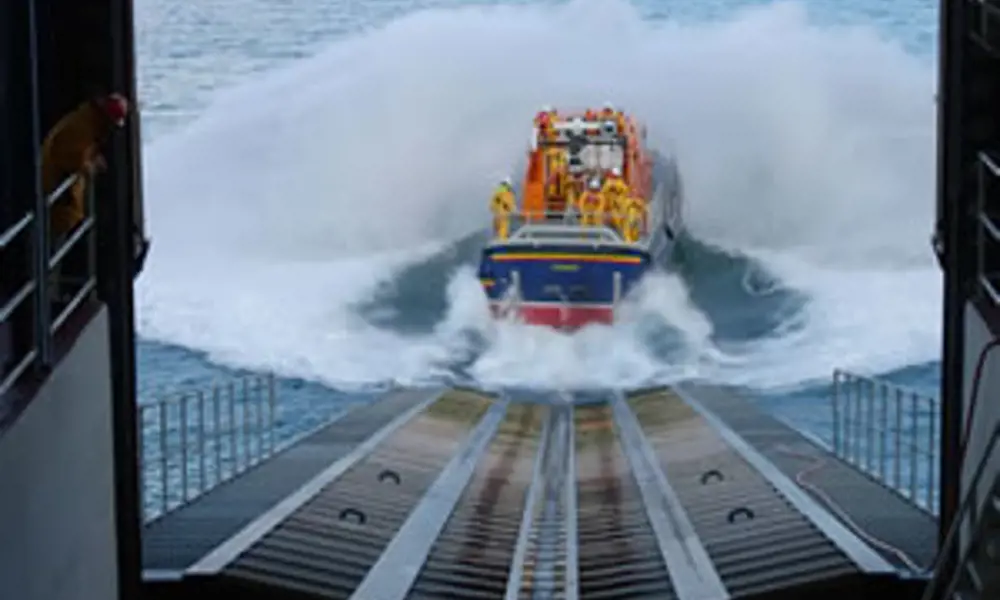
Launching the Tamar
Launching a Tamar-class lifeboat off the Tenby RNLI slipway © Eleanor Driscoll
The Tamar-class lifeboat is entering service around the UK as the most technologically advanced vessel of the Royal National Lifeboat Institution’s (RNLI) fleet. Many of the innovations in the design for this new boat arise from the need to protect its crew and augment their abilities. Two key RNLI employees write about the development of the impact seats and a complex onboard computer system. Neil Chaplin is the RNLI’s Principal Naval Architect and John Nurser is its Principal Electronics Design Engineer.
Few working environments anywhere become as stressful to the human mind and body as the wheelhouse of a lifeboat on a tricky mission off the coastline of the British Isles. Most of us can only imagine the experience of crewing a 16m boat as it forges through furious seas provoked by storm Force 11 winds in the blackest night, 100km from land, aiming for the unpredictable target of a vessel in distress – and then striving to rescue any survivors and casualties.
Over recent years the mission parameters of lifeboats have become more and more extreme. Boats have become faster (from 8 knot to 25 knot) their range has become wider (from 50km to 160km) and on-board electronic navigation and communications equipment has burgeoned from the radios and direction finders of 50 years ago to the Global Positioning System of today.
Boats have inevitably become more cluttered with new systems vying for space within the wheelhouse, sometimes restricting the field of view from windows and often crowding the nominated seat of a specialist crew member. These dedicated positions also mean that crew members need to physically change seats to undertake different roles – a hazardous requirement in a brutally pitching and rolling vessel sustaining hammer-blow punishment from heavy seas. Clearly, the entire ‘human-machine interface’ needed a sea-change of its own.
Sowing the seeds
This is why the late 1990s saw the start of development of the new Tamar-class slipway-launched boat to serve the Royal National Lifeboat Institution. The Tamar-class (named after the River Tamar flowing between Devon and Cornwall) supercedes the Tyne-class slipway-launched boat. This completely new vessel gave RNLI engineers a golden opportunity to begin with a clean sheet.
As engineers, it was critical for us first to focus on the fact that nearly 90% of our 4,000-plus men and women lifeboat crew members around the coast of Britain and Ireland are volunteers with no professional maritime experience. If this new class of lifeboat is to achieve mission success, we need to ensure the advanced technology on board is safe, effective and intuitive for these ‘ordinary people’ to use. In practice, we need effectively to bring the boat and its controls to the crew member for the first time by applying ergonomics – the science concerned with the ‘fit’ between people and their work.
Working alongside consultant specialists in ergonomics, we began by examining the safety hazards crews face from within the vessel, both moving around to achieve their tasks and while they are seated. As the speed of new lifeboats increases, it is vital that crew seating develops accordingly to protect the crew from the worst effects of extreme boat motions.
Prioritising crew members
We looked in particular at the crew seat. The seat in service on existing classes of 25 knot all-weather lifeboats is a variant of a unit designed for use in quarry vehicles. Comfort is good in slight to moderate sea states but the seat has a tendency to ‘bottom-out’ in heavy seas. Crews members are adept at raising themselves out of their seats to isolate themselves from a heavy shock load, but only when they can see a severe impact is imminent in large seas. If they cannot see the impact coming – at night, for example – crew members may be subjected to severe loading, transmitted directly into the lower spine.
Our research into the effects of vertical vibration and shock on the human body found that spinal injury, in particular lumbar spinal injury, is the biggest concern. Detailed computer models of boat and wave motion and the motion of the human lumbar spine were built to compare the amount and types of injury sustained on different seat designs, suspension settings and sea states.
This modelling showed the cumulative damage of the spine is dominated by high peaks rather than prolonged exposure to low-level accelerations – and the most critical motion for a seated person is the vertical direction, along the axis of the spine. So our key achievement in reducing the risk of injury has been to reduce the highest vertical acceleration peaks rather than eliminate low-magnitude movement, while retaining the good comfort of the current seat in calmer conditions.
Absorbing the shock
We found that a suspension spring with a progressive characteristic is vital to ensure a rapid increase in stiffness as the seat approaches the end of its stroke during a ‘slam event’ to lessen the chance of the seat bottoming-out. During simulated slams we found relative levels of spinal damage for the current seat is about l0 times more than for the new seat model.
We switched from a pedestal to a multi-point mounting, to carry the required loads more efficiently. The seat runs on two parallel bars with a single progressive spring-damper unit mounted centrally.
The seat can move up and down 200mm to combat shock loads and, crucially, the design includes armrest controls to overcome the problems of relative motion with console-mounted systems.
Computer controls
This new seat is just one element of the ergonomic design of the Tamar boats, which involved the use of a full-scale wheelhouse mock-up. We also addressed control-console design and boat systems management as two other key ways of bringing the boat to the crew member.
Since the inception of this project, we recognised that the development of a common, effective and a user-friendly interface would be fundamental to the success of SIMS, the new Systems and Information Management System. An early review of systems used in the RNLI’s current fleet and other similar vessels failed to reveal a suitable human-machine interface we could adapt. So we opted for a bespoke system, not least because RNLI has a relatively large fleet that would benefit from standardisation.
We began with the aim of achieving five crucial benefits for crew members: better situational awareness, shared task-loading between crew, improved safety through remote monitoring and control of systems, greater redundancy and simplified training through a common user interface. In place of a complex collection of stand-alone systems, the wheelhouse would gain a single system that is simple to use, clear in the way it presents information, robust and reliable and able to exploit redundancy in the event of failure.
Peer review
We created a Tamar project user group, comprising RNLI coxswains and mechanics from stations nominated to receive the new boats. Working alongside software specialists from Servowatch Systems Limited we also evolved a distributed network-based arrangement of components and data input/output devices designed to help manage, operate, control and log mission data.
The six workstations on each Tamar lifeboat include a single rugged processor connected to a high-resolution LCD screen and a seat-mounted control interface, a trackball, greatly reducing the need for crew to move around the boat at sea. SIMS also provides remote monitoring of many systems including main machinery, fire-fighting equipment, internal and external CCTV and hatches.
SIMS is designed to allow only one user to control any one system at any particular time – although all users can view all systems at any time. SIMS’ user interface is simple: a screen with fixed buttons on the side, armrest-mounted trackball and headset. No keyboards are featured (they are bulky, difficult to use in heavy weather and liable to inadvertent access) so all screen interaction is via the trackball pod. The screen uses colours extensively – yellow for live controls, cyan for signal faults and red for alarm conditions. Because lifeboats need to get to the rescue scene quickly, a single push-button by the deckhouse door fires-up SIMS in only around two minutes.
The system is designed to ensure no single unit failure affects the rest of the system. A unit may stop working, but it will not bring down additional non-dependent functions. The system features two fully independent dual redundant networks using proven and mature technologies. If any single node or hub fails, the data integrity of the system is not affected.
Trialling experience
So how does all this extensively-researched, thoughtfully-applied effort to bring the boat to the crew actually work in practice?
Robert Aggas knows better than anyone, he is not only an active RNLI crew member (second coxswain on the Mersey-class slipway-launched boat at Swanage, Dorset) but also the RNLI’s trials officer, working at the Institution’s headquarters in nearby Poole. Robert has spent many hundreds of hours manning Tamar boats during the new vessel’s trials and has gained a unique insight into the ‘people-centred’ systems on board.
“Remember that Tamar is still just a lifeboat, in spite of all its on-board equipment capability,” he points out. “Even if all the systems went down the crew would still take their boat to sea when it gets the call. The big difference SIMS makes is in crew awareness. SIMS is totally integrated and it works for everyone on board to bring everyone together, to make liaison easier, to make it safer and reduce many of the sort of difficulties and risks that can catch you out on other types of lifeboats.
“For instance, if the coxswain needs to look at the chart-plotter he doesn’t now have to move to the navigator’s position to do so, and believe me, moving around the wheelhouse in Force 11 conditions really is a hazardous thing to do. All he does is bring the chart-plotter up on his screen and he’s instantly in the picture, he gets the information he needs immediately and he can make the right decision immediately.
Charting progress
“Or if the radar operator says he’s uncertain about some strange images on the radar picture other crew-members can help work things out by bringing the radar picture up on their screens.
“With the Tamar, three push-buttons and a tracker-ball can control the whole boat. And there is so much more redundancy built-in than on other vessels, which itself is a big benefit to have.
“The beauty of the system from an operational viewpoint is that it has been integrated into the Tamar design from day one. It works as one piece of equipment and we can update it simply by putting a new disc in. Our requirements in on-board systems are probably unique and quite specific to our role, so there’s no commercial equivalent that we could use anything like so effectively.
“The feedback we have had from the first Tamar crews is extremely positive. A lot of crew members were sceptical when they first heard this new boat would be full of computer equipment. But now they’re using it they are sold on it. Their workload, particularly at times of peak effort, is more manageable and productive and that is crucially important when you consider our role is to save lives.”
Prioritising the needs of Lifeboat crews
A lot of lifeboat stations have a full-time engineer and a group of dedicated volunteers, with daytime jobs, available for callouts by a pager call. It used to be that fishermen formed the body of the crew but today a crew may be formed mostly from people with no professional maritime experience.
“Enhancing mission success is the driving force behind the ergonomics-based engineering approach to the new Tamar-class boats” explains Dr Jonathan Earthy, Principal Human Factors Specialist for Lloyd’s Register, who has been paying close attention to the Tamar project as a demonstrator for marine ergonomics. Dr Earthy co-ordinates all technical aspects of Lloyd’s Register’s treatment of the human element and its involvement on this issue with national and international maritime agencies.
“The volunteer crews on whom RNLI – and mariners in distress – rely have limited training time and no special physical abilities. They are deployed at immediate notice up to 160km from shore in any weather. This necessitated a boat design process centred on the belief that looking after the crew allows them to look after the casualties.
“In lifeboat design the mission comes first. The mission dictates the shape and form of the platform. With the Tamar boat, RNLI engineers and Servowatch Systems specialists embraced the twin imperatives of mission success and crew safety with superb design. They have faced a known problem and have solved it with inspired engineering skills. They have facilitated much more integrated crew work through an exemplary application of ergonomics.
“All stages of the project involved RNLI staff and crews together with human sciences experts. Now Tamar boats are being deployed and crews are feeding back information to ensure SIMS, in particular, continues to be refined through experience at sea on board this most innovative vessel.”
Tamar at sea
Today SIMS is operational in the first eight Tamar-class boats (six on station at Tenby, Peterhead, Padstow, Longhope, Cromer and Barrow, with two boats in reserve). Orders for a further 10 boats are confirmed and the fleet size could ultimately reach 30, with a planned service lifetime of a least 25 years.
Away from the often dramatic front line of service, SIMS delivers another crucial benefit. As SIMS carefully presents only necessary data, it ensures the RNLI can maximise valuable crew training resources – a vital advantage both for RNLI and for the ‘ordinary’, dedicated and brave people who go to sea to save life.
The authors would like to stress that the Tamar project would not have been possible without public support. The RNLI receives no government funding and is entirely dependent on voluntary donations to pay its £130 million a year costs. If you would like to know more about the work of the RNLI or to make a dontaion, go to http://www.rnli.org.uk/
The robust structure is manufactured from advanced composites. Sandwich hulls (made in two halves) feature layers of PVC foam between pre-impregnated epoxy glass fibre shells. When bonded together, a separate single moulding of deck and wheelhouse is then stuck onto the hull after stiffeners and bulkheads are installed. Structural weight represents 30% of load displacement.
The thick (100mm) foam core in the topsides provides secondary buoyancy in the event of damage, and whilst wary of the term ‘unsinkable’, Neil Chaplin says the Tamar has excellent damage tolerance, remaining a safe haven in all but the most extreme circumstances.
Biography: Neil Chaplin and John Nurser
Neil Chaplin is Principal Naval Architect in the RNLI engineering office, where he has worked for 10 years. He was Project Manager for the Tamar-class lifeboat. The integration of SIMS into the Tamar has required in-depth involvement throughout the project, including extensive sea trials. He was previously Naval Architect with the Ministry of Defence Procurement Executive.
John Nurser has been at the RNLI for 10 years and is now Principal Electronics Design Engineer in the engineering office. In addition to the design and development of SIMS and other new electronics equipment, he is responsible for the through-life support for legacy systems. He previously served in the Royal Navy for 35 years as a weapons engineering officer, service in both sea and shore appointments until his retirement in 1997.
The authors would like to thank John Hutchinson, a freelance writer, with the construction of this article.
Further reference
Keep up-to-date with Ingenia for free
SubscribeOther content from Ingenia
Quick read
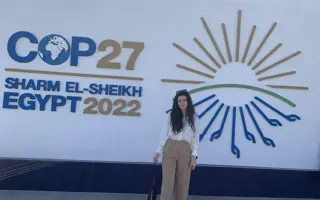
- Environment & sustainability
- Opinion
A young engineer’s perspective on the good, the bad and the ugly of COP27

- Environment & sustainability
- Issue 95
How do we pay for net zero technologies?
Quick read
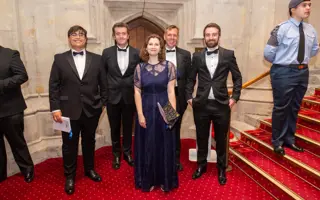
- Transport
- Mechanical
- How I got here
Electrifying trains and STEMAZING outreach
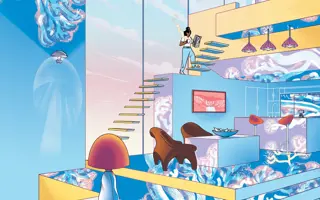
- Civil & structural
- Environment & sustainability
- Issue 95