Bringing cleaner seas to Sussex
A large civil engineering project on the south coast started off with passionate protests against it but has finished up with plaudits and awards. Richard Hodgson, Programme Manager, Southern Water, and Graham Sugrue, Project Director, 4Delivery, talked to Ingenia describing both the challenges of the build as well as detailing how a modern sewage treatment plant works.

Once Brighton and surrounding areas’ waste water has been collected and treated at the new Peacehaven water treatment facility, the cleaned wastewater is dispersed nearly 2km offshore. A tunnel was dug and constructed for the first 500m and then the remaining pipeline was laid in a trench. The outfall pipe tapers to 12 diffusers with concrete domes to protect them from possible damage
Five years ago, the site of the new wastewater treatment works at Peacehaven, about 15km east of Brighton, was a green field on coastal farmland at the edge of the South Downs National Park. The region relied on a sewerage network that dated principally from the Victorian era. It was the only area in Sussex, and among the last in Europe, that failed to meet European environmental standards on wastewater treatment.
Since then, a project team led by Southern Water, with project team 4Delivery and consultant Mott MacDonald, has sunk two new pumping stations and more than a dozen access shafts. It has driven more than 11km of new sewer tunnel, laid a new 2.5km outfall to carry cleaned wastewater into the English Channel and shifted more than one million cubic metres of earth at Peacehaven. That site now sits deep within the local topography, is covered by a vast grass roof and supports one of the most advanced wastewater treatment works to be built.
Recognition of these achievements has been widespread. The project has already won more than 20 professional accolades, including the Major Civil Engineering Project of the Year in the 2013 British Construction Industry Awards in which it was competing against The London 2012 Olympic Park Project. The project also collected the ICE’s Engineering Excellence Thomas Brassey 2013 Award and remains in the running for further recognition.
PLANNING CONSIDERATIONS
The contractor had to manage numerous sites engaged with tunnelling, shaft sinking, preparation for the sea outfall pipe and development of the land for the treatment works, which covered 39 hectares temporarily during the construction phase. There were 12 sites in all, and each was a major project in its own right.
One of the main reasons for choosing the Peacehaven site for the treatment works (from eight sites shortlisted for investigation, of 66 sites originally considered) was the existing gradient of Brighton’s Victorian sewerage network, which already gravity-fed wastewater eastwards, towards Peacehaven. The new network picked up the old one at Brighton Marina and, with the help of the two new pumping stations, continues to make the most of gravity to draw the flow to Peacehaven. Consequently, the tunnel has a saw-tooth profile in elevation; the flow is lifted at Brighton Marina and then runs downhill to Portobello, where it is lifted again and runs downhill to the site.

The base rock is chalk and, due to the topography of the land, the contractor tunnelled both through and above the water table in different locations at depths that varied from 8-40m below ground. There have been no subsidence problems for residents living above, with surveys of properties within the ‘zone of influence’ recorded before any work started. To achieve targets, miners worked underground for up to 12 hours a day, installing up to 37m of tunnel during each shift.
Four tunnelling machines worked simultaneously from Brighton Marina, where the new works meet the old Victorian system, to Friars Bay near Peacehaven, where the new works meet the new sea outfall. Local school children named these machines ‘Marina’, ‘Alice’, ‘Hollyblue’ and ‘Ava Frances’. ‘Marina’ connected a new chamber at Brighton Marina to a new pumping station at Marine Drive. ‘Alice’ tunnelled westwards from Ovingdean to Marine Drive and then eastwards from Ovingdean to Portobello, where there has been a treatment works (of sorts) since the 1870s. ‘Hollyblue’ tunnelled from the Peacehaven site to Portobello, where a new pumping station has now been built, and from the site to a shaft at Friars Bay. ‘Ava Frances’ bored its way at a maximum depth of around 45m depth from a shaft at Friars Bay 1km out to sea to a reception pit located at the start of the new long sea outfall.
The project required 18 shafts. The biggest were for the pumping stations, two along the sewer line at Marine Drive and at Portobello, and a third at the inlet chamber of the treatment works where pumps lift the flow so that it can be gravity-fed across the site. Other large shafts at Brighton Marina, Ovingdean and Friars Bay enabled the tunnelling machines to be lowered into the ground – and to be lifted out again. Smaller shafts provided access to the tunnels for maintenance and repairs and ultimately enabled connections to be made between the new sewer line and existing local networks.
Architecturally, the project team adopted contrasting styles to meet planning demands. The pumping station at Marine Drive has been designed as a landmark on the eastern gateway into Brighton; zinc plate covers its domed roof and its sweeping concrete walls are shaped to create the image of a fish in the midst of the coastal highway.
Meanwhile, the pumping station at Portobello is hidden below road level so as not to interrupt views out to sea from Telscombe Tye, an open area of ancient downland.
RAISING THE ROOF
In many ways, however, the most outstanding architectural feature of the project is the grass roof that covers much of the treatment works at Peacehaven. It shields the site from views across the South Downs – and has been designed to fulfil local planning stipulations to make the site as unobtrusive as possible. Defining the roof’s complex geometry demanded the creation of a wireframe CAD model, while the biggest factor influencing the roof’s structural design was the depth of the bedding substrate for the grass when wet.
Building the roof presented a new set of issues, with very little repetition of structural units across the entire 18,000m2 area. The basic structure consists of trusses supporting a network of purlins (horizontal supporting beams) that sit on stools whose heights are individually made to fit their specific locations on the roof; this was deemed to be the only way of ensuring that the curves remained true to the original mathematical model. Decking sheets on top provide the platform for layers of insulation, waterproofing, drainage, and root and vapour barriers that precede the turf and its thin substrate.
The seed mix for the green roof was chosen to reflect the neighbouring fields as was the turf. The grass was grown offsite for 15 months in a controlled environment and lifted 24 hours before installation to minimise the shock of transplantation. The grass covers an area of 18,000m2, or more than twice the area of an average Premiership football pitch, making it one of the largest green roofs in the UK.
PLAUDITS
In the face of considerable local opposition to the project, Southern Water and the construction teams engaged with the two planning authorities, local environmental health representatives and local residents. The plant now blends into the landscape, thanks to the green roof and to the extensive reprofiling and landscaping of the surrounding areas, in order to screen the works from view.

The pipe-jack tunnel boring machine ‘Ava Frances’ being lifted out of the water and loaded onto a lorry at Newhaven to be refurbished before going on to its next job. Ava Frances was lowered into an access shaft at Friars Bay and then dug its way 1km out to sea, towards a reception pit located at the start of the new long sea outfall. Giant inflatable buoys were used to lift the TBM onto a bespoke barge which took it to port
The Peacehaven scheme was named Major Civil Engineering Project of the Year at the British Construction Industry Awards 2013, beating other entries including the London 2012 Olympic Park Project. The four-year construction project has brought in two dozen more awards that recognise the scale and success of the project. Peacehaven has brought cleaner seas to Sussex and has, on the way, learned and shared lessons on public engagement that could be used on future sensitive construction projects.
PUBLIC ACCEPTANCE
Since the late 1990s, opposition from local planners and residents had stalled various attempts to modernise the network; the final scheme was dubbed ‘Poohaven’ and covered an area that encompassed two planning authorities, a district council, two town councils, two parish councils and numerous community groups.
Then, in May 2009, a judicial review collapsed. The review had been sought by local residents angered at the final granting of official planning consent, albeit with 87 conditions attached, including stringent limits on both noise and odour. But the residents ran out of money. Two months later, contractors moved in.
At the same time, the project team also went out of its way to support and engage with the local community. It established a liaison group and appointed a leading local protestor as its chair. It visited schools, distributed newsletters and funded local events and good causes.
The team encouraged the scheme to be used as a real-life STEM learning experience for students and promoted the findings of archaeologists who explored the site before construction work began and revealed evidence of human occupation dating back more than 5,000 years to the late Stone Age. It promised, at the end of the project, to return a third of the construction site to agriculture and lease another third to the local community as a much-needed sports park.
The team listened to concerns about traffic, noise and smells, and explained how they would deal with these issues. It invited tours of the site (2,000 people took up the offer during construction), played cricket against the local high school (and lost), knocked on doors and had tea with neighbours. The civil engineering contractor, 4Delivery (a joint venture of Veolia Water, Costain and MWH), engaged local young people as apprentices, 10 of whom moved into other jobs with the firm. And the £300 million project still came in on time and within budget – without a RIDDOR (reporting of injuries, diseases and dangerous occurrences regulations) after more than 3.5 million hours of activity from a workforce that topped 600 people at its peak.
HOW THE PEACEHAVEN TREATMENT CENTRE WORKS

The project’s main sewerage tunnel collects wastewater from a population of almost 300,000 people over a catchment area that stretches west from the treatment works at Peacehaven to the major coastal conurbation of Brighton and Hove. The flow arrives at a wet well, to one side of the works, where pumps lift the wastewater through 22 metres so that gravity can take over and pull the flow through the rest of the plant.
The first stage of preliminary treatment that wastewater arriving at the Peacehaven treatment centre goes through is the screening. This is a mechanical process that feeds the water through a narrowing aperture. These 6mm screens remove solid objects like cans, rags, plastic bags and nappies. This refuse is then washed, drained, compacted and taken away.

Water flow in this primary stage of the treatment process rises gently through an array of thin,plastic honeycombs, known as lamella settlers. Gradually, thin films of toxic sludge accumulate on the honeycombs’ surfaces. As the sludge settles, tiny bubbles stream up through the honeycombs to agitate the sludge and help it to slide off the surfaces, and to sink to the bottom of the cell. A stirrer then guides the sludge into a conical sump from where it is transferred into a sludge-holding tank
At this final stage of the second primary treatment process, the wastewater is distributed equally among 10 flooded cells. These are supplied with air from compressors which flows upwards in each cell through several metres of tiny, densely packed polystyrene beads. A perforated concrete slab contains the three-dimensional lattice of beads. but nozzles in the slab allow water and air to pass. Water emerging from the cells is then clean enough to leave the Peacehaven site via the sea outfall
The waste water continues through to the fats, oils, grit and grease (FOGG) channel. The flow slows as it passes through three enclosed channels and air bubbles up through the waste water. This encourages a concentrated fatty scum to collect on the surface and grit to settle at the bottom. The scum is scraped off, drained and transferred to the anaerobic digesters further along the works. The grit is then collected with Archimedean Screws and placed into skips for transfer to dedicated contamination landfill sites.
The next stage is a settlement process that forms part of the primary treatment and removes sludge from the wastewater. On this site, a lamella (filtration membrane) is used where ferric and polymer chemicals are added to the waste water to assist in separating the solid waste from the waste water. In the primary treatment process, the waste water is split equally into four lamella cells. Each cell is made up of a series of thin plastic honeycombs, which increase the settling area. The solids settle first on the honeycomb and then are agitated off by bubbles before sliding down the 60° sloped surfaces to the bottom of the cell.
The sludge is continuously removed and goes to co-settlement tanks before it is thickened and placed in digester tanks. There it is kept for two weeks where it is heated to 37° C and broken down by anaerobic reaction. Once the sludge has been digested, more water is removed in a centrifuge before it goes into the drier. The drier, operating up to 600° C, removes 95% of the remaining water. The solid granules produced by the drier are then used in agriculture as a soil conditioner.
During the sludge treatment, gas is produced at different stages of the process. The methane is collected and through the combined heat and power (CHP) plant is converted into electricity, which is used onsite. The heat recovered from cooling the CHP is used to heat the anaerobic digesters.
Once the waste water has been through the lamella it goes on to the final stage of the treatment at this site. This stage uses aerobic bacteria, present in the waste water, to break down the remaining solids, based on what is known as biological aerated flooded filter (BAFF) technology. On entering the BAFF, the waste water is split equally into 10 separate cells, where air is added. The water passes through a layer of polystyrene balls, which are home to microorganisms.
The beads provide a huge surface area on which the bacteria can grow, digesting the nutrients and oxygen supplied by the wastewater and air as they flow through. The polystyrene media in each of these cells is regularly cleaned through a back-wash process.
Once the waste water has been through this final process, it heads off towards Friar’s Bay and the new long-sea outfall. This outfall has been constructed under the seabed 2.5km offshore. At the end of the outfall are a number of diffusers, used to disperse the waste water over a wider area.
A video of this process can be found at tinyurl.com/mxyuo9k
Ingenia also talked to Robin Woodward, Project Manager, Southern Water and Madeline Stoneman, Southern Water's Public Relations Manager.
Keep up-to-date with Ingenia for free
SubscribeOther content from Ingenia
Quick read
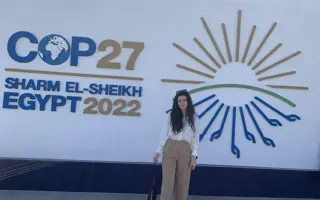
- Environment & sustainability
- Opinion
A young engineer’s perspective on the good, the bad and the ugly of COP27

- Environment & sustainability
- Issue 95
How do we pay for net zero technologies?
Quick read
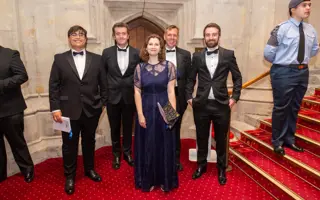
- Transport
- Mechanical
- How I got here
Electrifying trains and STEMAZING outreach
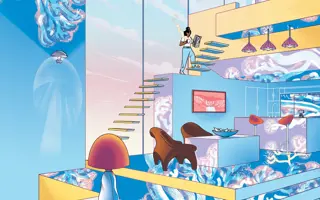
- Civil & structural
- Environment & sustainability
- Issue 95