Fusion turns to Engineering
After more than a half a century addressing the scientific challenges of controlled nuclear fusion, the research focus is moving from plasma physics to engineering. Chris Warrick from the Culham Centre for Fusion Energy explains how remote handling, materials and superconducting magnets are taking fusion energy into the reactor era.
Nuclear fusion has long been the ‘holy grail’ of energy production, with its promise of an effectively unlimited supply of fuel and the possibility of safe, carbon-free electricity production with much shorter-lived radioactive byproducts compared to fission. But the challenge of turning the power of the sun and the stars into a viable and economic source of commercial energy has taken so long that sceptics sometimes write off fusion as a technology that is ‘always in the future’.
The quest to tame fusion has been under way since the 1950s and research is now making significant progress. So much so that, as the physics behind the fusion process is better and better understood, fusion research programmes are shifting from a scientific challenge to an engineering one. The time has come for engineering companies to see how they can contribute to, and benefit from, the next generation of fusion projects.
So, what is fusion? In 1920, physicist Sir Arthur Eddington put forward – in a seminal presentation at the British Association for the Advancement of Science – that only the very powerful release of energy that results from the fusion of light atomic nuclei could produce the massive amounts of energy produced by the sun and stars. Indeed, the very high temperature (15 million °C) and pressure (billions of atmospheres in the centre of the sun) force 600billionkilograms of hydrogen nuclei to ‘stick together’ every second, fusing into helium and releasing huge amounts of energy in the process.
FUSION CHALLENGES
Since the 1950s, researchers have asked how we can harness that energy and use it in a controlled way to produce electricity in a power station. The scientific and engineering challenges are considerable, which is why it has taken so long. The favoured fusion reaction is between nuclei of deuterium (D) and tritium (T), heavy isotopes of hydrogen. D-T fusion, which produces much more energy per cubic metre than the sun, releases helium and a spare neutron that carries most of the fusion energy. It is the neutron’s energy that fusion researchers hope to capture.
As in the sun, nuclear fusion does not happen at room temperature. It requires heating the gases until the neutral atoms are separated into a plasma of interacting positive nuclei and negative electrons. For fusion to occur, the nuclei need to be travelling fast enough to overcome their natural charge repulsion. D-T fusion requires plasma temperatures of 100to 200million °C.

Tokamak schematic: In a magnetic fusion device, deuterium and tritium fuse to produce helium and high-speed neutrons, releasing 17.6 MeV (megaelectron volts) of energy per reaction. This is approximately 10 million times more energy than is released in a typical chemical reaction © CCFE
The challenge for fusion research has been to build a device that can keep the tenuous and unstable plasma away from a reactor’s walls long enough to sustain fusion. One of the most promising approaches has been to utilise powerful magnetic fields to control and confine the plasma. The tokamak, originally developed in Russia in the 1960s – the name comes from the Russian for ‘toroidal chamber with magnetic coils’ – has become the most efficient design in magnetic confinement fusion research.
Tokamaks confine the hot plasma inside a ring-shaped vacuum chamber, using magnetic coils to provide the fields needed to hold the plasma away from the walls. A hot plasma that hits the walls will cool rapidly ending the fusion process. Plasmas that are successfully held away from the vessel walls have reached conditions needed for fusion, most notably in the pan-European Joint European Torus (JET) experiment, based at the Culham Centre for Fusion Energy (CCFE) not far from Oxford.
While fusion research has been essentially a scientific challenge over the past half century, engineering has contributed significantly to that progress. Electrical engineering has played a major role in achieving magnetic confinement in a tokamak, which has helped to advance research at the Large Hadron Collider at the European Organization for Nuclear Research (CERN). Similarly, advanced mechanical engineering made it possible to build tokamaks that can withstand the enormous mechanical stresses induced by powerful plasma currents and magnetic fields.
EUROPE’S FUSION EXPERIMENT

Remote handling has allowed engineers to make many upgrades to the Joint European Torus (JET), despite its radioactivity. These same techniques will be crucial in any future fusion reactor © CCFE
JET is the world’s largest tokamak. CCFE operates the facility on behalf of Europe, providing the 300 to 400 engineers who maintain and upgrade the device. The European Fusion Development Agreement then enables scientists from European fusion laboratories to undertake experiments on JET.
This success in understanding the behaviour of the plasma has meant that key engineering questions have now come to the fore, such as the choice of plasma-facing wall materials, how to remove the helium byproduct from the fusion reactions and how to heat the plasma using radio frequency waves and accelerated particle beams.
JET is perfectly positioned to start to answer some of these questions. Its extensive remote handling capability means that CCFE’s engineers can carry out maintenance and upgrade work, regardless of the radioactivity inside the vessel.
REMOTE HANDLING
Remote handling technology has been a key part of the success of JET, which has been through a series of upgrades since it started up. JET’s inner wall and other components inside the vacuum vessel have been changed and upgraded several times, keeping it at the cutting edge of fusion research. Recently, CCFE undertook a major upgrade of JET. Over 18 months, the engineers changed 4,000 inner-wall tiles, replacing carbon tiles with tiles made of either beryllium or tungsten.
The quality of JET’s remote handling technology has already brought benefits to engineering companies in the UK. For example, Oxford Technologies Ltd, an independent engineering consultancy that specialises in remote handling, worked in collaboration with CCFE engineers to develop the system that has been in operation there since the mid-1980s. The company recently won a €3.5 million contract to provide engineering support for the design of remote handling equipment for JET’s successor, the international ITER device. This is just one example of the successful industrial takeup of engineering developed at Culham.
The interaction between the hot plasma and the container vessel’s wall tiles is a good example of how fusion research is moving from plasma physics to engineering. The wall tiles need to be robust enough not to excessively erode and pollute the plasma, and not to cause too much power loss from the plasma if they do (materials with high atomic mass contribute to very high levels of plasma radiation). The tiles need to allow fast-moving neutrons to pass through without causing too much damage. At the same time, the tiles should resist the unwanted retention of the fusion fuels, especially tritium, which could create unacceptable radioactivity levels within future power plants. Efficient tokamak operation is optimised if the fuels stay in the plasma. Fuels retained in the walls would adversely affect the efficiency and economics of future power plants.
In all, over 80,000 components were changed in the recent shutdown of JET, almost all by remote manipulators. The new beryllium and tungsten “ITER-like wall” is now being tested with full power plasmas. The initial results are encouraging, with fuel retention reduced by as much as a factor of ten.
JET will continue to be at the forefront of advances in fusion physics and engineering. Full D-T fusion experiments, planned for 2015, should see the machine break its own fusion records and approach the momentous break-even energy level, where fusion reactions generate as much energy as it took to heat the plasma.

The Joint European Torus (JET), hosted at the Culham Centre for Fusion Energy (CCFE), is the world’s largest fusion facility. It has produced 16 megawatts of fusion power and proved the technical feasibility of fusion using deuterium and tritium, currently considered the most efficient fuels © EFDA
THE NEXT STEP
JET cannot answer all the engineering questions. Fusion research needs a new machine if it is to demonstrate commercial scale fusion power and to integrate the key engineering components (such as superconducting coils and blankets to capture the fusion neutrons) required in a power station. The €14 billion ITER project is a collaboration of seven partners: Europe, Japan, USA, Russia, India, China and South Korea. Construction of ITER has started at Cadarache in the South of France, with the aim of making the first plasma in 2020.
So what will ITER demonstrate? By being twice as big as JET in linear dimensions, and eight times the volume, ITER’s plasma will retain its heat for much longer. Its larger ratio of volume-to-surface-area will increase the time taken for energy to radiate out of the plasma. With fusion power output directly dependent on plasma temperature, density and energy confinement, increasing energy confinement ensures that ITER’s fusion output will be much higher than JET’s. The designers are confident that ITER can achieve an output of 500 to 700 MW.
ITER will have much more advanced engineering. The all-important magnetic containment system will use superconducting niobium-tin magnetic coils rather than the conventional, actively cooled copper coils on JET. While superconducting coils are cryogenically cooled, which will require some of the energy from the device, they exhibit essentially zero electrical resistance, ensuring that it will take very little electrical power to create ITER’s magnetic fields. In addition, the resistive heating of superconducting coils will be much less than in the existing copper coils. ITER hopes to operate with plasmas that last hours compared to 30or so seconds in JET.
Although ITER will not be a true fusion power plant, it will investigate how fusion power from high-energy neutrons can generate heat for conversion into electricity. Once the neutrons have passed through the first wall, they will need to be absorbed and their kinetic energy turned into heat. This energy conversion will take place in a blanket of lithium wrapped around the containment vessel. As the neutrons penetrate the lithium and slow down, the blanket will heat up. This heat will be extracted to make steam and drive a steam turbine in a future power station. In addition, the blanket is designed to breed the tritium fuel.
With a 10-year half-life, tritium is rare and expensive. But tritium can be produced by nuclear reactions in lithium, which is readily availale. By bombarding lithium in the blanket with neutrons, the tokamak will be able to ‘breed’ enough tritium to fuel the tokamak. ITER will test different blanket designs to assess which offer the best neutron absorption and the best tritium breeding rates.
MATERIAL CHALLENGES
As fusion research moves towards practical reality, a common theme emerges, that of materials. Beryllium and tungsten are needed for the first wall, lithium for the blanket, niobium-tin for the superconducting magnets. CCFE is undertaking extensive materials modelling, especially to understand which materials may be most suitable for the vacuum vessel, such as low-activation steels. Neutrons that are not absorbed in the lithium blanket could damage the vacuum vessel and supporting structures physically and make them radioactive. Clever choice of materials can minimise damage and activation.
Modelling advances our knowledge only so far. We also need a major materials testing facility, such as the International Fusion Materials Irradiation Facility (IFMIF). IFMIF is designed to generate a continuous stream of neutrons with energies equivalent to those produced from the D-T fusion reaction. The facility will allow engineers to test candidate materials in parallel with the programme of activities on ITER. In many ways, commercial fusion is just as dependent on results from materials research as from ITER.
How long will fusion take to become a reality? ITER and materials research should expect to provide the key results we need to finalise the design of the first electricity-producing demonstration reactor sometime in the mid-2020s. The first reactor could be running in the mid-2030s with commercial reactors by 2050.
INDUSTRY SPIN-OFFS
There have been tangible benefits from the long and sustained support of fusion research. For half a century, Culham and other fusion establishments have improved the high voltage circuits, power supplies and flywheels needed to power the many different magnetic coils on a tokamak. In the process, they have pushed forward the frontiers of high-voltage electrical engineering and this has brought benefits to electrical engineering in general. For example, in the 1990s, in their Altrobus hybrid bus, Ansaldo Richerche and Fiat Iveco used power invertors and battery chargers that were based on devices developed for JET’s high-voltage circuits. By the end of 1999, a hundred such hybrid buses were operating in Genoa.
More recently, NNC (now part of AMEC) developed a new bonding technique – hot isostatic pressing – with assistance from CCFE engineers – enabling them to produce prototype tile components for ITER. This technique has also been used in other parts of AMEC business – notably in a new copper-bonded steam generator for use in a sodium-cooled fast fission reactor.
Another company to benefit from CCFE support is Reaction Engines. Based at Culham since 2001, Reaction Engines is developing a reuseable spaceplane, SKYLON. This is designed to enter space, deliver up to 10 tonnes of cargo and then return to Earth. Crucial to realising the huge potential of this project is the SABRE engine which can ‘breathe’ air like a jet engine while in the atmosphere, becoming a rocket engine in space. The heat exchanger pre-coolers are one of the most challenging features of the SABRE design. Initial collaboration with CCFE allowed Reaction Engines to build up significant experience in brazing and tube manipulation techniques in the early days of development.
ITER poses significant engineering challenges. It is also a major business opportunity for engineering companies. Culham’s Fusion and Industry programme is helping companies in the UK to benefit from the commercial opportunities, notably in contracts for ITER. This programme has already helped to secure €180 million worth of contracts.
In 2010, the Engage consortium, which includes WS Atkins International Ltd, won a major engineering contract, worth approximately €150 million, for ITER’s buildings and civil infrastructures. More recently, Energhia, a consortium led by the UK engineering company, Halcrow, and which also includes France’s Altran and Spain’s Idom, has won a contract worth up to €27 million to provide overall supervision. This work includes design checking services, coordination of interfaces and project management of between 15 and 20 ITER construction contracts.
It is now that things get serious with ITER, as fusion research intensifies. In the next decade, ITER will place some €5 billion worth of contracts for construction and for the components and systems that make up ITER. These are huge opportunities for the UK’s engineering companies.
While the value of the contracts is itself an incentive, perhaps more important is the increased knowledge and expertise gained as fusion moves ever further from scientific research into engineering development.
BIOGRAPHY
Chris Warrick is the head of communications at CCFE. Graduating with a physics degree from University College Swansea in 1988, he undertook experimental fusion research at Culham from 1990 to 2001. Since then, he has been in the communications group with particular responsibility for schools and public outreach; he has been leading the group since 2010.
Keep up-to-date with Ingenia for free
SubscribeOther content from Ingenia
Quick read
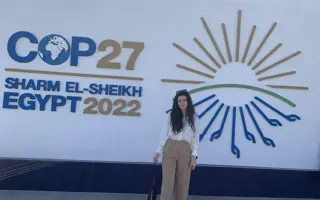
- Environment & sustainability
- Opinion
A young engineer’s perspective on the good, the bad and the ugly of COP27

- Environment & sustainability
- Issue 95
How do we pay for net zero technologies?
Quick read
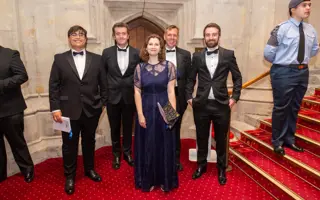
- Transport
- Mechanical
- How I got here
Electrifying trains and STEMAZING outreach
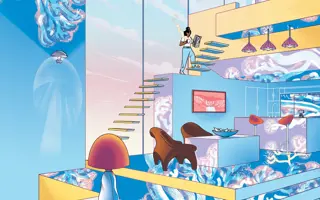
- Civil & structural
- Environment & sustainability
- Issue 95