
Slimmer solar cells
Manufacturers of concentrating photovoltaic systems, such as SolFocus, use mirrors to focus sunlight by factors of several hundred onto triple-junction solar cells © SolFocus
The most commercially available solar cells are not the most efficient or flexible. Thin-film photovoltaics are now challenging the market leader made from crystalline silicon and now account for around a sixth of the world market. Dr Richard Stevenson, editor ofCompound Semiconductormagazine, considers the efficacy of thin-film PVs and how research is seeking to improve them.
Most solar cells manufactured today are made from crystalline silicon. They have been used to convert the sun’s energy into electricity since the 1950s when they powered the first satellites. Since then, silicon cells have been used for many different applications. Smaller versions are fitted to calculators, while panels are emerging on streets to power road warning signs and parking meters. The most visible are the arrays of solar panels used to limit the carbon footprints of homes and businesses and on solar farms to generate ‘clean’ energy for national grids.
Although the commercial success of photovoltaics based on crystalline silicon has been significant, these devices have some fundamental flaws. Their manufacture takes a full day, and the devices are not particularly efficient. In the lab, the best cells convert one quarter of the energy that they receive from the sun into electricity, while the efficiency of modules shipped today is significantly lower, typically just 15%. What’s more, these silicon cells are a hundred times thicker than they need to be to absorb sunlight, so a large amount of material used in their manufacture is surplus to requirements. In addition, they cannot bend or flex, which prevents them from being wrapped or shaped around items.
Some of these weaknesses can be addressed with thin-film photovoltaics. These are made by depositing several layers of photovoltaic material on a substrate. The resultant modules can be used for building solar farms and powering homes and businesses, and can also make smaller, flexible solar sheets that can be folded into pockets and offer portable power generation for electrical gadgets. While these thin-film cells can be made with silicon, the material is no longer crystalline, and this lack of crystallinity drives down cell efficiency.
Slightly higher efficiencies are possible with cadmium telluride panels that can be produced very quickly and far higher efficiencies result from using a stack of thin films deposited on germanium or gallium arsenide substrates. It is also possible to make cells that are flexible by using semiconducting plastics or a family of alloys based on copper, indium and gallium.

Sputter deposition: an inert sputtering gas, such as argon, is led through an opening in a metal and subjected to a negative electrical potential, forming a plasma. The plasma knocks ions out of the target which are deposited on the substrate where a film develops
Thin film market leader
The device that has made by far the biggest commercial thin-film impact to date is the cadmium telluride solar cell. This started to grab a significant share of the solar market towards the end of the previous decade, when prices for silicon photovoltaics were fluctuating between about $3 and $4 per watt. Back then, the leading manufacturer of cadmium telluride photovoltaics, First Solar of Tempe, Arizona, could produce its panels for just over $1 per watt, so it could price them competitively and generate a healthy profit. Recently, however, the price of silicon panels undercuts that of cadmium telluride, following a rapid rise in the number of Chinese manufacturers of the incumbent technology.
First Solar has produced millions of panels at its manufacturing lines in the US, Germany and Malaysia. Manufacture of a cadmium telluride panel on these lines, which takes just two and a half hours, begins by feeding large glass sheets onto rollers that transport the substrates through four chambers. The first heats the glass to 600 °C, before this sheet is transferred to a second chamber filled with cadmium sulphide vapour, which has been created by heating solid cadmium sulphide to 700 °C. Some of this vapour condenses to form a thin film on the glass sheet before it enters a third chamber, where a similar process leads to the deposition of a cadmium telluride layer. Together, the cadmium telluride and cadmium sulphide layers form a p-n junction – see the panel The inner workings of a solar cell. A gust of nitrogen in the fourth chamber then cools the coated substrates to 300 °C, a step that also strengthens them so that they can withstand high winds.

London-based start up company Solar Press is working with partners to develop manufacturing equipment and processes for roll-to-roll deposition of plastic semiconducting materials on flexible substrates © Solar Press
Subsequent heating in a chloride-based environment increases the efficiency of the photovoltaics before a laser patterns the coated glass sheets to form an array of cells that are connected in series. The output of an individual cell is less than 1 V but, by stringing them together in series, it is possible to produce an output of about 70 V. The current produced by these modules can reach just over 1 A, and the power output is up to 80 W.
Although these modules take just a few hours to produce, and use far less semiconductor material than their crystalline silicon counterparts, they have two weaknesses. According to some industry insiders, there are concerns over long-term availability of tellurium and, secondly, the efficiencies of these devices are inferior to those of conventional silicon devices. First Solar holds the record for for cell efficiencies at 17.3% and module efficiencies at 14.4%. However, the efficiency of a typical module produced by the company is several percent lower, and the rate of improvement is slow.
CIS modules
Higher efficiencies are possible with other types of thin films, such as those based on alloys of copper, indium, gallium, sulphur and selenium – a family of materials that should be available for many years and is commonly referred to as CIS (copper indium selenide). In the labs, cells based on this collection of elements can produce efficiencies of just over 20%, and in production panels have hit 13.4% efficiency. The superior efficiencies compared to cadmium telluride cells and panels are thought to be a result of fewer defects and a higher degree of crystallinity in the CIS layer.
The CIS industry is smaller and vastly different from that associated with cadmium telluride photovoltaic production: instead of being dominated by one company, many rivals are competing for success with proprietary deposition technologies, bespoke production tools and different types of substrate. Not all will succeed, and some have already changed hands while others have failed spectacularly. Californian CIS manufacturer Solyndra falls into the latter category – despite receiving a government loan of $535million in spring 2009, it was unable to generate profits and in autumn 2011 filed for bankruptcy, laying off its 1,100 employees.
Most CIS modules are made by sputtering, a process involving the collision of ions onto materials to create atoms that are subsequently deposited on a substrate. Switching to a flexible substrate helps, because it opens up the possibility of the very high throughput, roll-to-roll processes that promise to slash production costs to just $0.60 per watt by 2014 – although after a decade of development, the biggest companies trying this method are only producing tens of megawatts of panels a year.
Forming photovoltaics with printing processes may be easier when CIS materials are replaced with a class of plastics known as conjugated polymers, which have a backbone of alternating single and double carbon-carbon bonds that give rise to semiconducting properties. A start up company based in London, Solar Press, is working with partners to do just this. The team is developing processes, materials and manufacturing equipment to print soluble polymers on large transparent, flexible plastics. These substrates are briefly heated to moderate temperatures, causing the solvent to rapidly evaporate and leave behind a polymer film.
Boosting efficiencies

The company First Solar manufactures its cadmium telluride modules on 1.2 m by 0.6 m glass sheets © First Solar
All the solar cells described so far have efficiencies well below 30%. At first glance, it appears that this can be addressed by building a solar cell from a material such as mercury cadmium telluride, which will absorb nearly all the light from the sun. However, although such a cell will generate lots of current, its voltage will be very small. And voltage is just as important as current, because it is the product of these two that determines the power produced by the cell.
It may seem counterintuitive, but more power is often possible by selecting a material that does not use all the sunlight and lets some infrared photons pass through the cell. But even a perfect version of this kind of device would only produce an efficiency of 33%. The key to far higher efficiencies is to stack different p-n junctions on top on one another.
Devices combining three different cells in electrical series have been built for powering satellites. They feature a bottom cell made from germanium, a middle cell of gallium arsenide and a top cell of gallium indium phosphide. This combination can deliver efficiencies above 30%, which are significantly higher than those produced by silicon cells.
These triple-junction cells are formed on substrates up to 150 mm in diameter by either molecular beam epitaxy, an evaporation technique in a very high vacuum, or a growth process known as metal-organic chemical vapour deposition. The latter process, which is more widely used for triple-junction device manufacture, involves directing gases through a nozzle to a substrate. This is heated, and when the gases hit the substrate they decompose. Elements that result include metals, arsenic and phosphorous, which all adhere to the substrates to form the likes of gallium arsenide and indium phosphide. By carefully controlling the rates that gases are injected through nozzles and the temperature profile within the growth chamber, it is possible to form crystalline alloys with very high material quality. However, it takes many hours to grow all the layers required to form a triple-junction cell, so the manufacturing costs for making these devices are very high.
On multi-billion dollar satellites, high prices are not a major impediment, and these triple junction cells are greatly valued for their high efficiency and their ability to withstand the harsh space environment. However, high costs prohibit the deployment of photovoltaic systems on earth that mimic those found on satellites. But it is possible to build photovoltaic systems with triple-junction cells that promise to offer the lowest electrical generation costs of any solar technology in sunny climes. The trick is to turn to a radically different approach, which uses lenses or mirrors to focus sunlight by a factor of several hundred onto the devices. This has the added benefit of increasing the voltage produced by the device, which in turn propels efficiencies to 40% or more.
Absorbing infrared
Reaching the very highest efficiencies requires significant modifications to the design of the photovoltaic cells. One option is to replace the traditional germanium bottom cell with one built from a dilute nitride, which is an alloy of indium gallium arsenide antimonide with a trace of nitrogen. This bottom cell is better at absorbing infrared light, because, unlike germanium, its absorption characteristics can be optimised by altering the composition of the alloy. With this approach it is possible to reach an efficiency of 43.5%.
These cells and more traditional triple-junction variants are starting to be used in photovoltaic systems in southwestern regions of the United States. Cadmium telluride modules are also starting to be deployed there, showing that thin-film solar technologies can even win sales in markets where there are no subsidies to encourage adoption of green technologies.
These thin-film photovoltaic manufacturers are competing for market share with makers of silicon modules, which are locked in fierce competition with one another and have slashed their retail prices in the last 12 months. Many of them are based in China and are receiving high levels of subsidy, according to the Coalition for American Solar Manufacturing. These tremendous falls in prices were not widely anticipated, and how long the incumbent technology will dominate the solar industry is unclear. It appears that the battle with thin-film photovoltaics will be influenced heavily by politics and manufacturing subsidies. However, the great attributes of thin films, such as low material usage, very high efficiencies and fast production times should enable them to win through in the end.
Dr Richard Stevenson, a freelance science and technology journalist, is editor ofCompound Semiconductor magazine and a Contributing Editor toIEEE Spectrum. The author would like to thank Dr Milan Rosina, an analyst at Yole Développement,
Dr Jonathan Halls, Chief Technology Officer at Solar Press, and Professor Kwang-Leong Choy, a director at IMPT, for their help in compiling this article
Keep up-to-date with Ingenia for free
SubscribeOther content from Ingenia
Quick read
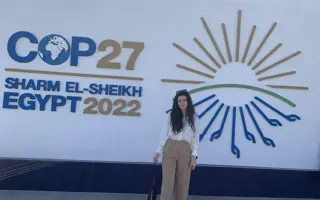
- Environment & sustainability
- Opinion
A young engineer’s perspective on the good, the bad and the ugly of COP27

- Environment & sustainability
- Issue 95
How do we pay for net zero technologies?
Quick read
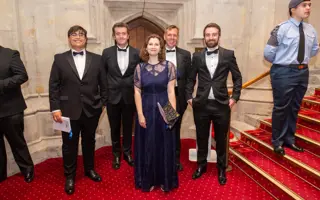
- Transport
- Mechanical
- How I got here
Electrifying trains and STEMAZING outreach
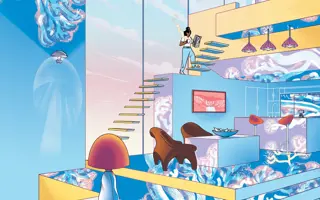
- Civil & structural
- Environment & sustainability
- Issue 95