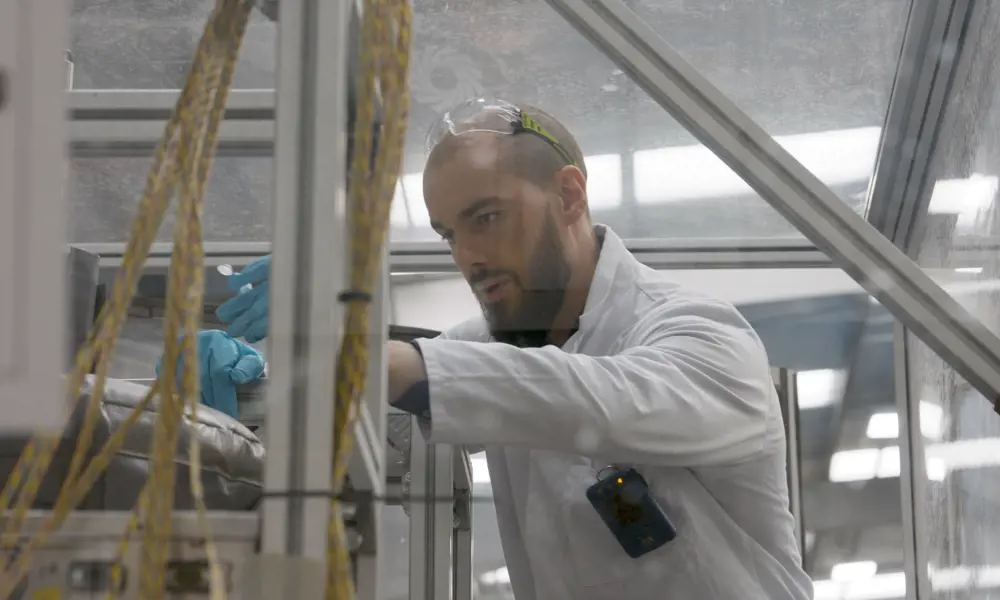
Imaging the plastic recycling process
Plastic waste is one of the greatest challenges facing the world today. Every year, 32% of plastic packaging produced finds its way into our oceans, while 73% of beach litter worldwide is plastic. The problem is not only contained to oceans, and it affects humans, wildlife and their habitats. Yet only about 9% of plastic is recycled.
Dr Kit Windows-Yule, a nuclear physicist turned chemical engineer working as a senior lecturer at the University of Birmingham, wanted to do something to address this crisis. He has been working with Swindon-based Recycling Technologies (RT), which is developing a modular system designed to stop large amounts of plastic being transported from waste sites.
RT has developed a machine, the RT7000, that uses a method called pyrolysis – heating plastics at a high temperature in an oxygen-free environment so that the molecules that make up the plastic break up into smaller pieces, turning them back into something like the crude oil from which they were formed (‘Processing the plastic problem’, Ingenia 75). This means they can be used again to make ‘good-as-new’ plastic products, as well as clean, low-sulphur fuels.
RT already had a longstanding relationship with the University of Birmingham’s School of Chemical Engineering. When Kit was awarded a Royal Academy of Engineering Industrial Fellowship in 2019, it allowed him to spend half his time working with the company, alongside lecturing at the university. He is helping RT analyse the internal dynamics of the RT7000 by using the positron emission particle tracking (PEPT) technique, developed by the University of Birmingham, to produce detailed imaging and study the 3D dynamics of what is going in the machine.
He explains: “The PEPT technique was originally developed at the University of Birmingham by Professor David Parker and Dr Michael Hawkesworth, the former of whom I was lucky enough to have as my PhD supervisor.
"Since its inception in the late 1980s, PEPT has continued to be developed in the university’s Positron Imaging Centre, an interdisciplinary centre founded in collaboration between the university’s schools of physics and chemical engineering. In the early 2000s, the centre developed the world’s first modular positron camera, which (unlike conventional systems) was both portable and could be reconfigured into effectively infinite different geometries, meaning it could image a wide range of scientific and industrial systems (including unusually shaped systems).
"Recent upgrades of the camera, led by the Positron Imaging Centre’s Director, Professor Tzany Kokalova Wheldon, combined with novel algorithms and radioactive tracers developed within my research group, have enabled the work with RT to be realised.”
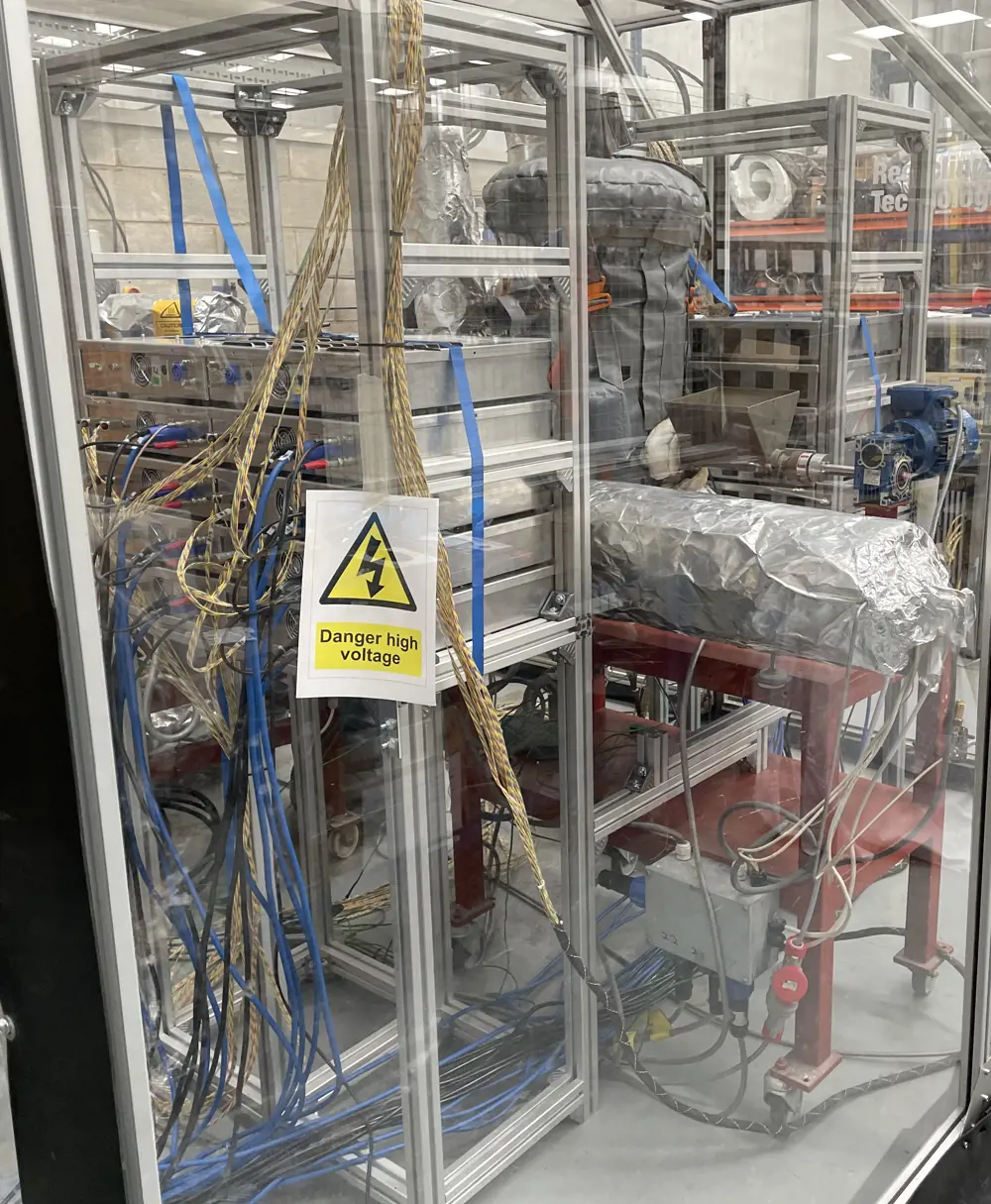
The modular PEPT camera on site
Inner workings
The technology is a portable, modular positron imaging camera, which allows researchers to ‘see inside’ industrial systems and understand their inner dynamics. “It carries a big advantage over, for example, X-ray imaging in that it uses highly penetrating gamma rays (as opposed to lower-energy X-rays), which means that we can even see through materials such as steel and titanium,” explains Kit. “This makes it ideal for imaging industrial systems, which are often constructed from such materials.” However, the innovation is that it is both portable and modular, consisting of a lot of individual blocks that can be built, Lego-style, to suit various industrial geometries.
RT’s challenge was that it did not previously know how the plastics behaved once fed into the RT7000 system: for example, how long do they stay as solids? How quickly do they melt and evaporate? Are they spread evenly (and thus efficiently) throughout the system? “By using our positron imaging methods, we were able to directly image these processes for the first time ever,” adds Kit, “and provide valuable information regarding how their systems should be operated to ensure maximum efficiency.”
Kit secured follow-on funding including a £440,000 EPSRC New Investigator Award, a Royal Society Research Grant, and an Academy-funded Proof of Concept Award. This allowed him to develop extra tools and acquire necessary permits to track individual particles and model the internal dynamics of the process, to measure the influence of gas flow rates, distributor design, and the size and shape of plastic inputs. “We used gamma radiation to actually see inside their [RT’s] solid steel reactor and image the processing, melting and devolatilisation of plastics as they are broken down into their basic chemical components for recycling. This is the first time that this kind of imaging has ever been done on-site in an active industrial facility.” Essentially, Kit and RT were able to better understand how the system operates, and how the process can be improved and optimised for better energy efficiency and more careful control of the end products.
The imaging work is supported by numerical modelling techniques such as coupled computational fluid dynamics and discrete element method (CFDDEM) simulations and Barracuda MP-PIC simulations, which allow true-to-life simulation of the systems of interest. The application of numerical simulations allows not only deeper insight, but also allows Kit to improve, expedite, and reduce the financial impact of optimisation processes – he can come up with and test new ideas for different geometries or operating conditions, for example, using only a computer. Promising ideas can then be tested at the lab scale using conventional PEPT and, if successful, ultimately implemented in the real system.
Portable processes
“Conventional, lab-based PEPT is already widely used for exploring and optimising diverse process equipment in the agriculture, chemical, food, green energy, pharmaceutical, and personal care sectors (among others),” Kit says. “As such, there is significant potential value to the use of on-site PEPT in these sectors, especially for pilot-scale equipment that cannot be feasibly transported to Birmingham, or for continuous processes where the imaging of individual components of the process in isolation from up- and down-stream processes would not be meaningful.” In the coming years, the intention is to set up a spin-out company for such purposes. “Our modular camera can be applied to anything from pharmaceutical secondary manufacture and chemical processing to biofuels production, or even the development of personal care products like shampoo and conditioner.”
The modular nature of the RT system is also important, as all major components can be individually transported on a single flatbed truck. Firstly, it means that recycling centres can easily be set up across the country; this decentralised approach removes the need to transport plastic over long distances across the country to a single, centralised facility, and significantly reduces the greenhouse gases emissions caused by these long journeys. Secondly, the modular approach means that recycling facilities can be easily set up in areas with little infrastructure, making them suitable for use in low-income countries where the plastic waste crisis is most acutely felt. Since the recycling process converts plastic into pseudo-crude oil, it also ‘monetises’ plastic waste, turning it from a waste product into a resource with financial value, meaning that the arrival of these machines in such countries carry the potential not only to create jobs, but an entirely new economy.
Having been awarded his second Industrial Fellowship in 2021 to continue working with RT, Kit hopes that he will be able to contribute to the further development of this technology that, if widely adopted, could provide transformative in the fight against plastic waste.
***
This article originally appeared in the print edition of Ingenia 92 (September 2022).
Keep up-to-date with Ingenia for free
SubscribeRelated content
Environment & sustainability
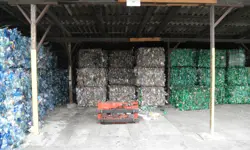
Recycling household waste
The percentage of waste recycled in the UK has risen rapidly over the past 20 years, thanks to breakthroughs in the way waste is processed. Find out about what happens to household waste and recent technological developments in the UK.
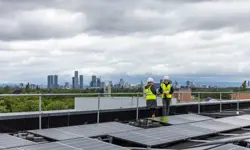
Upgrade existing buildings to reduce emissions
Much of the UK’s existing buildings predate modern energy standards. Patrick Bellew of Atelier Ten, a company that pioneered environmental innovations, suggests that a National Infrastructure Project is needed to tackle waste and inefficiency.
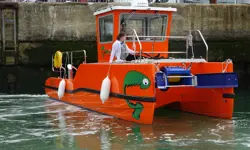
An appetite for oil
The Gobbler boat’s compact and lightweight dimensions coupled with complex oil-skimming technology provide a safer and more effective way of containing and cleaning up oil spills, both in harbour and at sea.
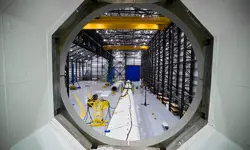
Future-proofing the next generation of wind turbine blades
Before deploying new equipment in an offshore environment, testing is vital and can reduce the time and cost of manufacturing longer blades. Replicating the harsh conditions within the confines of a test hall requires access to specialist, purpose-built facilities.
Other content from Ingenia
Quick read
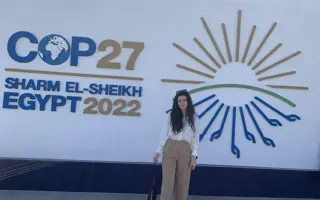
- Environment & sustainability
- Opinion
A young engineer’s perspective on the good, the bad and the ugly of COP27

- Environment & sustainability
- Issue 95
How do we pay for net zero technologies?
Quick read
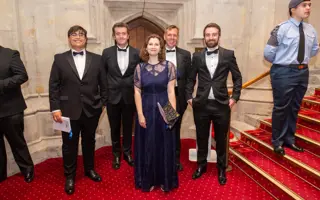
- Transport
- Mechanical
- How I got here
Electrifying trains and STEMAZING outreach
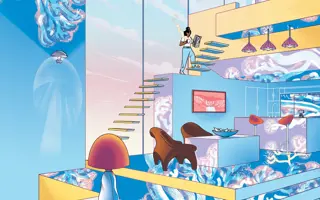
- Civil & structural
- Environment & sustainability
- Issue 95