High Speed 1
Built on time and to budget, the Channel Tunnel Rail Link Project will provide much more than faster rail connections to Europe when it opens in November 2007. The new railway line will also improve local rail services while playing a major part in the rejuvenation of Kent and the East Thames Corridor. Mike Glover FREng was instrumental in the design and management of the technical aspects of the £5.8 bn project and gives Ingenia an overview of the challenges faced and achievements accomplished.

Map of Channel Tunnel Rail Link
The Channel Tunnel Rail Link (CTRL) opens in November 2007 when the first trains arrive at the renovated and redeveloped railway station at St Pancras in London. This major rail project – now known as High Speed 1 (HS1) to commemorate the UK’s first high-speed railway – set out to be much more than a fast railway link for international trains. CTRL will increase the railway system’s capacity for commuter and freight traffic.
At the same time, the important new addition to the UK’s transport infrastructure will also support urban rejuvenation, making the link a major wealth creator for the country.
Work began on Section 1 of CTRL in 1998. Section 1 opened for commercial services on 28 September 2003, on time and within budget (‘The Need for Speed’, Ingenia 17, 2003). When Section 2 opens, it will also have created the opportunity for high-speed extensions beyond St Pancras to the north. When the first trains start to run on the complete link in November, they will halve the current journey time from the Channel Tunnel to London to 35 minutes. This will result in journey times from St Pancras to Paris of 2 hours 15 minutes and to Brussels of 1 hour 50 minutes.
These achievements underline a further, perhaps equally important, result of the CTRL. The project has demonstrated that the British construction industry can deliver a complex major infrastructure project, right into the heart of London, on time and within budget. The project achieved this while at the same time setting new standards of safety, efficiency, environmental protection and community relations.
Procurement strategy
When the procurement strategy for CTRL was established in 1996, it was against a background of lack of trust and co-operation in the construction industry in the UK, often resulting in cost and time overruns. Mindful of this legacy of mistrust, CTRL set out to devise a procurement strategy that would provide contractors with incentives to complete work ahead of time and on budget, while also encouraging competition.
To make this more likely, the strategy promoted cooperation, as opposed to confrontation, placing risks where they could be best managed, and sharing the benefits of cost-saving ideas. An important aspect of this strategy for large civil engineering was to allow contractors early involvement to contribute to the design process, and pre-plan and place early orders for the works.
For all this to happen, contracts for the works had to be clear, flexible and simple. In particular, the procurement strategy used contracts that provide incentives to the parties through its gain/pain share mechanism, whereby the contractor shared in the savings or excesses of the cost of the works compared to an agreed target cost.
Working partners
London and Continental Railways (LCR) won the concession to design, construct, operate and finance the project in February 1996. Rail Link Engineering (RLE), a consortium of Arup, Bechtel, Halcrow & Systra, became project manager, responsible for design, project management, procurement, construction and commissioning of the CTRL under an agreement with LCR, administered by Union Railways, a subsidiary of LCR.
The management of any major project has to adapt as circumstances change. As the work on CTRL progressed, the strategy developed to suit the nature of the activity. For example, for the tunnelling under London, the four contractors involved formed an alliance to increase collaboration on technical and resourcing aspects. Where the works were particularly complex with multiple trades and interfaces, with building works for example, RLE acted as construction manager and let individual trade contracts on fixed scope and price.
A long journey
The concept of a rail link from the Channel to London has a long history of failed starts.
The commitment to build the Channel Tunnel introduced an important ingredient, ‘political will,’ into the venture. Even so, British Rail’s initial proposals in the late 1980s and early 1990s did not go down well in the affected communities.
There were sceptics even within the transport community, with challenges on the feasibility of a link that was purely a high-speed international railway. It was only when Arup proposed realigning the route, and setting wider objectives of regeneration and improved local rail transport, that the project gained both public and political support.
Urban rejuvenation became the third key objective for CTRL. The new rail link will achieve this by providing the transport spine for the development of the East Thames Corridor. The new link will stimulate rejuvenation of derelict areas, at Ebbsfleet and the inner city sites around Stratford and King’s Cross. The new and expanded transport facilities and development at St Pancras, Stratford and Ebbsfleet were also a key feature in London’s successful bid for the Olympics in 2012. The CTRL’s success is important in encouraging greater political will for future grand infrastructure projects.
Engineering design
There are many notable elements within the design of the CTRL. For example, the design teams had to find a route that satisfied the tight constraints associated with a high-speed railway, whilst at the same time complying with the numerous undertakings given to protect the environment and amenity and to meet political demands, as with the routing of the railway through the centre of Ashford. This resulted in some heroic engineering, and imaginative three-dimensional solutions.
There is a marked difference in the nature of the engineering works for Section 1 and Section 2. Section 1 is essentially across open countryside with substantial earthworks and numerous bridge crossings, although it does include the North Downs Tunnel and the massive cut and cover tunnelling works required to bring the CTRL through the centre of Ashford. Section 2 runs through a predominantly urban environment and involves long, large diameter bored tunnels for most of its length and station construction.
Much of the work involved innovations in engineering, particularly in the construction of bridges, and of the concrete sprayed North Downs Tunnel, the Earth Pressure Balanced Tunnel Boring Machines (EPBTBM) for the tunnels in Section 2, and the active minimisation of waste, in materials and resources. As if these challenges were not enough, most of the work for Section 1 took place during some of the worst weather conditions ever recorded for Kent!
Melding old and new
As well as creating the UK’s most modern railway line, the project also had to respect one of the rail network’s older buildings. The huge challenge at St Pancras was to create a design which was acceptable to all stakeholders and then to restore and extend the existing, rundown, 150 year-old Grade 1 listed station, from six short operational platforms into a major new international gateway to Europe with 13 platforms and a new underground station for Thameslink.
The station had to operate throughout construction: delivering the restored and extended station as a world class public building must rank as the high point of the project’s technical and design achievements.
Mixed traffic
The CTRL is double-track with a line speed of 300 km/h, reducing to 230 km/h in tunnels in Section 2. Unlike the French TGV network, the line can handle not only high speed TGV passenger trains but also high speed commuter operations, and freight trains.
The need to operate mixed traffic has a marked impact on the infrastructure. The route has to accommodate freight loops, high-speed curves that are subject to maximum levels of cant deficiency, and neutral sections to deal with a range of train lengths. The signalling also has to accommodate the different speed requirements and braking characteristics.
The need for three intermediate stations – at Stratford, Ebbsfleet and Ashford – also had significant implications for the design of CTRL. The stations added greatly to the complexity of the rail infrastructure. For example, they increased the number of turnouts required and the complexity of the signalling control. To satisfy security considerations and the gauge of the trains, each station had to accommodate international TGV and commuter trains on different platforms, with separate access loops off the main line to the platforms for TGV and commuter trains.
The safety of staff and public was the top priority, with constant attention to safety and training through our Target Zero campaign. Many parts of the works were hazardous undertakings – underground, in close proximity to electrified operating railways, roads and busy operating stations. The project’s accident frequency rate was 2.5 times better than the industry average. This substantially reduced the risk of delay and disruption due to unsafe or environmentally damaging working.
Environment and community
From the start, the project’s managers realised that they had to forge good relationships with the community, third party stakeholders and planning authorities. The project’s achievements on this front are all the greater when viewed against the backcloth of the scale of the works and its potential for disruption to the communities involved. As well as providing a 21st century railway line, the long term legacy of the CTRL will be in the regeneration of the derelict lands around the new stations.
As with CTRL’s engineering management, the project’s quality and environment management systems set out to achieve their objectives through self-certification and a programme of measurable continuous improvement. A number of initiatives improved communication and information management. These included setting up at the outset of the project a pan-project electronic data management system and purpose-written software for managing the project data and records.
Attention to environmental matters was a high priority in the development of the design and execution of the works. An example of this was the route itself. Over 60% of its length, the completed railway follows existing transportation corridors, specifically the M20 and M2 Motorways in Section 1. A quarter of the route also runs in tunnels, dominated by the deep bored tunnels in Section 2 under the Thames and then under London, running from Dagenham in the east to St Pancras/King’s Cross in the west.
Earth moving
A further environmental requirement was to reduce visual intrusion. This resulted in the deliberately low vertical alignment of the track through Section 1. One consequence of this need to keep the track low generated a disproportionately high quantity of earthworks and requirements for drainage. For example, more than 15 million cubic metres of material has been excavated, but the work used only 2 million cubic metres of this as structural fill in the works.
The project used this excess of excavated material to good effect, largely in earthworks to mitigate the environmental effects of CTRL and in widening the M2. At Stratford, material excavated from the London Tunnels provided a clean and raised site around the new station, on lands that were once contaminated and subject to flooding. This now forms the site for the £4 bn, 25 ha Stratford City and Olympic Village developments. At King’s Cross/St Pancras the original railway land behind the stations has been cleared and decontaminated, with the remaining tenants accommodated in new facilities. This has created 25 ha for the £3bn development of King’s Cross Central. A £3bn development is planned at Ebbsfleet, supported by the new station and highway infrastructure.
Mitigating the environmental effects of CTRL also required extensive landscaping, planting and land drainage. For example, 1.2 million trees have been planted, 30km of noise barriers erected and over 250ha landscaped. Archaeological and ecological investigations, together with the provision of barriers, sympathetic landscaping and resilient track forms to mitigate noise and vibration, demonstrated the care with which the project responded to environmental concerns.
Construction challenges
Apart from the development of St Pancras station, which has always dominated the programme, the critical path of the project ran through those parts of the civil infrastructure with the greatest impact on the logistics of installing the railway infrastructure which is linear from the construction railhead. For example, in Section 1 this was the Medway Bridge and the North Downs Tunnel.
For the same reason, the Thames Tunnel was the greatest challenge for Section 2. The railhead had been sited to the south of the Thames for clear logistics reasons. To mitigate the risk, Rail Link Engineering planned the activity in these areas in minute detail and procured the works early. As a result, the contractors completed the work in these areas ahead of programme and under budget, demonstrating the importance of risk analysis and planning in large infrastructure.
Engineering highlights
The success of the project owes much to the contractors. They delivered some amazing feats of construction within very tight time and physical constraints. There were many achievements, but among those that deserve special mention were the complex ‘cut and cover’ works through Ashford, and the 34 km of 8.1-metre bored (7.1 metres finished) diameter tunnelling under London.
Other notable activities within the CTRL included the bridge slides in the Ebbsfleet area, a 9,000 tonne bridge was constructed to the side of the live railway and then slid into position whilst demolishing the existing tracks during a three-day closure of the section. Then there was the ‘push launch’ of the 1km long Thurrock Viaduct which threads its way under the QEII Bridge and over the exit from the Dartford Tunnel. Finally there was the construction sequencing for St Pancras, putting in place a schedule that ensured that everything happened in time and in the right order so that the work could meet a very tight timetable whilst enabling the station to remain fully operational.
Many people contributed to the success of CTRL, whether they were the planners, designers and constructors who delivered it, or the neighbours whose forbearance helped them. The success of CTRL provides a new confidence in the construction industry’s ability to deliver large, difficult and complex projects on time, within budget and to specification for the benefit of the nation. CTRL will bring benefits for many generations to come, just as we have benefited from the Victorian engineers who gave us St Pancras and other important parts of our often overlooked infrastructure.
Building bridges – Push-Launch Techniques

Picture of the Channel Tunnel Rail Link design
Essential to good bridge design is consideration of site safety. Prefabrication and avoiding working at heights are fundamental to safe construction. As a result, launching techniques have been widely developed. In this case the bridge is constructed progressively at a prefabrication area behind one of the abutments. Thurrock Viaduct, which crosses over the Dartford Tunnel northern approach viaducts and under the QEII bridge, was built using the push-launch method. This pre-stressed concrete bridge used a lightweight steel launch nose at its head to limit the bending moments, shears and deflections during construction on the permanent bridge section. As the bridge is projected forward over the supports, the stress regime at the top and bottom of the bridge reverses from compression to tension and vice versa. Concrete is very strong in compression but not in tension and, as a result, pre-stressing techniques have been developed to neutralise the tension fields whereby the concrete is pre-compressed to give the full concrete section compressive strength. The concept is as follows:
During launching
Provide constant pre-stress to cater for selfweight moments during launching. This is provided using internal bonded pre-stress cable within the top and bottom slab.
After launching
Provide additional continuity pre-stress to cater for the additional moments from trains, ballast and other superimposed loads. This is provided using pre-stress located within the box of the superstructure and held in place at the top at pier diaphragms and at the bottom at intermediate deviators to balance the applied loads.
Construction sequence
The bridge is built on the launching bay at the abutment. Launching is carried out a span at a time using large pushing jacks which grip onto skidding beams underneath the casting area. For Thurrock Viaduct the span was cast in four segments with the more complicated pier segment being built first. The launch cycle was approximately two weeks per span. The internal cables were two spans in length and overlapping by one span. This means that half of the launching pre-stress would be applied at each span at a time. These cables overlapped at pier segments and the back segment of each launch was a pier segment.
Cut and Cover Tunnels
The CTRL (High Speed 1) passes through Ashford in Kent in cut and cover tunnels. The tunnels are located beneath a light industrial area and railway lands and close to housing through the centre of Ashford. The tunnels, together with approach ramps within retained cuts, are about 1.7km long. The western tunnel is about 25m wide and is designed to accommodate four
tracks which comprise up and down through lines and to each side the connections to Ashford International Station. The through two track tunnel is about 14m wide and takes the up and down lines towards the Channel Tunnel. The maximum depth of the cut and cover tunnels is about 20m below ground level.
The cut and cover tunnels comprise 10 separate underground box structures which were designed to take account of the varying ground conditions, final layout and the most appropriate method of construction. The ground conditions in the area of the tunnels comprise Fill and Alluvium overlying Hythe Beds, Atherfield Clay and Weald Clay. The groundwater level is about 1-2m below ground level.
The cut and cover box structures and retained cuts were constructed using both top-down and bottom-up methods with a combination of temporary steel props, ground anchors and shallow and deep dewatering techniques. The structures consisted of embedded contiguous bored pile walls with reinforced concrete base and roof slabs and prop beams. Construction of the tunnels adopted the principles of the Observational Method – using defined trigger levels to control wall and ground movements as well as measurement of temporary and permanent prop loads during excavation. This enabled the construction to be completed successfully within the planned programme and generated savings in construction costs by reducing the number of levels of temporary propping.
Permanent gravity relief wells have been installed beneath the tunnel base slab to control and reduce the long term groundwater pressures. This enabled the capital cost of the box structures to be reduced with the owner and the maintainer of the tunnels inspecting and maintaining these wells during the lifetime of the structure.
Vital Statistics
-
150 bridges of various construction forms including viaduct structures of 1.5km at Medway, Thurrock and Ashford – the central span of the Medway Viaduct is probably the longest span, high-speed rail bridge in the world (see ‘The Need for Speed’ Ingenia 17).
-
7km of piled raft across the Rainham Marshes.
-
25km of twin single-track bored tunnels and approach structures, including the Thames crossing at Ebbsfleet and the tunnels from Dagenham to King’s Cross in London, the longest single drive being 7.5km from Stratford to King’s Cross.
-
3km of double track, sprayed concrete tunnel through the North Downs.
-
3km of cut and cover tunnelling including St Pancras Thameslink Station and Ashford.
-
1km-long Stratford Station Box, involving 1 million cubic metres of excavation.
Finding a lining
The alignment and size of the running tunnel was heavily influenced by the characteristics of the high speed railway. A 7.15m internal diameter was required to allow for the aerodynamic effects of trains operating at 230km/h, and to limit the air pressure changes to maintain passenger comfort. Other constraints included the space requirements needed for mechanical equipment, kinematic envelope (the extremes that a train will move during its path) of the train sets, pressure relief, emergency ventilation and tunnel emergency and maintenance walkways which also provided derailment containment.
The running tunnel linings were 350mm-thick, bolted precast concrete segmental rings, with an EPDM gasket (the black rubber linings in the photo above). Segments were bolted together using spear bolts (the holes in the segments above). Supported by an extensive loading and fire testing programme, the decision was taken to reinforce the segments with Steel Fibre Reinforced Concrete (SFRC) and monofilament polypropylene fibres, rather than traditional reinforcement cages. This was to increase durability and, more particularly, to increase fire survivability through, building on experience from the Channel Tunnel fire.
Each running tunnel ring comprised seven ordinary segments, two top segments and a key to limit the arc length of each segment and associated bending stresses to within the capacity of SFRC. All 25,000 precast concrete segments were cast on site at two temporary manufacturing facilities at Ripple Lane and Stratford. At these locations, a fully automated four-carousel system with a computer controlled batching facility was established to manufactured segments for the four tunnel drives serviced from Stratford.
Biography: Mike Glover FREng
Mike Glover is a Fellow of The Royal Academy of Engineering, an Arup Fellow, a Director of Arup and Technical Director of Rail Link Engineering. His early career focused on leading the engineering design of a number of signature buildings including Foster's Hong Kong Shanghai Bank, followed by the design and execution of projects in the oil and gas industry from which he developed whole-project management skills. He subsequently became Technical Director and Deputy Project Director for the £5.8bn high speed Channel Tunnel Rail Link (CTRL), a position he has held throughout its design, construction, commissioning and handover.
Keep up-to-date with Ingenia for free
SubscribeOther content from Ingenia
Quick read
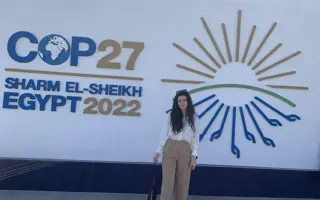
- Environment & sustainability
- Opinion
A young engineer’s perspective on the good, the bad and the ugly of COP27

- Environment & sustainability
- Issue 95
How do we pay for net zero technologies?
Quick read
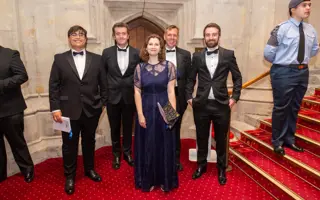
- Transport
- Mechanical
- How I got here
Electrifying trains and STEMAZING outreach
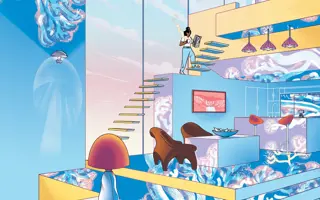
- Civil & structural
- Environment & sustainability
- Issue 95