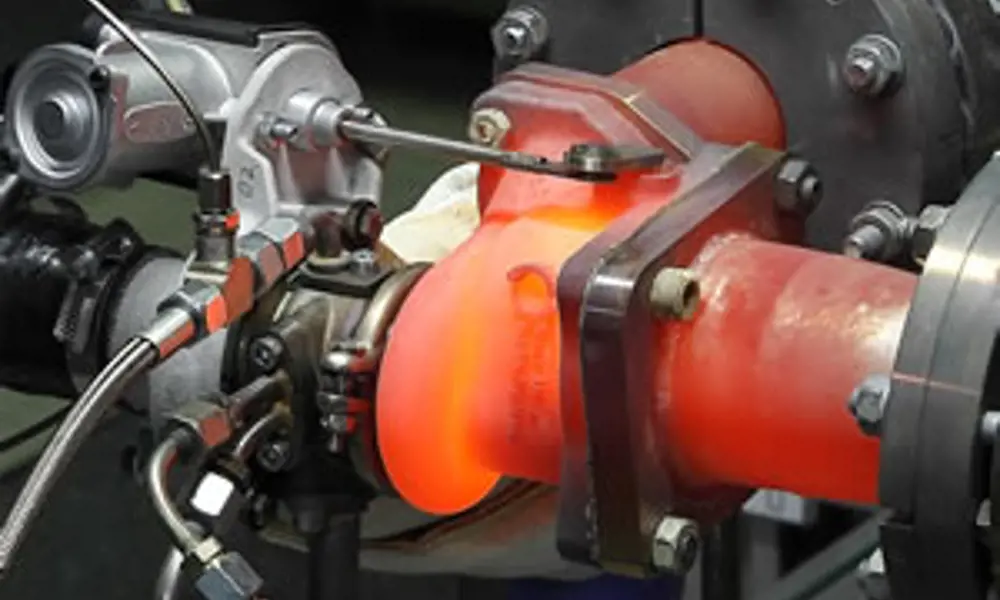
How low can we go?
Small gasoline engine with electrical waste gate actuator being tested on hot gas test bench © MAHLE
Downsizing the internal combustion engine
In the race to cut carbon dioxide emissions and boost fuel efficiency, there is broad consensus among vehicle manufacturers that downsizing the internal combustion engine should be a part of the process. Dr Martin Knopf, managing director of Bosch Mahle Turbo Systems, explains how the exhaust gas turbo charger is the enabler for downsizing concepts.
The last year has seen a flurry of petrol-powered medium-sized vehicles downsizing from their usual six cylinders to just four. Earlier this year, Korean car manufacturer Hyundai released a revamped Sonata with four cylinders. Germany-based Audi soon followed with a four-cylinder powered A4 and Volvo, of Sweden, now plans to downsize all its engines to four cylinders and 2.0 litres by 2014. Indeed, there are plans to downsize to three cylinders and eventually, two. Why? Engine downsizing is the most effective measure to cut fuel consumption and carbon dioxide emissions.
Downsizing is a simple concept; replace a larger engine with a smaller version, with a lower displacement. The downsized engines of tomorrow will have fewer, smaller cylinders, so the volume swept by pistons as they pump up and down inside is reduced. This will reduce friction, thermal losses and the mass moved, boosting fuel economy and cutting carbon dioxide emissions.
Diesel engines have already undergone aggressive downsizing – up to 40% – over the last decade and more stringent emissions legislations see this trend moving over to petrol engines.
Consumers want to drive more fuel-efficient vehicles, but not at the expense of engine performance. Innovations from components suppliers have been crucial in ensuring that power is not lost in the process.

Figure 1. Turbocharger cutaway labels the main assemblies within the turbocharger © Bosch Mahle Turbo Systems
Avoiding power losses
Despite having a lower displacement, the performance of a downsized engine can be maintained by injecting more air into its combustion chamber to burn additional fuel. This is made possible by turbocharging, which provides the engine with the mass of air needed to ensure highly efficient and clean combustion.
In 2008, Bosch teamed up with Germany-based Mahle to form Bosch Mahle Turbo Systems to develop modern turbocharging systems for new petrol and diesel engines in passenger cars and commercial vehicles. Progress since then has been rapid.
A turbocharger developed by the joint venture has recently been fitted into Mahle’s three-cylinder petrol engine. The engine can produce 160 horsepower and 286 Nm from a displacement of only 1.2 litres, matching the performance of a conventional engine twice its size. The team has also installed this downsized engine to a series production Volkswagen Passat with excellent results. Fuel economy is exceptional at 49 mpg and the vehicle can accelerate from 80 to 120 km/h in nine seconds. Bosch Mahle Turbo Systems expects to produce more than one million performance-optimised turbochargers by 2015.
Turbocharging explained
In both petrol and diesel vehicles, the turbocharger comprises two assemblies: a centrifugal compressor powered by a turbine that is driven by the engine’s exhaust gases (see Figures 1 and 2). Hot exhaust gases flow through the turbine’s wheel blades, accelerating the turbine and driving the compressor.
These turbines are made from high-temperature resistant nickel alloys, and can withstand temperatures in excess of 1000°C and accelerate to speeds upwards of 280,000 revolutions per minute.
The compressor itself comprises an impeller and a diffuser, housed in the compressor casing. The precision-milled aluminium alloy impeller draws in air, accelerating it to a high velocity before forcing it towards the diffuser. The diffuser slows the fast-moving air, raising the pressure and temperature in the compressor housing, and compressing the air before it is directed to the engine. In this way, more air can be injected into the combustion chamber, ready to burn the additional fuel needed to maintain engine power.
To prevent the turbocharger from overcharging at high engine speeds – and also to maintain torque at lower engine speeds – the flow of exhaust gases through the turbine and compressor is carefully controlled. In a petrol engine, at high engine speeds, a waste gate is opened to divert part of the exhaust gas flow away from the turbine. This decreases pressure in the compressor housing and prevents overcharging (see Breaking the knock limit).
Meanwhile at low engine speeds, the waste-gate will close so that the entire exhaust flow can drive the turbine and the compressor. These turbochargers are also designed to provide ‘over-boost,’ a temporary, excessive increase in pressure for when, say, the driver is accelerating.
The mechanism to control gas flow to the diesel engine is different. Developers have introduced ‘variable turbine geometry’ to the diesel turbo-charger in which a set of adjustable vanes in the exhaust housing control gas flow across the turbine.
At low engine speeds, turbine speed is maintained or increased by minimising the cross-section of the vanes’ inlet. This ensures the exhaust gas flows quickly through the inlet, hitting the turbine blades at high speed and raising the rotational speed. Meanwhile at higher engine speeds, inlet cross-section increases so the exhaust gases hit the interior of the turbine blades at a lower speed, reducing rotational speed. Controlling the velocity of exhaust gases in this way gives a high turbine efficiency.
More room for diesel
But following a decade of downsizing, can diesel engines be designed to even lower displacements? Developers believe so and are looking to improve the common-rail fuel injection system to boost engine performance even further.
Fuel injection is the system used to mix fuel with air in a diesel internal combustion engine. In common rail fuel injection systems, all injectors are supplied fuel by the common fuel rail, in which fuel is stored at high pressure (see Figure 3). Raising this pressure improves control of fuel injection, so fuel can be injected into the engine with greater accuracy and frequency, increasing power.
Injection systems have developed at breathtaking speeds over the last decade with higher fuel pressures and faster, more accurate dosing of fuel helping manufacturers to meet tougher emissions standards. Many of today’s common rail diesel systems have fuel pressures up to 1,800 bar, but there are plans to start series production of the first 2,200 bar common rail system for passenger cars by the end of 2011. In fact, engineers are already working on a 2,500 bar system to help boost engine power further.
And so-called ‘two-stage turbocharging’ could also be used in downsized diesel engines to maintain performance and solve the well-known problem of ‘turbo-lag’. When accelerating in a vehicle from low speed, a single turbocharger may not inject enough air to the engine for combustion, and the car ‘hesitates’. A two-stage system overcomes this problem.
Here a smaller high-pressure turbocharger, used to rapidly raise pressure levels and pressure build-up in the compressor casing, is connected to a larger low-pressure charger. The first charger is activated at low engine speeds and supplemented by the second at medium speeds. At high speeds, control software switches off the smaller charger leaving only the larger turbocharger operating. This approach delivers high torque at all speeds; there is no turbo-lag and the diesel engine performs more powerfully.

Direct injection in the diesel engine – extreme downsizing makes even lower fuel consumption and carbon dioxide emissions possible. Bosch sees potential for a further 30% reduction
On the road ahead
Thanks to the ongoing developments in turbocharging technology, the internal combustion engine will retain its dominant position over alternatives, such as all-electric and hybrid drives, with the proportion of turbocharged engines found in passenger cars set to rise steadily. Thanks to extreme downsizing, the petrol and diesel engines of the future could have just two cylinders and a displacement of lower than a litre.
Emissions targets are also fuelling research into alternative carbon-cutting technologies. Engineers are currently exploring combustion control using combustion chamber pressure sensors as well as looking to recover energy from exhaust heat to increase automotive efficiencies further. These technologies will contribute significantly to more economical driving and ensure car manufacturers will meet the stringent emissions targets of tomorrow.
Keep up-to-date with Ingenia for free
SubscribeOther content from Ingenia
Quick read
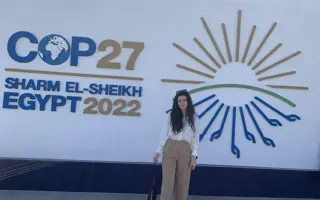
- Environment & sustainability
- Opinion
A young engineer’s perspective on the good, the bad and the ugly of COP27

- Environment & sustainability
- Issue 95
How do we pay for net zero technologies?
Quick read
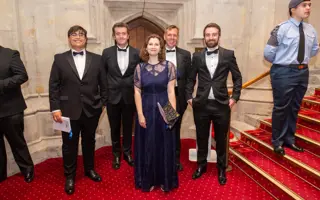
- Transport
- Mechanical
- How I got here
Electrifying trains and STEMAZING outreach
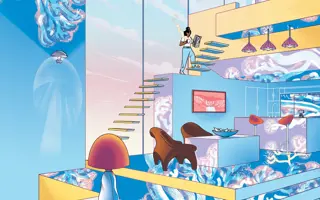
- Civil & structural
- Environment & sustainability
- Issue 95