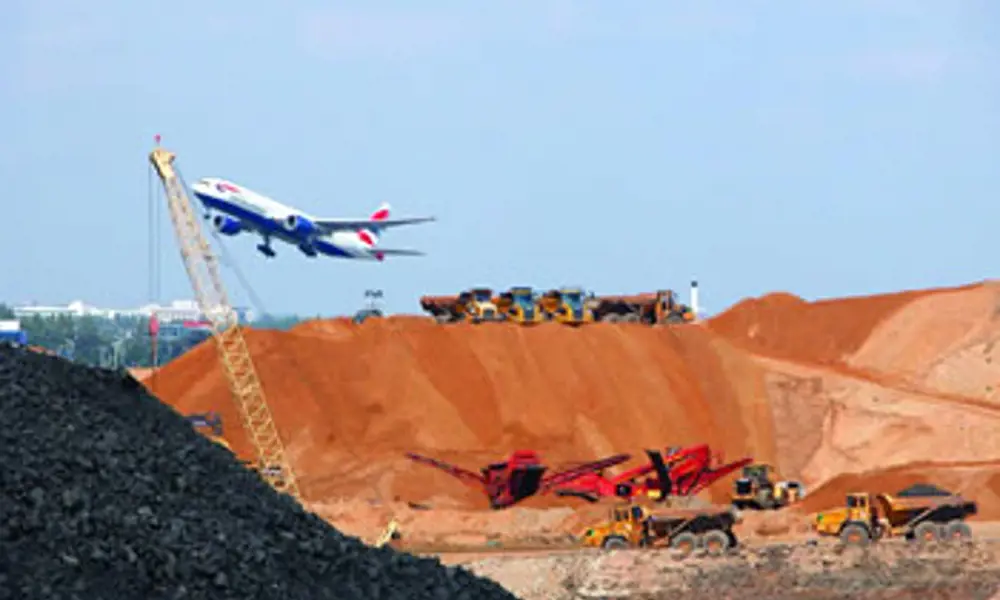
Engineering the space below Terminal 5
Excavation materials were stockpiled for reuse in landscaping of the T5 site. Mounds of earth were also used to restore earth pressure adjacent to areas of excavation Image supplied by Mott MacDonald
Terminal 5 at London’s Heathrow Airport has been the largest building project in Europe over the past few years, with a construction bill of nearly £4.3 billion for the British Airports Authority (BAA). The immense size of the structures and their basements posed significant challenges for both BAA’s designers and constructors. These included excavation in London clay and tunnelling around both existing infrastructure and under the world’s busiest airport. Mott MacDonald’s Haresh Shanghavi, Jim Beveridge, Arthur Darby and Alan Powderham FREng explain the engineering solutions that have helped deliver T5 to time and within budget, ready for its opening on 27 March 2008.
London Heathrow Airport, owned and operated by BAA plc, is the busiest international airport in the world. Today, Heathrow handles 67 million passengers a year, but its original four-terminal infrastructure was designed for far less. When the new Terminal 5 development opens to the travelling public in March 2008 it will be one of the world’s most advanced airport terminals and will increase the airport’s passenger capacity to up to 95 million passengers a year.
Above ground, Heathrow’s Terminal 5 embraces design and architecture at its best while below ground it hides one of the most notable engineering achievements of its kind anywhere in the world.
The three buildings that make up Terminal 5 have a combined floor area greater than all the other Heathrow terminals added together. The main terminal building, called T5A, and one of two satellite buildings, T5B, are now complete (see the map overleaf for the airport layout). The substructure of satellite T5C is in place and its superstructure will be ready for use by 2010.
The sheer size of the buildings, particularly the main one, is clear from the aerial views. These buildings are above large underground structures – the basements, foundations and tunnels essential to the operation of the terminal – the total ground volume of which, like an iceberg, greatly exceeds that of the visible superstructures.
Hidden depths
Nearly a fifth of the construction budget went underground. The main T5 basement volume is believed to be the greatest-ever excavated in the UK – and one of the deepest. Its plan area is 396 m by 176 m (equivalent to 60 football pitches) and its depth of 22 m would hold an eight-storey building. The foundations for T5B and C, although much smaller, are substantial works in their own right.
A complex unseen network of road, rail, baggage, passenger transit and drainage tunnels has been created close to and underneath the new terminal buildings and beneath the airport’s taxiways and aprons (the areas where aircraft are parked). These include extensions to the Heathrow Express and London Underground Piccadilly Line rail tunnels, the airside road tunnel, stormwater outfall tunnel and a light rail passenger transit tunnel connecting the three terminal buildings. Each tunnel represented a significant project in itself.
BAA, the client, developed and followed a strategy for managing the construction and the many contractors and suppliers needed to complete T5. This overarching strategy and the benefits it stimulated are summarised in the box labelled 'BAA's construction strategy and their team for these works‘.
For the work described here – the creation and use of underground space –the critical factor was the ground in which basements were excavated, foundations installed and tunnels advanced.
The ground and its behaviour
The T5 underground structures are all set within London clay, a particularly challenging material in which to dig and construct. London clay is an overconsolidated material. Aeons ago it was thickly covered in deposits that compressed it, making it stiff and impermeable. The clay resists further compression under loading. Below a depth of about 50 m this clay gives way to substantial amounts of water-bearing silt and sand.
When the clay is unloaded by deep excavations compressive stress is relieved and it expands. In the deep T5 excavations, the small immediate rebound of approximately 50 mm would be ‘lost’ in the excavation process. That is not the end of the story, however, as this material then continues to swell, producing significant uplift at the surface – as much as 250 mm within 50years or so.
If the total load of the building and basement matches or exceeds the weight of soil excavated, this uplift can be prevented. However, this was not going to happen at T5, and had several major implications. Swelling clay would try to lift up foundation piles. A floor slab directly on the clay would be lifted and lateral stresses would affect side walls. The stress-field around an existing tunnel would change rapidly at first and then more slowly with time, depending on how close it is to the excavation. For new tunnels, swelling could result in distortion with implications for track alignment, ride quality and even safety.
So our challenges were clear: when building T5’s five new tunnels, with their combined length of some 14 km, we needed to ensure the swelling effects of London clay would not affect these tunnels or the new tunnels being developed.
When creating the huge basements of T5 and its satellites, we had to ensure the natural swelling of the ground beneath the basements was controlled in a way that avoided short-term and long-term hazard, not only to the new above-surface structures, but also to existing and new tunnels.
Countering swelling clay
For basement construction, swelling ground can be handled in two ways. A massive slab can be cast directly on the ground and anchored with very long piles to resist uplift. Alternatively, the base slab can be formed above the ground supported by piles but leaving a void beneath, into which the ground is allowed to swell. The first is a heavy option with large material requirements and higher construction costs. The second method is far more economical and BAA selected it, but it did involve a more complex design. Foundations had to support the base slab and terminal superstructure while resisting the swelling clay acting to push the piles upwards.
To complicate the task still further, different basement levels offered varying amounts of unloading and potential swell. Added to this were different structural loads which meant the amounts of force exerted on the piles would differ. Pile sizes therefore varied as did the behaviour of those piles in contact with swelling clay and the foundation design needed to balance these opposing forces (see the box opposite).
Excavating the T5C basement
T5 relies on tunnels of many types, sizes and purposes to function. The alignments of 14k m of new tunnels were dictated by the need for the stations to be close to the arrivals and departure halls, by the locations of existing tunnels and by the constraints of the site itself, which is boxed in by the M25 motorway and Heathrow’s north and south runways.
By the time the foundations of T5C came to be built the tunnels were already in place. The basement excavation was therefore just a few metres away from the new underground structures of the Piccadilly Line and Heathrow Express – a mere 3 m in the latter case. This nearness meant swelling of the clay would affect the tunnels, with potentially destabilising effects. This could happen in various ways.
Balancing pressures
We designed a construction sequence for the foundations that ensures the least ground movement or structural displacements. The design included establishing ‘trigger levels’ of key parameters at particular locations, particularly of displacement, at which pre-planned mitigating measures would be initiated to control, and if appropriate, halt further movement. We surveyed movement sensors in the tunnels in real time during excavation of the foundations and throughout the construction process – none of the trigger levels was reached.
We excavated the basement in stages rather than across the whole area to minimise the amount of unloading at any one time. Excavated soil was mounded temporarily on previously excavated areas to maintain load, and then tunnel spoil was re-used as fill on the T5 site.
At the critical location where the crown of the Heathrow Express tunnel is only 3 m below the excavation base we installed massive holding-down beams connected to anchor piles to span across this section rather like giant staples.
New tunnels
Five new tunnels now serve Terminal 5. Existing twin bore tunnels for London Underground’s Piccadilly Line and the Heathrow Express rail link were extended by 1.7 km and 1.6 km respectively. A new, 1.3 km-long, road tunnel provides airside vehicle access to T5 from the rest of the Heathrow complex, crossing above both Piccadilly Line and Heathrow Express tunnels and beneath taxiways. A 4.1k m, 3 m diameter stormwater outfall tunnel removes rainwater runoff from the airport area and incorporates four 20 m deep shafts. Also, new passenger track transit and baggage transfer tunnels link all three T5 buildings.
We considered ground movements arising from tunnelling to be among the major risks because of the way they could damage existing infrastructure and disrupt rail services or airport operations. So monitoring and control of ground movement became a key part of our risk management strategy. While most tunnelling has used tunnel boring machines, innovative developments meant that a single shell shotcrete lined tunnelling method, Lasershell (see overleaf), was used to build the many short, complex tunnels associated with the main bores.
Airside road tunnel
At 8.8 m diameter and 1.3 km in length this twin bore airside road tunnel is the largest of the five new T5 tunnels and required particularly delicate tunnelling. It crosses the existing Piccadilly Line tunnel with 3 m clearance and the Heathrow Express tunnel with 5 m clearance. Excessive movement of either existing tunnel would endanger railway operation and potentially force suspension of services. The airside road tunnel also passes beneath taxiways. Ground movement resulting from tunnelling had to be limited to ensure the safety of BAA’s operations.
To overcome this, the vertical and horizontal alignment of the airside road tunnel was fine-tuned to minimise the influence of tunnelling. In plan, the tunnel is curved to avoid taxiways and apron areas as far as possible, while in profile it undulates. Near their portals the twin bores of the airside road tunnel are extremely shallow. Risk assessments showed a danger of settlement if excavation broke out of the stable London clay stratum into the overlying gravel layer. So the gravel within 2 m of the tunnel crown was removed near the portals before tunnelling started and replaced with concrete.
A bespoke earth pressure balance tunnel boring machine was designed to minimise ground movement, allowing pressure to be maintained on the tunnel face even while the ground was being gouged away. We closely monitored settlement during excavation by instrumentation in the rail tunnels and on the surface, with surveys for distortion.
Airside road tunnel portals
At the airside road tunnel portals the transition from tunnel to ground level is made in cut-and-cover boxes. Here we constructed piled walls, excavated the ground between the walls and then constructed base and roof slabs. Conventionally piled walls like these would be propped with massive temporary steel struts to resist overturning forces as excavation advanced. However, analysis of the piles plus our carefully planned construction methodology meant we could eliminate the struts, saving 31 weeks on the excavation programme and greatly reducing safety risks inherent in handling temporary steel struts.
Temporary support was provided at intermediate levels as work advanced by pouring concrete slabs directly onto the base of the excavation – the slabs acted as struts. They were progressively broken out as excavation to full depth advanced and the permanent base slab was cast.
If movement was detected, additional slabs could quickly be installed to provide support and prevent excessive deformation. A special concrete mix that cured and provided strength quickly was designed for the job. In practice, no unplanned propping was needed.
Lasershell method
A new excavation and tunnel-lining technique developed by T5 tunnelling contractor Morgan Est was used to build cross-passages and short connecting tunnels for the rail lines. This Lasershell technique speeded up construction, improved worker safety and maintained ground stability.
The Lasershell method uses a back-hoe excavator to remove smooth scoops of ground from the working face. Its advance is continuous, but further ahead at the top than at the bottom – maintaining a profile like that shown below. The walls, crown and floor of the tunnel are lined with a coating of sprayed concrete as tunnelling advances. The geometry of this sprayed concrete lining is carefully controlled with the aid of laser surveying.
Completion of the ‘support ring’ in a steady progression closely behind the face means that both excavator and concrete gun (and their operators) remain beneath the protective canopy of a completed portion of tunnel lining. This contrasts with conventional tunnelling methods advanced in partial-face headings where the lining cannot be fully completed until the next headings have advanced. For the same reasons, ground stability is more likely to be maintained by the Lasershell method.
The next phase
Work will soon start on T5 phase two, creating a second satellite building and 13 new aircraft stands. This new satellite building is not needed until 2010 but to minimise disruption to the airport after T5 opens it made sense to complete all groundworks alongside construction of T5A and B.
The 18 m deep foundations for T5C are already in place and so is the passenger-tracked transit tunnel linking T5C to T5A. T5C’s superstructure will use prefabricated steelwork that will be brought onto site during night-time hours when aircraft are not flying, allowing T5C’s four levels to be built without hindering aircraft movements.
On completion, British Airways will transfer its entire operation, currently split between Terminals 1 and 4, to T5. As a result BAA will be able to address the investment and refurbishment needs of the four remaining terminals and complete the transformation of Heathrow airport.
The authors would like to thank Andrew Milius and Finlay Jardine for their help writing this article.
Biographies – Haresh Shanghavi, Jim Beveridge, Arthur Darby, Alan Powderham FREng
Haresh Shanghavi is a Senior Project Manager within Mott MacDonald’s Metros and Civils division and is currently Project Manager for London Underground’s upgrade of Victoria Underground Station.
Jim Beveridge is a Geotechnical Advisor and Commercial Director for Mott MacDonald’s Metros and Civils division. He is currently project director for the £6 billion Transnet upgrade of ports and freight railways in South Africa.
Arthur Darby is a Director within Mott MacDonald’s Metros and Civils business. He has managed very large projects, including the Channel Tunnel, the Channel Tunnel Rail Link, the Lesotho Highlands Water Project, diversion of the Yellow River and Kuala Lumpur’s Stormwater Management and Road Tunnel.
Alan Powderham FREng is among the UK’s foremost geotechnical engineers and a Director in Mott MacDonald’s transportation group. He is a leading practitioner of the observational method and value engineering, with experience on projects including Docklands Light Railway, the Channel Tunnel, Medway Crossing, Jubilee Line Extension, Heathrow Express, Boston Central Artery and London’s Crossrail.
Keep up-to-date with Ingenia for free
SubscribeOther content from Ingenia
Quick read
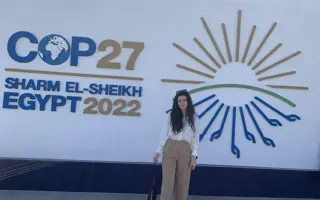
- Environment & sustainability
- Opinion
A young engineer’s perspective on the good, the bad and the ugly of COP27

- Environment & sustainability
- Issue 95
How do we pay for net zero technologies?
Quick read
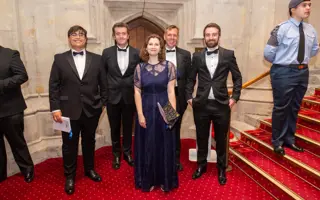
- Transport
- Mechanical
- How I got here
Electrifying trains and STEMAZING outreach
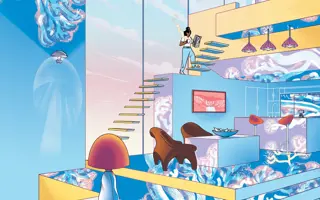
- Civil & structural
- Environment & sustainability
- Issue 95