Tate Modern
Tate Modern was opened by HM The Queen on 11 May 2000. This new gallery, created from the shell of a disused mid-twentieth century power station at Bankside on the Thames in Central London, is devoted entirely to modern and contemporary art and enables the Tate to display a significant proportion of its collection. It has received almost universal acclaim and has been compared favourably with other major modern art galleries around the world.
The public has responded enthusiastically, with one million visitors in the first 47 days, compared with the predicted three million per year.
Working with the existing building
The development of the design involved consultation and collaboration between artists, the client, (including curators) and the design team. The design works with the grain of the original building, which has been used sympathetically, but has not been over-protected. Much more than a conversion and renovation of the original building has been achieved. A true transformation of Giles Gilbert Scott’s power station has taken place.
In the conventional fashion, the plan form of the power station was divided into three: the Boiler House in the northern part, the Turbine Hall in the middle and a Switch House to the south, the latter remaining operational today.
When Bankside was first identified as a possible site for the Tate Gallery, the building was disused, leaking, in need of fabric repair and still contained all the plant from its time as an operational power station. Interim measures were undertaken to reduce the rate of deterioration of the structure and fabric of the building, and remained in place during the contract to ‘deplant’ the power station.
The combined Turbine Hall and Boiler House was a huge volume, 160 m long, 54 m wide, with a height from basement to roof of 34 m.
The approach adopted was to locate the main galleries and associated support facilities over seven levels within the Boiler House area. The Turbine Hall remains, providing an impressive entrance volume to the gallery.
Exhibits vary enormously in size and some are very big and heavy; some use unusual materials or electronics that need to be connected to support systems; many are highly sensitive to the display environment, particularly variations in environment; all are valuable and many are priceless. Art works are framed or unframed; sculptures are displayed with or without plinths; some objects are displayed on walls, some on the floor; some are hung from the ceiling. The response to these issues has been to provide rooms of differing sizes and proportions, all with a clean and uncluttered appearance, so that visual distraction is minimal and with the potential for adapting the room layouts in the future.
Wide cavity walls and dismantleable light boxes for easy access
A key component of the design developed was the concept of a double skin, wide cavity display wall. The cavity is accessible and, as well as leading to the ceiling space, provides a route for air distribution to the floor plenum for the displacement air conditioning system. The accessible cavity also allows gallery staff the facility to enhance the load capacity of the walls for the display of particularly testing wall-mounted exhibits.
The lighting system is designed to avoid veiling reflections, which would obscure the detail of exhibits, and to provide an even distribution of light on display surfaces. The spacing of the lights is such that, if a wall were removed, the space left is on the lighting grid. Similarly, if any new wall is built, its top will coordinate with the gap left by removing a luminaire. This reduces to a minimum the disturbance created by adapting wall and, therefore, room layouts.
There is equipment above ceilings that needs regular inspection. Wherever possible, this is close to walls, so that it can be accessed by climbing up inside a wall, but some had to be located further than a safe stretching distance from walls. The only elements in the ceilings are the light boxes and the glazing to these is hinged to provide additional access into the ceiling.
Internally the boxes have removable sides and top and all equipment needing servicing or inspection is located within arm’s reach of the nearest light box. The ceiling is, therefore, kept clean and clear of any access panels. Visually the light boxes are a glowing surface, which is achieved by spacing the light tubes from diffusing glass below. In the upper level side galleries, the light boxes link to rooflights to allow natural light to be used. Lighting levels are enhanced or reduced using artificial light or filtering blinds as appropriate.
The air conditioning system
The criteria for the air conditioning systems for the display spaces became apparent almost from the beginning of the project. The obvious criterion was to maintain conditions suitable for the display and preservation of the artefacts with very widely varying population densities and lighting arrangements. Not quite so obvious was the need for robustness to cope with the ways the art would be displayed: for instance, some or all of the air supply diffusers in a space might be blanked off, if they were considered to be a distraction to the optimum display of the art. Energy efficiency and simplicity in operation were high on the priority list, as was the need for maximum stability of conditions in the event of plant failure.
After analysing several systems, we chose low velocity, low level air supply through grilles in the floors, with extract through the light boxes and into the ceiling void. This system has the fewest active components at high level and thus requires minimum elevated access for maintenance, which is beneficial in terms of costs, disruption to the use and appearance of the space. The system is also energy-efficient and robust. As the supply air temperature is only slightly below room temperature, outside air can be used for much of the year, providing ‘free cooling’. This system can also make best use of the thermal inertia of the structure, in the event of short-term failure of cooling plant.
The performance of the system was assessed using computational fluid dynamics. This included considering variations in loading, reduction of supply grilles available and the potential for air to be supplied from adjacent rooms. Monitoring of the system in operation shows that it is up to expectations and is providing a stable environment. Air extracted from the galleries is discharged into the Turbine Hall to temper conditions, which would otherwise be close to those outside.
Foundation system and structured frame
The selection of the structural frame and foundation systems depended on several issues, the most influential being the presence of the massive concrete pad and strip foundations of the original building. Breaking through these would have been costly in terms of both time and money. Also, it would not have been possible to locate piles to best suit the new frame, as the existing foundations to the central line of retained columns and to the perimeter retaining walls had to continue to function. Piles would also have had to be located clear of the mass retaining wall, which would have necessitated expensive transfer structures, in order to avoid columns in gallery spaces. The preferred foundation solution was therefore a raft constructed above the original foundations and ground bearing slab. The raft was designed using iterative analyses of soil and structure models.
A steel frame complements a raft foundation, as loads from structure selfweight are reduced. The frame could also be constructed within and tight to the retained envelope of the power station. The fabrication of the frame proceeded in parallel with other construction, allowing a programme advantage. The structural grid coordinates with both that of the retained building envelope, allowing the lancet windows to be unobstructed, and with the room layouts, so that vertical structure is mostly concealed within the display walls.
Columns from the new frame are seated either directly on the raft or onto the top of the mass retaining walls at level 2. Where seated on the retaining walls, it was necessary to provide resistance to splitting or shear failure within the concrete. This was provided by tensioned bars placed in holes drilled through the retaining walls at the stanchion bearings. The raft foundation was cast into pockets cut into the retaining wall, in order to provide load transfer from the retaining walls to the raft.
Floor system and loading
The gallery floor system had to have a high load-carrying capacity, provide a sufficiently airtight plenum for air supply, and separate fire compartments at different levels. The solution developed comprises an upper structural slab with high local load capacity, supported by a lower slab integral with the overall frame.
The design floor loading for all buildings has a direct effect on the cost of the structural frame and foundations and the design load should, therefore, be the minimum commensurate with function. However, ‘normal’ recommendations for gallery floor loading would not provide the Tate with an appropriate level of flexibility in use, bearing in mind the nature of some modern art. In order to balance cost and flexibility, a loading study was undertaken.
Sculptures are clearly critical in assessing floor load requirements.They apply quite large loads over relatively small areas. However, once installed, the surrounding areas are only subject to loads from people and the gallery walls.
The Tate provided, from their database, information on weights and sizes of exhibits which had historically caused loading problems. The most critical of these were initially identified as shown in the table below.
In addition, the effect of art handling – moving loads through the building – needed to be considered. The capacity of the art handling lift was agreed as 10 tonnes, approximately 100 kN. It was, therefore, also agreed that the floor should be capable of supporting this load equally distributed between four points. The minimum track of the supporting trolley was agreed at 1.5 m. The minimum wheelbase was 2.6 m, which means that a pair of 25 kN loads can only be applied to one floor beam at any time.
The effect of concentrated load is greatest on the local, short-span structure of the upper plenum floor. The greater spans of the lower floor are less affected by local, concentrated loads, as these are averaged over the whole area supported.
The approach adopted has, therefore, been to use high local loads for the design of the plenum structure and lower overall loads for the design of the lower floor structure. It was also agreed that the level 5 galleries would be designed for slightly greater loads than other floors. At this level, the upper floor was designed for:
20 kN/m2 or two point loads of
25 kN at 1.5 m centres.
The lower floor was designed for:
12 kN/m2.
This caters for the display of: Ruckreim ‘Untitled’, Hirst ‘Mother and Child Divided’, two versions of Rodin ‘The Kiss’ placed adjacent to a display wall or three versions of ‘The Kiss’ placed away from a display wall. For each scenario, the floor member design forces due to exhibits, display walls and people were compared with those due to the overall design load of 12 kN/m2.
A user guide for floor loadings was provided to the Tate; this provides information on specific scenarios for gallery floors and a methodology for considering others.
The design has, so far, met the needs of Tate Modern.
The project required areas of the existing envelope to be opened up for both visual and access purposes. The three principal locations were above the north entrance, through the west retaining wall and the glazed openings to the ground floor cafeteria. Each needed a particular approach. The west entrance, for example, was formed through the original 2 metre thick mass concrete retaining wall below the brickwork which is retained. This required careful sequencing of work, to maintain both vertical and lateral support to the base of the brickwork during execution of the work.
Further reading
-
This article is an abstract from that published in The Arup Journal, Vol. 65, No. 3.
-
Tate Modern, Hirst et al., The Structural Engineer, Feb 2000.
Keep up-to-date with Ingenia for free
SubscribeOther content from Ingenia
Quick read
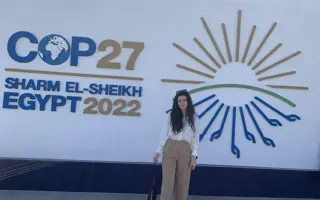
- Environment & sustainability
- Opinion
A young engineer’s perspective on the good, the bad and the ugly of COP27

- Environment & sustainability
- Issue 95
How do we pay for net zero technologies?
Quick read
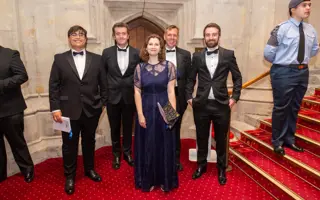
- Transport
- Mechanical
- How I got here
Electrifying trains and STEMAZING outreach
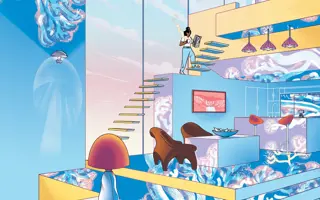
- Civil & structural
- Environment & sustainability
- Issue 95