The Wheel: The British Airways London Eye
The opening ceremony for the British Airways London Eye marked the culmination of 18 months intense activity designing, building and testing one of the Millennium Year’s most publicised and noteworthy projects.
Behind the very welcome media exposure lies an engineering achievement that is across disciplines and across national borders on a breathtaking scale. More importantly the project is being consistently described as an ‘engineering triumph’ and has done more to raise the profile of construction engineers with the general public than any of the numerous initiatives mounted by bodies representing engineering.
The ‘Wheel’ started life over 6 years ago when David Marks and Julia Barfield responded to a competition held by the Sunday Times soliciting ideas on how London should celebrate the Millennium. They proposed a huge observation wheel, sited at the heart of the capital on the bank of the Thames. Overcoming the challenges of obtaining financial backing, planning approval and the general political backing is in itself a story of perseverance, skill and dogged determination to succeed. But for the purposes of this article, it is merely sufficient to record that after a frustrating false start in early 1998, the project finally got underway in the autumn of 1998 leaving just over a year to complete all the work.
Project strategy Unusually for such a complex project, the work was carried out on a ‘Design and Build Basis’ through a Construction Management form of contract. The Client (The London Eye Company) appointed a management contractor Mace, whose role was to prepare and let separate trade contracts; run the entire project; co-ordinate the work and drive the programme. A key part of the strategy was to galvanise the enthusiasm of the separate contractors for the ambitious task ahead. Right from the outset it was realised that the only chance of achieving their common goal was in a spirit of openness and partnership.
The Dutch steelwork contractor, Hollandia, had the responsibility for design, fabrication and erection of the Wheel’s superstructure and drive system. The capsules and overall control system were the responsibility of Poma, a French Company with considerable expertise in cable cars and ski lifts. The Wheel’s foundations and all the river works were designed and built by the English contractor, Tilbury Douglas. Altogether six European countries contributed significantly to the project and co-ordinating their work over that geographical area and cultural spread added significantly to the project team’s task.
The key technical role of sustaining the Wheel’s appearance and style rested with its originators, Marks Barfield. They remained on the team both as shareholders and project architects. Babtie Allott & Lomax, consulting engineers, acted as Key Consultant on the trade Contracts plus fulfilling the major role of Independent Checking Engineer, verifying the design and certifying safety (this is a requirement under HSE guidelines for ‘rides’).
The technical challenges of the Wheel centre around two key features, namely that it:
-
cantilevers out over the River Thames, i.e. the spindle is supported at one side only; and
-
the capsules are supported on rings outside the rim, and passengers are free to move around inside the capsule so that an active floor levelling system is required.
Structure
The wheel itself has the relatively simple structural form of a stiff ‘rim’ supported by cable ‘spokes’ back to a central hub. The whole of the rim, hub and inner spindle are then supported on a massive inclined A frame stabilised back to foundation level by cables. The rim is an open triangular-section truss, fabricated from a large number of steel tubes welded together. Visually the wheel appears to be a true circle but is actually formed by 64 straight chords around the perimeter with a kink at each joint.
The rim is connected to the hub by 64 spoke cables (70 mm diameter) which carry the main structural loads from rim to hub. All these cables are prestressed to prevent slackness in high winds and as a by-product of this, the whole rim is kept in constant ring compression. Since the Wheel is driven from the rim edge, the central hub must be made to either follow or stop in braking and this is achieved by means of slightly inclined ‘rotation’ cables. These rotation cables are arranged in two sets of eight, one set per face with one set allowing clockwise and the other anti-clockwise rotation. Lateral rim support is provided close to ground level by the two Restraint Towers, one at each end of the boarding platform. As well as providing structural restraint, the north tower supports the rim drive system and the south tower supplies the power to the rim.
The hub rotates around the fixed spindle on a pair of spherical roller bearings, one of which is configured to provide axial restraint and thereby prevent the rim sliding longitudinally along the spindle. The bearings are an ‘off-the-shelf’ design selected at an early stage in the process, so that hub and spindle dimensions could be matched to suit the bearing size.
The spindle is a critical part of the structure. It acts as a single component cantilever carrying the Wheel’s selfweight of approximately 1600 tonnes together with the worst storm wind loading (blowing in from the east); this wind nearly doubles the over-turning moment from self-weight. Although the passengers are a highly visible part of the loading, it is worth noting that even if all 32 capsules were full with their complement of 25 persons each, then the resulting 800 passengers would only weigh about 60 tonnes. They would thus account for only about 2% of the maximum moment on the spindle!
The spindle takes the form of a massive hollow tube of steel made in eight separate ‘slices’, seven from cast steel and one from steel plate rolled into a tube. If aligned vertically, the spindle is 25 m high, equivalent to about seven stories in a normal building. All cast sections were made under a subcontract to Hollandia by Skoda Steel in the Czech Republic. Due to the extreme criticality of this part, a very comprehensive inspection and testing programme was instigated, and this concentrated on ensuring and validating the reliability, toughness and integrity of the spindle as fabricated, rather than its ‘strength’ as such.
The tube walls of the spindle were up to 230 mm thick and the separate sections were butt welded together through this full thickness. To reduce the magnitude of locked-in stress concentrations that are an inevitable consequence of welding, each of the circumferential butts was subjected to post-weld heat treatment. Moreover, once the whole spindle had been completed, it was load tested to a magnitude simulating 20% above the maximum working forces. This test in itself was a major undertaking, but it gave positive reassurance of load capacity and beyond that, it bestowed further improvements to the spindle’s toughness, reducing the risk of failure from fast fracture.
Erection
The Wheel’s structural layout was readily established as sufficiently strong and stiff when complete but getting to this state was foreseen as problematical. With the rim in the vertical orientation, the spokes could not have been added without extensive, costly and physically disruptive ‘falsework’ (temporary supports). Such falsework would have been essential to allow the rim to be built in sections and then held secure against self-weight and wind loading until the spoke cables were installed and stressed in sequence. The stressing would have been sequenced between ‘equal and opposite’ pairs. The alternative method of construction, and the one famously adopted, was to assemble and stress the whole rim laid out flat, and then ‘lift’ the whole Wheel structure upright in one single operation. The target was to erect the fourth tallest structure in London in just one day. To achieve this, bearing in mind the Wheel’s final location was over the Thames, a series of steel-piled ‘islands’ were built as working platforms on which to rest and join up the rim quarters shipped over by barge from Holland. Each quarter weighed 160 tonnes and was lifted into position by floating crane. The hub bearings and spindle assembly, as one unit weighing 350 tonnes, was installed in the centre of the rim onto a further temporary platform (this was actually a barge sunk to the river bottom to provide enough base support). The spoke and rotation cables were then installed using a purpose-designed bridge structure spanning from hub to rim and manoeuvrable to allow delivery of prepared lengths of cables to their anchorage points. All cables were then prestressed in sequence by a precise controlled displacement method (although the loads in each cable were monitored throughout the stressing process).
Meanwhile the pair of A-frame legs was installed between the spindle and two land based foundation plinths. These plinths incorporated a simple stainless steel ‘pin’ around which the whole structure would rotate during the main lift. The lifting force itself was delivered from a strand jacking system located at the top of a further temporary A-frame standing some 90 m high and erected vertically on top of the foundation plinths (Figure 1).
This method of erection had many advantages, not least of which was providing an amazing spectacle to millions of people (since it was televised live over the weekend of October 9th/10th 1999). In engineering terms, the lift geometry provided the comfort of a peak loading test on all critical components of the system at the instant of lift-off – thus monitoring and testing most of the main Wheel’s structure literally at ‘ground level’.
It is well known that the initial lift was aborted because of a cable problem. To prove the system it had been decided to hold the rim down on the river islands whilst simultaneously pulling upwards with about 110% of the calculated lift load. During this test, a number of temporary anchor cables slipped their connections, forcing a delay. But in the spirit of the contract, the principal engineers involved immediately retrieved the damaged parts, spent the next couple of days simulating the failure until they understood the cause and could devise remedial measures. These were implemented fairly quickly and the second lift was of course successful. During both lifts, cable forces were constantly monitored via load cells and shown to match theoretical predictions almost exactly.
Passenger capsules
The 32 capsules are where the public comes face-to-face at a close-up level with the Wheel, and the capsule design has from the start focused on the passengers’ needs rather than the technology itself. The prime requirement has been to provide a safe and userfriendly environment in which the passengers can experience the clearest and most exciting views possible over the whole of London. Unlike most other big wheels, fixed seating positions are not provided, as this would have greatly restricted the ability of each passenger to enjoy the experience, linger over the views in a particular direction, or interact as a group. The decision to house the capsules in a ring support outside the rim provides for the clearest possible views when capsules are above the centreline height. At that stage in most other wheels, the capsules that are traditionally top-suspended begin to drop down into the rim structure and take-away the clear and uninterrupted vision provided on the Eye.
Capsule structure
Although dwarfed by the main wheel structure, the capsule structure is itself equally unusual and innovative. Significant use has been made of the glass skin and of the inherent strength of the capsule’s double-curvature shape. Whilst there is a lightweight steel frame forming an underbelly chassis and a basic framework for the exterior skin, the panels of laminated double curvature glass (2 x 6 mm sheets with a 1.2 mm interlayer) provide in-plane stiffness to limit deflections and enhance rigidity. The glass panels are prefabricated to a high degree of optical quality and secured to the steel frame with a cured polysulphide based adhesive. Full size panels were load tested in advance, both for impact and to ensure they had capacity to carry the loading from passenger weight. Potentially this might be required in the extreme event of a floor levelling system failure since this could be accompanied by excessive tilt.
Floor levelling system
The centre-of-gravity of the loaded capsule is fairly close to the centre-ofrotation and therefore ‘gravity’ alone cannot provide sufficient control over the horizontality of the capsule floor when this is subject to uneven passenger loading. Although true in normal circumstances, capsule response to unbalanced loading is sluggish and so gravity control would be adequate for emergency use.
To control the floor, a motor-drive system has been incorporated within each capsule. The motor is capable of variable speed and drives the capsule relative to its supporting ring, so maintaining a high degree of stability. The single electric motor is connected through a magnetic clutch to a fixedratio gearbox. In turn, this gearbox drives a shaft that terminates at each end in a cog fitted into a toothed ring (the cog and ring are duplicated). The motor is controlled in two ways. Firstly encoded signals from the Wheel’s hub provide a calculated floor level for the particular capsule, relative to its then position on the rim. Secondly, inclinometers attached to the underside of the capsule floor react to any change in loading as the passengers move around. If minor tilt is detected, instructions are sent via a control system to provide for floor level correction. The inclinometers thus provide a check and fine control on the basic drive positioning. Naturally, a very high degree of safety (via duplication of components and a logic-based PLC control system) has been incorporated into the design.
Safety systems
Other capsule safety-related features are the door opening and closing arrangements. These are automatic and have to be interlinked with the capsule position data, so that doors are unlocked and opened only when the capsule is moving alongside the boarding platform. To assure this, a direct physical method of positioning is used, with sensors that establish the capsule’s approach to the boarding platform area. The physical check is combined with a software check so that two diverse systems are in control. All doors must be closed and locked before the capsule leaves the platform area and this must be verified by the control system. This same cycle of approach control is used to generate a signal to open (again automatically) a series of barriers in the front of passenger ‘corrals’ located on the platform. Passengers are ‘pre-boarded’ into these corrals by the ride operations staff to await the arrival of their capsule, and then the barriers open just in time allowing the passenger group to walk forward sequentially across the moving ‘gap’ and board the capsule for their ‘flight’.
Other facilities in the capsule include air conditioning and cooling, which is installed to ensure comfort in hot weather and to prevent condensation forming on the glass walls in cold weather: any misting would obviously detract from the viewing experience.
Power and control
All the capsule systems require electric power. But power has to cross two rotating interfaces to enter the capsules (i.e. ground–wheel, and wheel–capsule) and so this is accomplished via duplicated bus-bar/slip-rings (Figure 5). Power itself can be dealt with in this manner, but the electrical signals required for control would be disrupted across the mechanical interface so they have been established by radio transmission. The control system is based on dual PLCs in the operation room and dual on-board PLCs within each capsule. There is a two-way exchange of information – data is being provided from monitored sensors and circuits on board back to the central PLC and then instructions are issued back to the capsules to perform certain tasks such as controlling the stability system motors, or opening and closing the doors.
Concluding remarks
There are numerous fascinating features about the Wheel that are not widely known but add considerably to its interest. For example, at the design stage there were understandable concerns about the build tolerances achievable in the rim. To some limit, the rim will be neither round, nor plane nor concentric. These variations, together with predictions of movement under temperature and wind, suggested that the gaps between the capsules and the fixed Boarding Platform might be too variable for safe boarding. To pre-empt problems, a movable platform edge was developed and this is controlled by sensors such that it follows the rim motion in two planes. In the event, the method of rim assembly achieved exceptionally close tolerances so to date there has been no need to activate the movable platform edge.
Mention has been made of the measurements made during the erection of the Wheel and the assurance they gave. Amongst these, the cable tensions were read remotely by means of transducers housed in the hub. The system was installed by an Italian contractor and he can, even now, read the tensions from his offices near Milan! This monitoring system is to be maintained so that the cables’ response to environmental conditions can be observed and if necessary cable tension adjusted.
The Wheel is a very light structure and potentially susceptible to wind excitation. To counteract this and to limit any lateral motions that might cause sickness, the rim is fitted with 64 mass dampers tuned to the rim’s natural frequency.
During design much thought was given to the consequences of the main bearing jamming; remembering that the rim edge is being driven, this might lead to catastrophic damage. To assure against this possibility, apart from the use of high quality bearings, an acoustical monitoring system has been installed to constantly check bearing condition. Yet should this fail there is a second reserve system based on lasers. Three lasers fixed to the hub fire light beams radially to reflect off mirrors set on the rim. If the bearing were to jam, the mirrors would displace relative to the hub and the return laser beam would be disrupted: this would break the circuit and cause the control system to stop the wheel in advance of serious damage.
The conception of the London Eye was of a fun structure that people could enjoy as well as wonder at. It has achieved both of these objectives to popular acclaim and the views from the capsules are breathtaking. The technical and management challenges have been formidable, accentuated by the short time scale available; all the obstacles were overcome partly by technical skill but underpinned by the team’s tremendous desire to succeed.
The author is grateful to his colleague Dr Allan Mann for assistance with the text and illustrations, including the cover of this issue of Ingenia.
Keep up-to-date with Ingenia for free
SubscribeOther content from Ingenia
Quick read
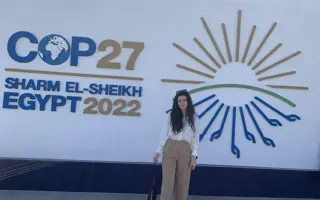
- Environment & sustainability
- Opinion
A young engineer’s perspective on the good, the bad and the ugly of COP27

- Environment & sustainability
- Issue 95
How do we pay for net zero technologies?
Quick read
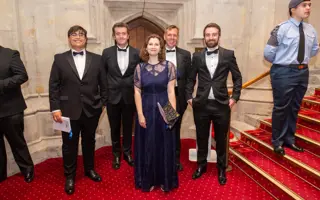
- Transport
- Mechanical
- How I got here
Electrifying trains and STEMAZING outreach
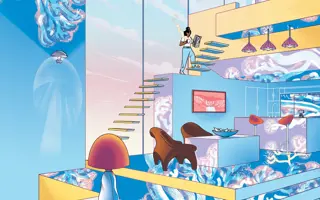
- Civil & structural
- Environment & sustainability
- Issue 95