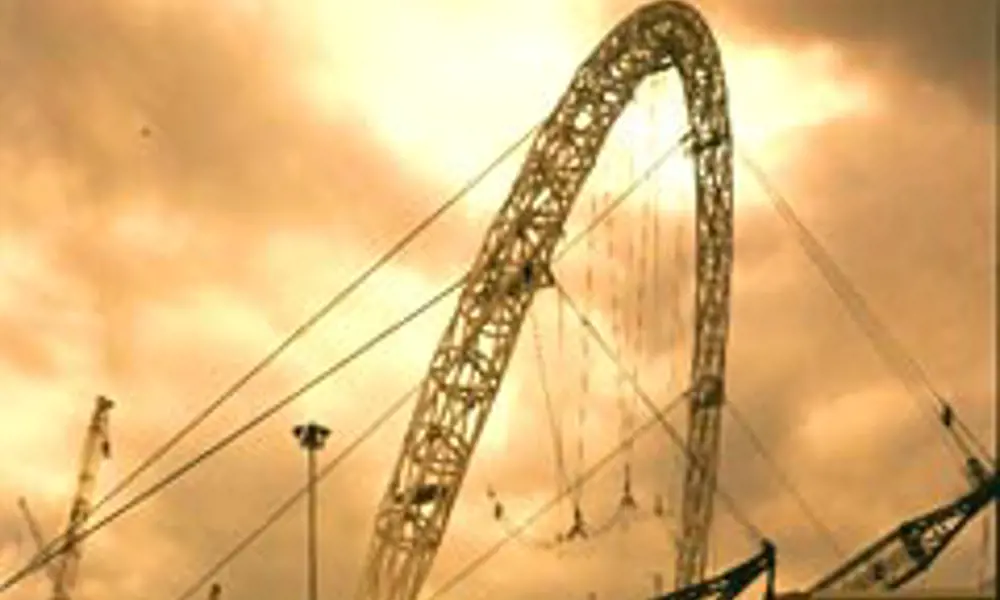
Stadia: Structural Giants
Wembley Stadium main arch Courtesy of Bianchi Morley
Anyone who sets out to build a large stadium has to consider the challenges of constructing long spans. These challenges include geometric changes under load, intuitive engineering in three dimensions and sustainability. Such considerations can be very different from those experienced in most other structures. Stephen Morley provides a personal account of his work on some of the world’s largest stadia.
After deriving the structural concept design and leading the detailed design (in most cases) on 23 stadia and arenas around the world, it is my belief that these structures are in a very different realm of structural engineering to those in general buildings. The buildings I have worked on include Stadium Australia, the main stadium for the 2000 Olympics Sydney, Benfica’s Estadio de Luz, Wembley Stadium and Wimbledon’s Centre Court moving roof. The sheer scale of these structures means that many of our simplifying assumptions and approaches for general buildings simply do not hold true for stadia. Amongst these differences is a need for engineers to retain an intuitive element to their calculations. From my experience there is a shortfall in understanding of these differences in the industry.
Intuitive engineering in 3-D
With large and complex structures the structural design engineer must have a clear and thorough understanding of the structure’s ‘behaviour’. To achieve this, the engineer must conceive the structure in three dimensions as it is built. They must imagine how the forces are transferred through the structure to the supports, and must anticipate how the structure responds in the process.
Calculations and computers are unthinking tools with which to quantify the distribution of forces through the various ‘load paths’ and the resulting deformations and should not be the only means by which the structural behaviour becomes apparent. It is not just a matter of maths and physics, rather it requires an ability to ‘immerse’ oneself in a structure and its constituent materials and ‘feel’ how it responds to loads. This is much more of an intuitive than an analytical process. Sometimes our calculation-based training gets in the way of seeing and ‘feeling’ the 'bigger picture' and hinders appreciating structural behaviour of real systems.
On a recent project I proposed a 'banana truss,' in which the main structure is curved in plan. The designated structural engineer was so concerned with this 'left field' system that he rang the project’s architect to say it could not be done. The architect informed him that not only was the arrangement I had proposed eminently stable when considered fully in three dimensions, but that the first banana truss he had worked on was one I had designed for him 15 years ago and which was still standing firmly!
Changes under load
An underlying assumption of many analytical processes and computer programmes is that the deformations under load remain small relative to the cross sectional dimensions of the elements used in the structure. This assumption does not hold true for long span structures where the deformations can be many times the cross sectional dimensions of the elements. Under the design loadings, roofs such as that for the new Wembley Stadium will deflect by metres rather than millimetres.
The effect of the change in geometry on the way in which the structure transmits loads to its supports must be considered fully and carefully – including the use of large displacement non linear solvers in the analysis process. Just ‘pressing the non linear analysis button’ on some computer programmes is not sufficient. Some of these systems use other simplifying assumptions and do not fully consider the changes in geometry. It is essential to use benchmark problems with exact mathematical solutions to verify just what the selected computer program the engineer proposes to use, and does and does not consider.
When these geometry changes are considered – depending on the nature of the structure – the forces in the elements can be found to be significantly different from those derived from an analysis that does not consider this aspect of the behaviour of the real structure. This can make all the difference to maintaining an adequate safety factor. Indeed, in some cases ignoring these geometry changes can lead to unexpected behaviour and can contribute to a potential disaster. Errors of 20% or more in design forces are common when geometry changes are not properly considered in these structures.
Another aspect of these geometry changes in real structures is that long-span flat and simply propped structures pull in at their ends or become noticeably shorter when they deflect under downward loads. The 165m span bowstring trusses of the moving roof for Melbourne's Telstra Dome pull in by about 200mm under the design loads for instance, which clearly needed to be fully considered in the design to ensure the trusses remain on the supporting bogies (similar to mini rail carriages).
Spans with memory
The way in which a long-span structure is constructed affects the stress distribution in that structure throughout its life. All too often the designers and contractors for such structures do not appreciate this factor.
Long-span structures are fabricated from elements that are small enough to be transportable. They are then assembled into sections suitable for the available cranage. While the sections are joined, these elements are temporarily supported in a different way from their support in the completed structure.
The result is that the structure ‘remembers’ the way in which it was constructed. The 'memory' is in the form of a different stress pattern within the structure when supporting loads from that resulting from the structure being completed in a zero gravity environment and then gravity being ‘switched on’.
The problem is that this latter hypothetical situation is exactly what current analysis computer programmes are geared up to analyse. They consider the weight of the structure, its ‘self weight,’ as just another load case applied to the completed structure when it is on its final supports.
In reality, the weight of each part of the structure is there all the time. It is there when the part is joined to others in the fabrication workshop, when that element is transported and assembled with other elements on site and when the resulting sections are lifted into place on temporary supports. At each stage, the deformations and stresses due to the self weight of the pieces and the way in which the pieces were supported when they were joined to other pieces is 'locked in'.
If a long span is to be designed properly and safely, self weight cannot be simply treated as another load case to be applied to the completed structure and superimposed with the effects of other loads. Rather the designer must determine a practical method of construction and must make due allowance in the design of the structure and its constituent members for the effects of this pre-installed memory.
Scale factors
It is not just the spans of the major elements that put stadia in a different realm to general buildings. The increase in the loads at the main supports are even more significant. This is because the loads on stadia roofs – such as cladding weight, snow, live load or wind – relate to the area of the roof and the area increases in proportion to length squared. Therefore it is essential to establish all loads on the roof accurately and at an early stage. This requires careful co-ordination with other design disciplines who should be equally experienced in stadia design.
We have to remember that up to 90,000 people could be sitting in one of these stadiums, which also may have a moving roof. I make no apologies for my pedantic reputation with regards to safety. If a roof of a supermarket were to collapse, as happened in recent years in the US for example, casualties may number in the tens or hundreds. If the roof of a fully occupied stadium were to collapse – to date, mercifully, collapses have been at empty stadia – then casualties could number in the thousands or tens of thousands.
Wind loads
Because the area on which they act is so large, wind loads are particularly significant in the design of roofs for large stadia. In efficient structures, the wind uplift can often exceed the self weight, leading to net uplift and a complete reversal of the direction of forces in the structure. Even when there is no net uplift due to wind, for primary structures formed of arches or catenaries which perform best under uniform loads, a critical design case can result from asymmetric wind pressures which lessen the downward loads more on one side of the span. National ‘standards’ or ‘codes of practice’ rarely have specific guidance on predicting wind pressures suitable for such bespoke structures. Therefore, wind tunnel testing is used to determine these wind induced pressures.
Pressure tapping readings measure air pressure at a specific point. They will fluctuate widely on a scale model of the structure in a wind tunnel. This is because wind flow – in both the test tunnel and for real conditions – is very turbulent. The traditional way of processing the data and deriving suitable design wind pressures has been to average the pressure readings from a number of adjoining pressure tappings across an area of the roof and to produce a weighted average of these values with time. A gust factor is then often subsequently applied to account for fluctuations due to turbulence.
A shortcoming with the traditional approach is that the ‘averaging’ process can miss major patterns of wind pressure which may be critical in design, particularly for structures which best enjoy uniform loading. To correct this, a much more sophisticated method of processing the data from the pressure tappings was developed by Professor John Holmes of Melbourne University called the ‘correlation method’ and was used for the first time for the design of the roof of Stadium Australia.
With the correlation method, sets of coefficients represent how the structure responds to pressures on the roof surface with each set relating to a particular action in the structure such as the maximum bending in an element at mid span and so on. The coefficients thus describe mathematically the pattern of wind loading that would cause a maximum response in that particular action. These sets of coefficients can then be used to ‘sift through’ the pressure tapping readings to find actual simultaneous pressure distributions experienced in the wind tunnel which would cause the maximum value for each of the selected effects.
The resulting pressure distribution can then be used, with some adjustment, to account for dynamic components of wind loading, in the knowledge that this distribution of pressures represents a ‘worst case’ for the chosen effect. As there are six potential effects, shears and moments, at each end of each member and typically a stadium roof structure would comprise many thousands of members, applying this procedure unthinkingly to every possible effect would result in an enormous and impractical number of design load cases. An engineer must therefore use experience and understanding of the behaviour of the structure to select carefully a small number of design effects that will act as markers for potentially critical overall behaviours of the structure in response to wind.
The correlation method has been criticised as being too laborious. However, with appropriate selection of ‘design effects’ based on experience and a proper understanding of the behaviour of the structure and a systematic approach to the processing of data, I believe that this need not be the case. More to the point, when properly used, the correlation method ‘seeks out’ wind pressure distributions that could cause conditions critical for the structure and for which the structure must be adequately designed. In addition, the correlation method usually results in more benign ‘uniform’ wind load cases by avoiding the artificial combining of peak pressures at different points that do not occur simultaneously – a feature of traditional post-processing methods.
‘Embodied energy’
There is much talk today of sustainable design. Sadly, a great deal of this, particularly in the design of field of sports facilities, seems to be rhetoric. Few seem to understand the importance of the ‘embodied’ or capital energy consumed in the creation of a building. In fact there are several instances where it has been shown subsequently that the embodied energy of additional construction – incorporated to reduce energy consumed in operating a building – exceeds the total energy saved during the lifespan of the building leading to a net increase in energy consumption.
It is imperative for all buildings to consider the total energy consumed, including fabrication and construction (embodied energy) as well as operation. For sports facilities, the embodied energy component is particularly important. The structures tend to be massive and require a lot of high energy materials. The facilities are also used infrequently, in some cases for only two weeks a year, and the operational energy consumption is correspondingly low.
Stadium Australia set the benchmark for the efficient use of high energy materials. Like most modern 80,000 to 100,000 seat stadia, it has a footprint approximately 300m in diameter, yet its Olympic mode side roofs, which provide three hectares of cover, use only 90kg/m2 of steel.
Few stadium designers seem to be taking up the sustainability challenge set by the Stadium Australia design. By comparison, from published data, the roof over the main stadium for the 2004 Athens Olympics used approximately 8,000 tonnes more steel to provide similar cover, consuming a further 110 million kWh and producing an extra 33,000 tonnes of CO2 in the process. It appears that the main stadium roof for the Beijing Olympics may be similar to Athens in weight.
The most sustainable structures are those used most frequently. The ideal stadium or arena is one that is used for a multiple of sports or frequently played sports, or a range of functions rather than one that is only used for a few weeks per year.
Lateral thinking
The factors that I have described demonstrate some of the reasons why stadia structures are in a different realm of structural considerations. They are all bespoke and are some of the most compelling and dynamic projects to work on. Perhaps the most important consideration for the team for a successful project, and in mitigating risk, is having an ability to think laterally, a thirst for knowledge and recognition of what they do not yet know providing an openness to learn. Designing in this field provides a wonderful challenge, an opportunity to utilise a range of applied mathematical and artistic design skills and to contribute to the creation of national and international landmark structures.
Biography – Stephen Morley
Stephen Morley is the Design Director of Bianchi Morley and an internationally renowned specialist in the field of long span structures. Stephen has designed the concept for and/or led the design of some 23 stadia/arenas and moving roofs around the world including the Gold Medal-winning Stadium Australia, UK Building of the Year McAlpine Stadium Huddersfield (which changed the way stadia were designed) and more recently Wembley Stadium and Wimbledon's Centre Court moving roof. Stephen Morley is now an advisor to the International Olympic Commission on structures, and was recently nominated for the Prince Phillip Design Award.
Further reference
Why Buildings Fall Down Matthys Levy and Mario Salvadori (WW Norton)
Environmental Design Chapter 6 Randall Thomas (Spon Press)
Keep up-to-date with Ingenia for free
SubscribeOther content from Ingenia
Quick read
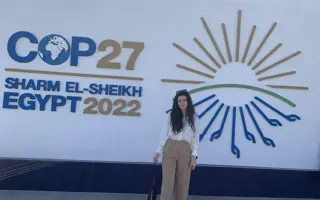
- Environment & sustainability
- Opinion
A young engineer’s perspective on the good, the bad and the ugly of COP27

- Environment & sustainability
- Issue 95
How do we pay for net zero technologies?
Quick read
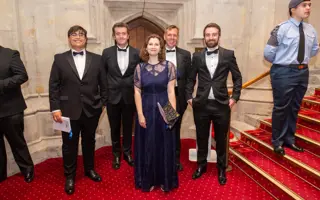
- Transport
- Mechanical
- How I got here
Electrifying trains and STEMAZING outreach
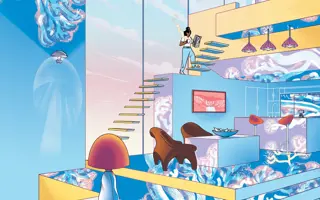
- Civil & structural
- Environment & sustainability
- Issue 95