Richard Parry-Jones CBE FREng - Not the retiring type
Career choice
Parry-Jones, brought up in Bangor, North Wales, and the descendant of a slate quarry worker, came to be in charge of product development for all of Ford vehicles, with responsibility for 30,000 engineers, scientists, designers and business professionals, thanks to an early obsession. “I became interested in cars and working parts from very early on. I think I decided to become an engineer at around 10 years of age.”
By the age of 12, Parry-Jones had picked automotive engineering as his career of choice. He wrote to Ford to ask what he should do to become a car designer and an engineer. Come back when you are 15, was the response. He did just that, with another letter. This time, he received a more considered response, along with something that convinced him that he wanted to work for Ford. Tucked in with the careers advice, he found two photos, a picture of the Lotus 49 signed by Jim Clark and one of its Cosworth engine signed by Graham Hill. That combination of car and engine had just won its inaugural Grand Prix: Parry-Jones decided then and there that this was for him and that he would not be writing to anyone else.
As well as advising Parry-Jones on which A-levels to take, Ford included a list of the six universities that it favoured. This is how he ended up at Salford University on a Ford-sponsored sandwich course combining six months at the company and six months at university. Parry-Jones left Salford with a First in mechanical engineering and joined Ford as a graduate apprentice.
Hands-on experience
The company employed student apprentices, technician apprentices and craft apprentices. “In the first six months, we all did the same work. So I learned how to operate a milling machine, a lathe, a shaping machine, a grinder and welding. This workshop experience was wonderful, truly fantastic!”
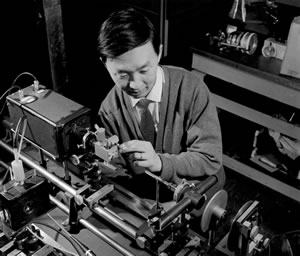
Richard Parry-Jones CBE FREng
Richard Parry-Jones remains keen on the hands-on experience that comes with an apprenticeship. “First, it gives you a real visceral understanding of the practical applications of what you are learning. The second big advantage is that, when you graduate, you are fit for work. You actually can work, instead of spending the next year learning all about the company.” Such is his belief in preparing students for work that, for many years, he was an advisory council member of Liverpool John Moores University, where he helped to develop its In at the deep end
Looking for something to move on to after completing a big design project, Parry-Jones was talking to the head of manufacturing in Europe, who asked him what he wanted to do next. “I said that I would really like to go and work in manufacturing, in process engineering for a while.” This wasn’t a bid to change careers, but a desire to get experience that would help him do a better job as a design engineer. His boss told him that if he really wanted to understand manufacturing, he needed to go and run a plant.
Parry-Jones smiles as he says: “This was said on a Friday and on the Monday morning when I went back into his office, he said, ‘Okay, pack your bags because as of tomorrow you are the general manager of the Cologne assembly plant.’ I had never run a plant in my life before and yet here I was going to be in charge of 8,500 workers, 1,320 cars a day – on top of which I didn’t speak a word of German. This was an interesting challenge with no time to get scared!”
Cologne turned out to be a good choice. It was where Ford developed processes that it then rolled out to other plants around Europe. Parry-Jones says: “It was where all the core engineering was done and it had some very experienced people there who could keep an eye on me and check that I didn’t mess things up.
“The most important thing that I learned during this time was that in manufacturing if you have got a problem you don’t write a paper about it. You go and fix it.” When a production line grinds to a halt, he adds: “You can’t ask too many people for an opinion. You get some basic information and then you had better make a decision, otherwise that line is not going to move while you’re faffing about. A stopped line costs a large company over a million pounds an hour.”
This isn’t just a manufacturing lesson, says Parry-Jones. “Product development is the same. It is just not so visible. Every day that you don’t do something upfront and prepare is a day you have lost from the launch date. And one day of slippage from the launch could cost $8 million.”
Considered testing
There are, though, some things that you shouldn’t hurry, like testing a new car. It was the racing car driver, Sir Jackie Stewart, who convinced Parry-Jones to resist the temptation to jump into a new prototype car, turn the key and put his foot down. “Jackie was tremendously helpful and influential with my approach. He’s not an engineer so he can’t fix cars, but he can extract information about a car’s behaviour in an uncannily detailed and superb way.”
Stewart said that, if you drive a car at top speed to gather information, the driver’s mind tends to get saturated with car-control issues. He suggested a calmer and more considered approach which involves sitting in the new car for 10 minutes before turning the engine on. Then, once the engine is running, to sit and listen for another five minutes. And finally, drive slowly forward. This approach gave birth to what is known in the car industry as the 50-metre test.
He says: “If you know what you are doing you can figure out between 50% and 75% of the key strengths of a car inside the first 50 metres. You need to create enough cognitive capability to be able to assimilate information about the car so that the control and handling issues are a background task rather than a foreground task.”
In his time at Ford, Parry-Jones had plenty of opportunities to run the 50-metre test. He led a development team that produced more than 70 vehicles, including many of the company’s iconic models such as the Mark 1 Ford Focus and the North American Ford Focus. Before that he had worked on the 1981 Escort and 1983 Sierra in Europe. More recently he was involved with other big production models such as the Ka, Fiesta, Puma, Mustang, Falcon, Galaxy.and many Aston Martin, Jaguar, Land Rover, Volvo and Mazda models.
He was a pioneer in introducing many safety technologies to the industry, such as electronic stability control systems and inflatable rear seat belts, and led the development of Ford’s low carbon technologies for over a decade, including technologies to remove over 500 kg from a 2.5 tonne vehicle, the introduction of small pressure-charged engines to save 25% of fuel, and electrification/hybridisation technologies including the world’s first hybrid SUV.
Dealing with difficulties
During Parry-Jones’s time at Ford he took on a variety of challenges. His most difficult time as an engineer was, he says, dealing with Firestone tyres. Tyre and tread separated on Ford Explorer SUVs that had been in service for four years or so. Sometimes, the drivers lost control, leading to some serious accidents. Ford may not have been the tyre supplier, but when a car maker has a safety problem, Parry-Jones says: “As soon as you know, the first thing you do is to go out and fix the problem. In the end, we sell the cars. We choose the tyres, we choose the tyre supplier.”
Parry-Jones entered the picture after the first tyre recall and when Ford set about replacing the defective tyres and checking to see if there were any other tyres that it should replace. It was a fraught time for him. “I was an expert witness in litigation cases,” he explains. “I was broadcasting on television about what was going on. I probably lost a half a stone over that period because it was just so intense. I learned a lot from that. Most of all I learned the power of really rigorous engineering analysis in saving lives.”
Parry-Jones reckons that he wasn’t personally responsible for any major disasters. Then again, he does not claim to have had an error-free career as a car maker. “I often joke with people that I have made so many mistakes that I cost the Ford Motor company millions of dollars in profit. People look at me horrified and ask, ‘Well how the hell did he get to be group vice president then?’ And I say that it is because I made a lot of other decisions that made the company billions of dollars.”
An engineer who never makes mistakes, he feels, is probably being too conservative. “The most important thing when you make a mistake is to figure out why and then don’t do it again. However, do a good risk assessment and don’t make any really big ones because the company can’t survive really big ones.”
Evidence-based policy
On retiring from Ford four years ago, Parry-Jones found that he had time to pay attention to political issues and to become involved in policy matters. For example, he advised the Welsh Government on economic development, transport, energy and IT infrastructure. He also worked with central government. For the Department for Business, Innovation and Skills (BIS), he chaired the new Automotive Innovation and Growth Team and then the Automotive Council.
“I use my engineering approach in policy development,” says Parry-Jones, “which is quite unusual. My observation is that most of the civil service is not populated by highly technical people.” He understands why this happens. “If you’re an engineer you want to make and design things. If you want to make things and design things, there are not many places in government where you can do that.” He would, though, like to see more active recruitment of engineers and scientists into the civil service. “That would improve the quality of some of the policy analysis and policy recommendations that are presented to ministers.”
If nothing else, having a few more people with an engineer’s way of thinking might nudge politicians in the direction of evidence-based policy making. “Policymakers have a difficult job, but one of the things that I discovered is that government is sometimes not very good at getting useful data for making decisions about their policies.”
As an engineer, he confesses that he is, “absolutely fanatical about using data to try and understand our world and solve problems.” In 2004, the Royal Society of Statistical Science made him an Honorary Fellow in recognition of his pioneering work on the use of statistical methods in automobile engineering.
He says that these skills are transferable to government activities too. With data to hand, you can build the right models and begin to forecast what might happen. Then, he explains, carry out trials or create a prototype. Then go out and build or carry out a project and measure the outcomes.
Track changes
Network Rail can expect Parry-Jones to take the same approach to his chairman’s role. It is the engineering challenge of the railways that appeals to him. There are, he believes, a lot of transformational technology opportunities in the railways. Engineering was important when the railways were built and there have been various “waves of technology” since then, such as electrification. “But I think we are in a time where another wave of technology can help the railways. Part of it is driven by opportunity and part of it is driven by need.”
Parry-Jones has also taken his hands-on approach to engineering to Network Rail. In the runup to assuming the chairman’s job in July 2012, he spent time on the tracks in Manchester Piccadilly, at a maintenance unit. “We had a wonderful time talking about the issues. The people who work on the railways are really passionate and very knowledgeable.”
For someone who, in theory at least, retired from from full-time employment five years ago, it might appear that Parry-Jones has finally managed to fail in one of his ambitions. As well as being chairman of Network Rail, he is a board member of GKN, serves on the Council of the Royal Academy of Engineering and on the panel assessing the Academy’s new scheme for Enterprise Fellowships. He is also a council member at Bangor University. Isn’t he a bit of a failure at retiring? Definitely not, he insists. “No, I’m actually a role model. I am brilliant at it.”
Parry-Jones has gone about retiring in the style of a methodical engineer. “We used to joke that I might have worked for the company for 38 years but the number of hours I put in made it 75.”
With so much happening on the UK’s railways, and the need to catch up in re-engineering the infrastructure, there is plenty of room for people who can work at double speed. “I have gone on public record as saying that I think that the railways have been chronically underinvested, for many decades. The good news is that things are starting to move in the right direction. It is not perfect, but the performance of the railways has increased enormously over the past 10 years. We are carrying nearly 1.5billion passengers a year – 50% more than 10 years ago, and twice the peak of the 1920s. Punctuality is at an all-time high, rail is the safest form of transport, and our railways here in the UK are the safest in Europe.”
However long Parry-Jones guides Network Rail, it won’t be just the engineering that keeps him going. When new opportunities arise he asks himself a couple of questions: “Are they playing to my strengths and are they things that I enjoy doing and where I can feel I am really contributing?” This is how he has ended up in “business engagements, policy engagements, that are very much anchored around my engineering background and my engineering profession”. While he clearly won’t go anywhere that doesn’t involve engineering, the first requirement for him is job satisfaction. “The most important thing is to enjoy the work and achieve something you can be proud of.”
BIOGRAPHY
Michael Kenward OBE has been a freelance writer since 1990 and is a member of the Ingenia Editorial board. He is Editor-at-Large of Science|Business.
CAREER TIMELINE AND DISTINCTIONS
Born, 1951. BSc in Mechanical Engineering, Salford University, 1973. Ford Motor Company, in roles including Group Vice-President of R&D for Ford and all subsidiary companies worldwide; Chief Technical Officer; Chairman of the Ford Global Product Committee; Chairman of the Mazda Advisory Board; and head of the World Rally Program at Ford, 1969-2007. Awarded Honorary Doctorate by Loughborough University, 1995. Elected Fellow of the Royal Academy of Engineering and the Institution of Mechanical Engineering, 1997. Awarded CBE for services to the automobile industry, 2005. Awarded Honorary Doctorate by Cranfield University, 2006. Founder and CEO of Consulting Engineering Company, 2007-present. Chairman of the Remuneration Committee and member of the Audit Committee GKN plc, 2007-present. Co-chair of UK Automotive Council (with Vince Cable), 2008-present. Member of the Governing Council, Bangor University, 2009-present. Non-executive Director, Cosworth Group Holdings Ltd, 2011-present. Appointed Senior Independent Director, GKN plc, 2012. Chairman, Network Rail, 2012.
Keep up-to-date with Ingenia for free
SubscribeOther content from Ingenia
Quick read
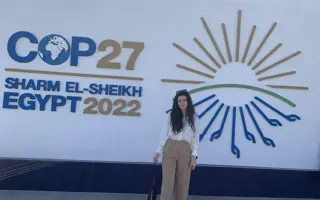
- Environment & sustainability
- Opinion
A young engineer’s perspective on the good, the bad and the ugly of COP27

- Environment & sustainability
- Issue 95
How do we pay for net zero technologies?
Quick read
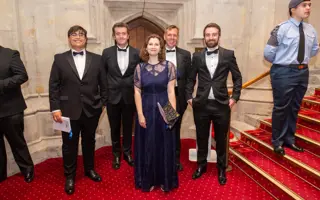
- Transport
- Mechanical
- How I got here
Electrifying trains and STEMAZING outreach
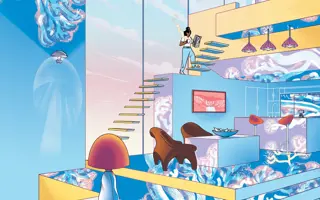
- Civil & structural
- Environment & sustainability
- Issue 95