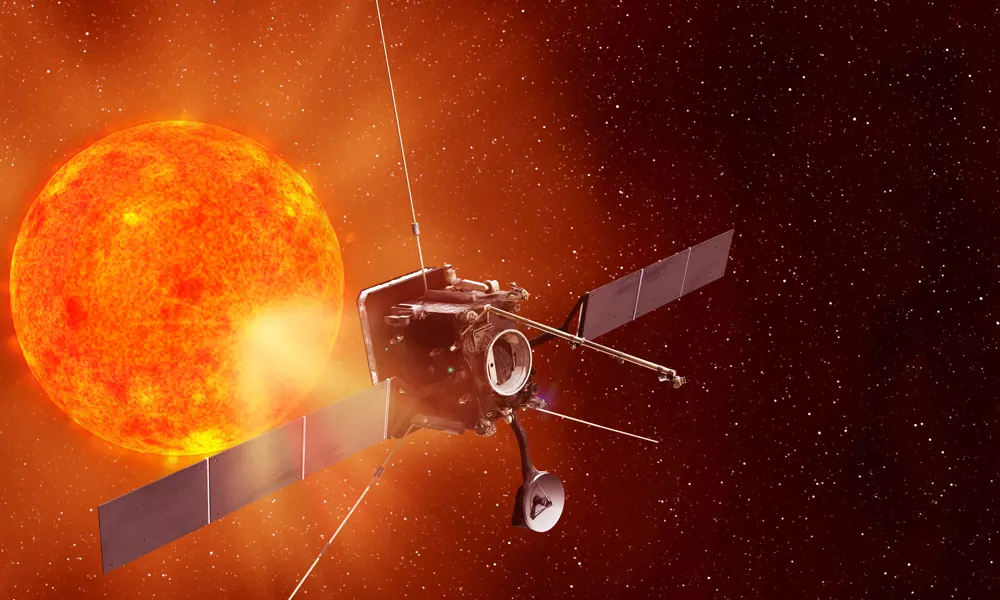
Flying close to the sun
“The Solar Orbiter is one of the most complicated spacecraft we have ever built,” said Ian Walters during a telephone call from Florida, where he and his team spent months ahead of the craft’s successful NASA launch on 10 February 2020. “We have built many scientific satellites for the European Space Agency (ESA) in the past but most of them only had one instrument. Here we have 10 main instrument packages, each containing many sub-instruments; more than 30 instruments altogether, and many of them have conflicting requirements.”
Airbus designed and built the 15-cubic metre probe for ESA at its UK facilities in Stevenage. The craft left the UK for Germany in September 2018 to undergo an extensive testing campaign at the IABG facility near Munich before it was shipped to the US in October 2019. Launched from NASA’s Cape Canaveral base, the probe will swing twice past Venus and once past Earth, using their gravities so that it can approach the Sun in 2022 at the right angle to best view its poles.
The Solar Orbiter will need to withstand these highly- charged electron and proton particles as well as temperatures up to 600°C and sunlight 13 times brighter than the levels experienced on Earth
The Solar Orbiter will travel around the star in an elliptical orbit. At its closest, it will observe the Sun from a distance of about 42 million kilometres, about a quarter of the distance between the Sun and Earth. With the exception of NASA’s Parker Solar Probe, which carries a simpler set of instruments and doesn’t have any telescopes to look directly at the Sun’s surface, no satellite before has been so close.
This will enable the spacecraft’s telescopes to see some of the never before imaged regions of the Sun, such as the north and south poles. Analysis of the star’s polar regions will enable a better understanding of the Sun’s magnetic field, which drives the powerful ejections of solar plasma that generate solar wind.
Geomagnetic storms caused by solar wind frequently disrupt the signals of navigation satellites, such as GPS, and could even knock out power grids on the ground and affect telecommunication networks. The Solar Orbiter will need to withstand these highly- charged electron and proton particles as well as temperatures up to 600°C and sunlight 13 times brighter than the levels experienced on Earth.
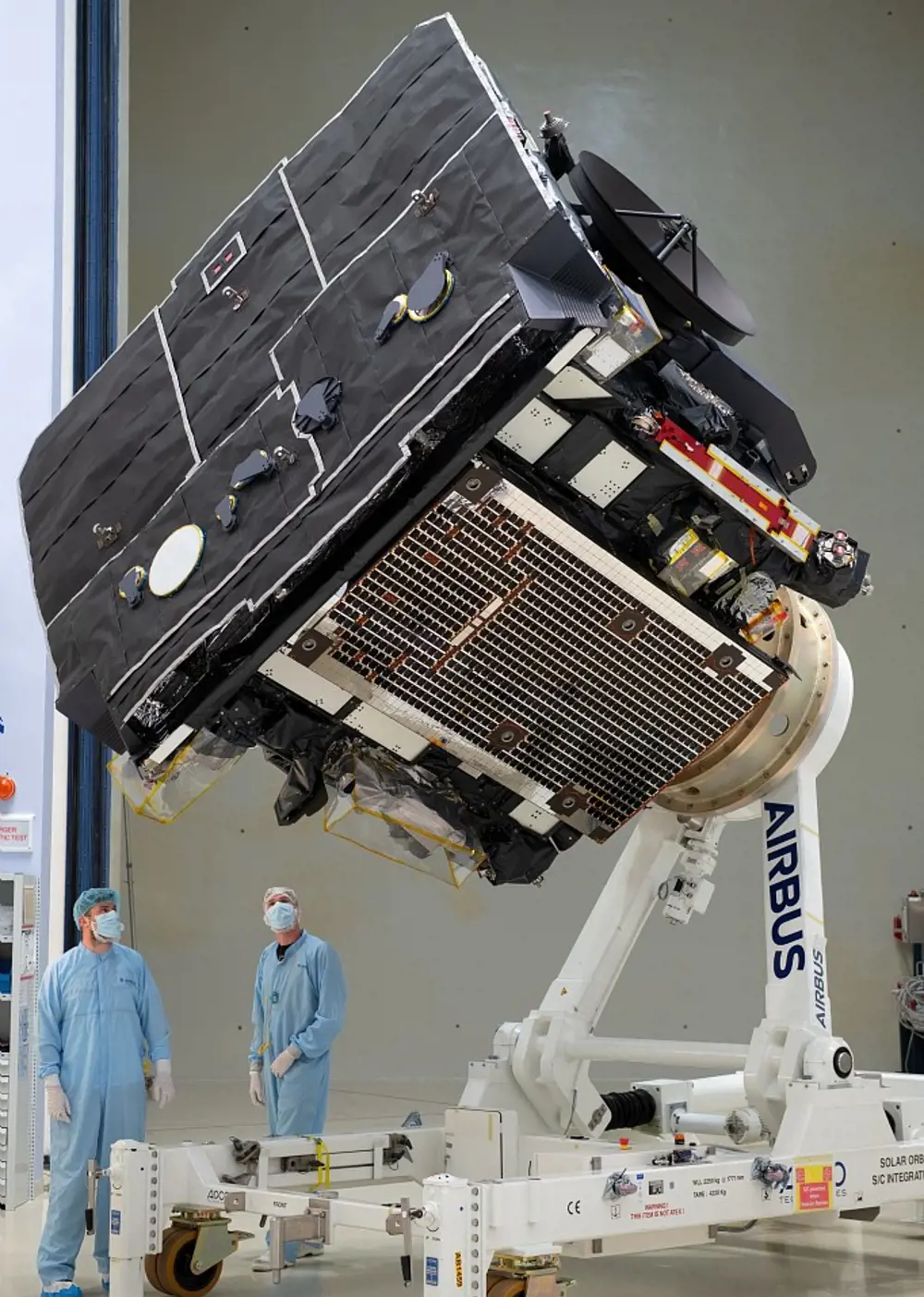
In October 2019, the Solar Orbiter had undergone a year’s worth of tests near Munich. It is seen here being packaged up to be flown to NASA in Florida. The heat shield is shown on the left of the probe pointing upwards © ESA – S Corvaja
Developing a sunshield
Ensuring that the spacecraft and its instruments survive in this extreme environment for at least seven years was the main challenge faced by the engineers. The team could partly reuse some of the technologies developed for ESA’s Bepi Colombo mission, which is currently on its way to Mercury, the planet closest to the Sun.
The Solar Orbiter, however, will get closer to the Sun than Mercury and therefore face even harsher conditions including extreme heat and cold. “However, the spacecraft will be hiding behind a sunshield,” explained Walters. “That means that we don’t need to design every item of the spacecraft to work at 600°C. The heat shield absorbs and re-emits the heat and behind that the spacecraft is relatively normal.”
In the vacuum of space, heat can only be transferred by radiation, or by conduction between objects that are in contact with each other. The shield was therefore designed to restrict all conductive paths and radiate all the heat it absorbs to the sides rather than into the spacecraft.
The outer layer of the 3.1 by 2.4 metre-wide, 30 centimetre-thick shield consists of 40 thin layers of titanium foil, which can withstand temperatures of up to 600°C. Behind this sandwich structure is a gap that guides any heat that has made it through sideways and away from the satellite.
Behind the divide, attached by 10 star-shaped brackets, is the base of the shield, made of a five centimetre-thick aluminium honeycomb structure covered with 30 layers of insulation. This layer can withstand temperatures of up to 300°C with 10 1.5 millimetre-thin blades attaching the shield to the main spacecraft.
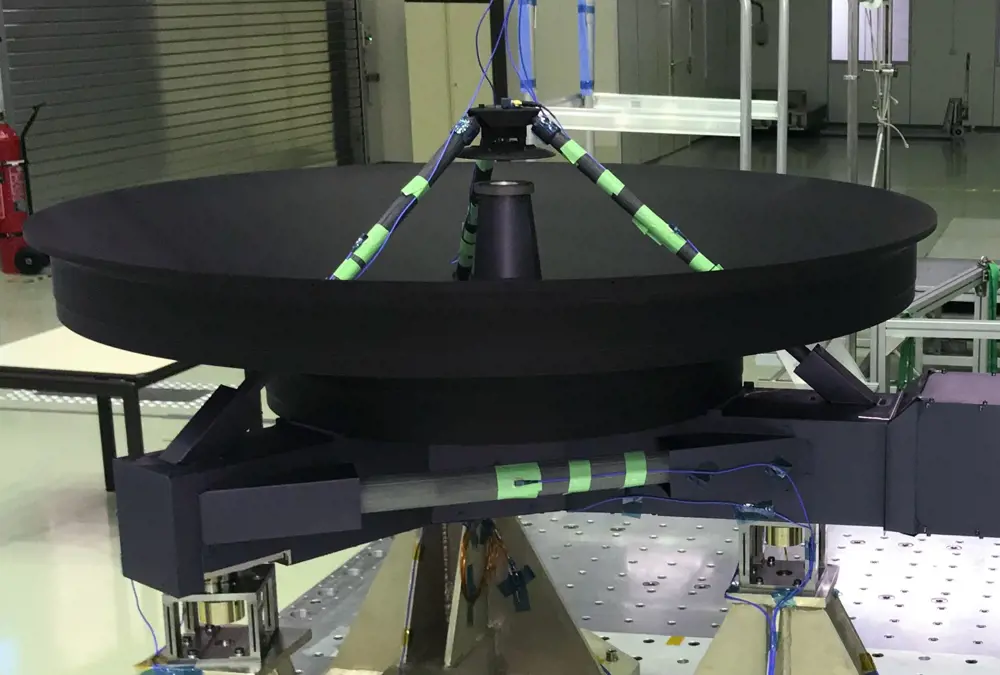
The high-gain antenna, coated in ENBIO’s SolarBlack, during vibration testing at ESA’s technical centre in the Netherlands © ESA/ATG medialab
How a SolarBlack coating enables a close approach to the sun
However, the key technology that enables such a close approach to the Sun is the coating on the outermost layer of the shield that directly faces the star. Called SolarBlack and developed by the Irish company ENBIO, the coating, according to Walters, is the blackest material ever flown in space and will remain as black as at the beginning of the mission, even after years in the extreme environment.
The blackness ensures that the shield radiates the heat it absorbs back into space in the most efficient way and will remain doing so after years of use. “People find it a little bit weird because black is hot on Earth,” said Walters. “But if you put it in the heat, it absorbs heat fast, while also emitting it fast, so it actually gets a bit colder than if it were white.” SolarBlack absorbs sunlight, converts it into infrared energy then radiates it back to space in the form of heat.
When choosing the right material for the task, it was important to ensure that it would not shed any material or release gases while in the extreme environment. In addition, the skin had to be electrically conductive in order not to create static charge, which could damage the spacecraft and disrupt measurements.
The engineers considered carbon-fibre fabrics but they did not meet requirements. Instead, animal bones were used. These were burned, ground into a powder and then blasted onto the surface.
ENBIO developed the blasting process, called CoBlast, which uses two types of material simultaneously blasted onto the surface through a single nozzle. An abrasive element removes the natural protective barrier on the surface and exposes an active chemical bond to which the coating powders attach before an oxide layer forms on the surface. The abrasive element is completely inert and does not bond to the surface.
The engineers used the same material to coat the Solar Orbiter’s high-gain antenna, a two metre diameter satellite dish that sticks up from behind the spacecraft into the bright sunlight and sends terabytes of scientific data to the Earth in a highly concentrated radio-frequency beam. The antenna generates a very fine beam, less than two degrees wide, to avoid any thermal distortion, which could disrupt the signal. The SolarBlack coating ensures that the antenna does not distort from the heat.
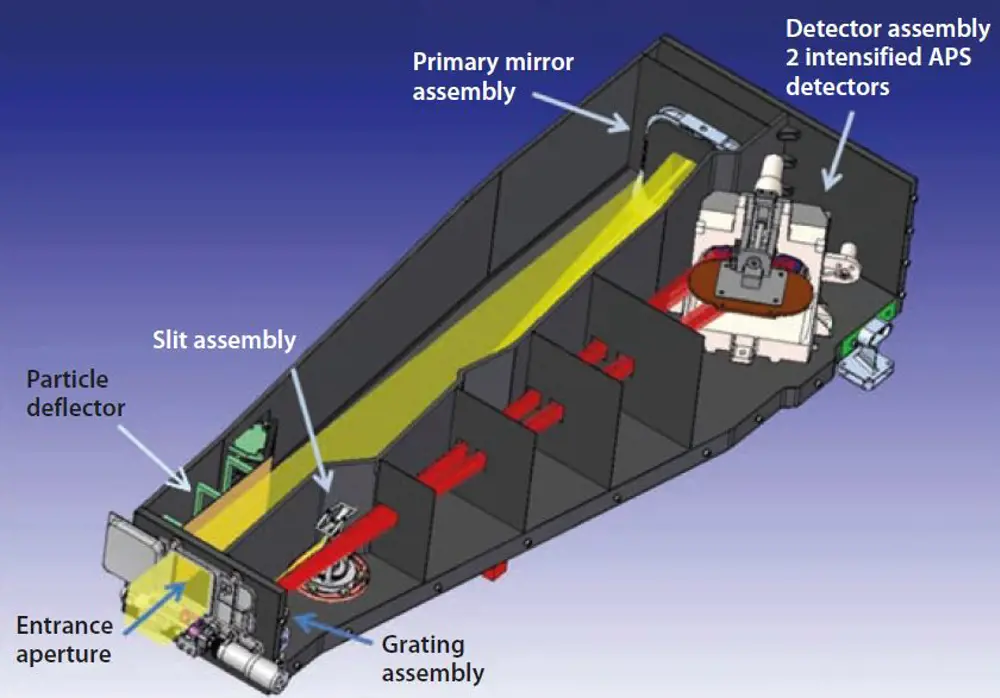
SPICE instrument optical layout. The off-axis parabola mirror forms an image of the Sun onto the entrance slit assembly containing four interchangeable slits of differing widths. The slit selects a portion of the solar image and passes it to a concave toroidal variable line spaced grating that re-images the spectrally dispersed radiation onto two array detectors © STFC RAL Space
Examining the coronal environment
The Solar Orbiter carries two types of instruments. The in-situ instruments measure properties of the environment in the vicinity of the spacecraft and are mounted on a 4.4 metre boom at the back of the spacecraft. There are also remote-sensing instruments, various types of imagers and telescopes to photograph the Sun at different wavelengths, which need to look directly at the star. To enable that, the engineers cut tiny windows into Solar Orbiter’s heatshield, which open at specific times for the observations. This approach prevents too much heat from leaking into the spacecraft through the instruments’ feedthroughs.
SPICE (the initialisation of ‘Spectral investigation of the coronal environment’), is one of these remote-sensing instruments. Built by an international consortium led by RAL Space, part of the UK Science and Technology Facilities Council, SPICE takes images of the Sun in the extreme ultraviolet part of the solar spectrum. It will study the temperature and velocities of the solar plasma, which gives rise to solar wind, according to Martin Caldwell, who served as the SPICE Systems Engineer at RAL Space.
The instrument is similar to other extreme ultraviolet spectrometers used previously on Sun-observing missions in the orbit around the Earth. SPICE though, had to fit into a much smaller envelope than had been used before, deal with the extreme amount of light and heat entering the instrument, and cool the spectrometer’s detectors to -20°C to ensure accurate measurements.
“With the previous instruments, we only had to solve the optical design,” said Caldwell. “But in this case, the optics wouldn’t work without a very good thermal design. Also, although we might have a lot of light coming into the instrument, most of it is in the visible and infrared part of the spectrum, which not only has a heating effect, but is of no use to us.”
As light enters the one-metre long instrument, it first encounters a particle deflector, a high-voltage plate that diverts the particles of the solar wind and prevents them from hitting a mirror at the end of the channel. The mirror is coated with thin boron carbide, which reflects only the extreme ultraviolet part of the spectrum into a detector compartment. The rest of the incoming energy passes through the mirror and is then sent back out into space. If the particles were not deflected and hit the mirror they would destroy the boron carbide filter within a few months.
SORA
🛰️ How a Solar Orbiter technology protects against vibrations and removes excess heat
The Stood-Off Radiator Assembly, or SORA, is one of the technologies designed specifically for Solar Orbiter. It consists of a set of aluminium radiators attached to the sides of the spacecraft.
The radiators are connected to the instrument detectors with flexible cold straps, which are each 30 centimetres long and made of pyrolytic graphite, a highly conductive material consisting of layers of carbon.
These pyrolytic graphite layers are as thin as a sheet of paper and are banded together, 70 at a time, into a flexible scheme. The material is five times more thermally conductive than copper and extremely flexible. The flexibility is important because everything stretches under the heat load and also everything vibrates during the launch.
The flexibility ensures that the straps do not transmit any vibration to the sensitive instruments from the radiators, which have to be mounted away from the spacecraft on special thermally isolating mounts.
Through the cold straps, all the excess heat from inside the instrument is radiated into space. Thanks to this technology, the SPICE detectors, for example, reach the desired temperature of -20°C, at which they are most sensitive and effective.
Achieving the below zero cooling required
With the unwanted part of the solar spectrum out of the way, the engineers focused on optimising the measurements of the small amount of the extreme ultraviolet light. The instrument uses a two-stage detector, a UV image-intensifier plus a silicon micro electronic array, based on technology commonly used to produce integrated circuits, a complementary metal oxide semiconductor (CMOS). However, these circuits have a thermal background electric current that would interfere with the measurements. The intensity of this current drops with temperature and cooling down to -20°C is required to eliminate the problem.
“The front of the SPICE instrument behind the heatshield is about 120°C,” said Caldwell. “At the end of the instrument, where the detector box is, it might be about 50°C. The detector box, which is about half the size of a shoe box, includes careful thermal-isolation, such as non-conductive materials to prevent the heat from seeping in. But that by itself wouldn’t be enough.”
The spacecraft engineers found a way to radiate all the excess heat out of the sides of the spacecraft that are permanently in the shadow of the shield and as cold as -200°C. The two silicon detectors, which are each only about 1.5 centimetres in size, are connected by what the engineers call a cold strap to a radiator on the shielded side – see SORA.
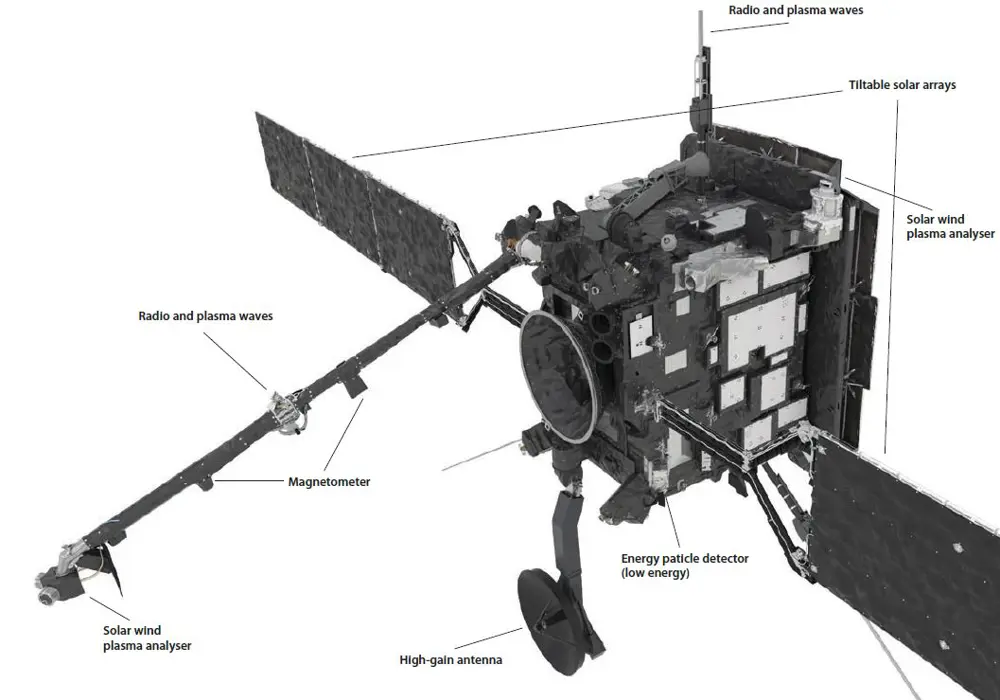
An artist’s impression of Solar Orbiter with some of its instruments and operating systems © ESA/ATG medialab
Instruments with UK input
☀️ Solar Orbiter instruments to measure extreme ultraviolet, the sun's magnetic field and solar wind.
In addition to SPICE, Solar Orbiter carries three other instruments that have been built in cooperation with UK scientists and engineers. The extreme ultraviolet imager (EUI) is another remote-sensing instrument that takes images of the Sun in extreme ultraviolet. It consists of three telescopes; one dual-band full Sun-imager and two high resolution imagers, each operating on different wavelengths. The EUI will observe and analyse the global morphology and local dynamics of the solar atmosphere, in particular at the base of the corona.
The other two instruments measure the environment directly around the spacecraft. The magnetometer measures the magnetic field in the Sun’s heliosphere. It is made up of two three-axis fluxgate sensors mounted on a boom in the spacecraft’s shadow. Because of the magnetometer’s sensitivity, the engineers had to ensure that the entire spacecraft is completely non-magnetic so as not to interfere with the measurements.
The other in situ instrument is the Solar Wind Plasma Analyser, created by a team led by UCL’s Mullard Space Science Laboratory. This will provide measurements of the ion composition of the solar wind as it changes throughout the orbit, measuring its speed, density and composition. It will do this through three sensors and a data processing unit onboard. The electron analyser system will track solar wind electrons to determine the nature of the magnetic field. The proton-alpha system will define the state of the solar wind itself (such as whether it is fast or slow). Finally, the heavy ion sensor will provide the connection to spectroscopic remote-sensing measurements, thereby providing a means to identify the solar source regions of the ambient solar wind passing the spacecraft.
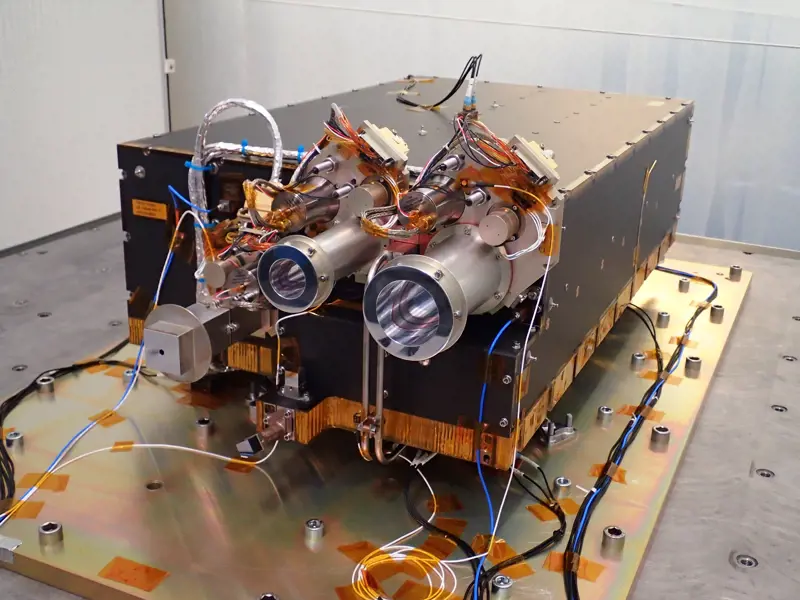
The fully integrated flight unit of the EUI instrument panel © Centre Spatial de Liège
Intelligent solar arrays to prevent overheating
The Solar Orbiter’s solar arrays presented another engineering challenge. The cells wouldn’t survive the high temperatures close to the Sun and therefore have to be tilted flexibly as the spacecraft follows its elliptical orbit. The spacecraft’s distance from the Sun can vary by 78 million kilometres, depending on where it is in the orbit. If the solar arrays were pointed towards the Sun perpendicularly, the temperature at the closest point would far exceed 300°C, the maximum at which the cells work efficiently. Over the planned 10-year mission span, the solar array will undergo about 20 hot-cold cycles, which, according to Walters, erodes them more than if they were constantly hot, as in the case of the Mercury probe Bepi Colombo.
“When we are very close, at 42 million kilometres, the solar array gets tilted 78 degrees away from the Sun, so that it’s almost edge on,” said Walters. “Otherwise it would get too hot and that would cause a lot of problems – the glues would stop being glues and the solar cells could detach, bend or distort. They would deteriorate rapidly; we would lose power and that would be mission-over.”
The spacecraft runs advanced software to control the solar arrays. Fault Detection Isolation and Recovery detects faults and ensures that the temperature stays within the required limits. Since the spacecraft spends up to three months out of sight of the ground control stations, the software has to operate autonomously.
The Solar Orbiter will reach operational orbit in just under two years after launch, when it will be close enough to observe the solar surface features. The probe will train its telescopes on the surface of the Sun, revealing details on areas 70 kilometres wide. The instruments will sense the constant flux of charged particles, which engineers hope will help explain the mechanisms that are producing the magnetic fields. It could also determine what causes the huge solar explosions that have the potential to disrupt the space infrastructure orbiting the Earth. This tracking of ‘solar weather’ could be crucial both for future lunar explorers and those going to Mars.
***
Since the writing of this article, the Solar Orbiter has lived up to its expectations of providing unprecedented scientific insight into the sun’s atmosphere.
This article has been adapted from "Flying close to the sun", which originally appeared in the print edition of Ingenia 82 (March 2020).
Contributors
Tereza Pultarova
Author
Ian Walters is a Senior Project Management Consultant for Airbus Defence and Space, as well as a Member of the Board of Directors for Gentian Ltd. He has a 39-year heritage in designing and project managing complex spacecraft, especially interplanetary and scientific missions. At the time of publishing, he was the Solar Orbiter Project Manager at Airbus Defence and Space.
Keep up-to-date with Ingenia for free
SubscribeRelated content
Aerospace
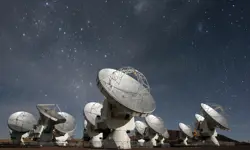
ALMA – the high altitude observatory
The Atacama Large Millimetre/submillimetre Array (ALMA) is the largest and most expensive ground-based telescope built, revolutionising our understanding of stars and planetary systems. Building it in the Atacama Desert in Chile required the ingenuity of hundreds of engineers.
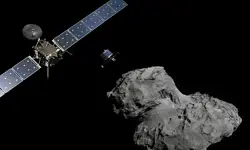
Communicating with outer space
The Royal Academy of Engineering awarded a team at BAE Systems the Major Project Award in June 2016 for their development of a powerful satellite modem system, pivotal in enabling the precise control of the pioneering Rosetta spacecraft and the first-ever soft landing of a spacecraft on a comet.
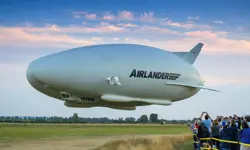
An aircraft like no other
The Airlander made headlines when it embarked on its first test flight in August 2016 as the world’s largest aircraft. Chris Daniels at Hybrid Air Vehicles Limited, and David Burns, Airlander’s Chief Test Pilot, talk about the engineering that helped it reach this stage and plans for the craft’s future.
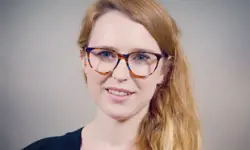
Q&A: Lucy Harden
Lucy Harden is a mechanical engineer on BAE Systems’ Digital Light Engine Head-Up Display development programme. She devises innovative solutions for pilots to display essential flight information that sits directly in their line of sight and is overlaid onto the real world.
Other content from Ingenia
Quick read
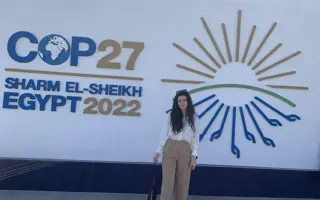
- Environment & sustainability
- Opinion
A young engineer’s perspective on the good, the bad and the ugly of COP27

- Environment & sustainability
- Issue 95
How do we pay for net zero technologies?
Quick read
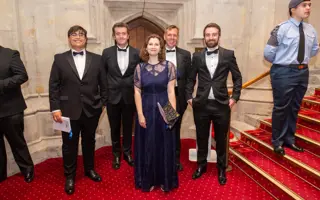
- Transport
- Mechanical
- How I got here
Electrifying trains and STEMAZING outreach
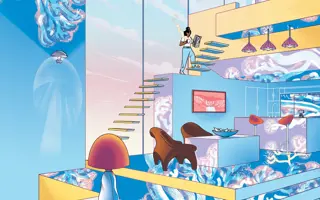
- Civil & structural
- Environment & sustainability
- Issue 95