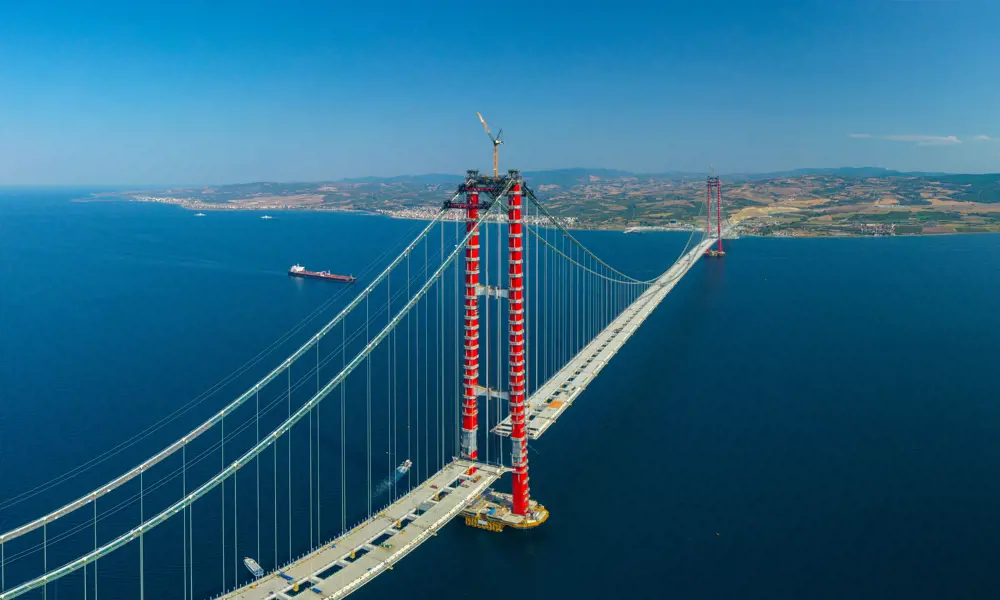
Bridging the Eurasian gap
Did you know?
Why did Turkey build the Çanakkale Bridge?
- The Dardanelles is one of two straits (narrow channels of water) separating European Turkey from Asian Turkey
- So, local passengers used to rely on a one-hour ferry to cross. Long waits often dragged travel times out to up to five hours. Now it takes just six minutes to drive over the bridge
- Ships travelling from Black Sea ports must go through these two Turkish straits to reach southern Europe and northern Africa – making the Dardanelles a crucial waterway for countries including Russia and Ukraine
Constructing a huge bridge across a busy international shipping channel presents a host of challenges. How do you minimise disruption to sea traffic? How do you keep workers safe in hazardous conditions – at height, over water, and in often ferocious weather?
But for the 1915Çanakkale Bridge, crossing the Dardanelles Strait in Turkey, one of the greatest challenges was time, for both political and commercial reasons.
The 1915Çanakkale Bridge joins the Asian and European parts of Turkey. It is named to celebrate an Ottoman victory against an Allied naval fleet during the First World War, which took place on 18 March 1915. The contract for the bridge was signed on 18 March 2017, with its expected completion during centenary celebrations for the formation of the Turkish Republic in 2023.
The contract was let to DLSY, a Turkish/South Korean joint venture, on a ‘build-operate-transfer’ basis. This meant DLSY financed construction, which would then be repaid from tolls until 2033. After this point, some 16 years from signing the contract, the toll fees would be paid to the Turkish government.
The construction works were valued at $1.68 billion. Based on the total in toll fees from the 60,000 vehicles expected to use the crossing each day, revenue of $900,000 a day was expected. So, each day saved would produce nearly $1 million extra for the contractor – a huge incentive to finish early and, vice versa, to avoid delayed completion. In the end, President Erdoğan of Turkey opened the bridge a year early on 18 March 2022.
How to build a suspension bridge
The construction programme on suspension bridges starts with the main towers, their foundations and the cable anchorages. Next comes the two main cables, and then the deck.

For the Çanakkale Bridge, each cable was an almost metre-wide bundle of 144 steel strands (each made up of 127 wires), anchored to the land either side and supported on the two towers. As with many other suspension bridges, constructing the deck involved floating prefabricated deck sections to site by barge, hoisting them into position, connecting them to hangers from the main cables, and then welding deck sections together.
But where the Çanakkale Bridge differed from most suspension bridges was by its innovative approach to assembling the deck, which saved months of construction time. Key to this was a piece of equipment called a gantry, which would do the heavy lifting once manoeuvred into place; and a sophisticated control system to coordinate its movement. Thanks to this system, two of these specially designed gantries could hoist two deck sections in tandem – up to 48 metres long altogether – to their final positions.
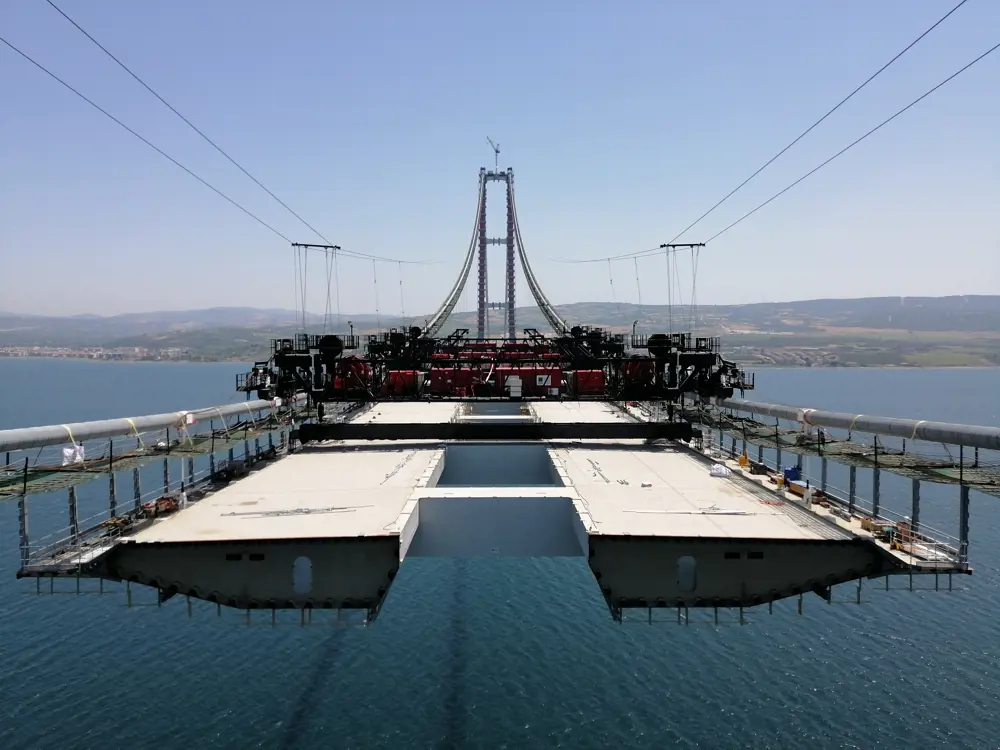
UK-based DLT Engineering designed and supplied these cutting-edge gantries, each of which weighed in at 260 tonnes – about twice the weight of the average blue whale.
They worked with DLSY and Çanakkale’s Danish bridge designer COWI, having trialled a prototype version of the same design with great success on the Nizhou suspension bridge in southern China. Twelve engineers and technicians from DLT’s Darlington office worked on the project, led by Principal Engineer Mercedes Ascaso Til, with support from DLT’s other offices.
Similar to how a butterfly spends far longer in a cocoon than as a butterfly, the gantries spent about two and a half years in design, manufacture and testing. It then took engineers just two months and one day to build almost 3.4 kilometres of deck. Ordinarily, this would take many months.
Similar to how a butterfly spends far longer in a cocoon than as a butterfly, the gantries spent about two and a half years in design, manufacture and testing. It then took engineers just two months and one day to build almost 3.4 kilometres of deck.
A cable-crawling, self-assembling gantry
According to Mercedes, who managed most of the process remotely from Darlington, the greatest innovation was the self-erecting, self-dismantling gantries – a world first.
Normally, to build the central span between the two towers, barges transport gantries to the midpoint of the bridge. A floating crane then lifts the gantry to the lowest point of the cables, temporarily blocking the middle of the channel.
The problem is, floating cranes large enough to access the cables more than 100 metres above sea level are expensive to hire, and companies have to book them months in advance – leaving no flexibility in the programme. Miss the slot and another may take ages to arrange; save time in the run-up, and the savings are wasted waiting for the crane.
Alternatively, gantries can be assembled using cranes on the towers. However, this method can add several days onto the process. Not only does it require temporary frames to be constructed on the towers, but the gantries must be lowered along the cables to where they will start lifting deck segments.
But what if the team could transport the gantries by barge, attach them to the bridge’s main cables, and lift them with their own jacks? And what if it could be lifted at any point in the span? This would remove the need for floating cranes, while also minimising disruption of sea traffic in the centre of the channel.
Mercedes’ and DLT’s ingenious self-erecting system made this possible. This delivered the gantry in three sections to the main cable level, via a steel lifting frame with strand jacks attached at either end, 38 metres apart – the same as the two main cables. This auxiliary structure supported the gantry until it was assembled into its final configuration and lowered onto the main cables.
Assembling the gantry
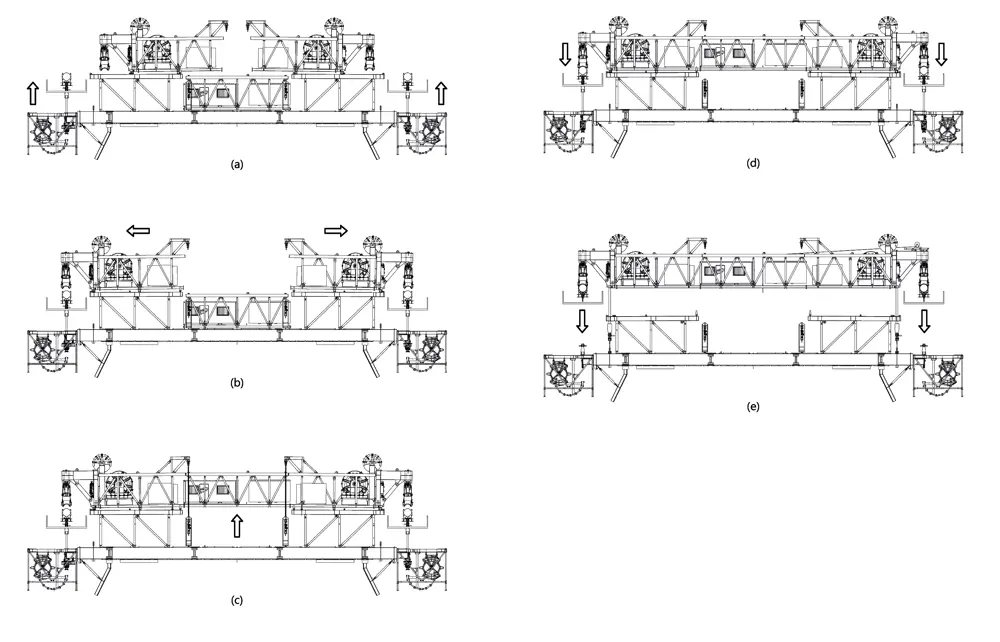
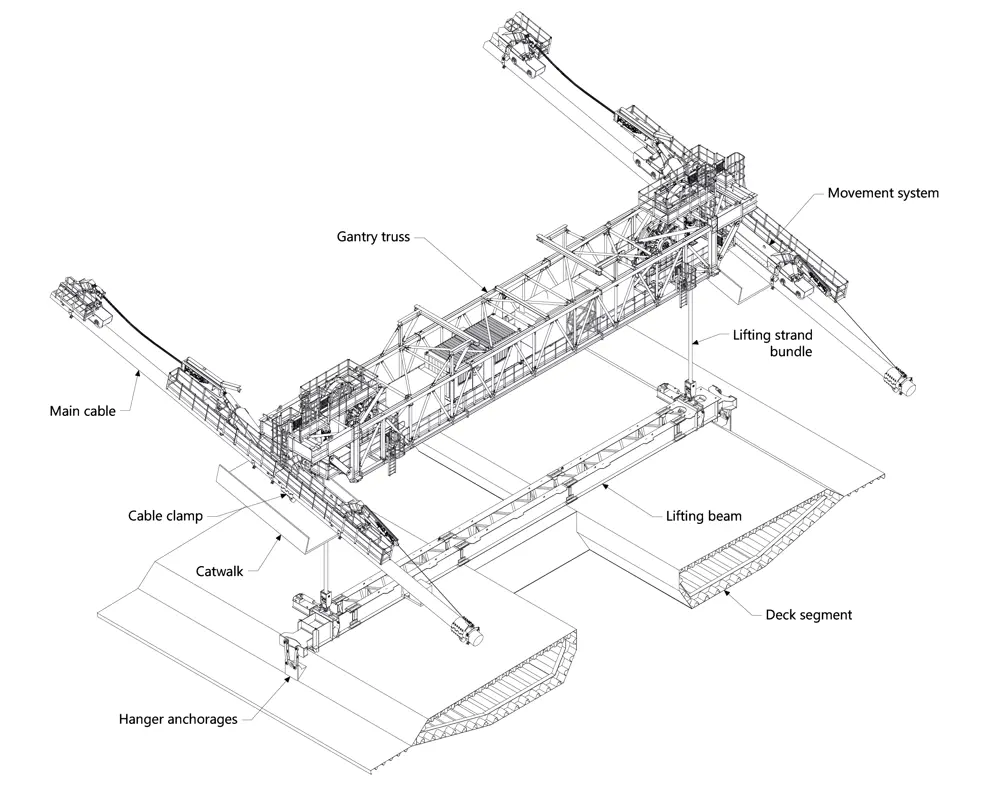
Lifting the deck
Once in place, the gantries had to be moved along the main cables to the right position on the cables for each lift. The strand jacks were used for this, too.
When stationary, or during lifting, the gantry rests on steel supports clamped to the main cables. For movement along the cable, its weight is transferred onto a set of nylon wheels running on the cables. The challenge here was that the cable clamps, which connect to the hangers that support the bridge deck, protruded above the cable. DLT’s innovation was to introduce small aluminium wedges that acted as ramps, allowing the nylon wheels to ride up and over the cable clamps. Each wedge had to be articulated and carefully contoured to transfer the weight smoothly.
Tandem lifting was another unique innovation. Each section of the deck was typically 24 metres long to match the spacing of the hangers and weighed up to 420 tonnes. Assembling deck sections in pairs on land beforehand, and then lifting them with two gantries, produced a considerable time saving. It also halved the number of interruptions to the shipping channel.
“I was delighted to see how easy and fast it was to move the gantries along the main cables,” says Mercedes, who visited the site to provide technical support for an especially complex ‘block lift’ near the towers, involving four gantries and three deck sections. She adds that according to the main contractor of the Nizhou Bridge, the time taken to relocate the gantry for each lift was reduced by about two-thirds, compared to traditional methods.
To maximise speed, DLSY used eight gantries, four for the main span and two each for the side spans. Placing each tandem deck took about 10 hours. In parallel, across the eight gantries, the team managed to execute up to four tandem lifts a day. In ideal conditions, DLT could have built all the standard deck units in less than four weeks.
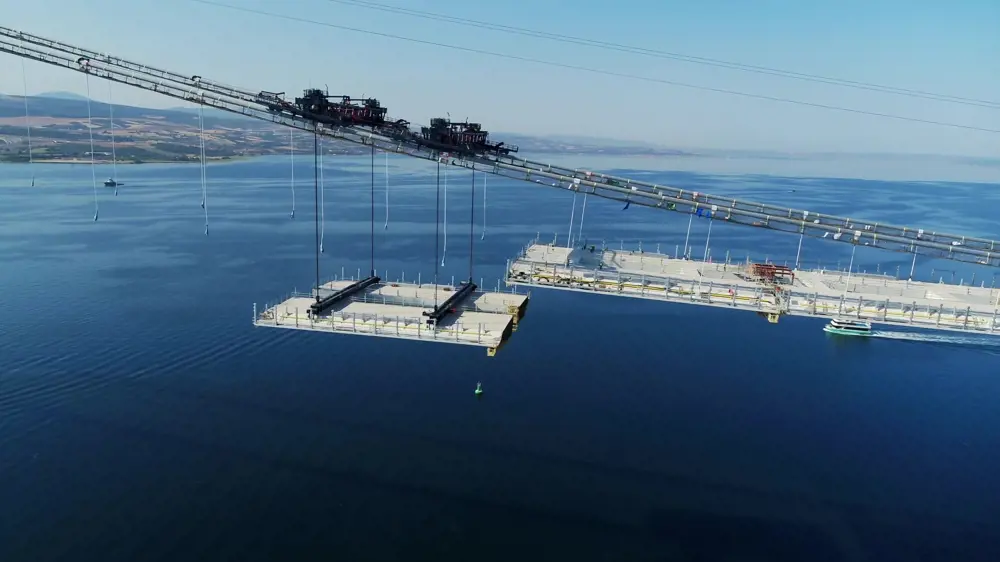
In reality, it took two months, because only two barges were available to deliver the units, and because of adverse weather. The gantries could operate in wind speeds of up to 20 metres per second, equivalent to a so-called ‘strong breeze’. “I can assure you, that feels very strong on the bridge catwalk, and not safe for workers to be operating there,” says Mercedes. However, conditions were frequently worse.
The sections of deck immediately beneath the towers presented an extra challenge, solved with a unique ‘block lift’, involving four lifting gantries, two either side of the tower. Here, the team was working with a 1,200-tonne block made up of three sections of deck. At this stage, the part-complete main span deck was continuously moving in the wind, so the team had to carefully synchronise the strand jacks, and only perform these lifts during periods with wind speeds slower than 10 metres per second.
“I was thrilled to see the bridge across the strait and our gantries in operation. They moved so smoothly,” says Mercedes. “I took so many videos and photos. It was one of the best moments of my career.”
Dismantling the gantries
With their work complete, the gantries self-dismantled. This involved a modified reversal of the self-erection sequence, where they were lowered to deck level near the towers and broken down. Then, the pieces were lowered through the gaps in the deck between carriageways onto barges for removal.
DLT won an innovation award for the Çanakkale gantries at last year’s British Construction Industry Awards. Earlier in 2023, the prototype Nizhou gantries were used to complete the deck of the ShenZhong suspension bridge, part of a 24-kilometre long crossing of China’s Pearl River now under construction. DLT Engineering is now hoping for a commission for its gantries on the forthcoming ShiZiYang suspension bridge, also on the Pearl River estuary.
This will create a new world-record span of 2,180 metres and will also be much heavier than Çanakkale, with twin decks each carrying eight lanes of traffic, and main cables more than 1.4 metres in diameter. However, this may yet be overtaken by the ZhangJinGao Yangtse River Bridge, where construction of tower foundations is already underway, with a 2,300-metre main span.
Long-span suspension bridges are getting longer.
DLT Engineering
A small engineering company with a history in iconic structures
DLT Engineering was founded in 2000 but can trace its links to historical companies formed in the 19th century. As such, the company has a long and distinguished history in the construction of landmark structures around the world, particularly iconic bridge works and building structures such as the Queensferry Crossing or the Wembley Stadium. Today, DLT Engineering is a private company, Chinese-owned but still with an engineering office in Darlington and head office in Higham Ferrers, England.
Hugh Ferguson would like to thank Mercedes Ascaso Til, Principal Engineer with DLT Engineering; Tina Vedrum, Senior Technical Director Transportation International at COWI and President of the International Association for Bridge and Structural Engineering (IABSE); and Richard Hornby, Long Span Bridge Lead at Arup who conducted independent design verification for the bridge, for their help in producing this article.
***
This article has been adapted from "Bridging the Eurasian gap", which originally appeared in the print edition of Ingenia 96 (September 2023).
Contributors
Mercedes Ascaso Til has over 20 years of experience in bridge engineering. In 2019, she received New Civil Engineer’s Technical Excellence Award. In 2022, the Women’s Engineering Society selected her as one of the Top 50 Women in Engineering: Inventors and Innovators. In addition, the gantries won the Innovation Product of Year Award at the British Construction Industry Awards 2022 and were shortlisted for the IStructE Awards 2022. Mercedes is passionate about music, theatre, philosophy, poetry, travelling, art, and much more.
Hugh Ferguson
Author
Keep up-to-date with Ingenia for free
SubscribeRelated content
Civil & structural
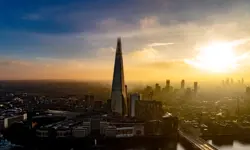
Building the Shard
The Shard is one of London's most iconic buildings. The tallest in Western Europe, it was designed by Italian architect Renzo Piano and dominates the city’s skyline. Ingenia spoke to John Parker, project director for structural engineers WSP, who outlined the engineering decisions made in building the enormous steel and glass structure.
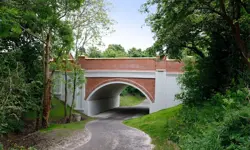
FlexiArch
Arch bridges are strong, durable and require little maintenance. However, very few had been built since the early 1900s until the FlexiArch was developed and launched in 2007. Now, there has been a minor renaissance for this ancient form of construction.
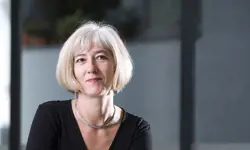
Creating user-friendly buildings
For Michelle McDowell, a former Business Woman of the Year, a passion for joined-up design thinking and building information modelling with a user-friendly approach has enabled her to pioneer revolutionary changes in her field.
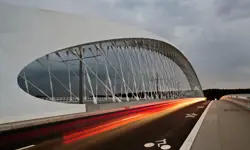
Troja Bridge
In November 2014, one of the world’s largest network arch bridges was officially opened in Prague. The UK may soon have its first network arch bridge if the go-ahead is given for a new rail project in Manchester.
Other content from Ingenia
Quick read
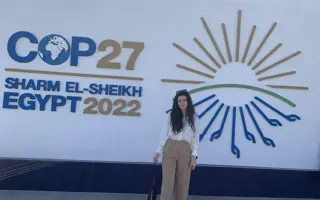
- Environment & sustainability
- Opinion
A young engineer’s perspective on the good, the bad and the ugly of COP27

- Environment & sustainability
- Issue 95
How do we pay for net zero technologies?
Quick read
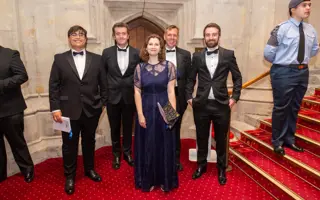
- Transport
- Mechanical
- How I got here
Electrifying trains and STEMAZING outreach
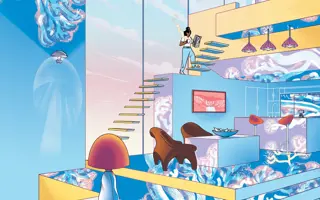
- Civil & structural
- Environment & sustainability
- Issue 95