The Falkirk Kelpies
Converting a sculpture of two horses’ heads into a dramatic 30m-high landmark on the Falkirk skyline presented an unusual challenge for the engineers involved. Felicity Starr, lead structural engineer for Atkins on The Kelpies project, worked with Andy Scott, the sculptor, on creating the 30m tall horses. She explains how the vision was turned into reality.
In 2006, Falkirk Council and British Waterways Scotland (later, Scottish Canals) were trying to resolve twin, related problems: how to regenerate derelict industrial land between Grangemouth and Falkirk, and how to overcome a low bridge carrying the M9 motorway over the River Carron that meant that canal traffic could only enter or leave the Forth and Clyde Canal at low tide. The answer to the former was the new 350-hectare Helix urban park; the answer to the latter was a short extension to the canal with a new lock, with the two projects merging into one.
A plan evolved to create two sculptures for the park, which would at the same time form an integral part of the lock mechanism, using the weight of the sculptures to displace the required amount of water to flood the central lock and lift boats into the canal network. Sketches were made of the sculptures, based on ‘kelpies’ – the mystical equine creatures said to inhabit the lochs and pools of Scotland. The idea was sold, but the sketches convinced everyone that now was the time for the engineers to defer to a professional artist.

With the main structural frame complete, contractors install the stainless steel cladding panels that create the surface form of the 30 m tall Kelpies. From the start, The Kelpies were designed for ease of erection, enabling assembly with standard mobile cranes and ‘cherry pickers’ with no need for scaffolding. Even the lifting pointsand sling lengths had been calculated for each frame of the structure, so that the frame hung from the crane at the right orientation for easy connection ©
SH StructuresAndy Scott was a natural choice. He had already established a reputation for large public sculptures, working mainly in welded galvanised steel. He frequently sculpts horses: his 4.5m-tall Heavy Horse was already a popular landmark beside the M8 motorway near Glasgow.
With one much smaller and simpler exception, he had always built his sculptures himself, with his welding kit in his workshop, without help (or interference) from others. Now he had to create two major structures, each as high as a 10-storey building, with a design that could be fabricated and assembled at an acceptable cost. This was an altogether different challenge, and one where he needed engineering help. For the engineers, our challenge had to be met while retaining the sculptor’s vision. Thus began a period of collaboration and learning for all involved, a process that would take us all outside of our comfort zones.The first creative stages were for Andy alone. He subtly shifted the brief away from mythological kelpies towards the heavy horses – the Clydesdales, Shires and Percherons – which had been the powerhouses of industry and agriculture in the Falkirk/Grangemouth area, and would once have pulled the boats along the Forth and Clyde canal.
His initial sketches, using two Clydesdale horses from Glasgow City Council as models, were developed into small-scale clay models, and then a pair of 1:10 scale maquettes, created by hand-welding individually cut rectangular plates onto a wire frame. The mosaic effect created by the flow of the plates and the view through the openings captured the horses as if in motion.
These helped secure the lottery funding which enabled the whole Helix park development to go ahead, and Andy was then commissioned to build a second set of 1:10 maquettes, exactly as he wanted them to appear. Now came the period of collaboration and compromise.
DESIGN INITIATIVES
Our first proposal was purely pragmatic. At full scale, the open steel surface would be an invitation to adventurous visitors to climb the structure, so the engineers suggested that the bottom 3m should be a smooth surface. Andy welcomed the change, recognising that the smoothing actually helped visually with the transition between the solid foundations and the perforated areas above.
Choice of material was also an area where he was happy to defer to the engineers, accepting that a stainless steel surface supported by a structure in painted carbon steel would have a much longer life than the galvanised steel he usually worked with. Another practical matter settled an important surface detail: concern about the effect of glare on motorists on the adjacent M9 motorway led the engineers to recommend a milled rather than smooth surface for the stainless steel.
Atkins scanned Andy’s second set of 1:10 scale maquettes to produce a 3D computer model of the surface. A file was created that reproduced each plate by recording the coordinates of three points on its surface. This approximately located each plate, and allowed its inclination in three dimensions to be calculated accurately, which was needed for the manipulation to follow. It also allowed a smooth, solid 3D-surface computer model of The Kelpies to be produced, which helped at a later stage when the plates needed to be made.
The most difficult and intractable engineering problem was how to replicate the surface, with its more than 9,100 separate plates, at 10 times the size of the maquettes. The construction workload would be huge: a massive supporting structure would be needed that would compromise the flow of light through the skin, and early estimates suggested the cost would be prohibitive. A solution was to replace between nine and twelve adjacent plates with a single sheet of 6mm-thick flat steel plate, laser-profiled to represent the separate sheets, and then bent in three dimensions to approximate the changes in angle between adjacent plates.
But how to avoid the costs and complications of shop-bending 959 sheets of steel in three dimensions? The answer was to erect the plates as flat sheets, and then use bolts to bend them to the shape of the underlying structure. This required careful design of the support structure, both to locate the bolt positions in the right place to achieve the required curvature, and to take the bending loads.
The engineers’ idea of merging the plates and then pulling the skin onto the outer frame made Andy nervous. He feared it would lead to unacceptable steps and discrepancies on the surface. Sketches passed to and fro, but when his questions were answered in full he supported the proposal, commenting that a little unevenness would actually lead to better-looking figures.
And so a process was developed for converting Andy’s maquettes into a buildable design. The individual plates were projected onto the smoothed solid surface model, and then examined by eye to see how the plates might best be grouped, bearing in mind the size of the profiling beds on which the panels would be cut, the maximum size of sections for transport to site, and the layout of the supporting structure. The plates in each group were joined to create an ‘ideal’ panel, smoothly curved in three dimensions and profiled to represent the individual plates. Then the anticipated support points were marked.
Further software was used to flatten the panel, producing the exact shape for cutting out during manufacture. A further routine was then run, taking the flat panel as it would be on arrival on site, and pulling it back to the required shape using the identified support points.
At this stage, we and Andy could accurately assess the error between the ‘perfect’ smoothed surface and the actual shape created – for each individual panel and between adjacent panels. Where necessary, the groupings were changed or the support points adjusted, and the process was repeated. A test erection of a sample section was carried out to prove that the system would work in practice.
BOLTING HORSES
Long consideration was given to the bolts holding the skin onto the structure. Besides taking the design loads, these bolts had to be tamper-proof and – above all – vibration-resistant. Wind tunnel tests on early models and computer simulations of wind loading showed large loading from the high winds in the area, but also the likelihood of eddies causing high fluctuating loads. The answer was borrowed from the railway industry: huck bolts, which are used in train undercarriages but rarely in construction, and never before by the fabricator of The Kelpies.
The biggest advantage of using huck bolts was that they allowed engineers to cope with the relatively large gaps between the panel and the brackets underneath before the tightening process. The panel could now be pulled using soft strops to a location close to the required shape, and then the remaining gap removed during the bolt installation; this was essential to the panel-pulling system proposed.
A huck bolt is a cross between a bolt and a rivet, consisting of a grooved pin and a smooth collar. After inserting the pin in the pre-drilled hole, the installation tool grips the pintail and swages (cold-forms) the collar over the grooves to form a tight joint. The bolts worked well, proving quick and simple to install.
FREE-STANDING
By this time, the idea of using the sculptures as part of the lock mechanism had been replaced with the proposal that they should be free-standing structures, enabling the public to go inside. From early work with the maquettes, Andy and Atkins had realised that the inside of the heads could be works of art in their own right, and this in turn required the internal supporting structure to be part of the sculpture. In any event, the supporting structure would be partly visible through perforations in the skin, so it had to look right from the outside.
Standard engineering structures are robust and geometric, but Andy wanted something that captured the form of the horse, recognising that there are no straight lines in nature. So we had to look at how to lay out the columns and members to avoid equal spacing and prevent the lines of the structure beneath jarring with the flow of the skin plates. The engineers and sculptor had to collaborate closely, poring over Andy’s books on horses’ anatomy to gain an understanding of the natural muscle form and look at how this could feed into the steel design. These studies led to the back under the mane and the natural bulge under the throat being used to hide some of the additional supporting structure. In places, curves were compromised by using straight pieces of steel which, when joined together, look like curves.
The resulting supporting structure comes in two parts. The first is a structure based around twin-braced triangular trusses, interconnected by bracing frames to form an efficient and stiff primary structure. This supports a secondary frame following the internal surface of the skin, consisting of cladding rails carrying the brackets which pick up the thousands of fixing points for the stainless steel skin.
Particular attention was given to the details of ears, eyes and chin, where the surface curvature was greatest and the steelwork most complex – and to the horses’ manes (see Flat plate solution).
The design for the whole structure was refined to ensure that it could be fabricated and assembled, and was put out to competitive tender. The £5 million contract was won by steel fabricator SH Structures.
EQUISTRUCTURE
Based at Sherburn-in-Elmet in North Yorkshire, SH Structures specialises in complex steel structures – the type of project which its competitors tend to avoid. The firm had been approached by The Kelpies’ team in 2008 to provide some input to the budgeting of the project, and had later assembled a trial skin panel to test the proposal to use laser-formed sheets bent to shape over the frame using huck bolts.

The HOME arts event, in April 2014, was the international launch of The Kelpies. The light and flame show was by Groupe F – the same company responsible for the millennium show at The Eiffel Tower © The Helix
After a prequalification process, SH Structures submitted its tender for the project in January 2012, along with several other fabricators. All of the bids came in over budget and, for a while, the future of the project was in doubt. But SH Structures had suggested in its bid that substantial savings could be made by modifying some of the internal supporting structure. Atkins’ design was for a tubular steel triangulated frame, with bracing that included a series of horizontal, flat diaphragm plates. These plates had to be profiled to follow the contours of the external skin, and stiffened, which involved a lot of work, and SH Structures thought that significant savings in fabrication and assembly could be made by replacing these plates with tubular steel, curved to follow the surface.
The firm was given four weeks to prove that the changes would have the desired effect. As a result, SH Structures was appointed as design-and-build contractors, working with structural engineers Sinclair Knight Merz (part of the Jacobs group). The original skin design was retained, but the supporting structure was redesigned in all tubular steel. This resulted in savings of around £750,000, enough to ensure that the project could go ahead.
SH Structures produced its own 3D model of the structure based on, and complementary to, Atkins’ surface model. A BIMsight building information model was used to exchange information between artist, engineer and fabricator. The model contained all the design detail, but fabrication and assembly drawings still needed to be prepared: nearly 2,000 were eventually produced.
The company fabricated all of the structure in its own workshops, assembled into the largest pieces which could be carried by road. The whole structure was far too large to test-assemble before delivery, but each adjacent frame was match-fitted to its neighbour before leaving the workshop, to ensure a perfect fit on site. A computer program helped define the lifting points for each frame and the correct sling lengths, so that the frame would be at the right inclination for assembly from the crane.

View looking up inside one of The Kelpies showing the primary structure based on twin braced triangular trusses, the secondary frame with cladding rails and brackets, and the stainless steel plates forming the outer surface ©SH Structures
Erection on site was remarkably straightforward, with no heavy cranes or complex access systems required: first the primary trusses were set in place, then the secondary steelwork, followed by the stainless steel skin. Standard mobile cranes sufficed for all the lifting, while safe access was provided by mobile elevating work platforms, or ‘cherry pickers’. All of the skin was added on site, most of it ‘in the air’ after the structure was erected: the exceptions were the more complex sections such as around the mouth, where the skin was added at ground level before lifting into place. The whole erection process was completed in 90 days.
Andy Scott visited SH Structures several times during fabrication, and was impressed by the project team’s positive attitude and passion for the project. He feels that few people will appreciate the complexity and skill that went into the fabrication and assembly process, or what he calls “the magic behind the scenes”. A total of 309 tonnes of steel, 6 km of steel tubes and 34,566 individual pieces went into building the tallest equine sculpture in the world and one of the largest pieces of art in the UK.
The Helix Park, with The Kelpies as its centrepiece, was opened in April 2014 to international acclaim. Visitor numbers in the first two months were 150,000 – already half the number predicted for the first full year.
As for the sculptor, his moments of doubt, the times when he nearly walked away from the project, came not from his relationship with the engineers and fabricators, which was excellent throughout, but from his frustration in the early days at the seemingly interminable issues of cost and politics. He now recognises that getting a £50 million regeneration project started in the teeth of a recession was a major achievement in its own right; that delays and compromises were inevitable; and that the transformation to the whole region has been amazing. His greatest joy is that the people of Falkirk and Grangemouth, who live with The Kelpies every day, appear to love them.
THE HUCK BOLT

This is a locking bolt that consists of a grooved pin and a collar. The fastener is applied by inserting the pin into the prepared hole and placing the smooth bore collar on the pin. The installation tool then grips the pintail, which is sectioned from the rest of the bolt by a breakneck groove. When the tool is activated, the jaws in the nose assembly pull on the pintail and the nose anvil pushes on the collar to remove any gap. Then the nose anvil starts to swage the collar into the grooves on the pin. Continued swaging causes the collar to lengthen and develop pre-load. When the swaging of the collar into the lock-grooves is complete, the pintail separates from the pin and the installation cycle is complete.
FLAT PLATE SOLUTION

1:100 scale models used for wind tunnel testing © Atkins
The details which required the most intense collaboration between sculptor and engineers were the horses’ manes. On Andy Scott’s first maquettes, they were formed from many long, flat sheets cantilevered out from the surface. After preliminary discussions, this was changed on the second maquettes to a structure using angled sheets. Even with the changes, two problems remained. Providing sufficient support points for the mane structure would require an unacceptably dense support structure underneath. And the mane area was known to have high, fluctuating wind loads: wind tunnel tests and computer analysis had highlighted eddy shedding off the mane elements, and peak pressures occurring in the mane area.
The sculptor was open to ideas for different solutions, but adamant that the mane area should have a different, rougher texture than the body of The Kelpies. The team reverted to the design of the mane on the 1:100 scale models, sculpted in clay and then cast in resin, which had been produced originally as discussion tools to test ideas, as well as wind tunnel models. Gradually, an acceptable solution emerged. In the final design, the manes consist of several segments, each made up of a series of individual large flat panels, with angles between the panels providing the shape of each mane segment.
Unlike the main structure, where the skin panels are pulled and shaped round the supporting structure, the mane panels all remain flat. However (as on the main structure), they have been laser-profiled, to create the illusion that they are made of longer, thinner pieces of plate. Uprights have also been added, welded to the outside surface to provide more texture and mimic the effect of using angles.
Throughout the structure, Atkins had been keen to rely on bolts for connecting elements, keeping welding to a minimum – for both engineering and visual reasons. These angles on the mane were the principal exceptions. The use of flat plate for the mane panels meant that a very simple stand-alone supporting structure for the manes could be developed, connecting to the main structure at just two or three locations.
BIOGRAPHIES
Felicity Starr graduated from Cambridge University in 2006 and is a senior mechanical and structural engineer with Atkins. She has worked on projects across a wide range of industrial sectors.
Andy Scott is a Scottish sculptor who graduated from Glasgow School of Art in 1986. He has, to date, completed 70 projects across a wide range of disciplines in a number of countries.
The author would like to thank engineer and freelance writer Hugh Ferguson for his help in writing the article and Tim Burton, SH Structures' sales and marketing manager.
Keep up-to-date with Ingenia for free
SubscribeOther content from Ingenia
Quick read
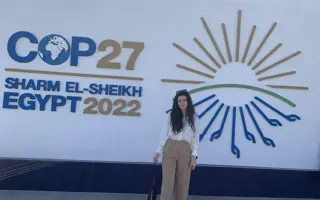
- Environment & sustainability
- Opinion
A young engineer’s perspective on the good, the bad and the ugly of COP27

- Environment & sustainability
- Issue 95
How do we pay for net zero technologies?
Quick read
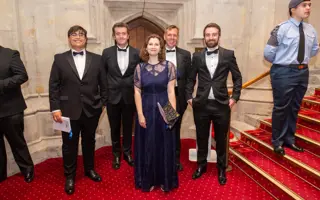
- Transport
- Mechanical
- How I got here
Electrifying trains and STEMAZING outreach
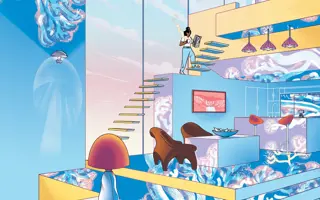
- Civil & structural
- Environment & sustainability
- Issue 95