Range Rover...with a twist
Land Rover has taken a concept car from prototype to manufacture and created a new vehicle category with the Range Rover Evoque. Within its first year of manufacture, it has sold over 80,000 vehicles and won over 120 awards. The vehicle’s technical design team won their first engineering prize in June 2012 when they picked up the Royal Academy of Engineering MacRobert Award for innovation. Here the Evoque team tell Ingenia about some of the car’s novel space-saving and energy-saving features

The LRX concept car (left) was first shown to the public at the Detroit Motor Show in 2008. Three years later the production model Evoque reached the sales rooms with little apparent change in design
When Land Rover’s LRX concept car was unveiled at the 2008 Detroit Auto Show, the enthusiastic reception inspired the company to put the bold design into production virtually unchanged. It has now been on sale for nearly a year as the hugely successful Range Rover Evoque.
There were some major engineering and design challenges to overcome while maintaining the LRX’s contemporary styling and Land Rover’s reputation for go-anywhere capability. In achieving this, the company has created an entirely new market segment: the premium off-road coupé.
Concept cars are often likened to the outlandish clothes paraded at fashion shows: there to attract attention. Even if they make it to the production stage, they rarely do so without significant alterations.
The creation of a new car is always a compromise. Designers want their vision to be translated into production unsullied, but engineers have to reconcile this with a host of conflicting demands, balancing performance versus fuel efficiency, practicality against size, and safety and feature content against weight.
Manufacturers also have to keep a careful eye on development and production costs. Jaguar Land Rover is a global business comprising two distinct brands, Jaguar and Land Rover. Land Rover has had to ensure that the car is easy to assemble with the Evoque spending no more than 70seconds at any work station during the build process. Then there are reams of documents that need to be prepared relating to construction and use regulations. These must be prepared before production and can vary from country to country.
It was obvious that some adjustments had to be made to the concept car, in particular to increase the headroom for passengers in the rear. By slightly raising the bonnet line and the rear section of the roof, the Jaguar Land Rover engineers were able to overcome these obstacles while ensuring that the Evoque retained virtually all of the original car’s appearance.
STARTING POINT
The development of an all-new car from scratch requires a huge amount of capital – in most cases, hundreds of millions of pounds. So for economies of scale, manufacturers endeavor to use stock components wherever possible.
Land Rover already had a compact four-wheel-drive vehicle that it could use as a starting point: the Freelander. Although the Freelander is a more rugged and traditional-looking off-roader than the Evoque, it was about the right size and contained many of the ingredients needed to create the Evoque.
However, the further into the development process the engineers went, the more they found themselves modifying, honing or replacing the parts they thought they could take from the Freelander to meet their objectives. In the end, more than 70% of the Evoque differs from the Freelander.
In many ways, this is because the Evoque was always meant to herald a new direction for Land Rover – more sustainable and less rooted in functionalism. The Evoque would be a showcase for new materials and assembly techniques, technically advanced, while retaining the off-road capability for which the company’s products have always been renowned.
In the end, the forward-looking Evoque has more in common with the generation of Land Rovers to come, rather than with the Freelander on which it is loosely based. It was this wholesale jump in thinking that attracted the MacRobert judges, who awarded the Evoque engineers the 2012 gold medal and £50,000 prize for engineering innovation.

An exploded view of the different car elements and how they fit together. The aluminium roof of the Evoque is bonded to a steel body shell. Using aluminium saves 7 kg in weight compared to a traditional steel roof. The two metals are held together with adhesive, and self-piercing rivets are applied every 10 cm along the roof joints
LIGHTER AND MORE EFFICIENT
In keeping with its remit as a car for the modern age – one developed around the themes of efficiency and sustainability – the Evoque is the smallest, lightest and most aerodynamic car ever to wear the Land Rover badge. At less than 4.4 metres long, it is shorter than the majority of family hatchbacks, while the average weight of the range is below 1.8 tonnes. Contrast that with the five-metre length and 2.6 tonnes in weight of a traditional Range Rover.
To achieve this while maintaining the structural stiffness necessary for good crash safety and vehicle dynamics, the engineers decided that the bare shell of the Evoque – what they refer to as the ‘body in white’ – would need to be made of a mixture of materials.
About 18% of the body is made up of high-strength and ultra-high-strength steels, including 5% boron steel for parts of the roof support structure. Boron steel has the advantage of being both light and strong, allowing the roof supports to be slim enough not to impede visibility.
The roof itself and the bonnet are made of aluminium, while the front cross-car beam, which adds lateral rigidity, is made of even lighter magnesium. The Evoque’s tailgate is a glass fibre-filled plastic composite which is as rigid as steel but almost 10 kg lighter. The front and rear bumpers are also made of plastic.
To avoid corrosion where different metals meet, joining techniques developed by Jaguar Land Rover engineers for the Jaguar car are used. The different thermal expansion rates of the various metals also had to be taken into consideration, as temperatures in the paint shop reach 200°C.
Overall, the body in white is around 70 kg lighter than one made entirely of steel. Another 12 kg has been saved by extensive use of aluminium in the suspension components. The lighter body has allowed the use of a smaller and more efficient engine with no loss of performance, so that the fuel tank can be reduced with no reduction in its range. In turn, all of this brings further weight savings and even lower fuel consumption and emissions – a virtuous circle.

The Evoque prototype being tested at the Land Rover test facility on the Eastnor Estate, Herefordshire. Although designed for city use, this compact SUV retains the brand’s cross-country abilities. Here it is being measured for its entry and exiting capabilities in deep mud and clay © Jaguar Land Rover
SMALLER ENGINES
Early in the Evoque’s development, it was decided that it would be powered solely by compact, fuel-efficient, small-capacity four-cylinder engines – despite clamour from US dealers for the 3.2-litre six-cylinder petrol engine from the Freelander.
Perhaps an even bigger step-change, with an eye on emissions legislation and taxation in many European markets, is the production of a two-wheel-drive model – a first for Range Rover. Two-wheel-drive trims about 75 kg from the Evoque’s weight, bringing down fuel consumption and emissions still further.
For the European market, some Evoques will have the 2.2-litre turbodiesel engine, borrowed from the Freelander but extensively modified. Diesel engines deliver significantly better fuel economy and lower carbon dioxide emissions than petrol engines, so in countries with emissions-based taxation regimes they will have a head start.
The diesel is available with either 150 hp or 190 hp, while a recalibrated, high-economy version of the lower horsepower engine powers the two-wheel-drive Evoque. This helps to bring CO2emissions down to 129 g/km, by far the lowest figure for any model in Land Rover’s 64-year history and a significant milestone for Jaguar Land Rover’s work towards achieving greater sustainability.
The Evoque’s petrol engine is a 2.0 litre unit, which has a turbocharger to boost performance to 240 hp; this means it is more powerful than the six-cylinder engine – and is also 20% more fuel-efficient.
There are other fuel-saving measures that include the vehicle’s electronic power steering, which delivers assistance only when the car is turning. Unlike conventional hydraulic power assistance driven by the engine, it is not constantly sapping power. The Evoque’s intuitive power system management and smart regenerative charging recover energy during vehicle deceleration, delivering a further 1.5% improvement in fuel economy. The car also has a highly efficient air conditioning system. Even the tyre compounds are designed to minimise rolling resistance to save fuel.
RANGE ROVER…WITH A TWIST
One thing that was not even on the agenda for discussion during the development of the Evoque was that it had to preserve Land Rover’s legendary off-road capability. It has the high ground clearance necessary for off-road use – more than a Freelander. At the same time, it had to have the poise and handling to match its coupé-like appearance. This was one of the bigger engineering challenges.
Off-road vehicles need to be supple, with lots of suspension travel, to soak up ruts and bumps. Crisp responses on ordinary roads, however, demand more reactive suspension. The company has solved the conundrum with Terrain Response® and MagneRide™, electronic systems that control almost every aspect of how the car drives.
Terrain Response is a rotary switch located in the centre console which offers various operating modes, depending on the kind of surface the car is being driven on, be it Tarmac, gravel, grass, snow, sand or mud and ruts. Depending on the setting chosen, the car decides how sharply or gently the accelerator should react, when and how quickly the electronic traction aids should intervene and what level of steering assistance is required. On cars with automatic transmission it governs the shift patterns, while on those with MagneRide it chooses the firmness or suppleness of the suspension.
MagneRide is an active suspension system. It has been used in high-performance sports cars, but never in an off-roader. Unlike Terrain Response, it requires no selection by the driver. Sensors monitor how the car is being driven and the state of the road 1,000 times per second. The car uses the information from the sensors to adjust the suspension characteristics independently at each wheel up to 50 times per second. It will make the suspension firmer when the car is being driven sportily through a series of corners, for example, or softer when it is travelling at lower speed on a poorly surfaced road.
It works through oil-containing magnetic particles within the suspension dampers – also known as shock absorbers. When a magnetic field is applied to the dampers, the particles change position, effectively changing the thickness of the oil and, therefore, how the suspension responds. The magnetic field constantly varies according to information from the sensors.
FOR THE CITY
Land Rovers are fairly common sights in towns and cities, but the Evoque is the first one designed with the city in mind. While highly capable away from public roads, it is primarily targeted at the urban lifestyle – more likely to be seen in Mayfair or Manhattan than in the mountains.
It also offers every technology from other members of the Land Rover family including a five-camera surround-vision system that is as useful when parking in a tight spot as it is while picking a course across difficult terrain. Appearing for the first time on a Land Rover is the Evoque’s optional park assist feature, which uses ultrasonic sensors to steer while the driver operates the accelerator, brake and clutch. This helps the driver to parallel park in spaces as little as 1.2 times the length of the vehicle.
Compact, stylish and agile, the Evoque has established a new segment in the market. It advances a brand which was perhaps becoming self-conscious about its image in these changing times. A lot of what it offers will benefit Land Rovers of the future. The Evoque is intended to be the start of this journey. With sales of more than 80,000 in over 170 countries in its first year of production, it seems that the new niche it has created has resonated with car buyers and is on the road to financial success.
Roger Stansfield, director of Interchange Europe, an automotive news agency, compiled this article with contributions from: David Mitchell, Chief Programme Engineer, Range Rover Evoque; Ian Hulme, Principal Engineer, Electronic Damping Systems, Land Rover; Mark White, Chief Engineer, Body Complete, Jaguar Land Rover; Sam Anker, Manager of Off-Road Capability and Brian Lidgard, Senior Manager, Glasshouse & Lids, Jaguar Land Rover.
LIFE CYCLE ASSESSMENT
During the development of the Evoque, Land Rover decided to subject it to a life cycle assessment (LCA) – in effect, an audit of its environmental impact from the start of production to the day it is scrapped. While not yet a legal requirement, the engineers wanted to see how much ‘greener’ it is owing to the lightweight materials in its body construction and the recycled matter used for some of its trim.
Around 1,000 recycled plastic bottles, weighing 16 kg, go into every Evoque – for the seat covers, centre console, wheel-arch liners, air cleaner, cooling fan, air ducting, underbody trays, parcel shelf, engine cover and speaker boxes. Recycled polyester from plastic bottles and fibres is used for the headliner and door pillar trim.
There are almost 20 kg of natural and renewable materials, such as leather, cotton, cardboard and rubber, in every car. All but 5% of the aluminium used in the roof, bonnet, suspension and dash trim is recycled metal.
While by far the largest proportion of the emissions from cars is created during usage, a significant amount (about 15%) occurs during manufacture, with another 5% at the end of the vehicle’s life. Land Rover is now making increasing use of what it calls ‘secondary materials’ – waste created during the production process which would once have been thrown away, or waste taken from cars being scrapped. In some parts of the production process, the amount of waste used to be as high as 50%.
Jaguar’s Castle Bromwich production plant and Land Rover’s Solihull facility, both in Birmingham, have now adopted this ‘closed-loop recycling’ system. And it will soon spread to Halewood on Merseyside, the home of the Evoque. Suppliers are also being encouraged to follow suit.
Initially, the LCA was intended as an academic exercise, but it has now grown to become an essential part of the development of every new Jaguar, Land Rover and Range Rover. The aluminium Jaguar XJ saloon and now the multi-material Evoque have gained LCA accreditation from the UK’s Vehicle Certification Agency.
Keep up-to-date with Ingenia for free
SubscribeOther content from Ingenia
Quick read
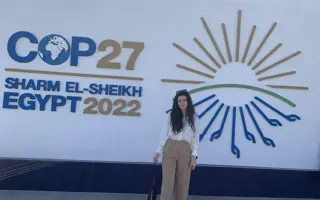
- Environment & sustainability
- Opinion
A young engineer’s perspective on the good, the bad and the ugly of COP27

- Environment & sustainability
- Issue 95
How do we pay for net zero technologies?
Quick read
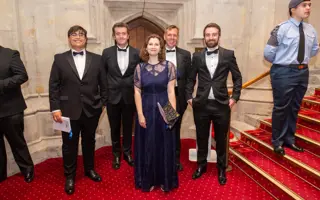
- Transport
- Mechanical
- How I got here
Electrifying trains and STEMAZING outreach
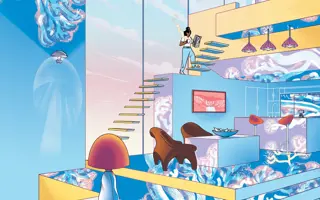
- Civil & structural
- Environment & sustainability
- Issue 95