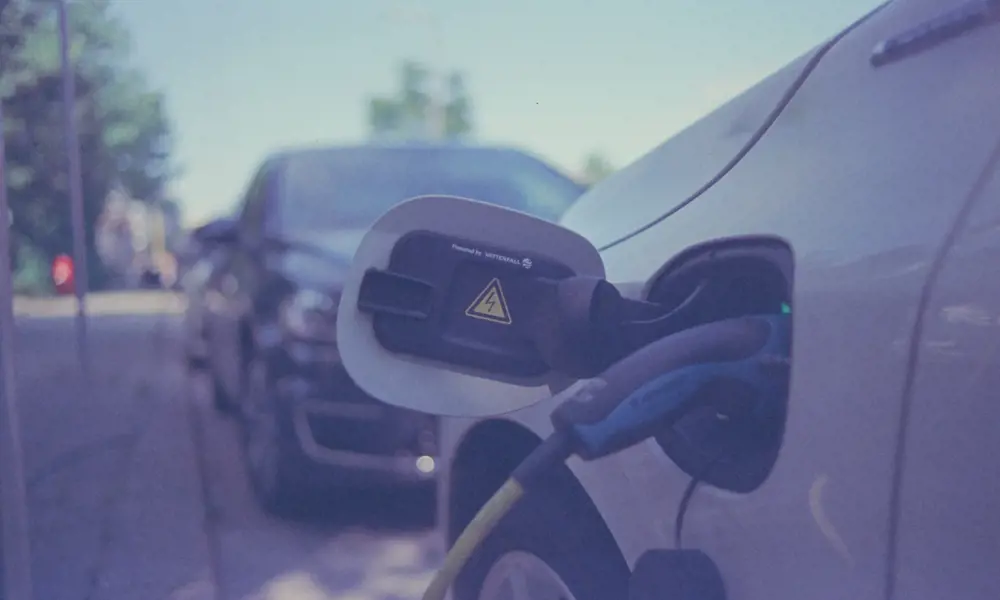
Powering the pursuit of net zero
Did you know?
🔋 Broaden your battery knowledge
- Li-ion batteries are used in almost all your rechargeable gadgets
- It is expected that more than 1 TWh (Terawatt-hour) of batteries will be manufactured in 2023 – enough to power more than 14 million electric vehicles or over 80 billion smartphones
- The Li-ion battery stores almost 10 times the amount of energy per unit weight compared to lead-acid batteries
Lithium-ion (Li-ion) batteries are one of the modern world’s most transformative technologies. These are the types of rechargeable batteries you might have in your smartphone, laptop or games console.
In the 20th century they revolutionised mobile computing and consumer electronics, and now promise to have even more significant impact. From decarbonising road transport to electrifying flight, batteries that range from tiny cells to power implanted devices to very large grid-scale storage will be used in a vast array of applications and will be a cornerstone in achieving net zero.
Battery is the generic term for the storage unit consisting of cells, the electrochemical units that convert chemical energy to electrical energy. In the simplest form, cells are assembled from three components: a positive electrode, a negative electrode and an electrolyte.

A schematic diagram showing the operation of Li-ion batteries during charge and discharge. During charge, the Li-ions move through the electrolyte from the positive to the negative electrode, and during discharge this process is reversed © Alamy
Batteries are generally categorised as primary (non-rechargeable) and secondary (rechargeable) cells. When a Li-ion battery is charging, lithium ions from the positive electrode move through the electrolyte (generally an ionically conducting liquid) to the negative electrode. When the battery supplies power, lithium ions move back to the positive electrode. In both cases, electrons flow around an external circuit to balance the charge.
The electrolyte conducts Li+ ions, but is an electrical insulator (it does not conduct electrons) so electric current doesn’t flow freely through it, and alongside a physical separator material, it prevents the cell from short-circuiting. A rechargeable battery’s ability to undergo reversible charge and discharge cycling over hundreds or thousands of cycles without substantial degradation is a critical indicator of its performance.
Li-ion batteries have achieved market dominance thanks to their high energy density (the amount of energy they provide), which is determined by the capacity of the constituent materials and the voltage during discharge. Practical energy density can be reported by unit weight (gravimetric energy density) or volume (volumetric energy density). Both of these must also consider the other components in the cell, for example the packaging, separator material, current collectors, and safety hardware, which all add extra weight or volume, therefore reducing the overall energy density at cell level.
State-of-the-art Li-ion batteries used in cars typically achieve about 250 Wh/kg (watt-hours per kilogram) and 700 Wh/l (per litre). The range covered depends on the make and model of car. For example, the Nissan Leaf – the UK’s bestselling electric vehicle (EV) at the end of 2020 – is expected to travel 168 miles (270 kilometres) with a 39 kWh battery. However, with increasing demand for advanced batteries in more and more applications, researchers across the world have been searching for ways to improve energy density in Li-ion batteries and in the development of next-generation batteries.
Developing the Li-ion battery
Chemist Gilbert N Lewis first identified the opportunity to exploit lithium as an electrode in an electrochemical cell more than a century ago. Lithium is the lowest density metal and also has the lowest standard reduction potential. This combination makes it an ideal candidate for a lightweight battery. However, development of the Li-ion battery didn’t begin in earnest until the 1970s. In 2019, US physicist Professor John Goodenough, British-US chemist Professor Stanley Whittingham and Japanese chemist Professor Akira Yoshino were awarded the Nobel Prize in Chemistry for their collective achievements that led to the development of Li-ion batteries in the 70s and 80s.
Li-ion batteries were commercialised in the early 1990s, and since then there have been improvements in safety, cost and performance. Development of cathode chemistries has provided more sustainable options (primarily a reduction in the use of cobalt); improvements in electrode formulation and cell design have enhanced practical energy density; and manufacturing scale up and automation have substantially reduced costs.
The cost advantages in battery manufacturing have led to the establishment of many ‘gigafactories’ (generally considered to be a battery production facility capable of >1GWh of annual output). These cost reductions are the result of an increase in highly automated manufacturing processes and standardised form factors for cylindrical, pouch and prismatic cells. As understanding and scrutiny of batteries’ lifecycles increase, the need to significantly improve the ‘embedded carbon’ in battery manufacture to minimise its environmental impact also grows. This can be achieved through areas such responsible materials supply and recycling, reduction of process energy use and improvements to manufacturing yield. In the EV sector, the lifecycle assessment (LCA) of a vehicle is also naturally connected with the supply of electricity, and simultaneous decarbonisation of electricity supply is required to maximise environmental benefits.
Addressing challenges
Despite progress in Li-ion battery design, there is still room for improvement. There is also substantial consumer demand for high-performance batteries in a range of increasingly challenging applications; for example, in the automotive sector, drivers want to charge their cars quickly, but also have extended driving ranges to overcome range anxiety. So, engineers are looking to design batteries that can store more energy and deliver it quickly.
A battery’s power capability is measured by ‘C-rate’: 1C is the equivalent of charging/discharging a battery to its full capacity over one hour, while a rate of 10C is equivalent to dispatching the same capacity in six minutes. In the EV sector, the ability to charge at high C-rates provides an opportunity to ‘refuel’ cars in an acceptable time (compared to expectations built by the time it takes to refuel a combustion engine vehicle), and during discharge provides an opportunity to match, or exceed, the performance of conventional vehicles. The amount of energy stored in a battery is generally determined by how much material is present in the active electrodes within a cell (which are those that participate in the chemical reaction). By contrast, the power density is generally determined by the electrical and ionic conductivities of an electrode. This means that, when developing a battery, engineers must carefully address competing requirements for energy and power density so that a cell can be tailored to its use: a high-energy cell requires low porosity electrodes with a high packing density of active materials, while a high-power cell favours thinner electrodes with high porosity and high conductivity.
Engineers must also consider the balance of volumetric and gravimetric energy (and power) density. In consumer electronics and passenger vehicles, batteries that can store the maximum energy per unit volume have been carefully optimised over many years (enhancing volumetric energy density). However, with growing uses in the aviation sector an emerging challenge is to make lightweight batteries (with enhanced gravimetric energy density).
Academic and industrial engineers are also carrying out substantial research into battery degradation. While recent research has promised a ‘million-mile battery’, current technologies usually do not come close to achieving this. A critical measure of degradation is the capacity fade (capacity loss over time) and in general a battery in an EV is deemed to have reached end of life once this falls to 80% of the original rated capacity. This occurs alongside power fade, which impacts a vehicle’s ability to charge/discharge at a high rate and is considered to be of equal (or perhaps greater) importance by the automotive industry.
Extending a battery’s lifetime before these critical thresholds are crossed is central to minimising a battery’s lifetime cost and providing confidence to adequately warranty batteries in service. Many processes impact battery lifetime, including the operational voltage limits, maximum charge and discharge current, and temperature. All of these variables are monitored and controlled by a vehicle’s battery management system (BMS), and for lifetime and safety reasons, the BMS often applies a conservative control strategy, which can limit the battery performance.
Which countries are manufacturing the most batteries?
We need gigafactories in the UK and Europe.
As demand for battery manufacture grows, and governments recognise the need for domestic manufacture (in particular to support the automotive sector), the geography of battery manufacture has diversified. While China retains the largest battery manufacturing capability, projected growth of gigafactories in Europe is also increasing significantly, as demonstrated in the figure above. In the UK alone, the potential domestic demand equates to approximately 10 gigafactories by 2040, according to research from the Faraday Institution. Manufacture of this magnitude is needed to keep prices competitive.
However, there are growing imperatives for security of supply and decarbonisation of the battery manufacturing sector. In Europe, this has led to the integration of manufacturing with clean energy supply: recent estimates reveal that in manufacture up to 65 kWh of energy input are required per kWh of battery produced. Ambitious sustainability targets could also lead to improved manufacturing yield and a requirement for improved process monitoring and quality control.
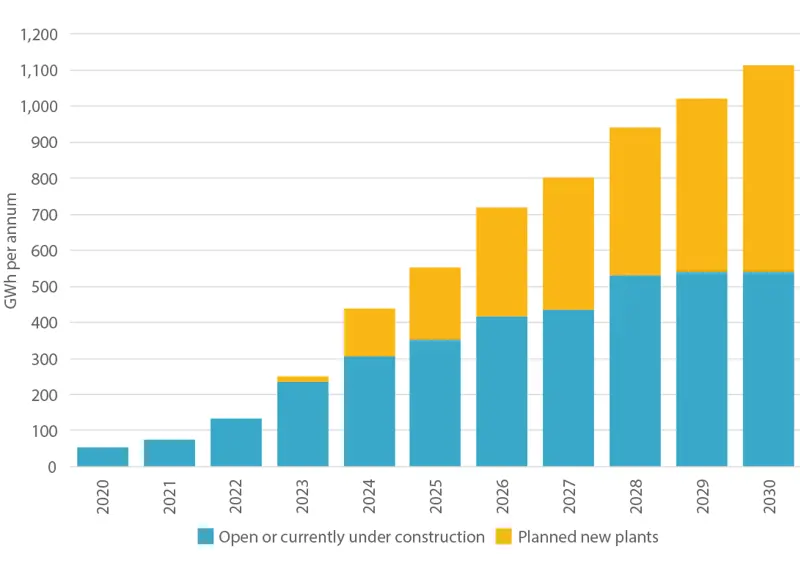
European Li-ion gigafactory battery manufacturing capacity to 2020 © The Faraday Institution
Post Li-ion technology
As projected improvements to Li-ion batteries’ performance begin to plateau, these remaining challenges have motivated the search for next-generation battery chemistries.
Fortunately, there is no shortage of possible contenders, offering batteries with lower cost, improved sustainability and safety, and higher performance.
These include:
Solid-state batteries:
Conventional batteries use liquid electrolytes, and in the case of Li-ion batteries, contain non-aqueous and flammable solvents. The volatility of the electrolyte is one of the main challenges in designing inherently safe batteries.
Solid-state batteries combine a wider class of battery technologies, where the liquid electrolyte is replaced by an ion-conducting solid, generally an oxide or sulphide material. Removing the flammable components has obvious safety benefits, but also provides the framework to re-examine the use of metallic electrodes.
Historically the use of lithium metal electrodes has been hampered by the growth of dendritic lithium (microstructures that resemble whiskers). These, on repeated cycling, eventually short circuit the cell. The solid-state electrolyte provides a physical barrier to dendrite growth and was therefore widely expected to avoid this issue.
However, it was discovered that above critical current densities, highly mobile lithium could still penetrate the solid electrolyte, leading to short-circuiting. Researchers are currently looking at several strategies to address these issues (for example by applying external pressure). If successful, the solid-state battery promises high energy density and safe energy storage.
Na-ion batteries:
As a raw material, sodium (Na) is substantially more abundant than lithium, providing an opportunity to improve the sustainability and security of supply. Na-ion batteries operate via similar principles to Li-ion, wherein sodium ions are transferred between solid electrodes via a liquid electrolyte.
While Na-ion batteries have a lower energy density, the cost benefits of the technology make it an attractive alternative for some applications and it can easily ‘drop-in’ to existing Li-ion battery manufacturing infrastructure.
Li-sulphur batteries:
Sulphur is an abundant and cheap commodity chemical, often considered a by-product of industrial processes, and the LiS battery offers the possibility for a low-cost and high-energy battery. Unlike Li- and Na-ion batteries, the solid sulphur positive electrode reacts with lithium to form soluble (liquid phase) products. This reaction can occur over a wide temperature range, and is fundamentally different from the solid-state reactions that typically happen in conventional batteries.
Understanding this process, and mitigating against the active material loss that can arise from the ‘polysulfide shuttle’ mechanism is central to further developing LiS batteries. Engineers will also need to overcome other challenges associated with the electrically insulating nature of sulphur, and the comparatively low power density of the LiS system, but there is significant promise to offer a battery optimised for lightweight applications.
What are the sustainability challenges with batteries?
Cobalt, nickel, manganese and lithium mining all present issues.
Across the breadth of battery usage there are complementary challenges in reducing costs and improving the sustainability of materials supply and battery manufacture. Removing components from the battery that are expensive to source, and where supply chains are unethical, unsecure and unsustainable, is critical to contributing towards net zero. The well-documented reliance on cobalt is particularly important, because raw materials supply is largely confined to areas of low geopolitical stability, including the Democratic Republic of Congo.
Over the past decade, there has been a reduction in the amount of cobalt used in state-of-the-art batteries and it has been systematically replaced with nickel and manganese. However, cobalt is not the only scarce element found within a battery, and the EU’s Critical Materials list documents the pressure on lithium and natural graphite supply chains, as well as a watching brief on nickel. Given the rapid acceleration of the battery manufacturing sector, securing ethical and sustainable supply chains is a growing challenge that will require a significant growth in raw materials extraction. It is also essential to improve battery recycling infrastructure to establish a circular economy for the sector.
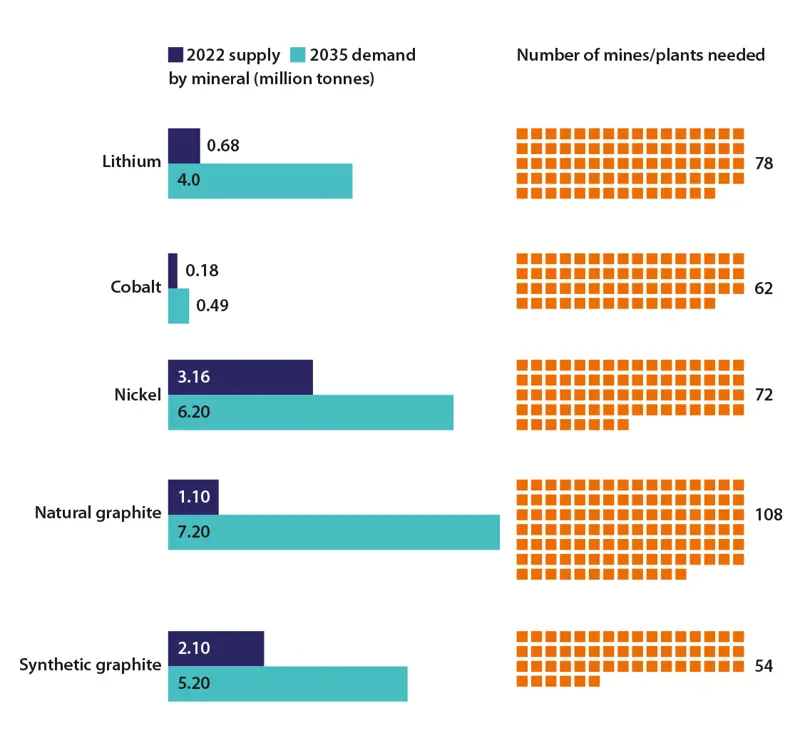
The critical minerals needed to meet global battery demand by 2035 (redrawn using figures from Benchmark Mineral Intelligence article ‘More than 300 new mines required to meet battery demand by 2035’, September 2022, and ‘Asian battery makers jeopardise raw materials access by delaying deals’, ft.com, November 2022)
Supporting net zero
‘Electrify everything’ using renewable energy is one of the key strategies to reach net zero. Energy storage, where batteries can play a central role, could meet wide-ranging energy use (across stationary, mobile and transport applications), and compensate for the intermittency of wind and solar generation. Li-ion batteries have already substantially reduced emissions through decarbonised road transport, particularly in passenger vehicles. However, this also highlights the need to integrate decarbonisation across the energy system, including in manufacturing.
As we progress towards 2050, the plateauing performance of Li-ion batteries, alongside increasingly challenging applications, will require the introduction of a portfolio of batteries. This will collectively provide opportunities to improve cost, safety, performance, and sustainability. There are already several substantial, coordinated research programmes targeting these goals, including the UK’s Faraday Institution, which brings together research scientists and industry partners to tackle scientific challenges and explore projects with commercial potential. Investing in these next-generation batteries could effectively matchmake the right battery with the right application helping to engineer a net zero world.
***
This article has been adapted from "Powering the pursuit of net zero", which originally appeared in the print edition of Ingenia 94 (March 2023).
Contributors
Professor Paul Shearing co-directs the Electrochemical Innovation Lab at UCL. Launched in 2011, it is now one of Europe’s leading centres for technological innovation in electrochemical technologies. He is a co-founder of the Faraday Institution, the UK’s independent institute for electrochemical energy storage research, and is a member of its Expert Panel. As a founder of the STFC Batteries Network, he has acted as an ambassador for UK science on an international stage, and frequently advises the UK government on policy matters.
Keep up-to-date with Ingenia for free
SubscribeRelated content
Electricals & electronics
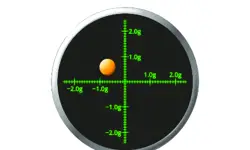
Accelerometers
Used in earthquake measurements, laptops, planes and even in stargazing apps, today’s accelerometers are much smaller than when they were first developed in 1927. Find out how they detect movement and vibration.
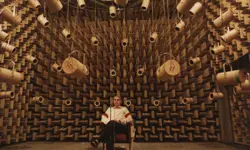
How to maximise loudspeaker quality
Ingenia asked Dr Jack Oclee-Brown, Head of Acoustics at KEF Audio, to outline the considerations that audio engineers need to make when developing high-quality speakers.
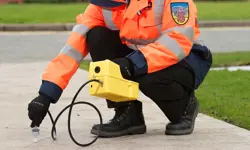
Cable fault locator
The winner of the Institute of Engineering and Technology’s 2014 Innovation Award was EA Technology’s CableSnifferTM, which uses a probe and chemical sensing technology to identify faults, saving energy companies millions of pounds each year.
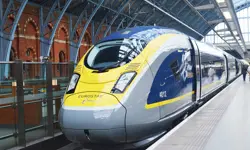
High speed evolution
In December 2010, Eurostar International Ltd awarded a contract for 10 new high speed trains to Siemens. The company has used a system developed over decades to maximise the performance and passenger-carrying ability of its 320km/h trains.
Other content from Ingenia
Quick read
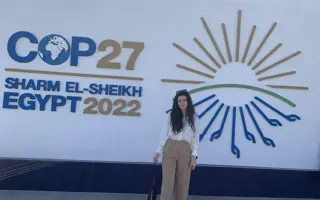
- Environment & sustainability
- Opinion
A young engineer’s perspective on the good, the bad and the ugly of COP27

- Environment & sustainability
- Issue 95
How do we pay for net zero technologies?
Quick read
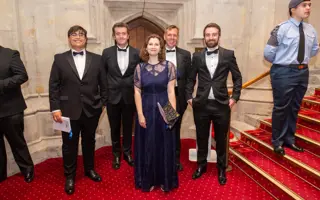
- Transport
- Mechanical
- How I got here
Electrifying trains and STEMAZING outreach
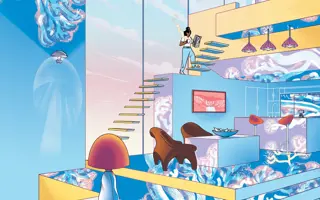
- Civil & structural
- Environment & sustainability
- Issue 95