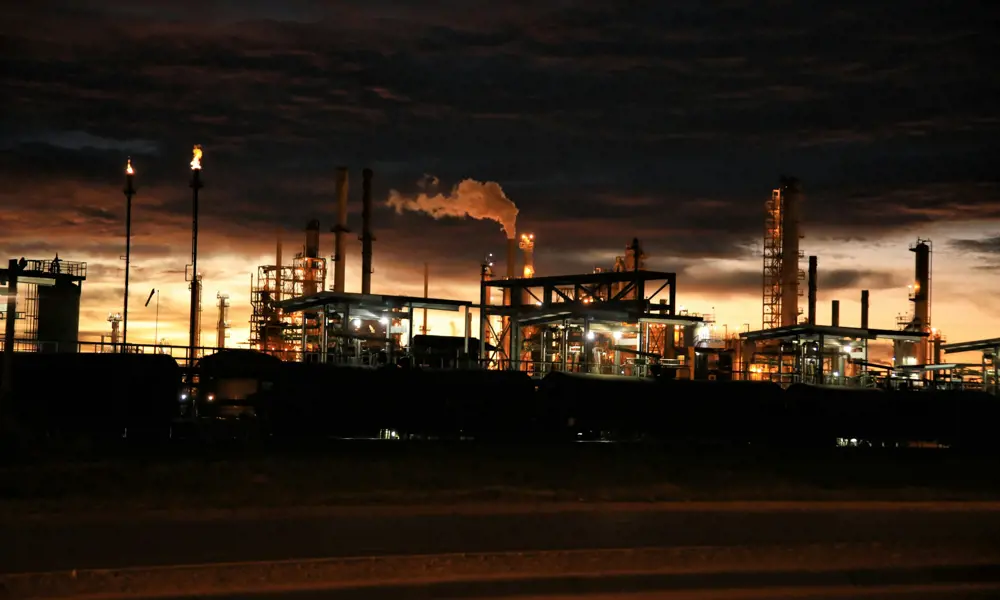
Steel can arise from the ashes of coal
Hardly a week goes by without more bad news for the UK’s steel industry. Global over-production of commodity steel, exacerbated by so-called ‘dumping’ by Chinese manufacturers, have depressed prices, causing redundancies and forcing the closure of steel plants in the UK. When the Steel Committee of the international Organisation for Economic Co-operation (OECD) and Development met in Paris last December it called for immediate action to address the excess global capacity in steel production. But any action, if it happens, could be too late for the UK’s steel makers.
If the UK’s steel industry really wants to ensure its future, it should give up its demand for energy subsidies and instead look for ways to survive in an era in which energy costs, driven up by pressure to reduce emissions of CO2, are likely to remain high. It can do this through the use of innovative technologies.
Many of the technologies that enabled steel to become the world’s dominant structural material were invented in the UK
Many of the technologies that enabled steel to become the world’s dominant structural material were invented in the UK. Sadly, in the past few decades, much of the UK steel industry has, remained innovatively static. The industry continues to produce large amounts of iron in coal-intensive blast furnaces, without implementing modern tools that would enable energy recovery and control of chemistry.
An industry that is leaner, more flexible and with the capability of producing high value products should arise from the brownfields of the large integrated plants. The key to this is to stop trying to compete with other countries in the inefficient mass production of commodity products through traditional energy- and raw material- intensive processes.
A study by the US Department of Energy shows that more than 90% of the energy, and CO2 involved in steel making is expended in the process of reduction in the blast furnace – when removing the oxygen bound to iron. We can avoid this step if we abandon iron ore and recycle steel to make iron. Currently, the UK exports steel scrap, although the value is now so low that it barely justifies the transport costs.
Is it possible to sustain a steel industry based largely on scrap? It would seem so. In the UK there is a policy to reduce CO2 emissions, disadvantaging industries that rely on fossil fuel. There is a drive to achieve affordable electricity from renewable resources and nuclear energy.
Is it possible to sustain a steel industry based largely on scrap? It would seem so
Some of the technological innovations required to move to a recycling economy in steel already exist. In the US over 60% of steel is produced by recycling used steel scrap in an Electric Arc Furnace (EAF). This exposes the scrap to an electric arc where the current in the furnace terminals passes through and melts the scrap. EAF-based scrap re-melting would eliminate a large part of energy consumption and CO2 production.
If the capacity needs to be increased beyond the available scrap (or if the price of scrap should rise), EAF can be coupled to a Direct Reduced Iron (DRI) plant. DRI uses natural gas rather than coal to remove oxygen; this would cut both costs and, thanks to the hydrogen in the gas, CO2 emissions. The combined EAF/DRI method produces far less CO2 per unit of reduced iron compared to the conventional reduction in a blast furnace.
Technologically, there is nothing to stop the implementation of combined EAF/DRI as the technology already exists. To encourage investment, the government could provide affordable electricity during a transition period before low-carbon electricity and shale gas are available.
A move to greater use of recycled steel would still pose technical challenges in manufacturing high-value products from flexible raw material. Scrap derived from cars or tin cans contain residual copper and tin that cause the surface of steel to crack during casting and hot deformation. However, EAF mills in the US have made advances by developing new methods of process control that produce advanced cold rolled sheets.
Recycling scrap steel would decrease the amount of energy required to manufacture steel. The remaining gap between the thermodynamic minimum and practice in terms of energy consumption are related to unwanted variations in temperature and chemistry, leading to yield loss. Here, too, new technology can come to the rescue. State-of-the-art sensing and automation, coupled with through-process modelling using Factory 4.0 (smart factories) allow for in-line corrections to processes that will minimise unwanted variations.
State-of-the-art sensing and automation, coupled with through-process modelling using Factory 4.0 (smart factories) allow for in-line corrections to processes that will minimise unwanted variations
To overcome the dumping of commodity steel from China (expected to be 100 million tonnes a year representing 50% more than the entire US steel production), UK steelmakers need to target products that fulfil the higher-end customers’ demand which means delivering a product that can be coated, formed and joined without a loss in properties. There are developments in the process of near net shape casting which converts liquid to solid products that are very close to their final shape and size, thereby reducing the needs for machining and forming. More innovations in thermomechanical processing and novel coating technologies will also open the doors to the manufacturing of high value products where performance and durability are important.
In short, smaller and more flexible steel mills that use electricity and/or natural gas can be built using current technologies. Over the next five to ten years, such flexible mills would create products that would match customers’ demands. Such plants would also be sustainable for the foreseeable future and resilient against global trends. To secure the future of the UK steel industry, we must develop new advanced high-strength steels that are produced using leaner, cleaner, more energy-efficient processes.
***
This article has been adapted from "Steel can arise from the ashes of coal", which originally appeared in the print edition of Ingenia 66 (March 2016).
Contributors
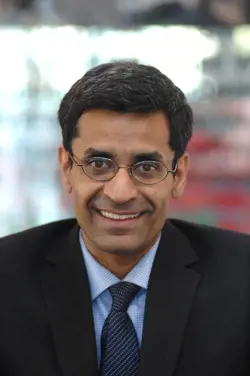
Sridhar Seetharaman is currently the RAEng/Tata Steel Joint Chair for Research into Low Carbon Materials Technology at the University of Warwick. He was, until 2013, the POSCO Professor at Carnegie Mellon University, co-director of the Industry-University Consortium, Center for Iron and Steelmaking Research and a Faculty Fellow at the National Energy Technology Laboratory of the US-DOE.
Keep up-to-date with Ingenia for free
SubscribeRelated content
Design & manufacturing
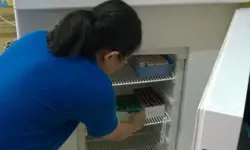
Super cool(er)
Welsh startup Sure Chill has developed a cooler that uses the properties of water to keep its contents cool for around 10 days without electricity. This is ideal for storing items such as vaccines where electricity sources are unreliable.
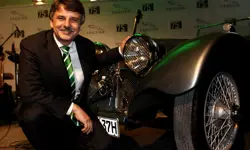
R&D investment makes good business sense
In just five years, Dr Ralf Speth FREng has presided over a revolution in design and manufacturing that has helped create a new family of engines and has overhauled Jaguar Land Rover (JLR) production facilities.
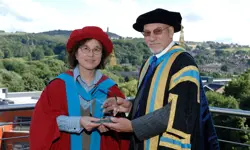
Integrating metrology in business and academe
Professor Jane Jiang’s interest in measuring began when she worked on a bus production line in China. She found that the best way to improve quality, consistency and productivity was through metrology, the science of measurement. Today, she runs the UK’s largest metrology research group.
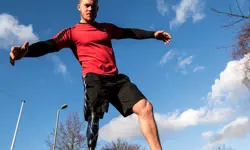
Intelligent prosthetics
Prosthetic limbs can help many amputees regain independence and mobility. The Linx limb system, winner of the 2016 MacRobert Award, developed by Blatchford, has smart robotics that constantly monitor and adapt to movement, making walking and movement more natural for lower-leg amputees.
Other content from Ingenia
Quick read
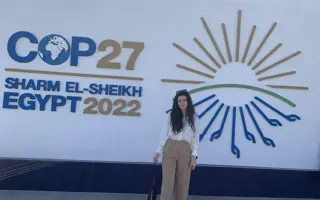
- Environment & sustainability
- Opinion
A young engineer’s perspective on the good, the bad and the ugly of COP27

- Environment & sustainability
- Issue 95
How do we pay for net zero technologies?
Quick read
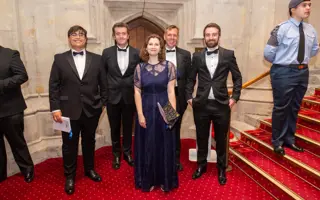
- Transport
- Mechanical
- How I got here
Electrifying trains and STEMAZING outreach
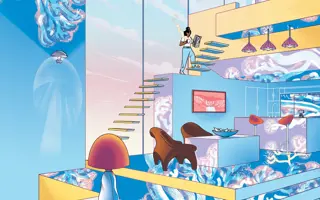
- Civil & structural
- Environment & sustainability
- Issue 95