Straddling the Thames
Over the last four years, the historic Blackfriars railway bridge has been upgraded, creating the first ever station to span the River Thames. Over 4,400 solar panels have been fitted to the roof of the station, creating the biggest solar bridge in the world and forming the largest solar array in London. Ingenia talked to Julie Quarmby, Jacobs’ lead structural engineer and Anthony Westlake, project director for Tony Gee & Partners, about the engineering design and structural challenges faced.
A new London landmark has been taking shape on the river Thames. A ribbon of glass and photovoltaics now connects Tate Modern on the south bank and St Paul’s Cathedral to the north. The reconstructed Blackfriars bridge supports a new station along its whole length, the first ever to be built straddling the river with an entrance on each bank. The completed station is due to be fully open before the start of the London Olympics.

To make the connections between the new steel deck and the existing wrought-iron arch ribs, the original rivets were removed and new high-strength bolts installed © Balfour Beatty/Network Rail
There was substantial innovative engineering needed to convert the Victorian foundations - two bridges and an underground station - into a modern railway interchange, part of Network Rail’s £6 billion upgrade of the capital’s north-south railway, Thameslink. All this had to be done while keeping Thameslink trains and the London Underground’s District and Circle lines fully operational. Once the outline design approval had been prepared by Arup (for the station) and Mott MacDonald (for the river bridge), the challenge of construction fell to consulting engineers Tony Gee & Partners for the bridge; Jacobs Engineering for the stations; and Balfour Beatty Civil Engineering as contractor on the project.
Designs on history
The project has reused an 1880s five-span wrought-iron arch bridge, together with the remaining piers of an older, long-demolished bridge alongside (see The First Rail Bridge). The scheme design had confirmed that the bridge could be successfully converted for its new use by making it 6m wider to accommodate four tracks and four platforms and stronger to carry the increase in load arising from the new tracks and trains and from the new station roof.
Some of the challenges concerned the 15 1.4m-deep l-section arch ribs in each of the spans of about 55m, which carried the load from the superstructure down into the piers near high-water level. Could they carry the extra weight? Wrought iron has little more than half the strength of modern steel, but analysis showed that by and large the ribs were comfortably strong enough for the new loads – provided the iron was still in good shape. Every part was minutely inspected, repaired and strengthened, where necessary, and eventually grit-blasted to remove all paint before being repainted to preserve the structure.
Some problems of localised corrosion were found where water had found its way through the deck, but the worst damage was from a World War II bomb that had exploded beneath the central span leaving shrapnel holes in the flanges of the ribs (varying from small to orange-sized). Around 300 repairs were needed, half due to the bomb damage. Most repairs involved bolting additional steel plate on to the flanges.

Barge works. Individual sections of the new arch ribs are installed to widen the bridge. They are hung from temporary supports cantilevering from the main bridge deck before the permanent bolted connections are made © Balfour Beatty/Network Rail
Another challenge was to create the extra width needed. On the downstream side there was just enough room to insert one additional line of arch ribs, in steel to match the old wrought iron. Alongside each pier on the other side was a line of three concrete-filled, cast-iron columns, conveniently left in place when the older railway bridge was dismantled in the 1980s. By incorporating one of these three columns into each pier, enough width was created to allow three more steel ribs to be erected on each span.
Solid foundations
There was a substantial amount of investigatory work undertaken to ensure that the pier foundations on the London clay were strong enough to carry the higher loads. More than one old bridge over the Thames has failed because of inadequate foundations – including the original 18th century Blackfriars road bridge. A sophisticated ground investigation was arranged.
From a jack-up barge in the river, 30 boreholes were sunk in the bed beneath and in the area of influence of each pier. Meanwhile, core samples were taken through the piers – including the pier of the old bridge alongside - to check whether they had been built with the depth and strength that the Victorian engineers had planned. The results were surprisingly good.
Taking the survey data, a Plaxis software package, which applies finite element analysis to ground engineering, was used to model the stress history of the bridge. The analysis considered 130 years of consolidation of the clay, stress relief during the current construction process, and then another 120 years of consolidation during the life of the new station.
The results were reassuring but two problems were detected. The first was that, as the clay consolidated, the pier from the older bridge was likely to settle at a different rate from the main pier. The solution was to create a rigid, heavily reinforced concrete saddle-beam running transversely across the top of each pier so that if one part of the foundation started to settle more rapidly, then load would immediately be redistributed to the remainder.
The other problem was more difficult. The foundations could take the extra load, but only if the weight were distributed evenly over the clay beneath, which meant that it needed to be a simple vertical load. Moving trains do not create even loads, and an out-of-balance load would create substantial horizontal forces acting along the length of the bridge. Unless something was done, the piers would then bend to resist these unequal forces, creating non-uniform stresses beneath the foundations. While this would lead to some stress release on one side of the foundation, there would also be an unacceptable increase of stress on the other.
The solution to this was to modify the principles of the original design and to carry all of these horizontal forces directly through the continuous, rigid steel-plate deck of the bridge into the abutments. On the north side, the massive existing structures provided an ample anchorage. On the south side, the solution was to design the structure for the new station entrance as part of the bridge – a massive concrete box below track level with piled foundations capable of restraining these horizontal forces at deck level as well as the thrust from the first arch span.
Construction commences
The construction started in 2009 and the need to maintain an operating railway throughout has meant that work has been constant, day and night. The essence of the construction sequence was to cut the bridge in two, literally by slicing the wrought-iron deck longitudinally from end to end. While the two-track Thameslink service remained on the upstream half, on the other half the deck and the ironwork in the spandrels were removed piece by piece and replaced with new steel. One of the crucial tasks was removing the vertical iron posts which were riveted on to the top of the arch ribs. This meant slicing the heads off some 30,000 rivets and then punching each rivet out of its hole before cleaning the iron and bolting on the new steel replacement posts. All site connections were bolted, owing to the difficulty of quality control with onsite welding. Then, in a very busy eight-week station closure period at the end of 2010 – the only time that Blackfriars station has been closed to passengers during the project – the Thameslink track was shifted to the newly reconstructed downstream half of the bridge, and the process repeated on the other side in order to create two new platforms for terminating trains.
On this side, the nearest of the disused bridge columns adjacent to each pier was stripped of its cast-iron casing and fitted with a pre-cast concrete collar from just above the water line. This contained the in situ concrete of the new combined pier.
All of the new bridge steel, including the extra arch ribs, was constructed by Watson Steel in Bolton and brought to the construction site by barge, from a temporary wharf downstream at Blackwall – by coincidence very close to where the original ribs had been fabricated in the 1880s. The specialists, Bourne Steel, fabricated the steelwork for the north and south station buildings. Most of the transport was done at night, when there was little river traffic on the Thames. For ease of handling, each of the new arch ribs was fabricated in three pieces, bolted together in position.
The bridge is designed against ship collision with cross-bracing providing support for the arch ribs, while the piers will resist the impact of massive container barges which may one day travel up the Thames.
As the bridge is reconstructed beneath the tracks, the station roof is taking shape above. Its saw-tooth shape allows natural light to enter through the steep north-facing windows, while the shallow south-facing sections support a huge array of solar panels (seeGreening the bridge). But the roof’s remarkable slenderness is dictated not so much by a search for elegance as by constraints on the design. The bottom of the roof had to be sufficiently high to accommodate not just the ballast, track and trains over the bridge deck, but also sufficient room for future overhead electrification, while the overall height was limited by the paramount planning requirement to maintain the view of St Paul’s downriver from the west.

Under construction on the east side of the bridge, the new bridge roof will provide supports for the photovoltaic cells when lifted into place © Balfour Beatty/Network Rail
Structural challenges
The solar panels require easy access for maintenance, and this was the main reason for a 1.7m-high spine beam which runs down the middle of the roof for the length of the bridge, with access hatches on to each roof section. The halves of the roof either side of the spine beam were built separately to match the construction schedule.
According to Jacobs, the real challenge has been to accommodate the huge amount of movement in the bridge, requiring complex movement joints where the bridge and roof meet structures at either end. At one point at the north end, the roof has to be able to move as much as 160mm relative to the adjacent structure.
Just to the north of the bridge, London Underground’s Circle and District lines cross underneath, and the opportunity was taken to rebuild Blackfriars tube station with a new common entrance to access all three lines. The underground station was closed early in the project, but underground trains had to continue almost uninterrupted throughout the reconstruction.
Balfour Beatty’s answer was first to surround the railway with a temporary track protection structure, made up of small steel sheets lowered down an old ventilation shaft and assembled during a weekend possession, with as little as 25mm clearance to the station structure. Then the ground could safely be excavated down by 5m or 6m either side within piled walls, and the new station built up around them. During another possession over the Easter 2011 holiday, the temporary structure was dismantled and removed the way it came, through the old ventilation shaft.
The frontage of the new north station is a three-storey curved wall of glass. Blast protection was important: the need to contain the effects of an explosion led to the building’s most distinctive feature – giant triangular-section, tapering bowstring trusses stretching from floor to roof behind the glass. These trusses are merely to withstand horizontal forces: the floors and roof are supported on more discreet concrete columns. Jacobs worked carefully with glass manufacturer Pilkington to get the right glass and the right fittings.
The same blast analysis was applied at platform level, where the glass side screens will provide weather protection as well as allowing stunning views along the river for passengers. Gaps above and below the screens will provide blast relief, as well as allowing the platform area to ventilate naturally.
Meeting timelines
The first major milestones – opening the south station entrance and introducing 12-car peak-time trains in place of the previous maximum eight cars – were met on time in early December 2011. The decision to create the south entrance, the first new station on London’s South Bank for 120 years, was vindicated by early traffic, that showed 40% of passengers use the entrance that serves the revitalised area around Tate Modern. The proportions may change in the summer when the project is completed and the new underground station is opened on the north side – in good time for the London Olympics.
With the new tube station opening in February 2012, and the south station and two further platforms due for completion in the spring, work on Blackfriars is coming to a conclusion. Network Rail’s Thameslink upgrade continues elsewhere with an equally ambitious redevelopment being undertaken at Farringdon, two stops up the line, which will provide 140 trains per hour once Crossrail services join Thameslink and London Underground trains. To the south of Blackfriars, the final piece in the Thameslink jigsaw is London Bridge where a tangle of tracks severely limits the number of trains that can run into central London. Network Rail’s remodelling of the rail layout and rebuilding of the station will allow a train every two-and-a-half minutes to run on Thameslink’s central London section, the metro-style service providing a vital boost for the capital’s transport capacity.
Keep up-to-date with Ingenia for free
SubscribeOther content from Ingenia
Quick read
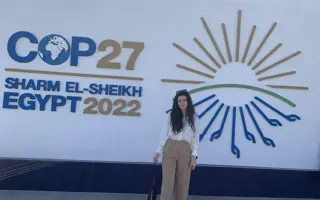
- Environment & sustainability
- Opinion
A young engineer’s perspective on the good, the bad and the ugly of COP27

- Environment & sustainability
- Issue 95
How do we pay for net zero technologies?
Quick read
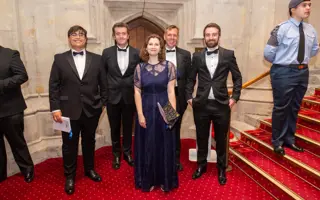
- Transport
- Mechanical
- How I got here
Electrifying trains and STEMAZING outreach
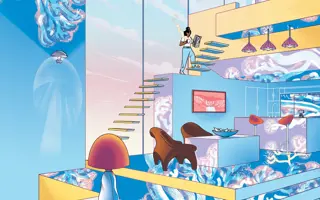
- Civil & structural
- Environment & sustainability
- Issue 95