Judith Hackitt CBE FREng - Culture of Safety
With the launch of the Health and Safety at Work Act and just after a major chemical disaster, Judith Hackitt entered chemical engineering at a time when safety was making headlines. She explains to Michael Kenward how safety has been a constant theme in a career that has taken her from running large processing plants to chairing the UK’s Health and Safety Executive.
Judith Hackitt’s career as a chemical engineer began with a sharp reminder of the importance of safety in the industry. While taking her exams at Imperial College London in 1974, a chemical plant at Flixborough in Lincolnshire suffered a catastrophic explosion. The accident killed 28 people, seriously injured 36 and badly damaged buildings up to a mile from the plant.
“That incident on a Saturday afternoon in June is still a vivid memory to me,” Hackitt says. Before then, she had never stopped to think what potential damage her chosen industry could cause. “It was really quite a salutary lesson, not just for me, but probably for everyone who was studying to be a chemical engineer at that time.”

Hackitt already knew that safety was important. Her chemical engineering degree course had included lectures from, among others, Sir Frederick Warner and Professor Douglas Napier, leading lights in risk and safety. Another key event was the Health and Safety at Work Act which finally became law in July of that year.
“So, just at a point when I was at university, not only did Flixborough happen, but the regulation that the Health and Safety Executive now lives and breathes was first implemented.” These days, Hackitt chairs the Health and Safety Executive (HSE), the body that, among other things, tries to ensure that there can be no repeats of this disaster.
Despite the coincidental timing of the Flixborough explosion, there were mutterings about the possible deleterious effects that health and safety legislation and regulation might have on companies. Indeed, Hackitt encountered them at home. Her father was a mechanical engineer. “I can remember having a conversation with him about the restrictions it was going to place on work practices.” These days, as the HSE celebrates its 40th anniversary, she spends some of her time trying to counter baseless tales of how safety legislation disrupts everyday activities.
TEACHING AMBITIONS
While many of her fellow graduates sought jobs with engineering consultancies, Hackitt, one of just four female chemical engineers in her year, wanted to get into manufacturing. However, her original career ambition was to be a science teacher rather than a chemical engineer. Wasn’t an engineering degree an odd choice for that? Why not a straightforward science degree? “I was absolutely clear in my own mind that to be any good as a science teacher I needed to be able to explain why you needed to learn things, and how they were applied in practice.”

Judith Hackitt CBE FREng
Thanks to her father’s experience as an engineer, she explains, she understood the difference between pure science and using science to provide solutions and benefits. “So I cooked up this plan for myself which said go to university, study engineering, get some industrial experience for a couple of years and then become a teacher.”
Studying for an engineering degree meant rejecting the advice of one of her teachers. “When my senior mistress at school said, ‘You can’t do engineering, Judith, because girls don’t do engineering,’ I said, ‘I think I can.’ And I did!”
When it came to finding a suitable job that applied her interest in science, Hackitt applied to and received job offers from most of the well-known names in chemical engineering. She eventually opted to work at Esso’s Fawley plant. “I liked the place, I liked the people, I liked the culture. I thought, I can fit in here.”
Safety was an important part of that culture. At Fawley, she explains, safety was at the top of the list of priorities and was nonnegotiable: “You will do this, you will be assessed on how well you handle safety in everything you do.” With Flixborough still a vivid memory, “I understood entirely why.”
Hackitt dropped her teaching ambitions, stayed in the industry and soon started to ascend the career ladder. She started as a process engineer, working first on butadiene production. Within three years, Hackitt had her first management position as supervisor for a butadiene production unit. Over the next 15 years, she moved into technical management, supervising and managing teams of engineers. She worked in various businesses before moving into butyl polymers for the last seven years of her time with Esso.
Hackitt then faced difficult a choice. She was married with two daughters, aged 18 months and four years. “The next career move for me, had I stayed with Exxon (Esso’s parent company), would have involved a lot of foreign travel. I am not criticising it in any way, because if you opt for that sort of career path you go wherever you need to go to do the job. That didn’t feel to me like what I wanted to do.”
Instead, Hackitt moved to become operations director at a much smaller chemicals company. “It was an inorganic water-based pigments business, as opposed to a major-hazard hydrocarbons company,” she explains, so safety issues shouldn’t have been as all-pervasive as they were at Exxon. Instead, she experienced something of a culture shock. “The safety record of this business was appalling. They had had 25 losttime accidents in the year before I started work for them, in a workforce of 230 people, lots of bad backs, slips and trips and people getting cuts to their hands and so on.” Such accidents were all but unknown at Exxon.
While sorting out the new employer’s safety culture, Hackitt also faced business challenges. The plant supplied commodity products and faced intense competition from China. “In terms of long-term competitiveness, it was on the road to nowhere.” So she had to fix the business and drive up quality, while at the same time changing the safety culture.
Hackitt’s success in sorting out the plant, and in transforming its safety record in particular, led to promotion to group risk manager. The company, Harrison and Crosfield, now known as Elementis, had plants all around the world in different sectors. “My role was to bring that health and safety culture to all the businesses.” For the first time, Hackitt’s career took on safety and risk as its main focus.
After eight years with Elementis, Hackitt next took on influential roles in the wider world of chemical engineering and safety in particular. She first moved to the Chemical Industries Association as Director of Business and Environment and, in 2002, became the organisation’s Director General. In the same year, she became a Commissioner on the Health and Safety Commission, the body responsible for the Health and Safety at Work Act. The Commission’s role was to monitor the operation of the act and to manage research, training and communication on health and safety.
MEDIA MYTHS
In 2006, Hackitt became Implementation Director, Chemistry for Europe with the European Chemical Industries Council and was awarded a CBE for services to health and safety. While fighting the corner for Europe’s chemicals sector, she became increasingly worried about attitudes to health and safety back at home. “What concerned me, when I was working in Brussels, was watching health and safety in the UK getting a bad name.” A lot of the press were, as she puts it, taking a pop at health and safety and complaining that it was stopping people from living their lives.
She thought that the Commission and the Health and Safety Executive (HSE), which enforced health and safety law, weren’t doing enough to raise awareness of the importance of their work. “I didn’t see the HSE fighting back in the way that I thought that it ought to, and defending what is and remains a world-class health and safety system.”
Determined to do something about it, Hackitt threw her hat into the ring when the Commission advertised for a new chair in 2007. She got the job and became Chair of the HSE when the two organisations merged. One of her priorities, she says, was to defend health and safety and the organisation from attacks from the SELLING SAFETY ADVICE
This appreciation of the UK’s approach can deliver benefits on several fronts. A recent review of the HSE’s work has encouraged the HSE to market its knowledge and services. “The next big step for us is to think about how we continue to be a first-class regulator here at home in the UK but at the same time share that knowledge on a more commercial basis with other places in the world.”
It isn’t just the HSE that could benefit if other countries adopt the UK’s approach to health and safety. “It is also a huge aid to business,” says Hackitt. “If the regulatory culture in other parts of the world is modelled on ours, then UK businesses know how to operate in that environment. Big construction firms, big oil and gas companies should be very supportive of us sharing our knowledge and our approach with other governments. Many tell us that they would like to see regulatory regimes as robust as ours in other parts of the world.”
What is it that makes the UK’s approach to health and safety special? “It is about responsible behaviour. All that the regulation does is to set basic standards. It does rest upon the notion that the risks will be managed by the individual who creates the risks, not by the regulator policing everything that the risk creator does.”
The suggestion that ‘self-regulation’ makes it easier for companies to police themselves and get away with sloppy practices annoys Hackitt. She says: “Selfregulation is a term that is abused and misunderstood.” Think of it in terms of driving, she explains. Yes, you have to pass a driving test, submit your car to an MOT, obey the speed limits and follow the highway code, but, “when we drive, we still have to exercise judgement that says it is foggy today or it is rainy today therefore I am not going to drive at 70mph. I know I could, but I need to self-regulate my behaviour to suit the conditions.”
Other countries have a very different approach to safety. In the US, for example, “the system is prescriptive, rules-based, and industry is very much driven by being able to tick the boxes to demonstrate that it is complying with the rules that have been set by the regulator. So it places the responsibility and onus in a very different place, and in a very different mindset.”
The UK’s approach to health and safety comes into its own when it has to accommodate new technologies. “Because it is non-specific and principles-based, our approach is adaptable to new technologies.” Take shale gas, which is a combination of tried and tested drilling techniques being put to a different use. “It is very similar to things that we have been managing and regulating in the North Sea and elsewhere for years.”
The HSE’s approach is to look at new technologies, such as shale gas and carbon capture and storage, for special or unusual risks that that would need new regulation. “Our approach is only to introduce new regulation if we can identify a real issue that cannot be covered by what we already have.”
FOCUSING ATTENTION
If anything, the HSE wants to slim down the rulebooks. “We have been trying very hard over the last couple of years to simplify the regulation. Part of it is adapting as technologies move on. Part of it is removing duplication.” Sometimes, regulations really aren’t needed any more. “Cinematographic film for example, why do you need specific rules and regulations applying to that today?” Then there is duplication that has come about for local reasons or when the UK has implemented EU decisions and has put new regulations in place that say the same thing.
Another motive for simplifying is to assist small companies. “A substantial part of what we have been doing is in recognition of the fact that there are now many more small and medium-sized enterprises out there. We are trying to rewrite regulation in a way that is much more accessible and simpler to understand for those small businesses. It is not about changing the standards but, because it is non-prescriptive regulation, it needs to be presented in a way that enables people to feel confident that they have done enough.”
Hackitt has been taking the message out to the wider engineering community. As outgoing president of the Institution of Chemical Engineers (IChemE), she has a receptive audience. “The synergy between my roles at HSE and IChemE is the message about safety being an integral part of every engineer’s role.”
Even so, Hackitt has used her role at the ICHemE to warn offshore oil and gas and other major hazards industries that young engineers need to learn about key safety issues. After all, few start their careers in the aftermath of a major disaster on their doorstep. As she said to younger engineers, “My generation has a responsibility to ensure that you too learn the lessons from our experiences. It is the only way to break this troubling pattern of tragic events which continue to occur in major hazards facilities around the globe.”

Judith Hackitt played an important part in the whynotchemeng Flash Bang campaign to promote more exciting science experiments in schools. She showed, in an experiment for school children, that under very particular circumstances a fire could be lit and held in the hands © Institution of Chemical Engineers
PROMOTING ENGINEERING
Engineering is also at the heart of what the HSE does. “We are a big employer of engineers, not least in the Health and Safety Laboratory in Buxton where we have got 350 people, lots of them with PhDs. In this organisation, we must have well in excess of 500 or 600 scientists and engineers.” HSE’s work ranges from shaping and reviewing regulations to producing research and statistics and enforcing the law.
Hackitt’s interests and influence are wideranging. “I have been on the board of the Energy Saving Trust for the last five years. I recently joined the supervisory board of the High-Value Manufacturing Catapult (– see Catapults in Ingenia 58). Both of those reflect my personal interests, my passion for sustainability, and in terms of the Catapult my passion for UK business and UK industry and wanting to see manufacturing really emerge in a new way in a new era.”
This leads to a major Hackitt concern, the importance of being able to communicate about engineering. “If there is one thing that I hope that I bring to the party, it is being able to explain to non-engineers – whether it is in terms of safety or energy or whatever it is that I’m involved in – what we do and what we are about. We are not good at telling our story to people outside the profession, and explaining what we do and what value we bring to the world. We often fail to get our value across. Ultimately, for me it is also the key that unlocks getting more people to want to become engineers, which is part of solving a supply problem.”
Engineers need to learn how to communicate and to realise that, as Hackitt puts it, engineer-speak is strictly for other engineers. “Until we learn some communication skills, we are better off continuing to talk to ourselves. But we do desperately need to learn those skills so that we can communicate with others.”
BIOGRAPHY
Michael Kenward OBE has been a freelance writer since 1990 and is a member of the CAREER TIMELINE AND DISTINCTIONS
Born, 1954. BSc Chemical Engineering, Imperial College London, 1974. Exxon Chemical Ltd (formerly Esso), 1975-1990. Operations Director, Harcros Pigments Europe, 1990-1996. Group Risk Manager, Elementis plc, 1996-1998. Director of Business and Environment, Chemical Industries Association, 1998-2002. Health and Safety Commissioner, 2002-2006. Director General, Chemical Industries Association, 2002-2006. Implementation Director Chemistry for Europe, Cefic, 2006-2007. Awarded CBE for services to Health and Safety, 2006. Chair, Health and Safety Executive, 2007-present. Elected member of Council of Institution of Chemical Engineers, 2008. Independent Board member of Energy Saving Trust, 2009. Elected Fellow of the Royal Academy of Engineering, 2010. Elected President of The Institution of Chemical Engineers (IChemE), 2013.Non-Executive Director, High Value Manufacturing Catapult, 2014.
Keep up-to-date with Ingenia for free
SubscribeOther content from Ingenia
Quick read
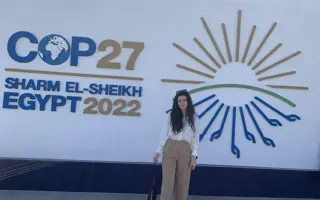
- Environment & sustainability
- Opinion
A young engineer’s perspective on the good, the bad and the ugly of COP27

- Environment & sustainability
- Issue 95
How do we pay for net zero technologies?
Quick read
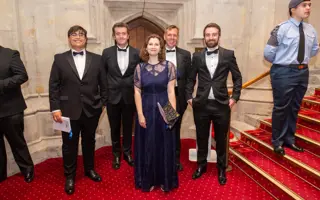
- Transport
- Mechanical
- How I got here
Electrifying trains and STEMAZING outreach
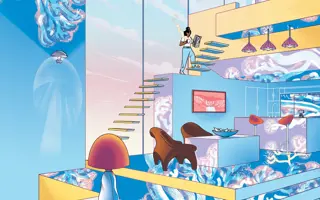
- Civil & structural
- Environment & sustainability
- Issue 95