Fishing for pollutants
An international consortium of engineering companies and university research departments, led by global maritime engineering and consultancy firm, BMT Group, has created autonomous robotic fish to seek out underwater pollutants. Luke Speller, BMT’s project manager, and other team members outline some of the challenges they overcame and where the new technology developed can be used.

Consortium members launching SHOAL II in the port of Gijon, Spain
Pollution monitoring in ports is a slow and expensive, but necessary, process. The increase in water traffic, discharge of untreated domestic and industrial wastes and the accidental spills of harmful substances by port vessels all contaminate water supplies and threaten local marine life. At the moment, teams of divers have to collect water samples by hand and then take them to a lab to be analysed. However, by the time samples have been collected and examined, any contaminants in a harbour could have spread to pollute a much wider area.
The SHOAL project (Search and monitoring of Harmful contaminants, Other pollutants And Leaks) was set up to tackle this problem. Funded by the EU and the research partners, it ran from 2009 to 2012. The groups working on the €3 million (€4.5 million with partners’ contributions) initiative developed three autonomous fish-shaped robots to monitor pollution across the port of Gijon, Spain. Working in real time, the fish combined flows of data from their sensors with environmental data from a manned base station. The resultant 3D map gave up-to-date details of port activity, thus ensuring the port authority could take quick action to remove any traces of pollutants.
In the beginning

Four modes of fish propulsion reflecting greater to lesser degrees of undulatory motion (l-r)
The project came together through a chance encounter in the London Aquarium. Researchers from a BMT Group team had been developing applications for networked autonomous underwater vehicles (AUVs). They saw a robotic fish designed by the University of Essex on display, navigating its way around a display tank. The robot’s movements replicated the biological movements of carangiform fishes – a class of fish including carp, cod and rainbow trout – which use the last half or third of their bodies for propulsion.
Underwater vehicles traditionally use rotary propellers to manoeuvre under water, but these can be difficult to manipulate, and propellers sometimes catch on undersea plant life. These robotic fish, on the other hand, propelled themselves with the movements used by real fish and had the potential to be agile and noiseless. Researchers at the department of Computer Science at the University of Essex, led by Professor Huosheng Hu, had designed their experimental robots to resemble a fish with four joints along its body and tail, driven by four remotely controlled servo motors. The BMT researchers saw that the University of Essex’s robots offered great possibilities – they were easier to handle than other AUVs, with a small turning circle, and caused less disturbance to their surroundings. Perhaps they could carry sensors, linked by a communications system, and monitor underwater pollution?
The SHOAL project became more complex as it developed, demanding expertise from several branches of engineering. With the University of Essex on board, BMT joined forces with a consortium of pan-European partners. The Spanish port of Gijon agreed to host the project, and French engineering firm Thales Safare SA, with expertise of undersea navigation and communications, developed a positioning and location system that could function in places where GPS signals could not reach. Hydrodynamics experts from the University of Strathclyde modelled the conditions of the port and how the water flows would affect the fish, and Tyndall National Institute, a leading research centre based at University College Cork in Ireland, designed the electrochemical sensors that the fish would use to sniff out petrol leaks or heavy metals.
BMT managed the project and devised the artificial intelligence (AI) to guide the fish and coordinate data communication. This involved managing the data flow between the fish and other information, including weather reports and the coordinates of other objects in the port. A central control base then managed this data communication and analysed the output from the sensors.
While BMT and the consortium partners drafted requirements for the final SHOAL prototypes, research continued for the robotics, communications and sensing teams. The robotics team at the University of Essex was busy adapting its fish from the London Aquarium. The team set out to build a more robust, simpler model that could cope with exposure to the port’s unfiltered waters, while still retaining a hydrodynamic shape. The new design also needed to house the rest of the system’s components, with an even distribution of weight and sufficient room for the power supply. SHOAL I was a ‘first draft’ of the fish used to test these factors, in combination with the fish’s locomotion and motor controls.
Location sensing
BMT developed a set of AI rules to guide the fishes’ actions, so that they could cover as much ground as possible and avoid obstacles in the port – see Positioning algorithms explained. Mapping the ships in the port was done by tracking the marine positioning system signals of larger boats at the base station, and relaying this information to the fish. Smaller boats and local obstacles were detected by the fish’s sonar communication system.
The fish can go anywhere within the defined area of the port. They need to be able to communicate with one another so that they can relay messages through a ‘line’ to the base station. The furthest fish from the station sends a message to its nearest neighbour, which relays the message to the next fish, which relays it to the station, which then updates the system.
BMT designed a hybrid robotic architecture to guide the fish around their environment. The architecture consists of three main units: a reactive agent, a deliberative agent and an off-board shore station agent.
The reactive agent uses feedback from the fish’s sensors to make quick decisions in order to maintain the safety of the fish and its environment. Using information from the sonar to detect walls and vessels, the reactive agent will avoid obstacles and determine swimming behaviour.
The deliberative agent uses the sensor feedback and information from the communications to make a model of the current environment and runs the higher-level AI and artificial potential field algorithms in order to decide where the fish should move to in the port.
Lastly, the shore station provides a global view of the system, as well as taking user input, to set motivations for the agents on the fish. Feedback from the shore station is fed into the deliberative agent, along with data from other fish, via the acoustic communications system. (See diagram to visualise the flows of information within this system). As the fish continuously take measurements of their position and chemical environment, and feed these back into this system, an emergent real-time underwater map results.
Location, location

The University of Essex autonomous robotic fish, on display in the London Aquarium from October 2005 to June 2007
One of Thales’s tasks within the project was to refine its communications module to map the fish’s locations underwater. GPS uses ultra-high frequencies, around 1.5 GHz, which hardly penetrate more than one millimeter in salt water. The solution was to use another biomimetic technology – acoustic signalling based on a sonar transducer (antenna) and modem connection, with much lower frequencies in the range of 15 to 40 kHz. This is similar to the underwater communications of whales and dolphins.
The acoustic environment of the port presented its own challenges: acoustic reflections (echoes) from nearby wharfs in the shallow waters at the port’s edges, and the noise of rain, real fish, waves, air bubbles and ships near the surface. The propagation of sound waves throughout the water also depends on the water’s temperature, pressure and salinity. With pressure increasing and temperature decreasing at greater depths, these factors also influenced the trajectory of the signals from the robot fish.
Thales developed complex signal processing algorithms in each fish to extract the signal from noise, and to adjust for environmental factors. The engineers tested the transducers and modems, first in a 10m tank, with walls that produced high levels of acoustic reflection, and then in sea trials in the Mediterranean. The range of the communications system extends to 1 km, and can reach up to 2.5 km in favourable environmental conditions.
For positioning, Thales fixed a set of four acoustic beacons on the sea bottom bounding the area where the fish operate, emitting signals every two seconds. The fish detect these signals, and use their knowledge of pulse recurrence and location to measure the propagation delays. Each fish’s position is then calculated by circle-crossing interception, or measuring where and when these signals overlap (see diagram). Once computed, a serial link in the fish sends the position data to the AI module, and to the shore station and the other fish by acoustic communication link.
Underwater sensing
The chemical sensing system was the final piece of the puzzle. The Tyndall group refined its chemical sensors, with miniaturisation being a big challenge. Traditionally, divers would take samples to labs, where very large equipment would analyse samples. For SHOAL, Tyndall used microfabrication to develop a scaled-down sensor system containing an array of sensors and instrumentation to fit inside the fish. When this was done, BMT incorporated into the system’s AI the timings needed to collect data from these sensors, and to communicate this data to the base station in the other fish.
Tyndall’s miniaturised sensor-on-chip environment includes electrochemical cells which use voltometric techniques to measure the amounts of pollutants in a given sample of water. Each cell contains three electrodes: a working electrode, a counter electrode and a reference electrode. The system applies a potential to a counter electrode to examine the currents formed at the interface between the working electrode and the solution. There are three cells inside each SHOAL robot: one to detect heavy metals, including copper and lead; one to detect phenol chemicals and one to detect dissolved oxygen and conductivity. The sensor system also contains oxidation reduction sensors to give a representation of overall water quality.
The sensing system in the fish is directly exposed to sea water, so chemical fouling could cover the sensor surfaces and render them useless. Tyndall designed a self-cleaning mechanism that applied voltage at the centre of a sensor to ‘blow off’ any chemical fouling that might occur.
When the partners were satisfied that they had achieved the optimal balance of weight, power and size restrictions, they developed SHOAL II. This final prototype housed all of the sensors, IT and communications equipment the fish required.
Testing times
Between SHOAL I and SHOAL II, Strathclyde University carried out computational fluid dynamics and tank tests to measure the hydrodynamic efficiency of the fish and recommend improvements. The shape of SHOAL II is now longer, at 1.5 m, so that it can accommodate the acoustic communication module. The body is also much more streamlined and hydrodynamic than its stub-nosed predecessor, reducing drag. At this stage, all of the individual components were incorporated into the SHOAL II protoype, which the teams then tested in the port.
The SHOAL project finished its test runs in June 2012. It has already demonstrated that it offers a solution for pollution monitoring in ports. There is scope for the model to be adopted by other ports, and the SHOAL partners are now looking to develop further commercial applications for the technologies they developed for the project.
Tyndall’s miniaturised chemical sensors can be used for in situ underwater sensing, and may have uses in medical and diagnostic testing. Thales plans to integrate its underwater communications system with its underwater telephones to add a capacity of data transmission in shallow water and noisy conditions. And in the future, Thales may apply the technology to its autonomous underwater vehicle CALAS, used for sonar operator training. Meanwhile BMT will continue to develop AUVs and AI systems. SHOAL itself may have further incarnations in the future.
For more about the SHOAL project, visit www.roboshoal.com
Keep up-to-date with Ingenia for free
SubscribeOther content from Ingenia
Quick read
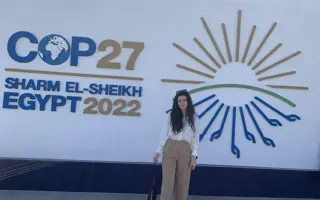
- Environment & sustainability
- Opinion
A young engineer’s perspective on the good, the bad and the ugly of COP27

- Environment & sustainability
- Issue 95
How do we pay for net zero technologies?
Quick read
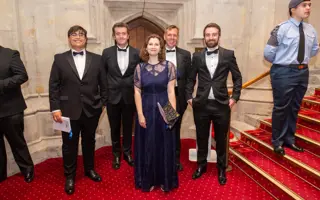
- Transport
- Mechanical
- How I got here
Electrifying trains and STEMAZING outreach
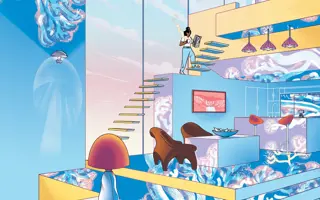
- Civil & structural
- Environment & sustainability
- Issue 95