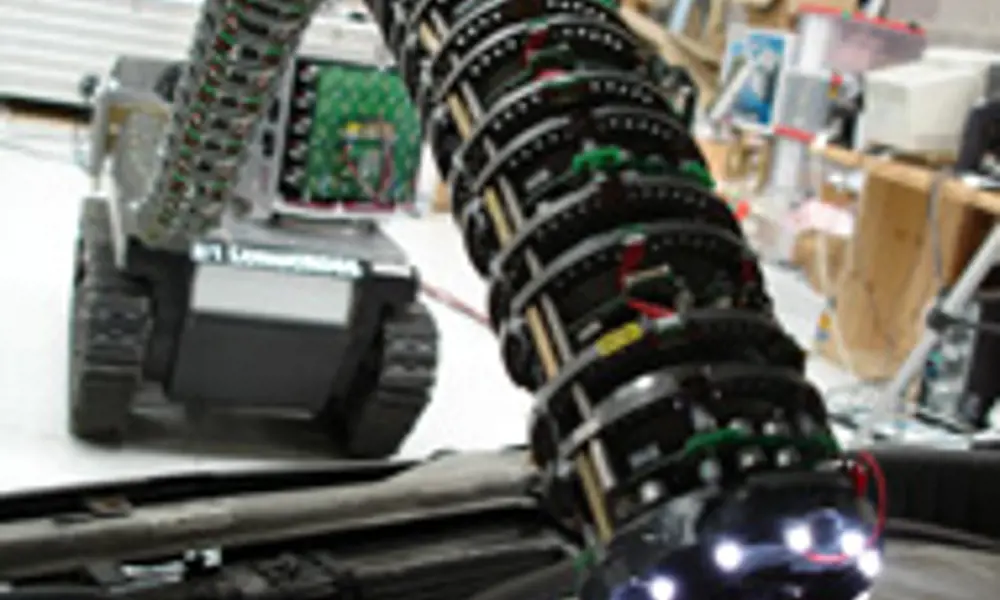
Snake-Arm Robots
Snake-arm mounted on a remote controlled vehicle reaching into a car © OC Robotics
A new species of robot has been developed that reaches into difficult-to-access parts of the human body, nuclear reactors and aircraft wings. The UK company that makes these robots attracted the attention of the Academy’s MacRobert Award committee. OC Robotics made it onto the Award’s shortlist in 2006 and co-founder Rob Buckingham tells the tale of this budding spin-off engineering company to date.
Interest and investment in robotics has waxed and waned over the last half century, with upsurges happening, on average, every 20 years. The ancestry of nearly all modern robots can be traced back to the pioneering work of Unimate in the 1960s, when they began the hugely successful process of installing the first industrial robots on car production lines. In the 1980s, significant investment was ploughed into ‘advanced robotics’, but this cycle was much less productive than that of Unimate.
What we do now at OC Robotics was formed by our experiences in the 1980s. Then, in an academic guise, we designed machines, or ‘robots’, that tried to interact with the natural world. We built machines that picked up chickens, handled and cut cod and salmon, folded cloth and sewed up jackets. All these machines worked, to a greater or lesser degree. However, none were a commercial success.
We are currently firmly into the next cycle. Perhaps the most significant difference between the current cycle and the last is the great surge in interest from politicians and potential customers. This market-pull, when coupled with technologypush, creates the possibility of massive new markets. One statistic, quoted in Europe, the USA and Japan, indicates that the robotics market will be worth $90 billion per annum by 2025.
Snake-arm robots
OC Robotics, as a company, is in its infancy. Nonetheless,we intend to win a percentage of this emerging market. Since 2000 we have focused on developing a species of robot called snake-arm robots. These are long, slender, robotic arms that can reach into confined spaces, more like flexible endoscopes than the powerful industrial robots used to assemble cars. Instead of rigid links, interconnected by joints like the human arm, they have a fluid, curving shape like a human spine.
The mathematics behind the arms aroused our curiosity (see box titled ‘The maths behind snake-arm’), but it was the realisation that these mechanisms might solve a range of difficult tasks that provided the impetus to raise venture capital and start designing.
Operational uses

Snake-arm colonoscopy is the 'scoping of the colon', which offers the ability to reach further into the colon without exerting large forces on the bowel wall © OC Robotics
The market-pull came from medical surgery. In the mid 1990s we held discussions with neurosurgeons and general surgeons about a device that could follow non-straight paths into the human body. In the brain this involved using the fluid filled ventricles as a 3D canal system to reach the lower brain, and for colonoscopy it involved following the curves of the sigmoid (the part of the colon that attaches to the anus), descending, transverse and ascending colon (see figure 1).
These are two surgical tasks that require a highly versatile and flexible device, one that can follow its nose along curved paths without exerting forces on the surrounding tissue. Surgical devices have to be very safe, easy to use, robust and easily sterilised. These practical considerations obviously led us away from standard robot designs with motors at their joints.
How snake-arm works
The basic component of a snake-arm is a patented link, which functions in the same way as a vertebra. Each link articulates with respect to its neighbours and springs are used to stabilize the link structure so that when unloaded it will straighten out. The shape of the arm is controlled by groups of three wires, 120 degrees apart, that pass through holes near the periphery of each link.
For example, if an arm has 100 links then, with three wires terminating at link 10, three at 20, three at 30 and so on, this arm would have 10 segments. The number of links and the number of segments are variables, specified according to the payload, length and curvature requirements of the arm. The shape of each segment can then be controlled independently by varying the length of each wire using motors.
The motors apply a moment at the end of each segment. This force is then distributed through the links which causes each segment to bend. One complication is that wires terminating at segments closer to the tip pass through segments closer to the base, meaning that the wire length to segment shape transforms are coupled and non-linear.
Secondary characteristics
A surprising by-product of the design of snake-arm robots is that customers are particularly interested in a range of secondary features that make the device easy to use. One feature is that the arms have a constant diameter and are hollow. This is ideal for routing services to tip-mounted sensors and tools. It also means that a snake-arm can be used like a steerable hose, as a vacuum cleaner or a fuel line.
Having a constant arm diameter means that protecting the arm from the environment and vice versa becomes as simple as sleeving the arm in a flexible skin. This is essential in situations when it is important to stop the arm becoming contaminated (in nuclear or field use) or to stop the arm contaminating the environment (surgery or food). We have also designed a snake-arm with a quick release interface between the motors and the arm. This means that the arm can be considered disposable or sacrificial.
With the motors at the base the arm mass is reduced and the centre of gravity is less variable. Consequently, the motors and electronics can be easily enclosed and easily maintained, since they do not enter the environment.
Standing out
Perhaps the most important feature and biggest difference between snake-arm robots and standard robots is that snake-arms can be designed to be inherently compliant and therefore safer than rigid robots. In most robot control systems the robot will strive to reach the requested shape, at the risk of breaking itself or anything in its way.
It is possible to equip a rigid robot with sensors and clever software to mitigate against this, but an alternative approach is to allow the robot to bend. Humans use both techniques. When we cannot avoid collisions we can become less rigid in order to attenuate large impulse forces and avoid impact damage. Many animals make use of flexibility in more obvious ways – a snake’s body, an elephant’s trunk, a swan’s neck or an octopus’ tentacles are good examples.
The challenge with less than completely rigid structures is that it is much more difficult to mathematically model what the structure will do. This would not be ideal for assembling a car – this is why robots for the automotive industry are built to be as rigid and unbending as possible. However, this does not mean that a flexible device cannot be repeatable. One of the snake-arm robots designed for the nuclear industry has a motion resolution of better than 20µm under joystick control, which matches the performance of rigid robots.
OC Robotics, along with Airbus, Remotec and Swisstulle, recently won funding from the DTI to investigate adding a skin to our snake-arms. The objective is to create a skin that is lightweight, flexible and protective with many in-built sensors that can measure touch and proximity to objects. The project is intended to discover what can be measured simply, rather than using high level behaviour control, since the outcome must be commercially viable.
Applications

Snaking into an aircraft wing rib bay for automated assembly in low access spaces
For any new technology the first customer is critical. Fortunately, in our case it was the UK MoD who took the risk. The result of this first contract in 2003 was a snake-arm mounted on a remote controlled vehicle. This was used to demonstrate gaining access into a car through a window and was highly technically demanding since the arm was largely horizontal and had to carry a payload equal to the arm mass (see figure 2).
In 2004,we designed two snakearms as part of the solution for repairing a leaking pipe in a Swedish nuclear reactor. In this case the robots enabled the customer to conduct the repair in a minimally invasive manner, using only existing access routes. An alternative repair solution would have involved removing and then replacing critical undamaged reactor pipe-work in order to create a man-sized access route to the leaking pipe. This might easily have resulted in the loss of the entire reactor.
Currently we are conducting a significant project in conjunction with Airbus, assessing how a snake-arm may be used for assembly automation within rib bays (see figure 3). At the moment wing rib bays and other enclosed spaces in aircrafts have to be designed so that people can reach or climb inside them. The advent of composite wing structures means that there are concerns over inadvertent damage. There are also health and safety risks associated with the composite fibre dust and working within such confined spaces. A tool that can reach through small holes and rivet or apply sealant will remove people from a potentially hazardous environment. It also offers the potential to standardise production methods and in the longer term may allow changes to wing design.
A significant recent achievement was winning a contract from the US Department of Defense for a very slender snake-arm (see figure 4). The primary interest is countering improvised explosive devices by giving the soldier a lightweight remote controlled device that can be used to conduct an investigation from a safe distance. We hope that this work will lead to nonmilitary spin-offs. There are many tasks in industry which require a fully steerable endoscope that can follow its nose into an awkward spot.
Portable progress
Although we have been working solely on snake-arm robots since 2000, OC Robotics is still at the start of a journey. The past five years have seen the first few hurdles flash by, including solving the mathematics and designing robust hardware. Winning the first MoD contract and then being part of the team that repaired the pipe at Ringhals was incredibly exhilarating. These successes have given us global exposure.
There are now many tens of thousands of people who know about snake-arm robots and have the power to shape our future. We will continue to invent, file patents, win and complete contracts, and develop the team. The focus of the next year will culminate in the launch of a portable snake-arm robot product with both security and industrial applications. The launch will signify the birth of this new species of robot and the start of a new chapter for OC Robotics.
The maths behind snake-arm
One of the technical challenges with the design of snake-arm is the mathematical description of the arm shape, since these robots have many more than six joints. The impact of this is best explained by the underlying mathematics. In 1955 Denavit and Hartenburg (D&H) wrote a paper that defined a general framework to describe robots comprising a number of rigid links interconnected by single degree of freedom joints. The basic control requirement for any robot arm is to take a desired position of the tip of the robot and calculate a set of joint variables that satisfy this position.
When the tip is moving in 3D space there are six independent inputs that define the required tip position and orientation. In vector notation this is a 6x1 vector which is commonly called x. If a robot has six joints there is also a 6x1 vector of joint variables commonly called q that describes the robot shape. The D&H parameters can be used to describe the relationship between the position vectors, x and q, or the velocity vectors, x and q. The resulting sets of equations are: x = f(q) and x = J q where J is the Jacobian.
The vector q is particularly useful in robot control, so the basic mathematical task is to invert J, since q = J -1x. This is straightforward if the robot has six joints because J is square and often invertible. But snake-arm robots are mathematically redundant, ie the dimension of q, dim(q), is greater than dim(x) which means that J is no longer square. The reason for inverting a non-square Jacobian is that a mathematically redundant robot has some very useful physical properties. In particular it is possible to change the shape of the robot without moving the tip. Controlling the self-shape of the arm means that it becomes possible to avoid obstacles.
Our work has shown that rather more than six joints are required to achieve this in practice. Our robots typically have 10 segments. Each segment has two degrees of freedom, which means that the mathematical challenge is to invert a 6 by 20 Jacobian in a stable and repeatable manner.
Further reference
Denavit J, Hartenburg RS,‘A kinematic notation for lower pair mechanisms based on matrices’, Applied Mechanics, June 1955, pages 215–221.
Further reference
Visit www.ocrobotics.com
Biography – Dr Rob Buckingham
Dr Buckingham MIEE CEng completed his first and second degrees on the Special Engineering Programme at Brunel University as a National Engineering Scholar. He completed his PhD entitled ‘Kinematic analysis of multiarm robots’ at the University of Bristol before becoming a Research Fellow and then Lecturer in Robotics. He left academic life to co-found OC Robotics in 1997 with close friend, and superb engineer, Andrew Graham.
Keep up-to-date with Ingenia for free
SubscribeOther content from Ingenia
Quick read
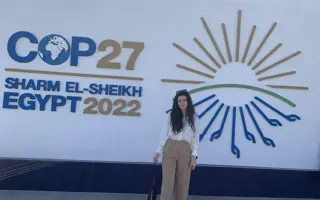
- Environment & sustainability
- Opinion
A young engineer’s perspective on the good, the bad and the ugly of COP27

- Environment & sustainability
- Issue 95
How do we pay for net zero technologies?
Quick read
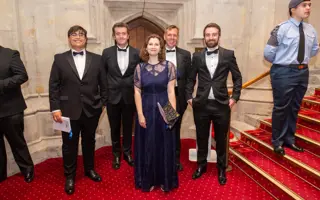
- Transport
- Mechanical
- How I got here
Electrifying trains and STEMAZING outreach
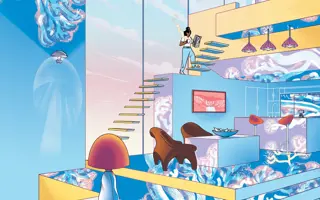
- Civil & structural
- Environment & sustainability
- Issue 95