Green facelift for concrete buildings

The first panel goes onto the renovated Angel Building in Islington, north London. The unitised panels installed were prefabricated complete with glazing, insulation and finishes. Fixing brackets were installed to the slab perimeter in preparation for receiving the unitised panels © Allford Hall Monaghan Morris
Attempts to reduce the UK’s carbon footprint will have to tackle the energy used in existing buildings, including many thousands of concrete-framed buildings put up between the 1960s and the 1980s. These buildings are often inefficient to heat and cool, uncomfortable to occupy and expensive to refurbish. New ways of cladding them could transform them into energy-efficient, low carbon buildings at a fraction of the cost of rebuilding. Professor Doug King FREng, Chief Scientific and Engineering Advisor to the Building Research Establishment, explains some of the benefits of recladding.
Buildings account for around 45% of all carbon emissions in the UK. They will, therefore, play a major role in plans to achieve the government’s commitment to tackle global warming and climate change with an 80% reduction in emissions of greenhouse gases by 2050.
Architects and civil engineers have focused on designing and constructing new buildings with low carbon footprints. However, this does little to improve the current building stock – an estimated 80% of the buildings which will be around in 2050 already exist. It is not practical to demolish and replace them all in a move that would, in any case, have its own implications for carbon emissions, given the need to remove and replace the large amounts of concrete. The energy performance of existing buildings needs to be improved if carbon targets are to be met.
The thousands of concrete-framed buildings that were built between the 1960s and 1980s are among the least energy-efficient – see Carbon counting. Many of these unrefurbished buildings will find it difficult to attract tenants when Energy Performance Certificates, which became compulsory under an EU Directive in January 2013, are issued. While a large number will need to be demolished, alternatives to rebuilding would ensure that many older buildings were able to meet new energy performance standards. The area with the greatest potential to improve the performance of most concrete-framed buildings is the cladding – the skin of glass, window frames and panels that forms the external walls of buildings.

Thermal emissivity coatings. As window glass heats up by absorbing solar radiation or by conduction from the heated interior it tends to re-radiate infrared in all directions. Selectively treating the panes of glass in a double glazed window with low thermal emissivity coatings controls the direction of re-radiation. Thus heat from the interior is reflected back and unwanted solar heat, which would lead to summer overheating, is rejected © Doug King
CLADDING AND CONDUCTION
Poor cladding causes most of a building’s heat loss and condensation in winter, and most of the heat gain and solar glare in summer. Other improvements, such as improving the heating and ventilation systems, are important, but the cladding is often the key.
The first items to fail on old cladding systems are usually the flexible gaskets that seal a variety of joints including those between glazing and metal window frames and between the cladding panel, the window frame and concrete structure of the joints. Failure of these seals causes draughts and significant heat loss through the gaps. For example, last year, when engineers examined the underperforming air conditioning system on a 1980s government building, they found that the poor quality of the building’s skin was a more serious problem. Replacing this could cost £1,200 per square metre, but for just £200 per square metre they could simply replace the failed gaskets of the cladding and solve most of the problem.
Heat conduction is also common in these buildings. This happens through the windows, usually single-glazed, via the opaque cladding panels and through the metal framing that designers often used in buildings of the period. A well-designed window should let in sufficient light while minimising heat loss and capturing the sun’s warmth in winter, and minimising solar gain and glare in summer. Today’s glass is ‘whiter’ than the glass installed 40 years ago, allowing more light through. When set as double-glazing in insulated frames, it also provides good insulation. Adding fins to the outside of a building can shade the sun-facing façades, solar blinds can provide variable shading and control overheating.
There are other ways to control the flow of heat through windows. Applying ultra-thin metallic coatings to each replacement pane of glass, protected within the double-glazing void, can reduce radiation through windows.
A coating on the outside pane reflects summer solar heat out of the building, while one on the inside pane reflects the heat back into the building – see Thermal emissivity coatings.
GE FOGG BUILDING
A couple of recent London projects have set out to maximise the benefits of recladding. Since it was built in the 1970s, the GE Fogg Building in the middle of the Queen Mary, University of London campus in East London has housed the university’s School of Biological and Environmental Sciences. Until a couple of years ago, the seven-storey, 7,000m² concrete structure had been rapidly degrading. Plastic covers to untreated steel window frames had cracked, allowing the steel to corrode and the windows to leak. The reinforced concrete frame was corroding near the outer edges. The building was cold in winter and inefficient to heat due to its leaky façade. In summer, some staff erected makeshift blinds to provide shade from extreme solar glare.
It can be disruptive and expensive to remove existing cladding in an occupied building, particularly where the original insulation contains asbestos. A better solution may be to leave the old panels in place, and cover them with a new layer of cladding. Mott MacDonald, the engineering and development consultancy, working with Fraser Brown MacKenna Architects, adopted this solution for the GE Fogg Building when carrying out the works while the university staff remained in the building.
Modelling showed that photovoltaic cells in the roof lights and parts of the vertical glazing could meet some of the building’s electricity demand. There was little available space on the roof for solar panels on the GE Fogg Building; instead photovoltaic cells were incorporated into the new double glazing. The outer pane is actually a solar panel, letting through sufficient light while converting the excess into electricity. The 120 m² of photovoltaic cells produce 2,700 kWh of electricity per year.
Mott MacDonald reclad the building at a cost of £4 million. The project achieved a 65% improvement in the thermal performance of the building’s cladding panels. The work has extended the building’s life at a fraction of the cost of erecting a new structure. Energy demand has fallen by 70%, and maintenance costs are lower, with carbon emissions cut by 6 kg CO2 /m².
GUY'S HOSPITAL
On a much larger scale, Balfour Beatty began a project last year to reclad most of the two 34-storey towers of Guy’s Hospital in south London. Built in the early 1970s and once the tallest building in London, the immediate problem was concrete spalling – concrete that is flaking, pitted or broken, usually due to corrosion of steel reinforcement bars. This exposed the steel reinforcing the concrete to further corrosion and posed a risk to passers-by below. The main challenge was to install new aluminium cladding and glazing panels safely and efficiently on a fully functioning hospital. This required structured planning and intricate scaffolding which had to be suspended on the on the outside of the building.
Once the overcladding is complete, the team will have to go inside the working hospital to remove the existing windows. Arup, the project engineer, has estimated that the annual savings in operational carbon emissions through the more efficient cladding would pay back the embodied carbon spent in carrying out the refurbishment in about 13 years.
THERMAL MASS
With the cladding properly dealt with, the heating, cooling and ventilation become secondary problems. In the perfect building with the perfect cladding, there would be no need for heating or cooling at all. Indeed, in most buildings, the main function of the mechanical and electrical systems is simply to correct problems within the building’s fabric.
While they may pose many problems, old concrete-framed buildings can carry one significant advantage in their large thermal mass. They retain heat. Concrete has a much higher heat capacity than the materials in suspended ceilings or even in the furniture within buildings. Exposed concrete (concrete that is not covered by plasterboard and other materials) absorbs heat from daily activity and limits the temperature rise. At night, when there is little heat being generated, the concrete re-emits stored heat into the interior. In winter, this prevents the building from getting too cold during the night and reduces the need for pre-heating the following morning. In summer, ventilating the building with cool night air can discharge surplus heat, cooling the whole structure in preparation for the following day.
Thermal mass works well with a strategy known as displacement ventilation. This replaces hot, stale room air with clean air at the desired temperature. The air does not have to be refrigerated to the same low temperatures as conventional air conditioning, so outdoor air can cool the building for most of the year, leading to significant energy savings. And as the air does not need to be heated to such a high temperature in winter, a low-grade source, such as heat pumps, rather than fossil-fuel boilers can supply heat.
The displacement ventilation solution also reveals a significant disadvantage of old concrete structures: by modern standards they usually have a low floor-to-ceiling height. This leaves little or no room for the large underfloor or ceiling ducts usually needed for displacement ventilation systems. When converting its own 1970s Fitzrovia offices in London, Arup solved this problem by running large ducts down the outside of the building, making them an architectural feature within the new triple-skin façade.

Before and after photographs of the Angel building © Allford Hall Monaghan Morris © Valerie Bennett
ANGEL BUILDING
This approach shows how careful use of external cladding, and the services it can carry, can turn old buildings into architectural masterpieces, while still saving money and saving carbon compared with demolition and rebuilding. Until recently, the Angel centre was a tired and unloved early 1980s concrete office block at the Islington junction in north London. It was scheduled for demolition when the design team of architect Allford Hall Monaghan Morris, structural engineer Adams Kara Taylor and services engineer Norman Disney & Young proposed to retain the existing structure – comprising four sides of a rectangle with an unused courtyard inside – and erect the new building around it.
The idea had plenty going for it. Although the cladding and the services were worn out and had to be replaced, the structural concrete was in remarkably good condition. There were also unusually large floor-to-ceiling heights, 3.7m, which put very few constraints on the type and location of services. Indeed, the concrete frame had considerable structural ‘redundancy’ which meant that the designers could cut holes where necessary without compromising the building’s strength. The thermal mass could be part of an efficient and sustainable heating and cooling system.
Preserving the building also meant that there would be no need to demolish and dispose of 39,500m3 of concrete. Nor would there be any need for an equivalent amount of new materials, with clear advantages in sustainability. The solution in this case was much more than a recladding; the design extended the old building by adding some steel framing on two sides plus an additional fifth floor and roof terraces on top. It also converted the old courtyard into extra office space plus a large covered atrium.
The Angel Building underlines an important reason for reusing existing buildings: it can reduce waste. According to the Waste and Resources Action Programme (WRAP), the campaign and advisory body on UK waste reduction, construction, demolition and excavation for buildings is responsible for over 100 million tonnes of waste every year, about a third of all the UK’s waste. Much of this waste goes straight to landfill. WRAP has been campaigning to improve the process of recycling, and to halve the amount of waste that goes to landfill. While it is certainly preferable to recycle material from old buildings, in reality, demolishing a building and crushing concrete for reuse is not a carbon-free activity. WRAP is urging the construction industry to reduce the amount of waste it creates in the first place, and avoiding the demolition of buildings helps this.
The developer of the Angel Building wanted to provide high specification office space and set three additional challenges for retaining the existing structure. The project had to be cheaper than complete demolition and rebuilding. Secondly, refurbishing the structure had to be quicker – with rental income of £10 million per year from 24,000 sq m of net floor area, a few months saved in construction was important. Finally, the new structure had to be more sustainable, with a lower carbon footprint.
The first two targets were relatively straightforward. The project team could demonstrate that the £72 million cost was 15% cheaper than demolition and reconstruction, and that this approach could save three months of rental income. Measuring the sustainability advantages was more difficult.
Conventional methods for assessing sustainability take little or no account of embodied carbon saved by reusing a building – see Carbon counting. Indeed, the Angel Building would have achieved its Building Research Establishment Environmental Assessment Method (BREEAM) rating as ‘excellent’ even if the old building had been completely demolished. Consequently, the team developed a concrete carbon calculator, using data assembled by the University of Bath, to identify the embodied energy in the building’s concrete structure. Applied to the Angel Building, this model showed that demolishing the concrete structure and replacing it with a steel frame would have wasted 7,400 tonnes of all greenhouse gases, roughly equivalent to the emissions of running the whole building for 13 years. The team was therefore able to argue that the refurbished building could run ‘carbon-free’ for 13 years, compared with new build.
For heating and cooling, an air displacement system pushes air through large ducts concealed in a new 450mm raised floor, entering the offices through grilles set in the floor. In winter, the hot return air from the system mixes with outside air to achieve the 19°C supply temperature, effectively recycling two thirds of the heat that would otherwise be thrown away. Overall, the team estimated that the heating and ventilation system reduced carbon emissions by more than 40%, compared with a conventional fan-coil system.

The atrium entrance to the Angel Building. The refurbished building now includes 260,000ft² of net space stripped back to the frame, enhanced, reclad and renewed with energy saving features and a BREEAM ‘excellent’ rating © Allford Hall Monaghan Morris
The Angel Building has been a success in a number of ways. It was shortlisted for the prestigious Stirling Prize for architecture. It was a commercial success with a full complement of tenants. The project was a model of sustainable reinvention of tired old concrete buildings. In addition, the Angel Building was a winner in the Chartered Institute of Building Services Engineers’ Building Performance Awards, where it pipped the GE Fogg Building to the prize.
These three projects, the GE Fogg Building, Guy’s Hospital and the Angel Building show just how much architects and civil engineers can achieve by imaginative use of modern material and technologies on older buildings. As well as helping to achieve the UK’s ambitions for saving energy and reducing emissions of CO₂, these new cladding techniques can also provide a facelift to some of the least admired architectural landmarks on a city’s skyline.
Keep up-to-date with Ingenia for free
SubscribeOther content from Ingenia
Quick read
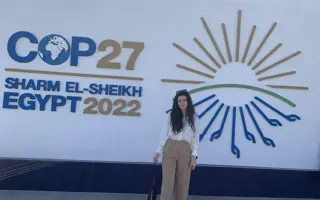
- Environment & sustainability
- Opinion
A young engineer’s perspective on the good, the bad and the ugly of COP27

- Environment & sustainability
- Issue 95
How do we pay for net zero technologies?
Quick read
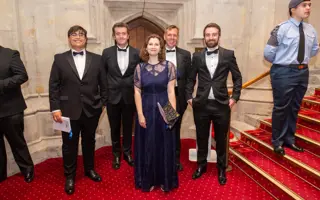
- Transport
- Mechanical
- How I got here
Electrifying trains and STEMAZING outreach
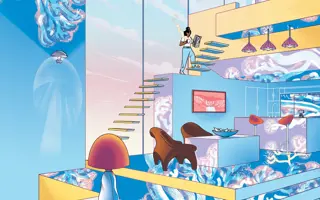
- Civil & structural
- Environment & sustainability
- Issue 95