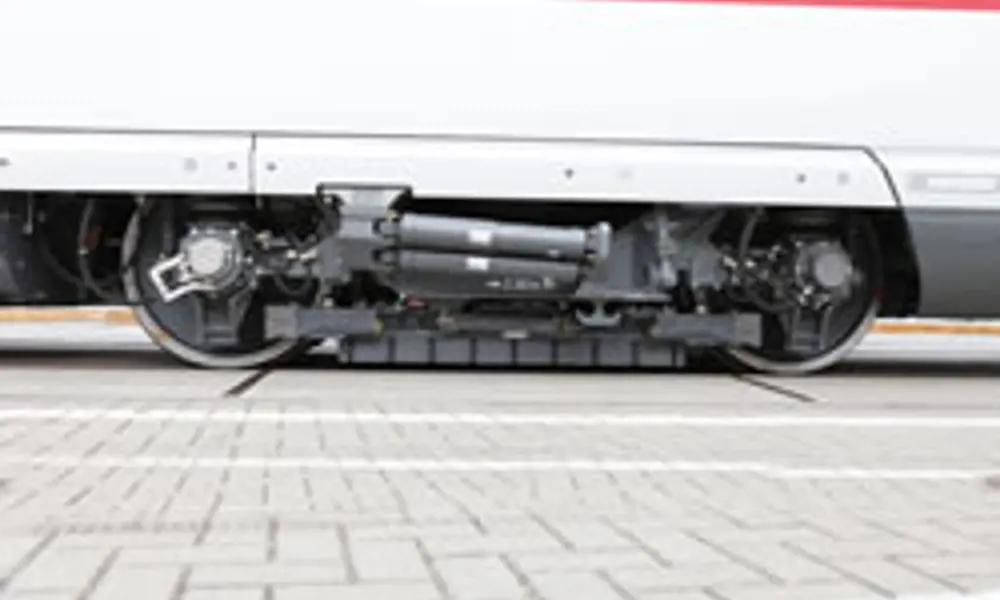
HOW DOES THAT WORK? - Clean rooms
A modular clean room © Starrco
Increasing miniaturisation and purity requirements in manufacturing demand that work environments are as free from dust, bacteria, hair and other contaminants as possible. The particle-control environments known as ‘clean rooms’ are associated with a range of high-specification manufacture including pharmaceutical products and silicon chips.
In the US, clean rooms were introduced in 1960 by Willis Whitfield, at Sandia National Laboratories. Air is passed through high-efficiency particle arresters, an industrial scale of the type of filters found in modern vacuum cleaners. This removes particulates to well-defined industrial standards, and the air is sometimes also treated with ultraviolet light to kill residual microbes, before being injected at ceiling level into the clean room.
In high-end ‘laminar flow’ clean rooms, the air streams down to the floor where it is carried away through holes. This allows any particulates that are introduced by users and equipment to be removed. Additional levels of protection are afforded by multi-step gowning procedures for workers, tacky mats to remove particles from shoes, entry through air locks and ‘air showers’ to throw off particles on clothing. The design of the rooms has also evolved, with modular, ‘soft wall’ clean room surfaces, which can be set up and dismantled quickly to create temporary particle-free environments within larger structures.
Future designs could include monitoring systems that speed up or slow down fans when particulate levels change in order to conserve energy without compromising cleanliness.
Keep up-to-date with Ingenia for free
SubscribeOther content from Ingenia
Quick read
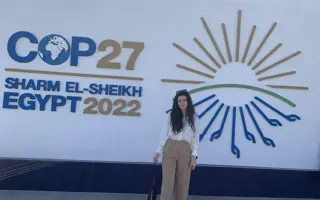
- Environment & sustainability
- Opinion
A young engineer’s perspective on the good, the bad and the ugly of COP27

- Environment & sustainability
- Issue 95
How do we pay for net zero technologies?
Quick read
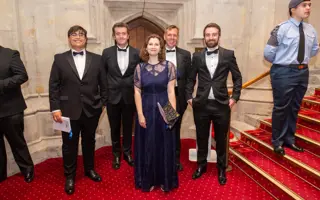
- Transport
- Mechanical
- How I got here
Electrifying trains and STEMAZING outreach
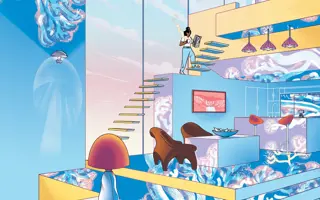
- Civil & structural
- Environment & sustainability
- Issue 95