Harnessing Offshore Winds
Wind farm operators are developing large arrays of turbines offshore, where winds are stronger and more consistent than onshore. Next-generation wind farms will be placed further offshore, in deeper water, and exposed to harsher environmental conditions. Ingenia examines the options available and how industry is addressing the engineering challenge of creating cost-effective structures.
Offshore turbines currently provide one third of the electricity generated in the UK from wind, and with more than 3.6 GW of installed capacity the UK generates more offshore wind energy than any other country. A recently published report by the Royal Academy of Engineering, Wind Energy (April 2014), points out that 7.7% of the UK’s electricity generation is derived from wind.
Building turbines offshore allows for large arrays to be erected, with many more turbines than could be sensibly erected onshore. Although it is cheaper to build turbines onshore, it is not possible to achieve the scale required given difficulties receiving planning permission.

UK wind speeds are higher offshore. The wind also blows more consistently and is less turbulent, making it more suitable for power generation © BERR Renewables Atlas
In April 2014, in a package of eight renewable energy projects, the Department of Energy and Climate Change announced five new offshore projects, with a total capacity of more than 3GW. The scale of these new offshore wind farms will be comparable to small onshore power stations.
Existing turbines are about 30 km from the shore, in water depths of 20 to 30 metres. The London Array, for example, one of the best known offshore wind farms, is about 20 km from the Kent and Essex coasts in waters up to 25 m deep. Many of the shallow water sites are now built on or have been granted planning permission. Future development has to move towards deeper water. For example, the current tender round for UK offshore wind is for sites up to 60 m deep. In the future, developers may consider building arrays up to 200 km offshore, in waters of up to 200 m; however, proximity to the coast will be a consideration, as the electricity must be brought ashore cost-effectively.
The future of offshore wind power depends on reducing fabrication, construction and installation costs, while providing a stable engineering design. The government-backed Offshore Renewable Energy Catapult stated in its report Generating Energy and Prosperity (March 2014) that the UK’s offshore wind industry could support 150,000 jobs, provide £6.7 billion of economic value, and prove one of the country’s most successful export industries if it can deliver on plans for rapid expansion. However, the scaling up of the industry envisaged by the report is dependent on the UK capturing a greater share of the supply chain, and at the same time slashing costs for the technology.
Developing cost-effective foundation designs will be key to the expansion of the offshore wind industry. Most existing wind turbines are on foundations fixed in place by a single pile driven into the seabed. Putting turbines in deeper waters will require different designs for structures and foundations. The alternatives include fixing turbines to multiple footings and designing floating structures. To reduce costs, it will be necessary to develop integrated and advanced design tools so that the entire wind turbine system can be optimised.
LOADING CONDITIONS

Figure 1 – Loads on an offshore wind turbine

Figure 2 – Different options for fixed structures where V is a vertical load, H is a horizontal load and M is the moment. © The University of Oxford
The loading applied to an offshore wind turbine consists of wind and wave forces (Figure 1). The wind load on the blades acts at the hub some 90 m to 110 m above the water. This force is typically between 1 MN (meganewton) and 2 MN, being dependent on the rotor diameter and the wind speed.
Waves and currents also act on the structure, usually applying a resultant force at a height close to the surface of the water. In shallow water, say 20 m, this might be 3 MN, while in deeper water, say 50 m, this force might increase to 6 MN. Although the horizontal force is important for design, it is the overturning moment that determines the choice of structural configuration. The example loads here result in overturning moments at seabed level of between 150 MNm and 620 MNm. Actual design values depend on site-specific conditions and structural configuration. The mass of the structure might be 600 to 1,000 tonnes (approximately 6 MN to 10 MN).
For fixed structures, there are two options for transferring the applied loads into the ground, as shown in Figure 2. This can be done by a single connection with the ground, such as a single footing (for example, monopile or gravity base). This is usually the simplest and cheapest option for shallow water sites, where the overturning moment is small. As the water depths become greater, this option becomes less feasible and so it is necessary to move towards a multi-footing structure. In this configuration, the overturning moment is transferred to the ground via the ‘push-pull’ action on opposing footings.
For the multi-footing structure, the vertical load helps determine the distance between the footings, and subsequently the magnitude of the load at each footing. A designer will be concerned with reducing the structural weight and footprint, which may depend on how much tension can be taken by the upwind footing during extreme loading. The complexity of multi-footing structures typically increases the cost of these structures when compared to a single footing structure.
DESIGN CONSIDERATIONS
Industry and government are focused on this task of reducing costs, with an aim to cut costs by about 30% to £100/MWh by 2020, taking in all costs, from construction to decommissioning. Foundations and installation account for between 20% to 30% of the installed cost for an offshore wind turbine. Optimising this part of the design could lead to considerable savings. In addressing these engineering challenges, the wind industry can look to the offshore oil and gas industry, which has designed and built numerous fixed and floating structures over decades, in some cases in water over 2,000 m deep. However, wind turbines pose new challenges particularly from the loading patterns – see FIXED TURBINE ALTERNATIVES
Two types of fixed structures are used for offshore turbines: a single footing structure or a multi-footing structure. All fixed structures have a transition piece between the subsea structure and the turbine tower. This is a critical connection in the design.
Around three-quarters of current turbines are fixed to steel monopiles. These are hollow steel tubes, driven into the seabed with a large hammer. They are simple, cheap to make and have been installed in water depths of up to 30 m, supporting 2MW to 4MW turbines. In deeper water, the wave forces become more significant so that the size of pile and weight of steel increase, leading to higher costs.
A number of developers are considering deploying larger monopiles to support wind turbines rated at 6 to 8 MW. These will weigh more than 1,000 tonnes and will present challenges for installation, as the diameters are between 6m and 8m with steel walls up to 100mm thick. It is possible that even larger monopiles might be used in still deeper water, and research is being conducted by the joint industry/university project PISA (Pile Soil Analysis) to aid this type of advance. The challenges with scaling up design in this way relate to the robustness of current and new design methods. To keep costs down, it is important to minimise steel thickness while ensuring that the pile does not buckle during installation.

Figure 3 - Different fixed support structures: (a) gravity-base, (b) monopile, (c) monocaisson, (d) piled multi-footing structure, (e) suction caisson multi-footing structure, (f) jacket/lattice structure © The University of Oxford
A small number of offshore wind turbines are on gravity-base foundations. These are typically large, flat-bottomed concrete structures containing ballast, typically of sand, iron ore or rock. The base width is designed to suit the soil conditions, being large enough to provide stability against overturning. The wind turbine tower sits on a steel or concrete shaft that rises from the base. Typically the substructure would have a base diameter of about 30 m, and consist of 6,500 tonnes of concrete with 3,000 tonnes of ballast.
An advantage of concrete gravity-base foundations is their lack of exposure to steel prices and lower maintenance costs, owing to concrete’s durability in the marine environment. Gravity base foundations have been used in shallow water and can be used on soft or firm seabeds, without the need for piling. They can be designed to float to site using tugs for transport and the process can be reversed for decommissioning.
A small number of offshore turbines are supported by jacket or lattice structures: forms of multi-footing structures. Jacket structures are commonly used in the oil and gas sector, in water depths of about 150 m. The jacket can be a four-legged or three-legged pylon-like structure of welded steel bracings with diameters up to 2 m. Steel piles at each corner pin the structure to the sea floor. Jackets are considered suitable for wind turbines in water depths of 20 to 50 m or more, and are likely to support turbines in next generation wind farms. Jacket structures will be more versatile as the water depths increase; however, the construction costs are greater compared with monopiles, largely due to the fabrication of complex joints. Transportation to site is also likely to be more complex compared with monopiles.
The remainder of fixed offshore turbines consist of variations of the multi-footing structure. For example, the tripod is essentially a three-legged steel jacket, but with variations on the framework connecting the piles to the tower support column. An alternative design is the tripile, where the three piles are connected to the turbine tower via a transition piece above the water surface. For fixed structures, there are issues of scour around the foundations, a process where the seabed currents erode away the soil around the foundation. Measures to protect against scour can add considerably to costs. For any of the designs, the issue of fatigue at the various connections must be addressed.
FIXED TURBINE RESEARCH
The Danish energy firm DONG, which will be developer for three new offshore wind projects recently approved, favours foundations fixed to the seabed. Developments in monopiles are accommodating larger turbines than were expected only five years ago. In scaling up monopiles, DONG optimises the design by maximising the ratio between the pile’s diameter and the thickness of steel. This requires the development of new technology for installation, and means that the transition depth between monopiles and jackets, based on cost, is likely to increase. At depths to 20 m, the financial case for monopiles is clear, while above 40 m it is likely that jacket structures will win out. Between 20 and 40 m there are variations in the optimal solution, and other factors such as soil conditions and size of turbine come into play.

Located 20km from the Kent coast, the London Array is the world’s largest offshore wind farm. 177 piles were needed – one for each of the 175 wind turbines and two more for the offshore substations. A purpose-built vessel installed the foundations in deep water. The vessel has four extendable legs that lift the deck out of the water to create a stable platform from which the piles can be hammered in. Work started in 2011, and the array went live in April 2013 © DONG
One of the ways to reduce installation costs is to find new ways of fixing structures to the seabed. As an alternative to driving piles into the seabed, DONG is developing a suction caisson founded jacket structure in a project funded under the Carbon Trust’s Offshore Wind Accelerator, a UK government and industry partnership.
Suction installed foundations are long established in the oil and gas industry to fix floating structures to the seabed at almost any depth. They have been used for a small number of fixed oil and gas platforms. Essentially an upturned steel bucket, the foundation is driven into the ground by pumping water out from the inside, once a seal is made between the bucket and ground. The foundation is ‘sucked’ into the ground.
A suction caisson foundation on a jacket structure is unlikely to lead to savings in materials, compared with piles. However, installation costs will be reduced because the installation time is likely to be shorter and less equipment is required. Installation of the suction caissons might take about a day, while driving piles into the ground for a jacket could take about four days. Installing suction caissons is virtually silent by comparison with pile driving. This is becoming an important consideration for wind farm construction.
There are concerns about the effect of pile driving noise on sea life, such as dolphins, which is leading to the emergence of legislation, principally in Europe, restricting the noise created when installing offshore turbines. Suction caissons are suitable for a range of soils including sands and clays, but not where there are large obstructions such as boulders. It is essential that the soil conditions allow a seal to enable the foundation to be sucked into the seabed.

A suction caisson founded tripod jacket structure. Installation simply involves using suction to penetrate the foundations into the seabed © DONG
By combining the advantages of monopile and suction caisson technology, the Danish consultant Universal Foundation is promoting the mono-caisson support structure. This is similar to a large diameter gravity-base foundation, but with skirts that penetrate the ground with the aid of suction. Research on both monocaisson and multi-footing caisson foundations has been carried out at Oxford University since 2000, specifically for offshore wind turbines.
FLOATING ALTERNATIVES
The prospect of operating in deeper waters has turned attention to the use of floating wind turbines. In shallow waters, the fabrication, transportation and installation costs for floating structures make them more expensive than fixed structures. But in depths beyond 50 m, floating structures may well compete economically.
Floating platforms combine a buoyant element with a counteracting ballast system, along with a seabed mooring. As yet, there are no commercial floating wind turbines in operation. However, there are three types of floating systems under development: tension-leg, spar and semi-submersible. The oil and gas industry uses all of these approaches in its deep-sea operations.
The principle behind the tension-leg platform is to fix a buoyant platform below its buoyancy level with legs or cables at the corners of the platform. The pull of the platform’s buoyancy keeps the legs taut. The legs can either be secured to a template, such as a heavy concrete ring that is anchored to the seabed, by piles or suction anchors. Holding the platform underwater limits the wave loads. A tension-leg platform could be suited to water depths from as low as 50 m up to 1,500 m. Their installation requires specialist ships.
The basic structure of a spar consists of a large tube, floating upright and anchored to the seabed by mooring lines. The turbine is fixed to the top of the spar. Spars are suitable for water depths of 120 to 700 m. Once again, specialist ships are needed to install spars.
Hywind is a pilot floating 2.3MW wind turbine, operated by Statoil, anchored 10 km off the southwest coast of Norway. It is a 100 m high steel cylinder spar with a diameter of just over 8 m, 6 m at the waterline. The spar weighs 1,500 tonnes and contains about 5,000 tonnes of ballast. The small cross section reduces the impact of wave motions. The weight of the ballast dampens wind-induced sway.
A semi-submersible platform carries the turbine on pontoons ballasted below the water line and moored by catenary (hanging cable) lines fixed by drag anchors. The lines are made sufficiently long to minimise vertical loads on the anchors. The main advantage of a semisubmersible platform over other floating structures is the ease of installation, with no need for specialist shipping. It can be towed into waters as shallow as 10 m for installation in port, without the upending or other manoeuvres needed for other floating designs. The design is highly susceptible to sway, pitch and roll and its large surface makes it sensitive to wave and tide movements. Of course the size of the structure requires a significant amount of steel, making the design heavy and costly.
FLOATING RESEARCH
Last year, the Energy Technologies Institute (ETI) commissioned and funded a 12-month, £4 million front end engineering design (FEED) study of a tension leg floating platform. If taken to construction and deployment, an investment of up to £21 million will be required, but it could be deployed off the UK coastline by as early as 2015.

The first large-capacity, 2.3 megawatt floating wind turbine is Hywind, which became operational in the North Sea off of Norway in 2009 © Øyvind Hagen - Statoil
ETI studies have shown that floating wind farms in areas of increased wind speeds off east coast of Scotland, northeast of England, southwest England and the Irish Sea have the potential to significantly reduce offshore energy cost. The water depths would be 60m to 100m.
To be cost-effective, these sites must allow worker access from a port base, rather than accommodating workers offshore. In addition, the transmission of the electricity to shore will be critical. The ETI has noted that at 70 to 80 km it becomes more cost-effective to One benefit of tension-leg structures comes from the possibility of dockside construction; this is production engineering rather than project engineering. There are also significant export opportunities for offshore wind at depths of 50 to 100m or more. All the technology is being developed in Europe and it is all capable of working in deeper water. The European Wind Energy Association agrees, stating that deep offshore designs can be exported. Expertise, skills and technologies developed in Europe can be exported across the globe, initially to Japan and the US. However, such opportunities may not last. R&D into offshore wind technology is gathering momentum in the US, Japan, and China. According to a recent report from Accenture, Shanghai, Jiangsu, Zhejiang, Shandong, Fujian and other coastal areas have made plans for offshore wind power development. transmit power to shore as DC rather than AC. For an offshore wind farm, this causes a step change in cost. The consulting engineers BVG estimate that a typical HVDC substation requires a platform weighing more than 9,000 tonnes, five to ten times heavier than needed for an HVAC substation. Optimising the electrical aspects of offshore wind and the connection to shore is an area of active research.
The ETI questions the view that 50m is the depth where floating structures can match the cost of fixed structures for 4-MW turbines. It believes that floating structures can compete, depending on site conditions, with fixed structures in shallower waters, perhaps as low as 30m. The tension-leg design is at an earlier stage of demonstration than either spar buoys or semisubmersibles; it does have the greatest potential for cost reduction, as it uses a lightweight hull, combined with high vertical load anchors.
One benefit of tension-leg structures comes from the possibility of dockside construction; this is production engineering rather than project engineering. There are also significant export opportunities for offshore wind at depths of 50 to 100m or more. All the technology is being developed in Europe and it is all capable of working in deeper water.
The European Wind Energy Association agrees, stating that deep offshore designs can be exported. Expertise, skills and technologies developed in Europe can be exported across the globe, initially to Japan and the US. However, such opportunities may not last. R&D into offshore wind technology is gathering momentum in the US, Japan, and China. According to a recent report from Accenture, Shanghai, Jiangsu, Zhejiang, Shandong, Fujian and other coastal areas have made plans for offshore wind power development.
MANY CHALLENGES REMAIN
The challenges in developing support structures for offshore turbines are many and complex. Soil mechanics, installation logistics, power engineering, aerodynamics and many other disciplines need to come together. Once again, the offshore wind sector can draw on the experiences of oil and gas operators, but foundations for wind turbines will also bring new challenges.

Schematic of Energy Technologies Institute’s tension leg floating platform currently undergoing front end engineering design studies. It has the potential to achieve £85/MWh or lower © ETI
Decades of data from the oil and gas industry bolster developers’ confidence in the use of computational modelling to drive designs to the demonstration stage. But there is little experience of the novel effects that wind turbines might have on the support structures – flaws may yet emerge. For example, serious problems arose with the recent discovery of faults in the grout connection used between the wind turbine and the monopile. The designers had underestimated the impact of lateral movement in the structures. A costly remedy was to change the cylindrical sleeve to a conical one. The upward tapering joint introduced a downward force to bring the grouted surfaces in firmer contact and prevent slippage. Subsequent monopile structures now include this design change.
FINANCIAL FUTURE
The Offshore Renewable Energy Catapult report, tinyurl.com/lxaatq2
Independent journalist Dr Trevor Loveday talked to Andrew Scott, Programme Manager Offshore Wind at the Energy Technologies Institute and Kim Ahle, Head of Offshore Technology at DONG Energy. He used material from the 2014 Rankine Lecture by Professor Guy Houlsby FREng – see tinyurl.com/oqzf8w7 Professor Byron Byrne, Associate Professor of Civil Engineering at Oxford University reviewed and revised the article.
Keep up-to-date with Ingenia for free
SubscribeOther content from Ingenia
Quick read
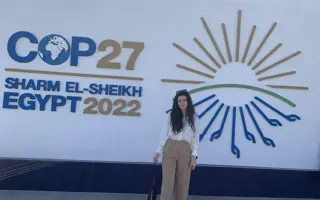
- Environment & sustainability
- Opinion
A young engineer’s perspective on the good, the bad and the ugly of COP27

- Environment & sustainability
- Issue 95
How do we pay for net zero technologies?
Quick read
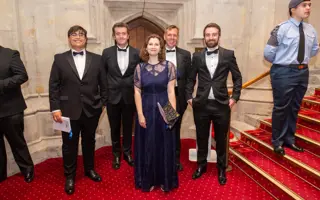
- Transport
- Mechanical
- How I got here
Electrifying trains and STEMAZING outreach
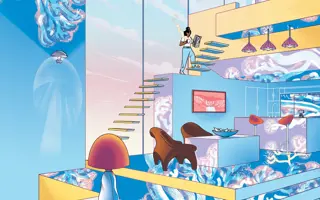
- Civil & structural
- Environment & sustainability
- Issue 95