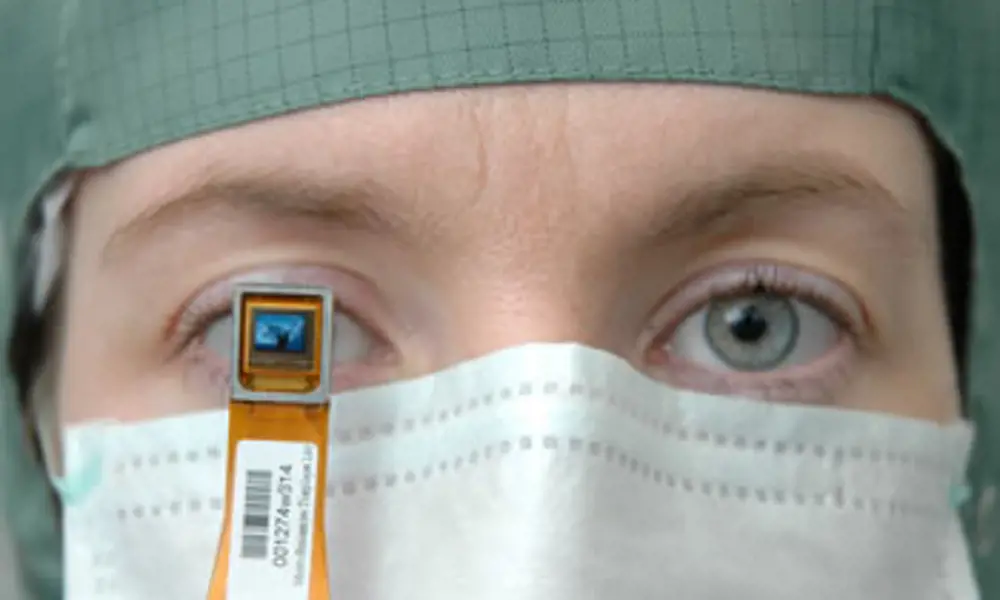
Innovation Watch: shock absorbing material
The d3o™ material is made of molecules that can flow and move past each other under normal circumstances but immediately lock together when undergoing rapid stress, such as a sudden impact © d3o labs
A UK company has developed a protective material that stiffens on impact, providing more mobility and greater protection to the user. Designed to be easily developed into a wide range of products, it is now finding application across the sporting world, consumer electronics, and in the military.
People whose professions or pastimes require body padding, or even full body armour, are potentially at the mercy of a dangerous trade-off: make the protection lighter and less bulky and it won’t be as effective at protecting the wearer, but make it thicker and the wearer will be carrying more weight and won’t be as mobile.
Brighton-based d3o lab looks to have overcome this dilemma with its intelligent shock-absorbing material, d3o™. The material is light and malleable like putty until struck with force, when it stiffens to absorb the energy of the impact before softening again, all in less than 1,000th of a second. Known as a ‘strain rate sensitive polymer’, it will react differently to impacts depending on the speed and length of the event – the degree of stiffening will vary with the amount of energy it receives.
The molecules of the polymer under normal circumstances are able to flow and move against each other but in a rapid event they lock together, creating a transient hard surface that spreads the impact over a larger area, thereby dissipating the energy – a property called ‘strain rate sensitivity’. The action of the molecules locking together, and the ability of the material to mould closely around the wearer’s body and then stiffen, makes it far more effective than conventional padding.
In its base state it is a liquid, which makes it easy to manufacture into a wide variety of products. Made into foam, it can be used in protective sportswear for all parts of the body and in a variety of sports (it is already becoming established in skiing, polo, and motor-racing) and in protective coverings for high-value items like iPods and iPhones.
The Ministry of Defence recently announced funding for d3o lab to design and produce linings for soldiers’ helmets. By using the polymer in military headgear, it is hoped that the number of head injuries suffered by combatants will be significantly reduced. The absorbent material can diminish the amount of energy transferred through the helmet to the head of the wearer by ballistic impacts from bullets and explosives.
Another possible development avenue is in soundproofing – soundwaves should have a similar effect as a physical impact, resulting in a material that becomes more soundproof as noise increases.
The shock-absorbing material was originally developed by snowboarding CEO Richard Palmer following research into the properties of sheer-thickening fluids. Possessing both an engineering and creative-design background, he founded the Brighton company in 2001 and immediately set his team to work on discovering applications for the technology.
“The uses of the polymer are basically endless,” claims Richard Palmer. “It was deliberately designed to make it easily developed into any kind of application. The fact that it is easily shaped and a liquid in its base form makes it very flexible from a manufacturing point of view.”
For more information visit: www.d3o.com
Keep up-to-date with Ingenia for free
SubscribeOther content from Ingenia
Quick read
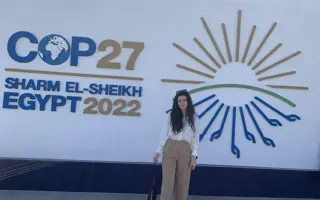
- Environment & sustainability
- Opinion
A young engineer’s perspective on the good, the bad and the ugly of COP27

- Environment & sustainability
- Issue 95
How do we pay for net zero technologies?
Quick read
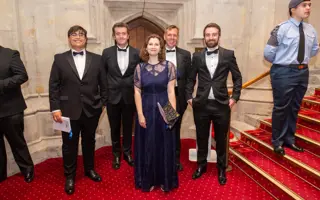
- Transport
- Mechanical
- How I got here
Electrifying trains and STEMAZING outreach
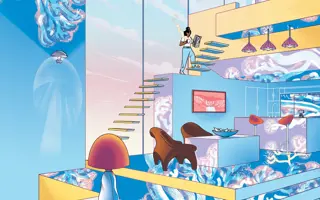
- Civil & structural
- Environment & sustainability
- Issue 95