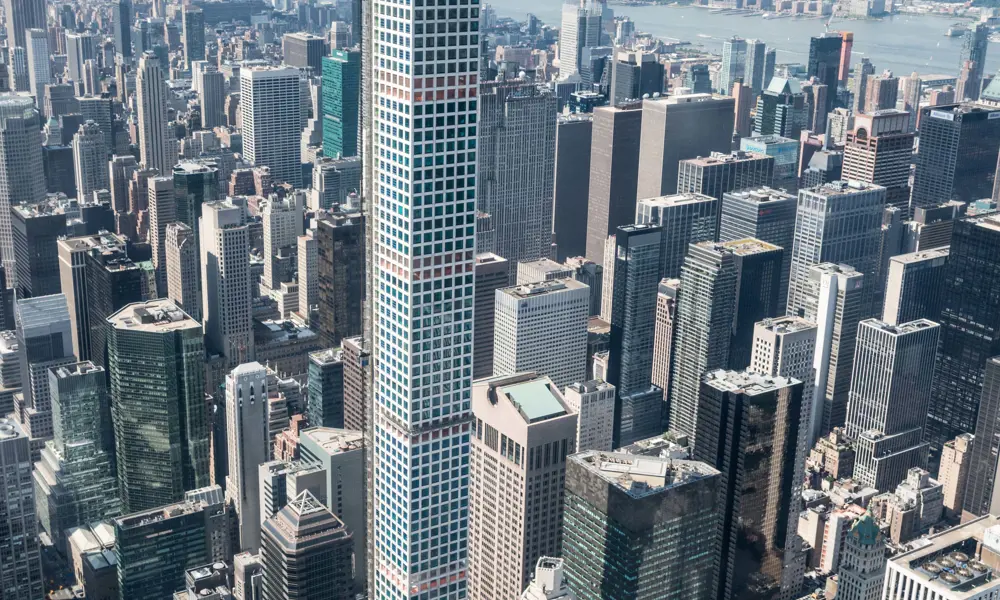
The sky's the limit
In the heart of Manhattan, where land values are among the highest in the world, stands 432 Park Avenue, one of New York City’s newest skyscrapers and a towering example of what new engineering techniques, combined with high-performance materials, can achieve.
New York was the birthplace of the skyscraper, notably with the Chrysler Building and Empire State Building in the early 1930s, both of which are steel-frame buildings of rectilinear shapes. In the 1960s, the skyscraper had something of a resurgence with the introduction of tubes (usually in steel) for perimeter and interior columns and perimeter diagonal bracing, which greatly reduced the weight of steel required and hence the cost. Many buildings over 40 storeys that have been constructed since the 1960s use a tube system adapted from the structural engineering principles of Bangladeshi-American structural engineer Fazlur Khan. This included the John Hancock Center in Chicago, and the World Trade Center twin towers in New York (1973).
New York was the birthplace of the skyscraper, notably with the Chrysler Building and Empire State Building in the early 1930s
Tall buildings continue to spring up throughout the world in response to many factors, such as increasing urbanisation, a desire to create iconic buildings, and the discovery that people across the world love grand views. Now, more than half of the world’s 20 tallest buildings are in China (with four elsewhere in the Far East, three in the USA and two in the Middle East). Before 2000, two thirds of skyscrapers were commercial: since then, more than two-thirds have been residential or mixed-use.
Slender and stable
At 426.5 metres, 432 Park Avenue is one of the world’s 20 tallest buildings. It is the second tallest building in New York City and the third tallest in the USA. The building is entirely residential and currently stands as the tallest residential tower in the Western Hemisphere. However, much more significantly, with its compact 28.5 metre-square footprint, it has an aspect ratio (height/width) of 15:1, a slenderness that would have been unthinkable a decade ago. This has helped the developer to gain more usable space out of a comparatively small plot, and to give the residents unrivalled views of the Manhattan skyline. It also presented interesting challenges for the building’s engineers.
432 Park Avenue had to be designed to transfer its own weight down to the foundations, to resist seismic and wind loads, and – most challenging of all with such a slender building – to manage the movement of the building under wind loading so that no movement would be detectable. All tall buildings move in the wind, but occupants, particularly residents, do not want to feel the sway. That meant keeping the lateral acceleration of the building (its movement in wind) below around 0.1 m/s2 (metre per second squared) in a ‘once-in-a-year’ gale.
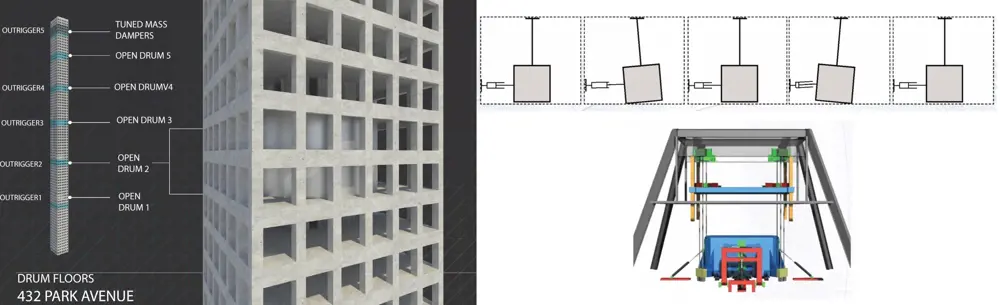
(Left): The square-shaped concrete core of the building is connected by ‘outriggers’ (double-storey concrete frames) to the exterior girder-column grid at roughly every 12th floor so that they act monolithically and increase the overall lateral stiffness. (Right): Two mass-tuned dampers were also added to the top of the building to control its movement. A tuned-mass damper is a mass that is supported by a pendulum arrangement and connected to the structure by means of springs and/or dampers
On most tall buildings, extensive wind tunnel testing is an integral part of the structural analysis and design. This may include: high-frequency force balance tests; multi-degree of freedom aeroelastic modelling, which explores the independently acting factors that influence the interaction between inertial, elastic, and aerodynamic forces that occur when the building is exposed to wind; wind studies done at large scale on just one section of the building at a time; cladding pressure and wind studies to ensure that cladding panels, windows and fixings will not be blown off in a gale; pedestrian-level comfort testing, to ensure downdraft wind on the building and any street-level wind tunneling does not create discomfort for nearby pedestrians; and wind-induced aeroacoustic studies, to check and ensure that wind will not cause any whistling or noise-generated issues.
At the time, 432 Park Avenue was one of the most slender buildings in the world, designed by engineering consultant WSP. Therefore, wind-related testing was particularly rigorous, with around five force-balance tests backed up by several all-day workshops to establish the optimum configuration, followed by a few aeroelastic tests on the final design.
wind-related testing was particularly rigorous, with around five force-balance tests backed up by several all-day workshops to establish the optimum configuration
First, the building had to be made as stiff as possible to resist overall bending, while still leaving large, open areas on the floor plan for attractive living spaces. This was achieved by creating a 9 metre by 9 metre concrete shear-wall core around the lift shafts, which formed the building’s central spine. Less conventionally, the strong core was supplemented by a framework of concrete columns and spandrel beams forming the building envelope and avoiding the need for externally mounted cladding. Cast-in-situ floors span between the central core and the perimeter frames. To ensure that the concrete perimeter framing and interior core respond monolithically to structural demands, they were connected by massive double-storey concrete frames, known as ‘outriggers’, which were concealed in the plant rooms at about every 12th floor.
Despite its lateral stiffness, the tower still tended to move unacceptably in varying wind conditions, and the lateral-load-carrying system had to be ‘tuned’ to minimise displacement, acceleration and vibration. This was solved by adding mass to the upper levels, achieved by increasing the typical 250-millimetre thickness of the concrete floors to 450 millimetres. Two 650 tonne mass-tuned dampers were also added to the top of the building: these are large steel weights supported by cables as pendulums and connected laterally to the structure by viscous dampers, which absorb the energy of the moving weights and transfer the associated forces into the building structure, slowing the building’s acceleration to acceptable limits.
Early wind tunnel testing had shown that the building exhibited significant ‘vortex shedding’, which is an oscillating airflow phenomenon that can occur when wind flows past a building at certain velocities. Vortices are formed at the back of the building, detaching periodically from either side. Each low-pressure vortex tends to pull the building towards the centre of the vortex, so the effect can be to induce vibration, particularly if the frequency of vortex shedding approaches the resonant frequency of the structure. The solution at 432 Park Avenue was ingenious and innovative: by leaving the building windowless at precise levels and creating ‘open’ floors – a technique comparable to making holes in the sail of a boat – the wind loading was reduced and so was the vortex shedding. Conveniently, these levels could be designed to coincide with the plant rooms, and to some extent the outriggers, at about every 12th floor.
by leaving the building windowless at precise levels and creating ‘open’ floors – a technique comparable to making holes in the sail of a boat – the wind loading was reduced and so was the vortex shedding
Although these ‘open’ floors take up valuable floor space, this is more than compensated for by the additional stability that allowed the height of the building to be increased to 86 storeys.
The concrete required for the building was no ordinary concrete. For the lower sections carrying larger vertical and lateral loads, it had to have a specified compressive strength of more than 100 MPa (‘high strength’ concrete is considered to have a compressive strength of 50 MPa or more). All structural concrete was designed for enhanced durability by minimising air content and the water/cementitious materials ratio, and with a higher-than-normal modulus of elasticity to minimise deformation. To aid placing and to improve the finished appearance, it had to be able to be pumped to great heights. Since there was to be no cladding to cover potential blemishes on the exterior of the building, architectural exposed concrete was specified in an attractive white colour and was placed with near-perfect workmanship. Although the exterior concrete should be maintenance-free, the exterior of the building required access for glass cleaning and replacement, which will be done using a telescopic building maintenance unit (BMU) mounted on the roof.
Safer skyscrapers
🧯 Why are skyscrapers among the safest buildings in the world and what is their fire strategy?
Skyscrapers are now among some of the safest buildings in the world, if only because they must be thoroughly engineered to the finest detail, and not just for structural safety. For example, the fixings of every external cladding panel should allow for sufficient movement to accommodate the building’s sway under anticipated conditions.
Most modern tall buildings have a fire strategy, which covers such issues as means of escape, detection and alarm, fire suppression, smoke control, firefighter access and facilities, compartmentation, and internal and external spread of fire. Most high-rises now include dedicated fire stairs and some have lifts that can be used for fire escape, which require special details such as pressurised lobbies where people can wait for the lifts and an independent cooling system for the lift motor room. The main fire element of tall building design is ensuring that compartmentation is maintained until the fire is exhausted or controlled. Spread of fire on the exterior of a building is usually mitigated by choosing insulation materials of limited combustibility, provision of adequate fire-stopping, cavity barriers around openings, and main compartmentation lines. For example, in August 2016, a fire burned dramatically for two hours on the outside of Dubai’s 84-storey Torch Tower, where some of the cladding systems were not of limited combustibility and fire-stopping was inadequate. Despite this, other elements of the fire strategy worked well, particularly suppression that ensured safe escape for occupants, and consequently there were no casualties.
Even taller towers
Now, just three blocks away, 432 Park Avenue’s successor is nearing completion. Not content with an aspect ratio of 15:1, 111 West 57th Street has a ratio of 24:1, which will make it the world’s most slender building. At 438 metres, it is slightly taller than its neighbour and shares many features: both are high-end residential buildings, both use high-strength concrete, and both have a tuned mass damper on the top and gaps allowing the wind to pass through to minimise vortex shedding.
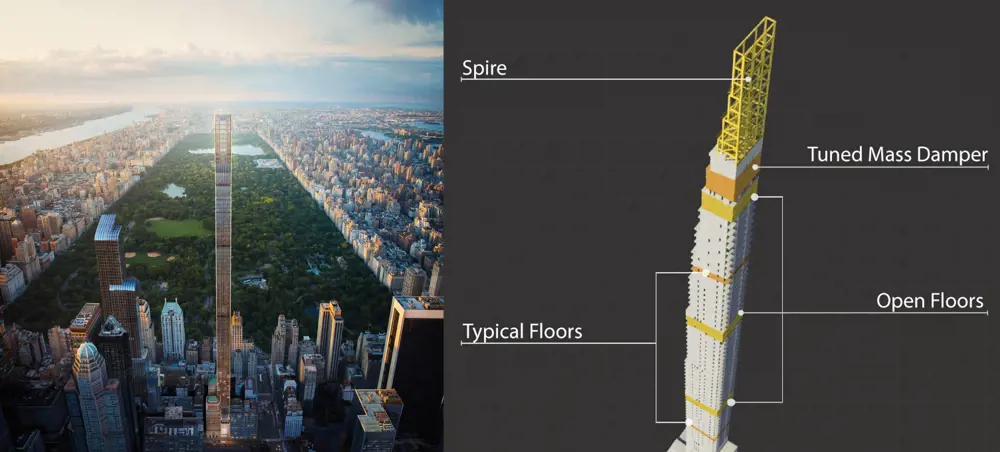
(Left): A rendering of 111 West 57th Street. Its aspect ratio of 24:1 will make it the world’s most slender building. (Right): Shear walls run the full length of the east and west exteriors and have been thickened to as much as one metre. Like 432 Park Avenue, it also has open floors that the wind will pass through to reduce vibration
Now, just three blocks away, 432 Park Avenue’s successor is nearing completion. Not content with an aspect ratio of 15:1, 111 West 57th Street has a ratio of 24:1, which will make it the world’s most slender building. At 438 metres, it is slightly taller than its neighbour and shares many features: both are high-end residential buildings, both use high-strength concrete, and both have a tuned mass damper on the top and gaps allowing the wind to pass through to minimise vortex shedding.
The main difference is that the architect and developer for the latter wanted clear, unobstructed views northwards over Central Park and south towards Lower Manhattan. The solution was a concrete core, linked to two concrete shear walls (a structural system composed of braced panels) running the height of the building on the east and west sides and allowing clear views north and south, so that the overall structure resembles a giant cantilevered concrete I-beam standing on its end. The tower is slightly tapered, and the external walls will be clad in terracotta and bronze rather than architecturally exposed concrete. Even more slender buildings are now being planned, although an aspect ratio of 24:1 is approaching the limit of what is currently feasible.
The engineering challenges of tall buildings
🏙️ What were the challenges of building The Shard, Newfoundland, Torre Mayor and 22 Bishopsgate?
The Shard
Completed in 2012, the Shard in London is the UK’s tallest building at 310 metres and 95 storeys. It is shaped as an irregular pyramid with highly complex geometry. The Shard is a modern mixed-use tall building with retail at the base, offices in the lower levels, a hotel in the middle and residential near the top. A strong central concrete core and a hat truss that engages all perimeter columns form the spine of the building, and the remainder varies with use: structural steel was the optimum solution for the offices, where deep steel beams could allow plenty of space for the extensive services required. For the hotel and flats, where acoustic separation was more important and where spans were shorter owing to the tapering of the building, concrete floors were preferred, which were thinner so that two extra storeys could be added within the same overall building height. The tower then reverts to steel for the viewing gallery and the spire.
Newfoundland
The 220-metre high, 60-floor Newfoundland residential tower in Canary Wharf, London, straddles the Jubilee Line tube tunnels, which are close to the surface at the tower’s location. This required careful piling between and beside the tunnels, as well as a major load-transfer structure to connect the building’s loads with the piles. However, to avoid disturbance to the tunnels, it was necessary to keep the weight of the building to a minimum. The solution was a ‘diagrid’ of diagonally placed steel members on the outside of the building creating a diamond pattern, and the use of post-tensioned concrete floor slabs connecting the diagrid to the concrete core. The diagrid was so light and strong that the thickness (and therefore the weight) of the shear walls in the concrete core could be reduced to just 300 millimetres.
Torre Mayor
The 225-metre high, 55-storey Torre Mayor in Mexico City was Latin America’s tallest building when it opened in 2003 and is now Mexico’s fourth tallest. The design priority for this building was seismic design, as it stands in the lakebed area where the heaviest damage from the catastrophic Michoacán 1985 earthquake was recorded. Designed to resist an 8.5 Richter earthquake, Torre Mayor has an arrangement of 96 viscous fluid dampers (with technology borrowed from the shock-absorbers of a car) attached to the diagonal cross-bracing on the perimeter of the building, which safely absorb the earthquake’s energy. A 7.6 Richter earthquake in 2003 did no damage: indeed, the occupants did not even notice that a tremor had taken place. The structure also responded as expected when the 7.1-magnitude earthquake of Axochiapan occured in September 2017.
22 Bishopsgate
When it is completed in 2019, 22 Bishopsgate will be London’s second tallest building at 278 metres with 62 floors. This will be even more of a ’vertical village’ including retail, restaurants, an auditorium, various leisure facilities, including a climbing wall on the 25th floor, and offices. It will be the first building in the UK to be accredited for standards to improve building users’ health and wellbeing. The main challenge here was to address what had gone before: a previous scheme was abandoned in 2012 because of the recession, with just the foundations and seven storeys of the core constructed. The core was deconstructed, but for the new tower to be economical, a way had to be found to place an entirely different building on the existing foundations (including London’s deepest piles). This required elaborate analysis and design at the base of the building to transfer the loads to the foundations such that the full strength of the existing piles was mobilised, but no individual pile was overloaded.
Evolution of skyscrapers
The buildings at 432 Park Avenue and 111 West 57th Street are responding to the specific parameters of the New York City market, including strong demand for high-end residential properties with outstanding views, and locally available high-strength coarse aggregates needed for making ultra-high-strength concrete (a similar compressive strength in London, for example, would require imported aggregate, and is therefore a much more expensive concrete). In different parts of the globe, the parameters or constraints are likely to be different and so too are the solutions.
The original rectilinear steel buildings most usually associated with skyscrapers have largely been succeeded by concrete or composite concrete-and-steel, and the equally ubiquitous office buildings have given way to varieties of mixed-use towers: modern skyscrapers are becoming self-contained cities in the sky with a mix of residences, offices, hotels, restaurants and public areas.
with increased urbanisation, a public appetite for tall buildings and the ingenuity of engineers, the surge in skyscrapers worldwide is set to increase still further
As ever-stronger materials are developed, there is no structural limit to how high skyscrapers could be built. The only foreseeable limits are likely to be the larger footprints required at ground level and the transport links to service the many occupants, for example the constraints of providing fast and efficient vertical transportation, and economic viability: larger buildings cost more, take longer to build, and take longer to let, so developers need even deeper pockets. However, with increased urbanisation, a public appetite for tall buildings and the ingenuity of engineers, the surge in skyscrapers worldwide is set to increase still further – and some of them will be even taller.
***
Hugh Ferguson also talked to Nick Offer, Head of London Building Services for WSP.
All projects mentioned in this article have been structurally designed by WSP
This article has been adapted from "The sky's the limit", which originally appeared in the print edition of Ingenia 73 (December 2017)
Contributors
Hugh Ferguson
Author
Kamran Moazami is Managing Director, Property and Buildings, at WSP. He studied structural engineering at Columbia University in New York. After obtaining his master’s degree, he joined New York skyscraper firm, Cantor Seinuk, where he worked on several high-rise buildings. In 1996, he relocated to the UK to head up the company’s London office. Later on, Cantor Seinuk was acquired by London-based firm WSP.
Keep up-to-date with Ingenia for free
SubscribeRelated content
Civil & structural
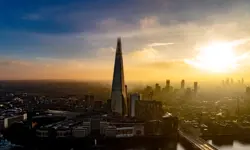
Building the Shard
The Shard is one of London's most iconic buildings. The tallest in Western Europe, it was designed by Italian architect Renzo Piano and dominates the city’s skyline. Ingenia spoke to John Parker, project director for structural engineers WSP, who outlined the engineering decisions made in building the enormous steel and glass structure.
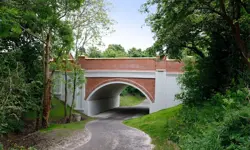
FlexiArch
Arch bridges are strong, durable and require little maintenance. However, very few had been built since the early 1900s until the FlexiArch was developed and launched in 2007. Now, there has been a minor renaissance for this ancient form of construction.
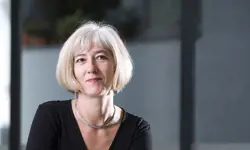
Creating user-friendly buildings
For Michelle McDowell, a former Business Woman of the Year, a passion for joined-up design thinking and building information modelling with a user-friendly approach has enabled her to pioneer revolutionary changes in her field.
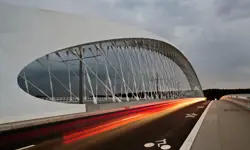
Troja Bridge
In November 2014, one of the world’s largest network arch bridges was officially opened in Prague. The UK may soon have its first network arch bridge if the go-ahead is given for a new rail project in Manchester.
Other content from Ingenia
Quick read
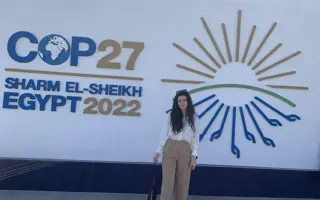
- Environment & sustainability
- Opinion
A young engineer’s perspective on the good, the bad and the ugly of COP27

- Environment & sustainability
- Issue 95
How do we pay for net zero technologies?
Quick read
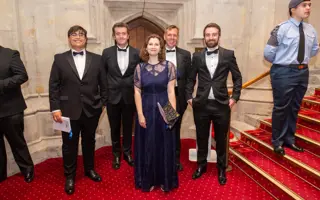
- Transport
- Mechanical
- How I got here
Electrifying trains and STEMAZING outreach
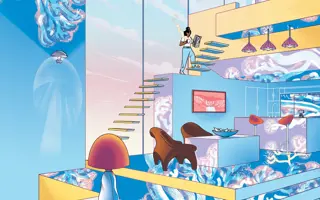
- Civil & structural
- Environment & sustainability
- Issue 95